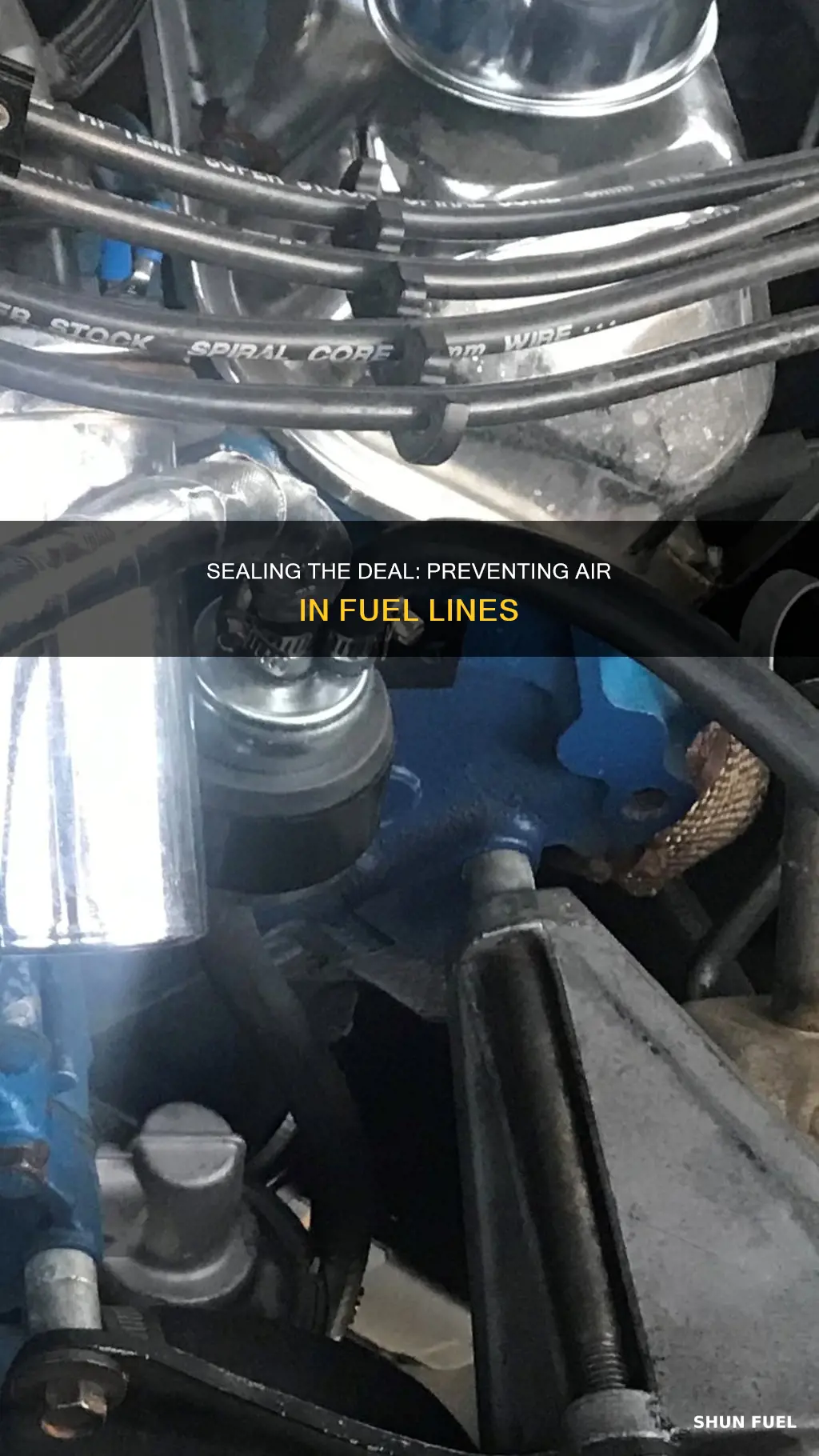
Ensuring that air doesn't enter the fuel line is crucial for maintaining the performance and longevity of a vehicle's engine. This guide will explore effective methods to prevent air intrusion, covering various techniques and best practices to keep the fuel system clean and efficient. By implementing these strategies, you can avoid potential issues caused by air bubbles, such as engine misfires and reduced power, ensuring a smooth and reliable driving experience.
What You'll Learn
- Fuel Line Material: Choose fuel-resistant materials to prevent air infiltration
- Sealing Mechanisms: Use effective seals and gaskets to block air entry
- Fuel Tank Design: Design tanks with tight seals to minimize air access
- Ventilation Control: Regulate fuel tank ventilation to prevent air intake
- Regular Maintenance: Inspect and maintain fuel lines to ensure air-tight connections
Fuel Line Material: Choose fuel-resistant materials to prevent air infiltration
When it comes to preventing air from entering the fuel line, the choice of material is crucial. The fuel line should be constructed using materials that are resistant to fuel degradation and can withstand the harsh conditions within the engine. One of the key properties to look for is the ability to resist fuel-related chemicals, which can cause corrosion and degradation over time.
A common and effective material for fuel lines is a high-quality rubber compound. Natural rubber has inherent fuel resistance, making it a suitable choice. It can withstand the presence of fuel without breaking down, ensuring a long-lasting and reliable fuel line. Additionally, rubber is flexible, allowing it to accommodate slight movements and vibrations within the engine, reducing the risk of damage.
Another option is to use synthetic materials specifically designed for fuel-carrying applications. These materials, such as fluororubber or neoprene, offer excellent resistance to fuel and its associated chemicals. They are often used in high-performance engines where fuel stability is critical. These synthetic rubbers can provide superior durability and resistance to aging, ensuring that the fuel line remains intact and functional over an extended period.
In some cases, a composite material, such as a rubber-reinforced plastic, can be an ideal choice. This material combines the flexibility of rubber with the strength and durability of plastic, providing a robust and fuel-resistant fuel line. The plastic component offers additional protection against fuel-related degradation, making it a reliable option for long-term use.
When selecting the material, it is essential to consider the specific fuel type and engine conditions. Different fuels may have varying effects on materials, so choosing a fuel-resistant option is vital. Proper material selection ensures that the fuel line remains intact, preventing air infiltration and potential engine issues. Regular inspection and replacement of the fuel line, especially in high-performance or high-mileage vehicles, can further enhance the prevention of air-related problems.
1975 Eldorado Fuel Line: Size Guide for Rubber Lines
You may want to see also
Sealing Mechanisms: Use effective seals and gaskets to block air entry
When it comes to preventing air from entering a fuel line, one of the most critical aspects is the use of effective sealing mechanisms. These components are designed to create a tight, airtight barrier between different parts of the fuel system, ensuring that air cannot infiltrate and cause issues. Here's a detailed look at how to utilize sealing mechanisms to achieve this goal:
Understanding the Importance of Seals and Gaskets:
Seals and gaskets are essential components in any fuel system, especially when it comes to preventing air intrusion. These items are typically made from materials that are resistant to fuel and air, ensuring they can withstand the corrosive nature of fuel over time. The primary function is to fill the gap between two surfaces, creating a continuous, airtight seal. This is crucial because even the smallest opening can allow air to enter, leading to potential performance issues and fuel contamination.
Types of Seals and Gaskets:
- O-Rings: These are commonly used in fuel lines and fittings. O-rings are circular and provide a flexible seal, adapting to slight movements and vibrations. They are often made from materials like rubber or silicone, which are resistant to fuel degradation.
- Gaskets: Gasketing is typically used for larger openings or joints. They can be made from various materials, including metal or rubber, and provide a more rigid seal. Gasketing is ideal for applications where there is a potential for more movement or pressure.
- Vacuum Seals: In some cases, a vacuum seal can be employed to create an airtight environment. This method is often used in high-performance applications where air intrusion must be minimized.
Installation and Placement:
Proper installation is key to ensuring the effectiveness of these sealing mechanisms. Here's a step-by-step guide:
- Clean the Surface: Before applying any seal or gasket, ensure the surfaces are clean and free of debris. This ensures a proper bond and prevents air from seeping through any contaminants.
- Precision Cutting: Cut the seal or gasket to the exact size required for the application. Precision is vital to ensure a tight fit.
- Alignment: Align the seal or gasket carefully, ensuring it is centered and properly positioned. Misalignment can lead to air leaks.
- Compression: For optimal performance, compress the seal or gasket slightly. This creates a firm, airtight seal, especially in high-pressure or vibration-prone areas.
- Regular Inspection: Regularly inspect the seals and gaskets for wear and tear. Over time, these components can degrade, and replacement may be necessary to maintain the integrity of the fuel system.
By implementing these sealing mechanisms and following the proper installation procedures, you can effectively block air from entering the fuel line, ensuring optimal performance and longevity of the fuel system. It is a critical step in maintaining a reliable and efficient fuel supply for any engine or machinery.
Amoutlander Fuel Line Diagram: A Comprehensive Guide
You may want to see also
Fuel Tank Design: Design tanks with tight seals to minimize air access
The design of fuel tanks plays a critical role in preventing air from entering the fuel lines, which can lead to various performance issues and potential safety hazards. One of the most effective methods to achieve this is by implementing tight seals within the tank's structure. These seals act as barriers, preventing air from seeping into the fuel system.
When designing the fuel tank, engineers should focus on creating a sealed environment. This involves using high-quality, flexible materials for the tank walls and ensuring that all seams and joints are meticulously sealed. The goal is to eliminate any potential pathways for air to infiltrate the tank. For instance, employing double-walled construction with an inner and outer layer can provide an additional layer of protection, making it harder for air to penetrate.
A key aspect of this design approach is the use of specialized gaskets and O-rings at critical points. These components should be made from materials that are compatible with the fuel and resistant to degradation over time. Proper installation and regular maintenance of these seals are essential to ensure their effectiveness. Over time, gaskets and O-rings may wear out or become compromised, allowing air to seep in, so regular inspections and replacements are necessary.
Furthermore, the tank's design should incorporate a breather system. This system allows air to enter the tank while maintaining a sealed environment for the fuel. A breather valve can be used to control the air-fuel mixture, ensuring that only the required amount of air enters the tank. This design feature is particularly important in high-performance engines where fuel efficiency and power output depend on precise air-fuel ratios.
In summary, fuel tank design with tight seals is a crucial step in preventing air from entering the fuel lines. By employing advanced sealing techniques, using compatible materials, and incorporating breathers, engineers can create a robust fuel system that ensures optimal engine performance and safety. Regular maintenance and inspections of these seals are also vital to guarantee their longevity and effectiveness.
Fuel Line Upgrades: Boosting Performance with Affordable Mods
You may want to see also
Ventilation Control: Regulate fuel tank ventilation to prevent air intake
Ventilation control is a critical aspect of maintaining a fuel system's integrity and performance. When it comes to preventing air intake into the fuel lines, managing the ventilation of the fuel tank is key. Here's a detailed guide on how to achieve this:
Understanding the Fuel Tank's Ventilation System:
The fuel tank's ventilation system is designed to allow the escape of vapors and gases while preventing the intake of air. This system typically consists of a small vent tube or pipe that connects the fuel tank to the atmosphere. It is crucial to ensure that this vent is properly sealed and positioned to maintain a positive pressure inside the tank. When the fuel level is low, the vent should allow the release of fuel vapors without allowing air to enter.
Regulating Ventilation:
- Vent Cap or Plug: One of the simplest methods is to use a vent cap or plug on the fuel tank. This cap should be designed to allow fuel vapor to escape while creating a tight seal to prevent air intake. Look for caps with a one-way valve mechanism that only opens when there is a higher pressure inside the tank, ensuring a controlled release of vapors.
- Vent Tube Positioning: Check the position of the vent tube. It should be positioned in a way that it is not easily accessible to contaminants or water. A submerged vent tube in a fuel tank, for example, can prevent water and debris from entering. Ensure the tube is long enough to allow proper ventilation without being a potential source of air intake.
- Breather Filters: Consider installing breather filters on the fuel tank. These filters are designed to allow fuel vapors to pass through while trapping contaminants and water. They create a barrier that prevents air from entering the system, ensuring a controlled environment for the fuel.
Maintenance and Inspection:
Regular maintenance and inspection of the fuel tank's ventilation system are essential. Over time, vents can become clogged with debris or damaged, leading to air intake. Inspect the vent lines and caps for any signs of damage or blockages and replace or repair them as needed. Additionally, keeping the fuel tank clean and free of contaminants is crucial to maintaining the integrity of the ventilation system.
By implementing these ventilation control measures, you can effectively regulate the fuel tank's environment, preventing air from entering the fuel lines and ensuring optimal fuel system performance. This approach is particularly useful in applications where fuel stability and longevity are essential, such as in aviation or marine environments.
Diesel Kleen: Effective Fuel Line Cleaner?
You may want to see also
Regular Maintenance: Inspect and maintain fuel lines to ensure air-tight connections
Regular maintenance of fuel lines is a critical aspect of vehicle care that can significantly impact performance and longevity. One of the primary concerns when it comes to fuel lines is the prevention of air intrusion, which can lead to a host of issues. To ensure air-tight connections and maintain the integrity of your fuel system, a proactive approach to maintenance is essential.
During routine inspections, it is crucial to check for any signs of damage, corrosion, or deterioration in the fuel lines. Over time, fuel lines can develop cracks, especially at connection points and bends. These cracks provide an entry point for air to infiltrate the system. Inspecting the lines for any visible damage and replacing any compromised sections is a vital step in preventing air from entering. Additionally, look for signs of corrosion, which can weaken the material and compromise its ability to form a tight seal.
Maintaining a regular cleaning schedule for the fuel lines is another essential practice. Accumulated dirt, debris, and contaminants can restrict fuel flow and create areas where air can become trapped. Using a fuel line cleaner or a compressed air system to blow out any debris can help ensure a clean and clear system. This process should be done carefully to avoid any damage to the fuel lines.
Checking and tightening connections is a simple yet effective maintenance task. Fuel lines are connected to various components, such as the fuel pump, injectors, and the tank. Over time, these connections can loosen due to vibration and movement within the engine. Looseness at these points can lead to air entering the system. Regularly inspect and tighten these connections to ensure a secure and air-tight bond. It is recommended to use a torque wrench to ensure the connections are tightened to the manufacturer's specifications.
Furthermore, monitoring the fuel pressure and system performance is an important part of regular maintenance. Air in the fuel lines can cause pressure fluctuations, leading to inconsistent fuel delivery and potential engine misfires. By regularly checking the fuel pressure and overall system performance, you can identify any issues related to air intrusion early on. This may involve using a fuel pressure gauge and comparing the readings to the vehicle's specifications.
In summary, regular maintenance of fuel lines is a proactive approach to preventing air-related issues. By inspecting for damage, keeping the lines clean, securing connections, and monitoring system performance, you can ensure that your fuel lines remain air-tight and efficient. This not only improves engine performance but also extends the lifespan of your vehicle's fuel system.
Mastering the Art of 2-Line Fuel Pump Installation: A Comprehensive Guide
You may want to see also
Frequently asked questions
One effective method is to ensure that the fuel tank is properly sealed and that there are no leaks or cracks in the tank or the fuel line itself. Regularly inspect the fuel system for any signs of damage or wear, and replace any faulty components immediately.
Air intrusion can occur due to various reasons such as a faulty fuel pump, a damaged fuel filter, or a loose fuel cap. Over time, fuel lines can also develop cracks or become brittle, allowing air to seep in. It's important to maintain and inspect these components regularly.
While fuel stabilizers can help maintain the quality of fuel over time, they are not a direct solution to prevent air from entering the fuel line. These products are designed to prevent fuel degradation and are typically used in long-term storage situations. For immediate prevention, it's best to address the source of the issue.
It is recommended to inspect your fuel system regularly, especially before and after long trips or if you notice any unusual behavior in your vehicle. Look for signs of fuel contamination, such as engine misfires or reduced performance, as these could indicate air entering the fuel line.
In emergency situations, you can temporarily block the fuel line with a rubber plug or a piece of cloth to prevent air from entering. However, this is a temporary solution and it's crucial to identify and fix the root cause as soon as possible to avoid further complications.