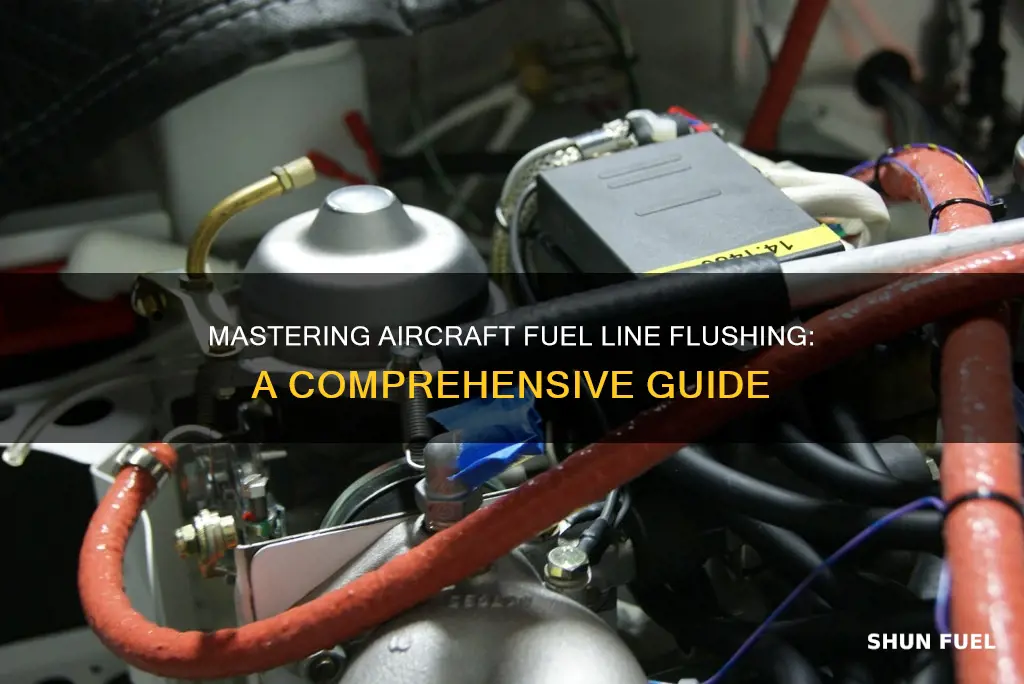
Flushing aircraft fuel lines is a critical maintenance procedure to ensure the integrity and performance of an aircraft's fuel system. This process involves removing contaminants and debris from the fuel lines to prevent potential issues such as fuel contamination, engine performance degradation, and safety hazards. The procedure typically involves using a specialized flushing system that injects a cleaning fluid through the fuel lines, dislodging any accumulated contaminants. It is essential to follow manufacturer guidelines and use the correct cleaning agents to avoid damage to the fuel system components. Proper flushing helps maintain the aircraft's fuel quality, ensuring optimal engine performance and safety during flights.
What You'll Learn
- Pre-flight Preparation: Ensure fuel lines are clean and debris-free before starting the process
- Fuel Type Identification: Verify the type of fuel used to select the correct flushing method
- Flushing Agent Selection: Choose an appropriate flushing agent based on fuel type and system compatibility
- Pressure and Flow Control: Maintain consistent pressure and flow rates during the flushing process
- Post-flush Inspection: Inspect fuel lines for any remaining contaminants and ensure proper drainage
Pre-flight Preparation: Ensure fuel lines are clean and debris-free before starting the process
Before embarking on the fuel line flushing process, it is crucial to prioritize pre-flight preparation to ensure a thorough and effective cleaning. This initial step is often overlooked but plays a vital role in maintaining the integrity of the aircraft's fuel system. The primary objective is to remove any accumulated debris, contaminants, or old fuel that could potentially cause issues during the flight.
To begin, access the fuel lines and inspect them for any visible signs of damage, corrosion, or blockages. Use a bright flashlight to examine the lines for any debris or foreign objects that might have accumulated over time. Pay close attention to the areas where the lines connect to the fuel tanks and pumps, as these points are more susceptible to contamination. If any debris is found, employ a small brush or a compressed air nozzle to gently remove it, ensuring you don't damage the delicate fuel line material.
Next, prepare the cleaning solution. A common and effective method is to use a fuel line cleaner, which can be purchased from aviation supply stores. These cleaners are designed to dissolve and remove contaminants. Follow the manufacturer's instructions for the correct dilution ratio and application method. Typically, the cleaner is injected into the fuel line using a specialized tool, ensuring it reaches all areas of the line. Allow sufficient time for the cleaner to work, as some products may require a few minutes to dissolve and loosen the debris.
While the cleaner is doing its work, it is essential to prepare the aircraft's fuel system for the flushing process. This includes draining any old fuel from the system to prevent it from mixing with the new, cleaned fuel. Locate the fuel drain valves and open them to release the used fuel into an appropriate container. Ensure you follow all safety guidelines and regulations regarding fuel disposal. Once the draining is complete, close the valves and prepare for the next step.
After the cleaning agent has had time to act, it's time to flush the fuel lines. This process involves running the aircraft's engines or using a dedicated fuel pump to push the cleaning solution through the entire fuel system. The goal is to dislodge and remove any remaining debris and contaminants. Monitor the fuel lines and tanks during this process to identify and address any potential issues. Proper flushing ensures that the fuel lines are now free of debris and ready for the upcoming flight.
Blue Clips on Ford Fuel Lines: Quick Removal Tips
You may want to see also
Fuel Type Identification: Verify the type of fuel used to select the correct flushing method
When it comes to flushing aircraft fuel lines, identifying the type of fuel used is crucial to ensure the process is done correctly and safely. Different types of aviation fuels have varying properties and require specific flushing techniques to maintain the integrity of the fuel system. Here's a detailed guide on how to verify the fuel type and select the appropriate flushing method:
Understanding Aviation Fuels:
Start by familiarizing yourself with the different types of aviation fuels commonly used in aircraft. The two primary types are Jet-A and Jet-A1, which are kerosene-based fuels. Jet-A is a standard aviation fuel, while Jet-A1 is a more advanced version with improved cold-flow characteristics, making it suitable for colder climates. There are also synthetic aviation fuels, such as biofuels, which are derived from renewable sources and offer environmental benefits. Understanding these variations is essential for accurate fuel type identification.
Fuel Identification Methods:
- Visual Inspection: In some cases, you can identify the fuel type through visual cues. Jet-A fuel is typically clear or slightly colored, while Jet-A1 may have a slightly darker appearance. Synthetic fuels might have a different color or appearance, so visual inspection alone may not be sufficient.
- Fuel Sample Collection: Take a sample of the fuel from the aircraft's fuel tanks. This can be done using a fuel sample pump or by drawing a sample through the fuel lines. Send the sample to a laboratory for analysis to determine the fuel type and its properties.
- Fuel Card or Manual: Refer to the aircraft's fuel card or maintenance manual, which often provides information about the fuel type used in the specific aircraft model. These resources can guide you in selecting the correct flushing procedure.
Selecting the Correct Flushing Method:
Once you have identified the fuel type, you can proceed with the flushing process:
- Jet-A and Jet-A1 Fuels: For these fuels, a standard flushing procedure using a kerosene-based flush solvent is typically recommended. This method helps remove contaminants and ensures the fuel system is clean and ready for use.
- Synthetic Fuels: When dealing with synthetic aviation fuels, consider the specific properties of the fuel. Some synthetic fuels may require specialized flushing agents or techniques to ensure proper cleaning and maintenance. Always refer to the manufacturer's guidelines for synthetic fuels.
Remember, proper fuel type identification is critical to maintaining the aircraft's fuel system and ensuring safe operations. Always follow the manufacturer's recommendations and guidelines for flushing procedures to avoid any potential issues.
Mastering the Art of Fuel Line Blowout: A Comprehensive Guide
You may want to see also
Flushing Agent Selection: Choose an appropriate flushing agent based on fuel type and system compatibility
When it comes to flushing aircraft fuel lines, selecting the right flushing agent is crucial for ensuring the process is effective and safe. The choice of flushing agent depends on several factors, primarily the type of fuel used in the aircraft and the compatibility of the agent with the fuel system components. Here's a detailed guide on how to choose the appropriate flushing agent:
Understanding Fuel Types: Aircraft typically use different types of aviation fuels, such as Jet-A, Jet-A1, or aviation gasoline (AVGAS). Each fuel type has unique properties and requires specific flushing agents to effectively remove contaminants. For instance, Jet-A and Jet-A1 are kerosene-based fuels, while AVGAS is a leaded gasoline. Understanding the fuel type is the first step in selecting the right flushing agent.
Considering System Compatibility: The fuel system of an aircraft can be complex, consisting of various components like fuel tanks, lines, pumps, and filters. Some flushing agents may be more compatible with certain materials and components than others. For example, certain chemicals might be suitable for kerosene-based fuels but could potentially damage rubber seals or aluminum components. It is essential to choose a flushing agent that is compatible with all the materials used in the fuel system to prevent damage and ensure the process's success.
Flushing Agent Selection Criteria:
- Fuel Type Compatibility: Different flushing agents are designed for specific fuel types. For kerosene-based fuels, you might consider using a kerosene-based flushing agent, which is effective in dissolving and removing contaminants. For AVGAS, a leaded gasoline flushing agent is necessary to address the unique challenges associated with this fuel type.
- System Compatibility: Check the flushing agent's compatibility with the materials in your aircraft's fuel system. Manufacturers often provide guidelines or recommendations for specific agents. Ensure the agent is safe for use with the fuel lines, tanks, and other components to avoid any adverse effects.
- Effectiveness: Evaluate the flushing agent's ability to remove contaminants. Look for agents that have been proven to dissolve and remove water, debris, and other impurities from the fuel system. High-performance agents might be required for systems with a history of contamination issues.
Consultation and Research: It is advisable to consult the aircraft's maintenance manual or seek advice from aviation experts and fuel system manufacturers. They can provide specific recommendations based on the aircraft model and its fuel system design. Additionally, researching and comparing different flushing agents available in the market can help you make an informed decision.
Remember, the goal is to ensure that the flushing process effectively cleans the fuel lines, removes contaminants, and leaves the system in optimal condition. Choosing the right flushing agent is a critical step in achieving this goal and maintaining the aircraft's fuel system integrity.
Oil Line Swap: Can You Plug It into Your Fuel Pump?
You may want to see also
Pressure and Flow Control: Maintain consistent pressure and flow rates during the flushing process
When flushing aircraft fuel lines, maintaining consistent pressure and flow rates is crucial to ensure an effective cleaning process. This step is often overlooked, but it plays a vital role in removing contaminants and debris from the fuel system. Here's a detailed guide on how to achieve this:
Understanding the System: Begin by thoroughly understanding the aircraft's fuel system layout. This includes knowing the location of the fuel tanks, the fuel lines, and the various valves and filters involved. Each aircraft model may have unique configurations, so it's essential to refer to the manufacturer's guidelines and diagrams. Identify the points where pressure and flow can be controlled, such as valves, pumps, or pressure regulators.
Pressure Regulation: Consistent pressure is critical during the flushing process. Use a pressure gauge to monitor the pressure at the flushing point. The goal is to maintain a steady pressure within the optimal range specified by the manufacturer. If the pressure drops too low, it may not effectively dislodge contaminants. Conversely, excessive pressure can lead to damage or over-pressurization of the system. Adjust the flushing equipment's pressure settings accordingly and regularly check and calibrate the gauge to ensure accuracy.
Flow Control: Controlling the flow rate is equally important. A steady and controlled flow ensures that the entire fuel system is thoroughly flushed. Use a flow meter to measure the rate of fluid passing through the lines. Adjust the flushing equipment's flow control valves to maintain a consistent flow. The flow rate should be sufficient to dislodge debris but not so high that it causes excessive turbulence or damage to the fuel lines. Regularly monitor the flow to make adjustments as needed, especially if the flushing process takes an extended period.
Consistent Technique: Consistency is key. Maintain a steady flushing technique throughout the process. Avoid sudden changes in pressure or flow, as this can lead to uneven cleaning. Gradually increase or decrease pressure and flow rates when necessary, allowing the system to adapt. This controlled approach ensures that all fuel lines receive adequate cleaning without causing unnecessary stress on the system.
Regular Monitoring: Continuously monitor the pressure and flow during the flushing process. Make adjustments as required to maintain the desired levels. Regularly check for any signs of excessive wear or damage to the fuel lines and address them promptly. By closely observing these parameters, you can ensure a thorough and safe flushing operation.
Mastering the Art of Braiding Fuel Lines: A Comprehensive Guide
You may want to see also
Post-flush Inspection: Inspect fuel lines for any remaining contaminants and ensure proper drainage
After completing the fuel line flush, a thorough post-flush inspection is crucial to ensure the system is clean and ready for operation. This step is often overlooked but is essential for maintaining the integrity of the aircraft's fuel system. Here's a detailed guide on how to conduct this inspection:
Visual Inspection: Begin by visually examining the fuel lines. Look for any signs of contamination, such as dark or discolored fluid, debris, or residue. Contaminants can accumulate in the lines during the flushing process, and these visible indicators will help identify areas that require further attention. Inspect all connections, fittings, and bends for any blockages or signs of damage. Make sure to check both the interior and exterior of the lines to ensure a comprehensive evaluation.
Pressure Testing: Perform a pressure test to verify the integrity of the fuel lines and detect any potential leaks. Use a pressure gauge to apply a controlled amount of pressure to the system and observe for any drops or leaks. This test is critical as it helps identify weak points or damaged areas that might have been missed during the flushing process. Ensure that the pressure is released safely and according to manufacturer guidelines to avoid any accidents.
Drainage Check: Proper drainage is essential to remove any remaining contaminants. Inspect the fuel tanks and ensure they are drained completely. Check for any residual fluid in the system, as this could indicate incomplete flushing. Verify that all drains and outlets are functioning correctly, allowing for the smooth flow of fluid out of the system. This step might require additional tools, such as a suction device or a specialized drain kit, to ensure all contaminants are removed.
Documentation and Reporting: Document the inspection process and any findings. Create a detailed report outlining the condition of the fuel lines, including any identified issues. This documentation is vital for maintenance records and can help identify patterns or recurring problems. It also ensures that the inspection process is standardized and consistent across different aircraft.
By following these steps, you can effectively inspect the fuel lines post-flush, ensuring that the aircraft's fuel system is clean, functional, and ready for safe operation. Regular maintenance and attention to these details are key to preventing potential issues and maintaining the overall health of the aircraft.
Optimizing Performance: Choosing the Right Fuel Line for Your CT70 Engine
You may want to see also
Frequently asked questions
Over time, fuel lines can accumulate contaminants such as water, debris, and varnish, which can lead to reduced fuel flow, engine performance issues, and potential safety hazards. Regular flushing helps remove these contaminants and ensures the fuel system's optimal performance.
The process typically involves using a dedicated fuel line flushing system, which can be a portable or onboard unit. It involves connecting the flushing system to the fuel line, introducing a flushing fluid (often a detergent-based solution), and running the system to agitate and remove contaminants. This process may require multiple cycles and careful monitoring.
The frequency of flushing depends on various factors, including the aircraft's usage, environmental conditions, and maintenance schedule. As a general guideline, it is recommended to flush the fuel lines every 500-1000 hours of operation or annually, whichever comes first. Regular maintenance checks and consulting the aircraft's maintenance manual are essential to determine the appropriate flushing interval.
Yes, it is crucial to follow safety guidelines and instructions provided by the manufacturer. Ensure the aircraft is properly secured and the fuel system is isolated before starting the flushing process. Wear appropriate personal protective equipment (PPE) and be cautious of potential fuel leaks or spills. Proper ventilation is also important to avoid inhaling any fumes.
No, using regular engine oil or water is not recommended for fuel line flushing. These substances may not effectively remove contaminants and can leave behind residue or cause corrosion. It is essential to use specialized flushing fluids designed for aircraft fuel systems to ensure thorough cleaning and prevent potential damage to the fuel lines.