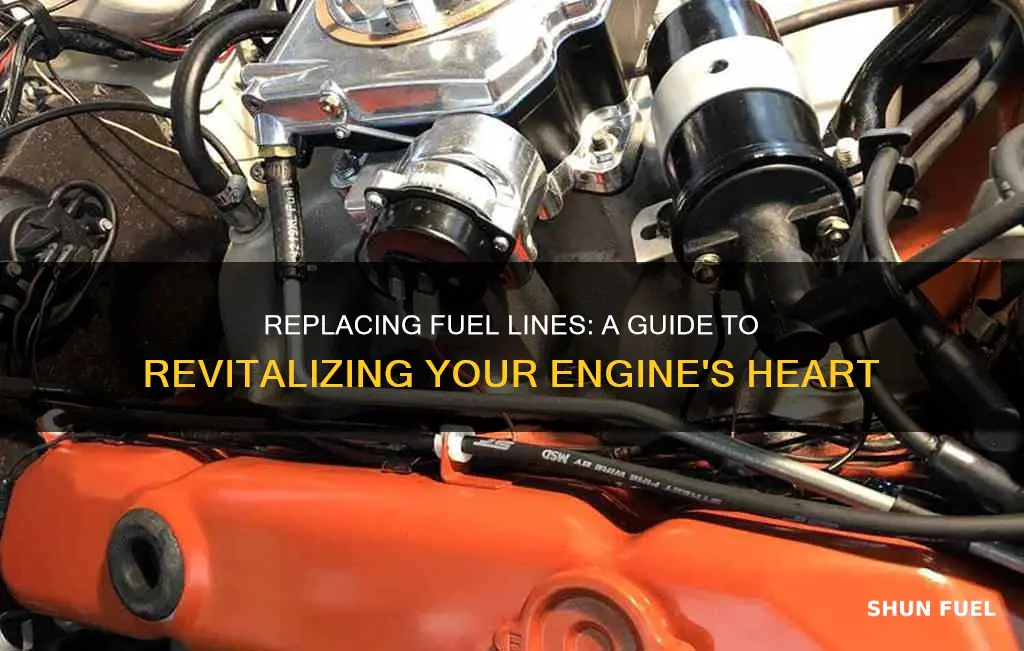
Replacing a damaged fuel line in a vehicle can be a challenging task, especially when dealing with rubble. This guide will provide a step-by-step approach to replacing the fuel line, ensuring a safe and efficient process. It is crucial to understand the specific make and model of the vehicle to ensure the correct parts are used. The process involves identifying the damaged section, removing the old line, and carefully installing the new one, ensuring all connections are secure and properly sealed to prevent fuel leaks. Safety precautions, such as wearing protective gear and working in a well-ventilated area, are essential to avoid inhaling harmful fumes.
What You'll Learn
- Identify the damaged section: Locate the affected area of the fuel line using visual inspection and pressure testing
- Prepare the replacement: Ensure you have the correct replacement part and necessary tools for the specific make and model
- Remove the old line: Carefully disconnect and extract the damaged fuel line, being mindful of any connections or clips
- Install the new line: Route the replacement line through the appropriate channels, securing it with clips or ties
- Test and verify: Check for leaks and proper functionality by starting the engine and monitoring for any issues
Identify the damaged section: Locate the affected area of the fuel line using visual inspection and pressure testing
When dealing with a damaged fuel line, the first crucial step is to accurately identify the affected section. This process involves a combination of visual inspection and pressure testing to ensure you pinpoint the exact location of the issue.
Visual inspection is a straightforward initial approach. Carefully examine the fuel line for any visible signs of damage, such as cracks, punctures, or corrosion. Look for areas where the line may have been cut, damaged by sharp objects, or affected by extreme temperatures. Pay close attention to any discolored or swollen areas, as these could indicate internal damage or the presence of contaminants. If you notice any of these visual indicators, it's essential to proceed with further investigation to confirm the extent of the damage.
Pressure testing is a more advanced method used to identify internal damage or leaks in the fuel line. This test involves applying pressure to the fuel system and monitoring for any leaks. Here's how you can perform it:
- Ensure the vehicle is parked on a level surface and the engine is off.
- Locate the fuel line and identify the section you suspect might be damaged.
- Use a mechanical gauge or a specialized fuel line pressure tester to apply pressure to the fuel system. Start with a low pressure and gradually increase it while monitoring for any signs of leakage.
- Check for any hissing sounds or the presence of fuel on the ground or nearby surfaces, indicating a potential leak.
- If a leak is detected, mark the location and take detailed notes for further reference during the repair process.
By combining visual inspection and pressure testing, you can effectively pinpoint the damaged section of the fuel line. This accurate identification is crucial for ensuring that the replacement process is targeted and successful, minimizing the risk of further issues.
Mastering Aircraft Fuel Line Flushing: A Comprehensive Guide
You may want to see also
Prepare the replacement: Ensure you have the correct replacement part and necessary tools for the specific make and model
When replacing a fuel line in a vehicle, it's crucial to start by preparing the necessary components and tools. Begin by sourcing the correct replacement part that is compatible with your specific make and model. This ensures a proper fit and functionality. Check the vehicle's manual or online resources to identify the specific fuel line specifications, including dimensions, material, and any unique features. Having the right part from the outset will make the replacement process smoother and more efficient.
Gather the required tools and equipment. This may include wrenches, pliers, fuel line cutters, and possibly a fuel line crimper, depending on the complexity of the replacement. Ensure you have the appropriate sizes and types of tools to handle the fuel line and any associated components. It's also beneficial to have a fuel catch can or container to collect any residual fuel during the process, preventing spills and ensuring a clean work area.
Before proceeding, inspect the existing fuel line for any visible damage or wear. This initial assessment will help you understand the extent of the replacement needed and ensure you have the correct replacement part. If there are any minor issues, such as small punctures or leaks, you might be able to repair them temporarily, but for a proper fix, a replacement is often necessary.
Organize your workspace to have all the necessary components and tools within reach. This includes laying out the replacement fuel line, any necessary fittings or adapters, and the tools you plan to use. A well-organized workspace will streamline the replacement process, making it more efficient and reducing the risk of errors.
By taking the time to prepare and ensure you have the correct replacement part and tools, you set the foundation for a successful fuel line replacement. This preparation step is often overlooked but is essential to the overall success of the repair, ensuring a safe and efficient fuel system in your vehicle.
Understanding Ford Fuel Line Valves: A Comprehensive Guide
You may want to see also
Remove the old line: Carefully disconnect and extract the damaged fuel line, being mindful of any connections or clips
When replacing a damaged fuel line, one of the crucial steps is to carefully remove the old line. This process requires precision and attention to detail to ensure that no damage is done to the surrounding components. Here's a step-by-step guide to help you through this task:
Start by identifying the damaged fuel line and its connections. Locate the line's entry point into the fuel tank or the engine compartment. It is often secured by clips or brackets, so identify these attachment points. Use the appropriate tools to loosen and remove these clips or brackets, being cautious not to force them to avoid damaging the surrounding components. Once the clips or brackets are removed, you should have access to the fuel line.
Now, carefully disconnect the fuel line from any fittings or connections. These connections might include fuel injectors, carburetors, or fuel pumps. Use a fuel line disconnect tool or a pair of pliers to carefully release the fittings. Take note of the orientation of the connections to ensure proper reassembly later. As you disconnect the line, be mindful of any fuel that might spill, especially if the line is still slightly pressurized. Have a container ready to catch any fuel that may leak.
With the connections released, you can now extract the damaged fuel line. Gently pull the line away from the fittings, maintaining a steady grip to avoid pulling on any other connected components. If the line is particularly stubborn, you may need to use a fuel line cutter to carefully sever the line at the desired point. Once the old line is completely removed, you can proceed with the installation of the new fuel line.
Remember, the key to successfully replacing a fuel line is patience and attention to detail. Take your time to carefully disconnect and extract the old line, being mindful of all connections and potential fuel leaks. This approach will help ensure a smooth and safe repair process.
Hayabusa Fuel Line Removal: A Step-by-Step Guide for 2003 Models
You may want to see also
Install the new line: Route the replacement line through the appropriate channels, securing it with clips or ties
When replacing a damaged fuel line, it's crucial to properly install the new line to ensure optimal performance and safety. Here's a step-by-step guide on how to install the replacement line:
Step 1: Route Planning
Before you begin, carefully inspect the vehicle's fuel system layout and identify the appropriate channels through which the new line will pass. This might involve tracing the existing fuel lines, consulting the vehicle's manual, or referring to a detailed diagram. Proper routing ensures the line is secure, avoids interference with other components, and maintains the integrity of the fuel system.
Step 2: Gathering Materials
You'll need a few essential tools and materials for the installation:
- New fuel line: Ensure it's the correct size, material (usually rubber or vinyl), and length for your specific vehicle.
- Clips or ties: These are used to secure the line in place. Choose the appropriate size and material based on the vehicle's specifications.
- Fuel line connectors: These are used to join the new line to the existing fuel system and the fuel tank.
- Fuel line cleaner: This is used to ensure a clean and secure connection.
Step 3: Installation Process
- Prepare the New Line: Carefully inspect the new fuel line for any damage or defects. Ensure it's free of kinks and ready for installation.
- Connect to the Fuel Tank: Using the appropriate fuel line connectors, securely attach the new line to the fuel tank outlet. Follow the manufacturer's instructions for connector installation.
- Route the Line: Carefully guide the new line through the identified channels. Use clips or ties to secure it at regular intervals. This prevents the line from becoming loose or damaged during vehicle operation.
- Connect to the Engine: Continue routing the line until it reaches the engine. Securely connect the line to the engine's fuel rail or carburetor using the appropriate connectors.
- Final Adjustments: Once all connections are made, double-check for any leaks. Tighten any loose clips or ties.
Important Safety Note:
- Fuel Line Handling: Always handle fuel lines with care. Avoid sharp bends or kinks, as these can lead to fuel leaks.
- Leak Testing: After installation, start the engine and check for any fuel leaks. If a leak is detected, immediately disconnect the line and seek professional assistance.
By following these steps and exercising caution throughout the process, you can successfully install a new fuel line and ensure your vehicle's fuel system operates safely and efficiently.
Poulan Pro's Unique Fuel Line: Unlocking the Mystery
You may want to see also
Test and verify: Check for leaks and proper functionality by starting the engine and monitoring for any issues
When replacing a fuel line, it's crucial to test and verify the system to ensure it's functioning correctly and there are no leaks. Here's a step-by-step guide to help you through this process:
Step 1: Prepare the Vehicle
Before starting the engine, ensure the vehicle is in a safe and stable position. Park it on a level surface and engage the parking brake. This step is essential for safety and to prevent any accidental movement during the testing process.
Step 2: Inspect the Fuel Line Connections
Carefully inspect the fuel line connections, including the fittings and clamps. Look for any signs of damage, corrosion, or deterioration. Ensure that all connections are tight and secure. If you notice any issues, address them before proceeding with the testing.
Step 3: Start the Engine
With the vehicle in the prepared state, start the engine. Pay close attention to any unusual noises or vibrations. A properly functioning fuel system should operate smoothly without any excessive sounds. Listen for any hissing or whistling noises, which could indicate a fuel leak.
Step 4: Monitor for Leaks
While the engine is running, visually inspect the fuel line for any signs of leaks. Check for wet spots or stains on the ground beneath the vehicle, especially around the fuel tank and lines. Also, look for any fuel vapor escaping from the lines or connections. If you notice any leaks, it's essential to identify the source and address it promptly.
Step 5: Check for Proper Functionality
In addition to leak detection, monitor the engine's performance during this test. Ensure that the engine starts easily and runs smoothly at various speeds. Check for any unusual behavior, such as stalling, hesitation, or erratic performance, which could indicate a problem with the fuel system.
Step 6: Revise and Re-test
If any issues are identified during the test, you may need to revise the replacement process and re-test. This could involve tightening loose connections, replacing damaged components, or re-routing the fuel line. Always ensure that all work is done correctly and securely before proceeding with the final verification.
Remember, thorough testing and verification are critical to ensuring the reliability and safety of your vehicle's fuel system after replacing a damaged fuel line.
Car Fuel Line: Loop or No Loop? Unraveling the Mystery
You may want to see also
Frequently asked questions
The initial step is to identify the specific fuel line that requires replacement. Peace of Rubble fuel lines are typically found in older vehicles or those with a unique design. It's essential to consult the vehicle's manual or seek professional advice to ensure you're replacing the correct part.
While some DIY enthusiasts might attempt fuel line replacement, it is generally recommended to have a professional mechanic handle this task. Fuel lines require precise installation, and any mistake could lead to fuel leaks, which pose safety risks. Mechanics have the necessary tools and expertise to ensure a secure and safe replacement.
The time required for the replacement depends on various factors, including the vehicle's make and model, the accessibility of the fuel line, and the mechanic's experience. On average, replacing a fuel line can take anywhere from 1 to 3 hours, but it's best to consult with a mechanic to get an accurate estimate for your specific vehicle.
Yes, it's advisable to gather the necessary tools and materials beforehand. This may include fuel line cutters, crimping tools, wrenches, and the replacement fuel line itself. Having these items ready will streamline the replacement process and ensure you have everything needed to complete the task efficiently.