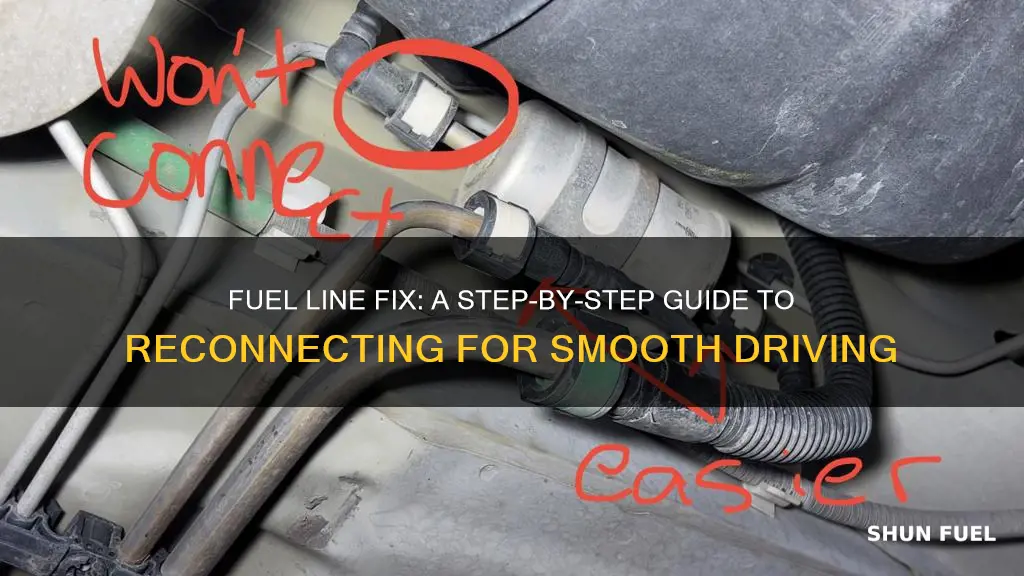
Reconnecting a fuel line is a crucial step in ensuring your vehicle's engine operates efficiently and safely. This process involves carefully reattaching the fuel line to the fuel tank and engine, ensuring a secure and airtight connection to prevent fuel leaks. It's important to follow a step-by-step guide to avoid any potential hazards and to ensure the job is done correctly. This guide will provide a detailed process, including the necessary tools and safety precautions, to help you reconnect the fuel line with confidence.
What You'll Learn
- Preparation: Gather tools and materials, ensure safety, and prepare the workspace
- Fuel Line Inspection: Check for damage, cracks, or leaks, and replace if necessary
- Clamping: Secure the fuel line with appropriate clamps, ensuring a tight fit
- Routing: Route the fuel line away from heat sources and potential hazards
- Testing: Verify the connection's integrity by checking for leaks and proper flow
Preparation: Gather tools and materials, ensure safety, and prepare the workspace
Before you begin the process of reconnecting a fuel line, it's crucial to ensure you have the necessary tools and materials ready. This preparation step is essential to guarantee a smooth and efficient repair. Here's a detailed guide on what you need and how to get ready:
Gather the Tools and Materials:
- Fuel Line Connectors: You'll need the appropriate connectors that match the size and type of your fuel line. Common types include quick-connect fittings, clamp-style connectors, or threaded fittings, depending on your vehicle's make and model.
- Fuel Line: Ensure you have a replacement fuel line of the correct length and diameter. It's important to measure the old line to get an accurate fit.
- Towel or Rag: A clean cloth will be useful for wiping away any dirt or debris from the fuel line and the surrounding area.
- Safety Gear: Safety should always be a priority. Wear gloves to protect your hands and consider eye protection, especially when working with fuel.
- Wrenches and Pliers: You might need various sizes of wrenches and pliers to tighten connections and adjust fittings.
- Fuel Filter (Optional): If your fuel line connects to a fuel filter, you may need to replace it as well, especially if it's been a while since the last replacement.
- Cleaning Supplies: Have some cleaning solutions ready, such as fuel line cleaner, to ensure the fuel system is free from contaminants.
Ensure Safety and Prepare the Workspace:
- Safety First: Before starting, ensure the engine is off and the vehicle is in a secure position. Never work on a running engine as it can be dangerous. Additionally, locate the fuel shut-off valve and ensure it is closed to prevent any accidental fuel release.
- Ventilation: Work in a well-ventilated area to avoid inhaling any fuel vapor. If working indoors, open windows or use a fan to improve air circulation.
- Clear the Area: Clear the workspace of any obstacles or items that could interfere with your work. Ensure there is enough room to move around comfortably and access all necessary components.
- Grounding: Consider using a grounding strap to prevent static electricity buildup, especially when working with fuel lines. This is an important safety measure to avoid sparks that could ignite fuel.
- Read the Manual: Familiarize yourself with your vehicle's owner's manual to locate the fuel lines and understand the specific procedures for your car. This will ensure you reconnect everything correctly.
By following these preparation steps, you'll be well-equipped to safely and effectively reconnect the fuel line, ensuring your vehicle's fuel system is secure and functional. Remember, taking the time to prepare is essential for a successful repair.
Unraveling the Mystery: Can Fuel Lines Withstand Heat?
You may want to see also
Fuel Line Inspection: Check for damage, cracks, or leaks, and replace if necessary
Fuel lines are critical components of your vehicle's fuel system, and ensuring they are in good condition is essential for safe and efficient operation. Over time, fuel lines can deteriorate due to various factors, including age, chemical degradation, and physical damage. Regular inspection and maintenance can help prevent costly repairs and ensure your vehicle's reliability. Here's a step-by-step guide to inspecting your fuel lines and addressing any issues:
Visual Inspection: Start by visually examining the fuel lines for any signs of damage, cracks, or leaks. Look for the following:
- Cracks and Tears: Inspect the lines for any visible cracks, tears, or punctures. These defects can allow fuel to leak out, leading to potential safety hazards and engine performance issues.
- Swelling or Bulging: Check for any areas where the fuel line appears swollen or bulging. This could indicate internal damage or the presence of fuel pressure.
- Leakage: Inspect the lines for any signs of fuel leakage. This might be visible as a puddle of fuel around the vehicle or a hissing sound. Even small leaks can lead to engine misfires and reduced performance.
- Corrosion: Look for signs of corrosion, especially if the lines are exposed to the elements. Corroded lines may have a rusty appearance or feel.
Feel for Leaks: In addition to visual inspection, use your sense of touch to detect leaks.
- Spray with Water: Spray a fine mist of water onto the fuel lines, especially where they are exposed. If you feel a wet spot or hear a hissing sound, it indicates a potential leak.
- Listen for Fuel: If you suspect a leak, you might hear a faint sound of fuel running or dripping.
Check for Cracks and Damage:
- Inspect the fuel lines for any signs of wear and tear. Look for soft spots, kinks, or bends that might indicate damage.
- Check for any signs of rust or corrosion around the connections and fittings.
- Ensure that the lines are securely attached to the fuel tank and engine.
Replace Faulty Lines: If you identify any damage, cracks, or leaks during the inspection, it's crucial to replace the affected fuel lines immediately. Here's how:
- Gather Tools and Parts: You'll need a new fuel line, appropriate tools for removal and installation, and possibly some fuel line sealant.
- Remove the Old Line: Carefully disconnect the damaged fuel line from the fuel tank and engine. Take note of the connection points and any fittings.
- Install the New Line: Follow the manufacturer's instructions to install the new fuel line. Ensure it is securely attached and routed correctly.
- Test for Leaks: After installation, start the engine and check for any leaks. If none are found, your fuel system is now ready for use.
Remember, regular maintenance and prompt attention to any issues will help ensure your vehicle's fuel system operates efficiently and safely. If you're unsure about any part of the inspection or replacement process, consult a professional mechanic for assistance.
Unraveling the Mystery: Why Diesel Engines Need Two Fuel Lines
You may want to see also
Clamping: Secure the fuel line with appropriate clamps, ensuring a tight fit
When reconnecting a fuel line, proper clamping is essential to ensure a secure and leak-free connection. Here's a step-by-step guide on how to achieve this:
Start by selecting the right clamps. The type of clamp you choose will depend on the specific fuel line and vehicle. Common types include metal or plastic clamps with a V-shaped or U-shaped design. Ensure the clamp is compatible with the fuel line's diameter and material. Measure the fuel line's diameter carefully to get the correct size.
Once you have the appropriate clamp, locate the fuel line's connection point. This is usually where the line splits or joins, often near the fuel tank or engine. Clean the area around the connection to remove any dirt or debris. This ensures a tight seal when clamping.
Now, carefully slide the clamp over the fuel line, positioning it securely around the connection. The clamp should fit snugly, providing a firm grip. Apply firm pressure to ensure the clamp is tight and won't come loose. You may need to adjust the clamp's position slightly to get the best fit.
For optimal security, consider using multiple clamps. This is especially useful for longer fuel lines or those with multiple bends. Space the clamps evenly along the line, ensuring they are tight and secure. This method provides added protection against leaks and ensures the fuel line remains stable.
Remember, a tight and secure clamp is crucial for the safety and performance of your vehicle. Take your time to ensure the clamp is properly positioned and tightened. If you're unsure, consult the vehicle's manual or seek professional advice to ensure you're using the correct clamps and techniques for your specific fuel line reconnection.
Dorman OE Solutions Fuel Line Connector: A Step-by-Step Guide
You may want to see also
Routing: Route the fuel line away from heat sources and potential hazards
When reconnecting a fuel line, proper routing is crucial to ensure the system's safety and optimal performance. The primary goal is to route the fuel line away from heat sources and potential hazards to prevent damage and reduce the risk of fuel leaks. Here's a step-by-step guide on how to achieve this:
Start by identifying the fuel line's original path and any areas that might be prone to heat exposure or potential damage. Heat sources can include engine compartments, exhaust systems, and even nearby electrical wiring. The fuel line should be routed away from these areas to avoid any potential overheating or damage. Use flexible fuel line kits or custom-made hoses if the original line is damaged and needs replacement. These kits often provide pre-cut lengths and bends, making the routing process more manageable.
When routing the new fuel line, ensure it is positioned at a safe distance from heat sources. A good practice is to maintain a minimum distance of 2 inches (5 cm) from any hot surfaces or components. This distance provides a protective barrier and reduces the risk of fuel line damage. Additionally, keep the fuel line away from sharp edges, protruding objects, or areas where it could be accidentally damaged during vehicle operation.
Consider the fuel line's flexibility and durability when choosing the routing path. The line should be able to move freely without excessive bending or kinking, which can lead to stress points and potential leaks. Allow for some slack in the routing to accommodate slight movements during vehicle operation. Secure the fuel line using appropriate ties or clips to prevent it from becoming a trip hazard or interfering with other components.
In areas where the fuel line passes through the engine compartment or other enclosed spaces, ensure proper ventilation. This is essential to prevent the buildup of volatile fuel vapors, which can pose health and safety risks. Proper ventilation also helps to dissipate any potential heat generated by the engine, further protecting the fuel line.
By following these routing guidelines, you can ensure that the fuel line is safely and effectively reconnected, minimizing the risk of fuel-related issues and maintaining the overall integrity of the vehicle's fuel system. Remember, proper routing is a critical aspect of fuel line maintenance and should be given careful attention during the reconnection process.
Fuel Line Fixes: A Step-by-Step Guide for Your 2002 Ford Ranger
You may want to see also
Testing: Verify the connection's integrity by checking for leaks and proper flow
When reconnecting a fuel line, it's crucial to ensure that the connection is secure and leak-free to prevent any potential issues. Here's a step-by-step guide on how to test the integrity of the connections:
- Visual Inspection: Start by visually examining the fuel line connections. Look for any signs of damage, corrosion, or debris around the fittings. Ensure that all components are clean and free from any obstructions. Pay close attention to the threads and seals, as these areas are critical for a proper seal.
- Leak Test: The most important step is to check for leaks. You can use a simple leak-down test by applying a small amount of fuel or a suitable dye to the connections. Carefully observe the area around the fittings and look for any signs of fuel escaping. If you notice any leaks, it indicates a potential issue with the connection or the quality of the fitting. Tighten or replace the affected parts as necessary.
- Pressure Test (Optional): For added assurance, you can perform a pressure test. This method involves attaching a pressure gauge to the fuel line and applying a controlled amount of pressure. If the system is designed for this test, you should hear a hissing sound or see bubbles forming, indicating an intact seal. If no sound or bubbles are heard, it suggests a potential leak or faulty connection.
- Flow Test: To ensure proper fuel flow, you can use a fuel flow meter or a similar tool. Connect the meter to the fuel line and measure the flow rate. Compare the reading with the expected or recommended flow for your vehicle. If the flow is significantly different, it may indicate a restriction or blockage in the line, requiring further investigation.
- Re-check Connections: After testing, re-evaluate the connections to ensure they are tight and secure. Use the appropriate tools to tighten any loose fittings, but be careful not to overtighten, as this can cause damage. Double-check that all components are aligned and properly seated.
Remember, proper testing is essential to guarantee a safe and efficient fuel system. By following these steps, you can identify and address any potential issues before they cause problems during operation. Always refer to your vehicle's manual for specific instructions and recommendations regarding fuel line maintenance and testing.
Winter Fuel Line Freeze: Prevention Tips for Cold Climates
You may want to see also
Frequently asked questions
If you notice that your fuel line is disconnected or has come loose, it's important to address the issue promptly. Start by identifying the cause of the disconnection, which could be due to a damaged line, a loose fitting, or a faulty fuel pump. Then, carefully reconnect the fuel line by ensuring it is properly aligned and securely attached to the fuel pump and the engine. Use the appropriate tools and torque specifications to avoid over-tightening.
To prevent damage to the fuel line during installation, it's crucial to handle it with care. Avoid kinking or bending the line excessively, as this can lead to reduced fuel flow or even a complete blockage. Keep the line as straight as possible and use fuel line clips or ties to secure it in place, ensuring it doesn't rub against sharp edges or hot surfaces.
Yes, you'll typically need a few essential tools to reconnect a fuel line. These include a fuel line cutter or a pair of sharp scissors to trim the line to the correct length, a fuel line crimping tool or a pair of pliers to secure the fittings, and a fuel line cleaner to ensure a proper seal. It's also a good idea to have a fuel line inspection kit to check for any leaks or damage before and after the reconnection process.
Fuel line disconnections can occur due to various reasons. Common causes include age-related deterioration, corrosion, or damage from previous repairs. Over time, fuel lines can develop cracks or become brittle, leading to leaks or disconnections. Additionally, improper installation, such as using the wrong type of fuel line or fittings, can also result in disconnections. Regular maintenance and inspections can help identify and prevent these issues.