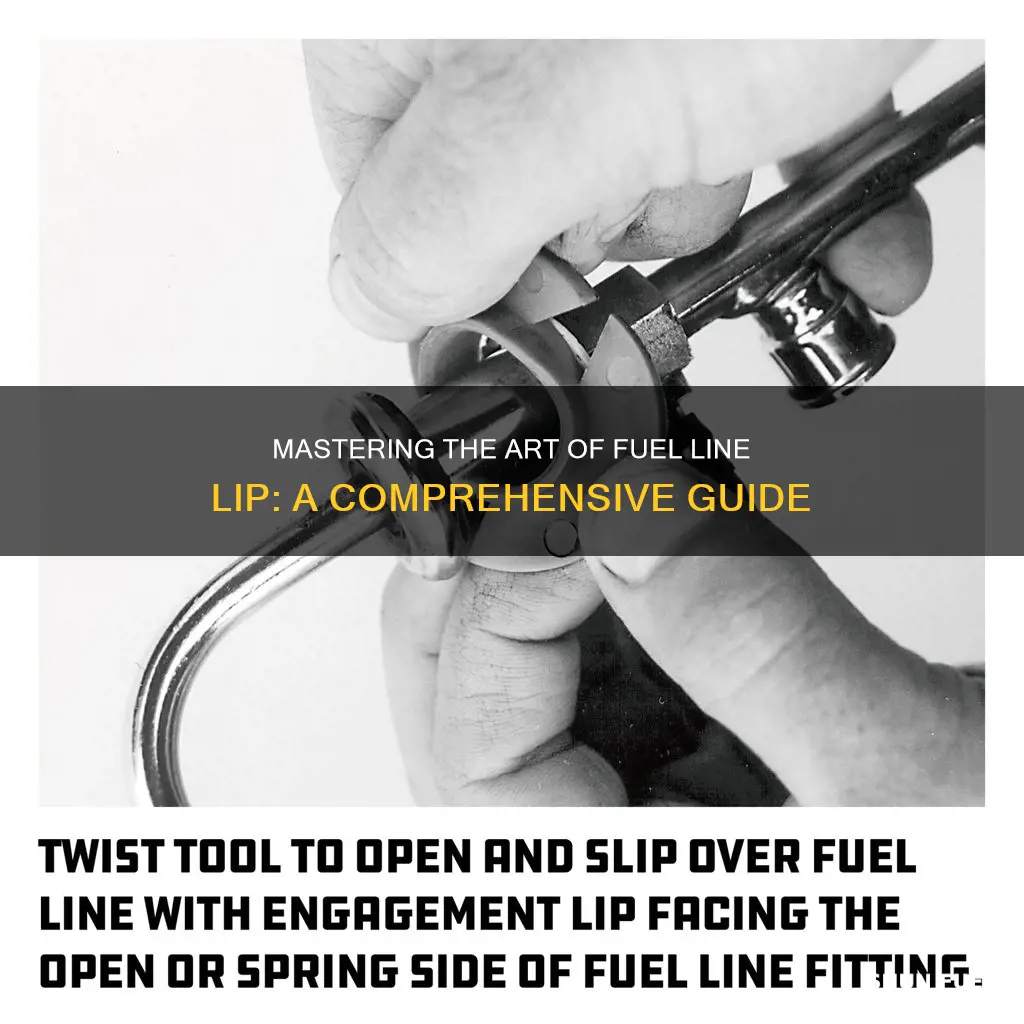
Making a lip on a fuel line is a crucial step in ensuring a secure and leak-free connection between the fuel tank and the engine. This process involves creating a small, raised edge on the fuel line to prevent it from slipping out of the fuel tank's opening. By following a few simple steps, you can easily create a lip on a fuel line, ensuring a reliable and safe fuel supply for your vehicle.
What You'll Learn
- Fuel Line Material: Choose the right material for the fuel line, considering durability and compatibility with fuel type
- Fitting Techniques: Learn various methods for connecting the fuel line to the engine, ensuring a secure and leak-free seal
- Bending and Routing: Understand how to bend and route the fuel line to fit the vehicle's layout without kinks
- Clamping and Securing: Discover proper clamping techniques to hold the fuel line in place, preventing leaks and damage
- Testing and Inspection: Learn how to test the fuel line for leaks and ensure proper functionality after installation
Fuel Line Material: Choose the right material for the fuel line, considering durability and compatibility with fuel type
When it comes to choosing the right material for your fuel line, it's crucial to consider the specific requirements of your fuel system and the type of fuel it will carry. The material selection is vital to ensure the longevity and reliability of your fuel delivery system. Here's a detailed guide to help you make the right choice:
Durability and Flexibility: Fuel lines need to withstand various environmental conditions and potential impacts. Look for materials that offer excellent durability and flexibility. Rubber, for instance, is a popular choice due to its ability to absorb vibrations and provide a certain level of flexibility. It can handle temperature fluctuations and is resistant to most fuels, making it a versatile option. However, keep in mind that rubber may not be suitable for high-pressure applications or in the presence of certain chemicals.
Compatibility with Fuel Type: Different types of fuels require specific materials to ensure compatibility and prevent degradation. For example, gasoline fuel lines often use rubber or vinyl, as these materials can withstand the volatility of gasoline. On the other hand, diesel fuel lines might utilize rubber or a specialized material like ethylene propylene rubber (EPR), which offers enhanced resistance to the higher temperatures and pressures associated with diesel. Always refer to the fuel manufacturer's guidelines to determine the recommended material for your specific fuel type.
Temperature and Pressure Considerations: The operating conditions of your fuel system play a significant role in material selection. If your vehicle operates in extreme temperatures, consider materials with superior temperature resistance, such as silicone or EPR. These materials can handle both high and low temperatures without compromising performance. Additionally, for high-pressure applications, ensure the chosen material can withstand the pressure without becoming brittle or leaking.
Chemical Resistance: Different fuels contain various additives and chemicals. It's essential to choose a material that is resistant to these substances to prevent corrosion or degradation. For instance, ethanol-blended fuels may require materials with enhanced resistance to ethanol's corrosive properties. Always research the specific chemicals present in your fuel and select a material that can withstand their effects.
Standard Sizes and Fittings: Ensure that the chosen material comes in standard sizes and fittings to facilitate easy installation and compatibility with your vehicle's fuel system. Standardized dimensions will make the repair or replacement process more straightforward.
By carefully considering the durability, compatibility, and specific requirements of your fuel system, you can select the appropriate material for your fuel line. This ensures a reliable and efficient fuel delivery system, contributing to the overall performance and longevity of your vehicle. Remember, consulting the manufacturer's guidelines and seeking professional advice can provide further insights tailored to your specific fuel line application.
Troubleshooting Tips: When the Fuel Line Refuses to Uncouple
You may want to see also
Fitting Techniques: Learn various methods for connecting the fuel line to the engine, ensuring a secure and leak-free seal
When it comes to connecting the fuel line to the engine, ensuring a secure and leak-free seal is crucial for optimal performance and safety. Here are some fitting techniques to achieve this:
- Compression Fitting: This method involves using a compression fitting, which consists of a ferrule (a metal or rubber ring) and a nut. The fuel line is inserted into the ferrule, and the nut is tightened around it, compressing the ferrule and creating a tight seal. This technique is commonly used for fuel lines due to its simplicity and reliability. Ensure that the ferrule is the correct size for the fuel line diameter and that the nut is tightened evenly to avoid damage to the line.
- Clamp-Style Fitting: Clamp-style fittings offer a quick and effective way to connect fuel lines. These fittings typically feature a metal or plastic body with a clamp on one end. The fuel line is inserted into the body, and the clamp is tightened securely around the line, creating a compression seal. This method is especially useful when working with flexible fuel lines. Make sure the clamp is tightened firmly but not excessively to prevent damage to the line.
- Crimping Technique: Crimping is a more advanced fitting method that involves using a special tool to compress a ferrule onto the fuel line. The ferrule is placed over the line, and the tool is applied to create a tight, secure seal. This technique is often used for high-pressure fuel lines and provides a robust connection. It requires precision and the right tools, but it ensures a long-lasting and leak-free seal.
- Soldering (for Copper Lines): If you're working with copper fuel lines, soldering can be an effective fitting technique. This method involves soldering the fuel line to the engine block or other components. It requires careful preparation, including cleaning the surfaces and applying flux to ensure a strong bond. Soldering creates a permanent seal and is ideal for high-temperature and pressure applications. However, it is a more complex process and should be done with proper safety precautions.
Each fitting technique has its advantages and is chosen based on the specific requirements of the fuel line and engine setup. It's essential to follow manufacturer guidelines and best practices to ensure a proper seal and avoid potential issues like fuel leaks or reduced engine performance. Regular inspection and maintenance of these connections are also recommended to identify and address any potential issues early on.
Step-by-Step Guide: Removing the Fuel Line on Your 2007 Chevy Suburban
You may want to see also
Bending and Routing: Understand how to bend and route the fuel line to fit the vehicle's layout without kinks
When working on a fuel line installation, bending and routing the line properly is crucial to ensure a safe and efficient setup. Here's a step-by-step guide to help you master this process:
Understanding the Layout: Begin by thoroughly examining the vehicle's interior layout. Identify the areas where the fuel line needs to pass through, such as engine compartments, dashboards, or under seats. Understanding the path the line will take is essential to avoid any obstructions or potential damage.
Gathering the Tools: Before starting, ensure you have the necessary tools for bending and routing. This includes a fuel line bender, which is a specialized tool designed to create smooth bends without kinking the line. You'll also need a pair of sharp scissors or a fuel line cutter to make precise cuts.
Bending the Fuel Line: Start by laying out the fuel line on a flat surface. Identify the points where you need to make bends to accommodate the vehicle's structure. Use the fuel line bender to create gentle, 90-degree bends at these points. Avoid forcing the line, as it can lead to kinks and potential leaks. Take your time and ensure each bend is smooth and consistent.
Routing the Line: Once the fuel line is bent to the desired shape, it's time to route it through the vehicle. Carefully guide the line along the identified path, ensuring it doesn't come into contact with any sharp edges or moving parts that could cause damage. Use ties or clips to secure the line in place, allowing it to follow the natural contours of the vehicle's interior.
Avoiding Kinks: The key to a successful installation is to prevent kinks. Kinks can restrict fuel flow and potentially cause damage over time. Always bend the line at a gentle angle, avoiding sharp bends that could create stress points. If you encounter a particularly tight space, consider using a flexible fuel line adapter to navigate the obstacle without compromising the line's integrity.
By following these steps, you can ensure that the fuel line is bent and routed correctly, fitting seamlessly into the vehicle's layout without any unnecessary kinks or strain. This attention to detail will contribute to a reliable and safe fuel system.
Mastering the Art: Plastic Fuel Line to Steel Fitting Connection
You may want to see also
Clamping and Securing: Discover proper clamping techniques to hold the fuel line in place, preventing leaks and damage
When working with fuel lines, proper clamping and securing techniques are crucial to ensure a safe and efficient system. Clamps play a vital role in holding the fuel line in place, preventing leaks, and minimizing the risk of damage. Here's a detailed guide on achieving this:
Understanding the Clamping Process:
Start by familiarizing yourself with the specific fuel line and clamp types you're working with. Different fuel lines may require unique clamp designs to ensure a secure fit. Consider the material of the fuel line and the clamp's compatibility. For instance, some fuel lines might be made of rubber or plastic, while others could be metal, each requiring a tailored clamping approach.
Selecting the Right Clamp:
Choose a clamp that is appropriately sized for the fuel line's diameter. A well-fitted clamp should provide a tight seal without causing damage to the fuel line. Common types of clamps include hose clamps, band clamps, and clip-on clamps. Hose clamps, for example, are versatile and can be tightened to secure the fuel line firmly. Ensure the clamp material is compatible with the fuel line's material to avoid any adverse reactions.
Proper Clamping Technique:
- Position the fuel line in the desired location, ensuring it is straight and free of any sharp bends that could cause stress.
- Slide the clamp onto the fuel line, positioning it at the desired attachment point.
- Tighten the clamp securely by turning it clockwise. Start with a firm grip and gradually increase the tension to avoid over-tightening, which can damage the fuel line.
- Test the clamp's tightness by gently pulling on the fuel line. It should feel snug, but not overly tight, to ensure a secure hold.
- Repeat this process at regular intervals along the fuel line's length to create multiple attachment points, providing additional support and leak prevention.
Preventing Leaks and Damage:
Proper clamping is essential to prevent fuel leaks, which can be dangerous and costly. Ensure that all connections are tight and secure. Regularly inspect the clamps for any signs of wear or damage, especially in areas exposed to vibration or extreme temperatures. Replace worn-out clamps to maintain the integrity of the fuel system. Additionally, avoid using excessive force when tightening clamps, as this can lead to fuel line damage and potential leaks.
By following these clamping and securing techniques, you can effectively hold the fuel line in place, ensuring a reliable and safe fuel system. Remember, proper installation and regular maintenance are key to preventing leaks and damage, ultimately contributing to the overall performance and longevity of your vehicle's fuel system.
Can Fuel Tank Fuel Lines Fuel a Car's Performance?
You may want to see also
Testing and Inspection: Learn how to test the fuel line for leaks and ensure proper functionality after installation
When installing a fuel line, ensuring its integrity and functionality is crucial to prevent leaks and potential engine issues. Here's a step-by-step guide on how to test and inspect the fuel line for leaks and proper operation:
- Visual Inspection: Begin by thoroughly examining the fuel line for any visible signs of damage or defects. Look for cracks, punctures, or any discolored areas along the length of the line. Inspect the connections and fittings for tightness and ensure they are free from any corrosion or debris. Pay close attention to the areas where the fuel line passes through any openings or openings in the engine bay, as these points are more susceptible to damage.
- Pressure Test: A pressure test is an effective method to identify potential leaks in the fuel line. You can use a fuel line pressure tester or a simple setup with a pump and gauge. Start by ensuring the fuel tank is full and the engine is off. Attach the pressure tester to the fuel line, ensuring a secure connection. Gradually increase the pressure in the line and monitor the gauge. A healthy fuel line should maintain pressure without any significant drops. If you notice a drop in pressure, it indicates a potential leak, and further investigation is required.
- Bubble Test: This test is particularly useful for detecting leaks around connections and fittings. Fill the fuel line with a small amount of water and carefully observe for any bubbles. If you notice bubbles forming, it suggests that there is a leak or a faulty connection. This method is simple yet effective in identifying issues that might not be visible during a visual inspection.
- Engine Operation: After the initial inspection and testing, it's essential to start the engine and monitor its performance. Run the engine at idling speed and listen for any unusual noises, such as hissing or whistling, which could indicate a fuel leak. Check for any signs of fuel vapor or smoke around the engine bay, especially near the fuel line connections. If the engine runs smoothly and without any fuel-related issues, it is a good indication that the fuel line is functioning correctly.
- Final Inspection: Once the engine has cooled down, perform a final visual inspection of the fuel line. Look for any signs of fuel accumulation or staining, which could indicate a previous leak. Ensure all connections are tight and secure. If you have access to a fuel pressure gauge, you can also measure the pressure at the fuel pump to ensure it meets the manufacturer's specifications.
By following these testing and inspection procedures, you can ensure that the fuel line is installed correctly and functions optimally, minimizing the risk of fuel-related issues and potential engine damage. Regular maintenance and inspections are key to keeping your vehicle's fuel system reliable.
Mastering the Art of Soldering Fuel Lines: A Comprehensive Guide
You may want to see also
Frequently asked questions
A lip on a fuel line, also known as a fuel line lip or boot, serves as a protective covering to shield the fuel line from potential damage caused by friction, heat, or sharp objects. It helps to ensure the fuel line's longevity and prevents leaks.
To determine the appropriate length, measure the fuel line's circumference and add a few extra inches for a secure fit. Consider the lip's thickness and ensure it covers the entire fuel line, providing adequate protection.
It's recommended to use materials like rubber, silicone, or vinyl for the lip, as these are durable and flexible. These materials can withstand fuel's corrosive nature and provide effective protection.
You will typically need a pair of pliers or a fuel line tool to grip the lip and fuel line securely. Additionally, a small amount of fuel line adhesive or tape can be used to ensure a tight and leak-free connection.
Regularly inspect the lip for any signs of wear, cracks, or damage. Replace it if necessary, especially after any fuel line repairs or replacements, to maintain optimal protection and prevent fuel leaks.