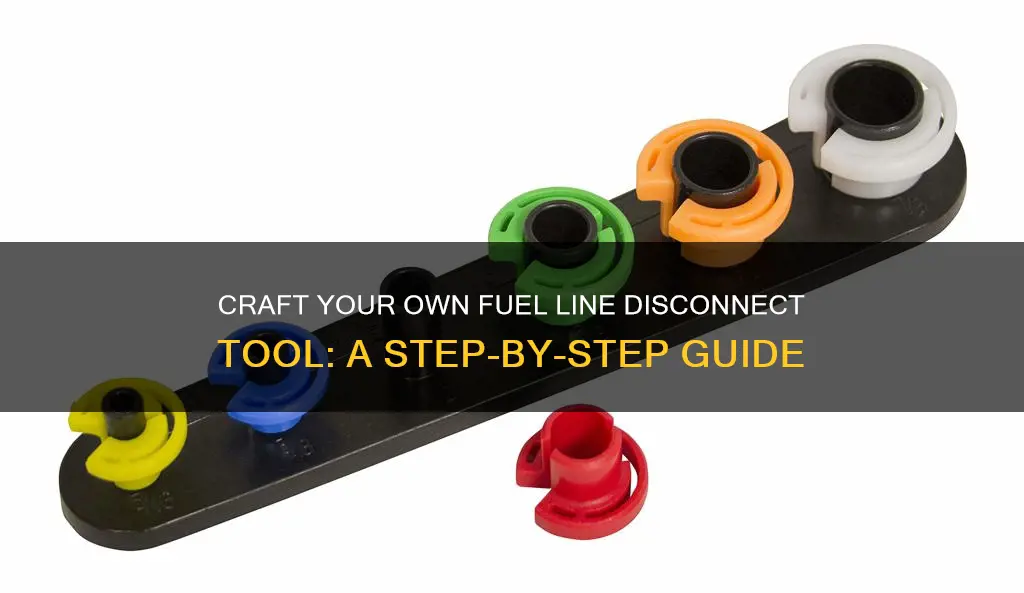
Creating your own fuel line disconnect tool can be a practical and cost-effective solution for vehicle maintenance. This guide will walk you through the process of building a simple, yet effective tool that can help you safely and efficiently disconnect fuel lines. By following these steps, you'll learn how to use basic tools and materials to construct a tool that can make your car repairs and maintenance tasks easier and safer.
What You'll Learn
- Materials and Tools: Gather metal pipe, wrenches, and pliers for construction
- Design and Blueprint: Create a blueprint for the tool's dimensions and angles
- Fabrication Process: Cut, bend, and assemble parts to form the disconnect tool
- Safety Features: Include a safety catch to prevent accidental disconnections
- Testing and Refinement: Test the tool's functionality and make adjustments for reliability
Materials and Tools: Gather metal pipe, wrenches, and pliers for construction
To create a fuel line disconnect tool, you'll need to gather specific materials and tools to ensure a functional and safe construction process. Here's a detailed breakdown of what you should collect:
Materials:
- Metal Pipe: Opt for a sturdy and durable metal pipe, preferably made of steel or brass. The pipe should be long enough to provide the necessary reach for your fuel line, typically around 12 to 18 inches in length. Choose a pipe with a diameter suitable for your fuel line; a common size is 1/4 inch or 3/8 inch.
- Pipe Fittings: You'll require various pipe fittings to connect the metal pipe to the fuel line and the disconnect mechanism. These fittings should include a tee, a coupling, and possibly a reducing bushing to adapt the pipe size to the fuel line.
- Metal Tubing (Optional): If you want to add flexibility to your tool, consider using small-diameter metal tubing to create a bendable section. This can be useful for navigating around tight spaces.
Tools:
- Wrenches: A set of wrenches is essential for tightening and loosening connections. You'll need a combination of adjustable wrenches and open-end wrenches in various sizes to accommodate different pipe and fitting sizes.
- Pliers: Pliers are crucial for gripping and manipulating small components. Get a pair of adjustable pliers and a pair of needle-nose pliers to handle delicate work.
- Pipe Cutter or Saw: You'll need a tool to cut the metal pipe to the desired length. A pipe cutter or a good-quality hacksaw will ensure a clean and precise cut.
- File or Sandpaper: These tools are useful for smoothing any sharp edges or burrs that may form during the construction process, ensuring a safe and comfortable grip.
- Safety Gear: Don't forget to prioritize safety by wearing appropriate gear, including gloves and safety goggles, to protect your hands and eyes during the construction.
By gathering these materials and tools, you'll be well-prepared to construct a custom fuel line disconnect tool, allowing you to safely and efficiently disconnect fuel lines without the need for specialized equipment. Remember to work in a well-ventilated area and follow all safety guidelines when using power tools.
Bicycle Motor Fuel Line Fix: A Step-by-Step Guide
You may want to see also
Design and Blueprint: Create a blueprint for the tool's dimensions and angles
When designing your fuel line disconnect tool, it's crucial to consider both functionality and ease of use. The primary goal is to create a tool that can safely and efficiently disconnect fuel lines without causing damage or requiring excessive force. Here's a detailed guide on how to approach the design and blueprint process:
Dimensions and Material Selection:
- Size: The tool should be compact enough to fit comfortably in your hand but sturdy enough to exert the necessary force. Aim for a length of around 6-8 inches (15-20 cm) for the main body, with a slightly wider base for stability.
- Material: Opt for durable materials like steel or high-impact plastic. Consider the trade-offs between weight, strength, and cost. For example, steel might be heavier but more robust, while plastic could be lighter and potentially more affordable.
- Handle: Design a comfortable and ergonomic handle. A T-shaped or pistol-grip handle with textured surfaces can provide better grip and control.
Angles and Geometry:
- Lever Angle: The most critical angle is the one formed by the tool's handle and the connecting rod that interacts with the fuel line fitting. This angle should be carefully calculated to provide the necessary mechanical advantage. A common starting point is 45 degrees, but you may need to adjust it based on the specific fitting size and material.
- Rod Length and Angle: The length and angle of the connecting rod will determine how much force is transferred to the fuel line. A longer rod with a steeper angle will provide more leverage. Experiment with different rod lengths and angles to find the optimal balance between force and control.
- Fitting Interface: The tool's interface with the fuel line fitting should be designed to securely hold the fitting without damaging it. Consider using a clamp-like mechanism or a friction-fit design.
Blueprint Creation:
- Drawings: Use computer-aided design (CAD) software to create detailed 2D and 3D drawings of your tool. This will allow you to visualize the design, check for potential issues, and make adjustments before manufacturing.
- Dimensions: Clearly specify all dimensions in your blueprint, including the length, width, thickness of each component, and the angles mentioned above.
- Assembly Instructions: Include a step-by-step guide for assembling the tool, specifying the order of components, fasteners, and any special considerations.
Prototyping and Testing:
- After finalizing your blueprint, build a prototype to test the tool's functionality, ergonomics, and durability.
- Conduct real-world testing with different fuel line sizes and materials to identify any areas for improvement.
- Iterate on your design based on feedback from testing and user input.
Fuel Line Barbed Connector: A Step-by-Step Installation Guide
You may want to see also
Fabrication Process: Cut, bend, and assemble parts to form the disconnect tool
The process of creating your own fuel line disconnect tool involves several steps, including cutting, bending, and assembling various parts to ensure a functional and reliable tool. Here's a detailed guide on how to approach this fabrication process:
Cutting the Parts: Begin by sourcing the necessary materials, which typically include a sturdy metal sheet or pipe, a metal rod for the handle, and any required fasteners. Measure and mark the metal sheet according to your design specifications. Using a sharp cutting tool, carefully cut along the marked lines to obtain the desired shape for your tool's base or handle. Ensure precise cuts to maintain the structural integrity of the final product. For the metal rod, you might need to cut it to the appropriate length for the handle, considering the overall size and balance of the tool.
Bending and Forming: Once you have the basic shapes, it's time to bend and form them into the required disconnect tool configuration. Take the metal sheet and carefully bend it to create the desired angles and curves for the tool's body or any additional components. You can use a metal brake or a vice to apply controlled pressure and achieve the necessary bends. Pay close attention to the dimensions and ensure that the bends are smooth and accurate. Similarly, bend the metal rod to form the handle, making sure it is comfortable to hold and provides a secure grip.
Assembling the Tool: With the individual parts ready, it's time to assemble them. Start by attaching the handle to the main body or base of the disconnect tool. Use appropriate fasteners like screws or bolts to secure the handle in place, ensuring it is firmly attached. Consider the ergonomics and accessibility of the tool during this step. Then, add any additional features or components, such as a release mechanism or a locking mechanism, if required. Test the tool's functionality at each assembly stage to ensure everything is correctly positioned and aligned.
Finishing Touches: After the initial assembly, inspect the tool for any sharp edges or protruding parts that might cause discomfort or injury. Use a file or sandpaper to smooth out these areas, ensuring a safe and user-friendly tool. Consider adding a protective coating or paint to enhance the tool's durability and aesthetics. Finally, test the disconnect tool's performance by simulating real-world conditions to ensure it effectively disconnects fuel lines without causing damage.
Remember, this fabrication process requires precision and attention to detail. Take your time with each step, and don't hesitate to seek guidance or advice from experienced fabricators or engineers if needed.
Optimizing Devil's Fuel Flow: Choosing the Right Line Size
You may want to see also
Safety Features: Include a safety catch to prevent accidental disconnections
When designing a fuel line disconnect tool, incorporating safety features is crucial to ensure the process is secure and accident-free. One essential safety mechanism is the implementation of a safety catch or latch system. This feature is designed to prevent the accidental disconnection of the fuel line, which could lead to dangerous situations.
The safety catch should be strategically placed and designed to engage with the fuel line connector. When the tool is in the disconnected position, the safety catch should securely hold the connector in place, requiring deliberate action to release it. This prevents accidental disconnections, especially in high-pressure environments where sudden movements could cause fuel to spray or leak.
To create this safety feature, you can utilize various design approaches. One method is to incorporate a spring-loaded mechanism that extends and locks into place when the tool is in the disconnected state. This spring-loaded safety catch can be positioned at the base of the tool, ensuring it engages with the fuel line connector firmly. When the tool is ready for use, a release button or lever can be included, allowing the operator to safely disconnect the fuel line.
Additionally, consider adding a visual indicator to the safety catch mechanism. This could be a small flag or a colored indicator that shows when the tool is safely locked and when it is ready for disconnection. Visual cues can be particularly useful in busy environments, helping operators quickly assess the tool's status without relying solely on tactile feedback.
By implementing a safety catch, you create a reliable barrier against accidental fuel line disconnections. This feature is especially important in applications where fuel line disconnections are frequent, such as in automotive repair shops or during vehicle maintenance. The safety catch ensures that the process is controlled and secure, reducing the risk of errors and potential hazards.
Thawing Frozen Fuel Lines: A Guide to Unfreezing
You may want to see also
Testing and Refinement: Test the tool's functionality and make adjustments for reliability
The process of testing and refining your fuel line disconnect tool is crucial to ensure its effectiveness and reliability. Here's a detailed guide on how to approach this stage:
Initial Testing: Begin by setting up a controlled environment to test the tool's functionality. Use a fuel line that closely mimics the real-world application, including the diameter and material. Connect the tool to the fuel line and apply varying levels of force to simulate different scenarios. Check if the tool can effectively disconnect the fuel line without causing damage or slipping. Observe if the mechanism locks into place securely and releases smoothly. This initial test will help identify any immediate issues with the tool's design and functionality.
Stress and Durability Testing: Proceed to test the tool's durability and resistance to stress. Subject the tool to extreme conditions, such as high-pressure simulations and temperature variations. This can be done using specialized equipment or by creating a controlled environment with extreme conditions. Ensure that the tool can withstand these tests without showing signs of wear or failure. Pay close attention to the connections and moving parts, as these areas are critical to the tool's performance.
Real-World Simulation: Create a scenario that mimics the actual use case of the fuel line disconnect tool. Set up a test rig that represents a vehicle's fuel system, including the fuel pump, lines, and tank. Test the tool under realistic conditions, such as different fuel pressures and temperatures. Evaluate its ease of use, speed, and effectiveness in disconnecting the fuel line. Consider factors like user experience, the time taken, and the tool's impact on the overall system.
Refinement and Adjustment: Based on the test results, make necessary adjustments to improve the tool's reliability. If the tool fails to disconnect the fuel line smoothly, consider modifying the locking mechanism or adding a spring to provide a more secure grip. Address any issues with the tool's grip or material compatibility by experimenting with different materials or coatings. Ensure that the tool can handle the expected range of fuel line sizes and materials without compromising its functionality.
Iterative Testing: After making adjustments, repeat the testing process to verify the improvements. Conduct thorough inspections to ensure that the tool now performs as intended. Consider seeking feedback from professionals or enthusiasts who can provide valuable insights into the tool's performance in real-world scenarios. This iterative approach allows for continuous refinement and ensures that the final product is reliable and user-friendly.
Troubleshooting: When Your Fuel Line's Performance is Compromised
You may want to see also
Frequently asked questions
To make a fuel line disconnect tool, you will require a few essential components. These include a length of sturdy metal pipe (such as steel or brass), a pair of pliers or a wrench for gripping, a fuel line clamp or ferrule, and a small piece of rubber or plastic to act as a seal. Additionally, you might want to consider using a heat source like a torch to melt the ferrule onto the pipe.
Start by cutting a piece of metal pipe to the desired length. Ensure it's long enough to provide a comfortable grip. Slide the fuel line through the pipe, then use the pliers or wrench to grip the pipe tightly around the fuel line. Next, attach the fuel line clamp or ferrule to the end of the pipe, ensuring it is secure and creates a tight seal. Finally, insert the rubber or plastic seal into the pipe to prevent any fuel leaks.
Yes, you can adapt your fuel line disconnect tool for various sizes. By using different sizes of metal pipes and fuel line clamps, you can accommodate different fuel line diameters. Simply adjust the length and type of clamp to fit the specific size required for your application.
When working with fuel lines, safety is crucial. Always wear protective gear, such as gloves and safety goggles, to prevent any potential injuries. Ensure you are in a well-ventilated area to avoid inhaling fuel fumes. Be cautious when using heat sources like torches, and never leave them unattended. Additionally, double-check your connections to avoid fuel leaks, which can be dangerous and cause fires.
Regular maintenance is key to keeping your fuel line disconnect tool in good condition. Inspect the tool periodically for any signs of wear and tear, such as damaged grips or weakened seals. Replace worn-out parts as needed to ensure a secure and reliable connection. Keep the tool clean and free from debris to prevent any interference with the fuel line.