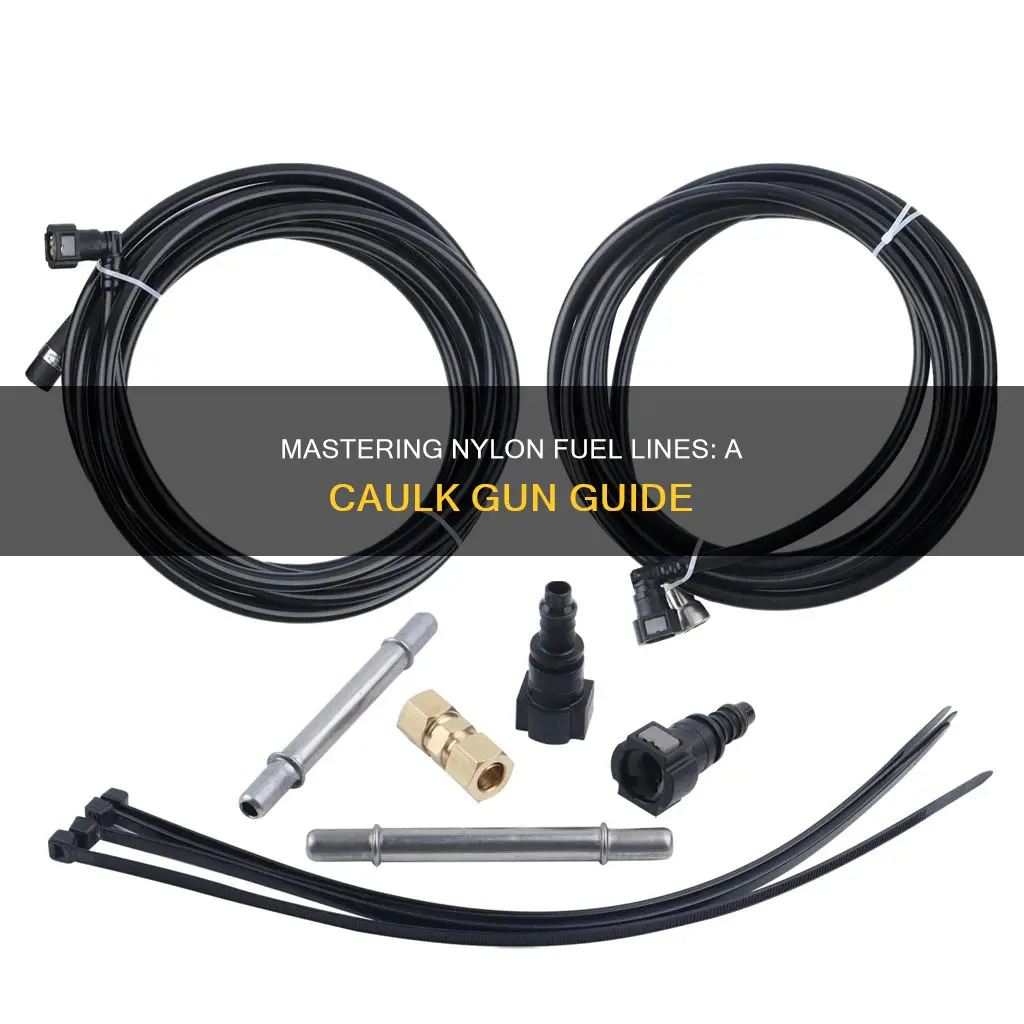
Creating nylon fuel lines with a caulk gun is a practical and cost-effective method for those seeking to customize or repair their vehicles. This technique involves using a caulk gun to apply a special adhesive to the nylon material, which then hardens to form a strong, flexible fuel line. The process is straightforward and can be completed with basic tools, making it an accessible project for DIY enthusiasts and mechanics alike. By following a few simple steps, you can ensure a secure and durable fuel line that meets your specific needs.
What You'll Learn
- Gather Materials: Collect nylon tubing, caulk, and a caulk gun
- Prepare Tubing: Cut and clean the nylon to fit fuel line needs
- Apply Caulk: Squeeze caulk into the tubing, ensuring an even layer
- Secure Connections: Use a gun to press connections firmly for a tight seal
- Test and Finish: Inspect the lines for leaks and complete the installation
Gather Materials: Collect nylon tubing, caulk, and a caulk gun
To begin your project of creating nylon fuel lines using a caulk gun, the first step is to gather all the necessary materials. This process ensures you have everything required to complete the task efficiently. Here's a detailed guide on what you need to collect:
Nylon Tubing: Start by acquiring the appropriate length and diameter of nylon tubing. The tubing should be specifically designed for fuel lines to ensure it can withstand the corrosive nature of fuels. Nylon is a durable material that can handle the rigors of fuel transport, making it an excellent choice for this application. Measure and cut the tubing to the desired length, ensuring you have enough to cover the entire length of the fuel line you intend to create.
Caulk: Select a high-quality caulk specifically formulated for sealing and bonding. Look for a caulk that is compatible with nylon and can provide a strong, durable bond. The caulk should be flexible enough to accommodate any slight movements or vibrations that may occur during the operation of the fuel system. Consider the color of the caulk to ensure it blends well with the nylon tubing, providing a discreet and aesthetically pleasing finish.
Caulk Gun: Invest in a good-quality caulk gun to facilitate the application process. A caulk gun allows for precise control over the amount of caulk dispensed, ensuring an even and consistent seal. Choose a gun with a comfortable grip and a mechanism that allows for easy loading and dispensing of the caulk. This tool will make the application process much more efficient and professional-looking.
When gathering these materials, ensure you have enough to complete your project without running out mid-construction. It's always a good idea to have some extra tubing and caulk on hand for any unforeseen needs or adjustments. With these materials ready, you'll be well-prepared to move on to the next steps of your nylon fuel line creation process.
Unraveling the Mystery: Marine-Grade Fuel Lines Explained
You may want to see also
Prepare Tubing: Cut and clean the nylon to fit fuel line needs
When preparing the nylon tubing for your fuel line, it's crucial to ensure precision and cleanliness to guarantee a reliable and safe fuel delivery system. Start by carefully measuring and marking the nylon tubing to the desired length. Nylon is a versatile material, but it requires careful handling to avoid damage. Use a sharp, clean knife or a tubing cutter to make a precise cut. Ensure the cut is straight and smooth to prevent any potential leaks or damage during the installation process.
After cutting the tubing, it's essential to clean the surface to ensure a strong bond. Start by removing any debris or dirt from the cut ends. You can use a small brush or a cotton swab to gently clean the area. For a more thorough clean, consider using a solvent like acetone or isopropyl alcohol. These solvents will help remove any oils or contaminants that could interfere with the bonding process. Ensure the nylon surface is completely dry before proceeding.
For an even more effective clean, you can employ a technique called 'debonding'. This process involves using a heat source to slightly soften the nylon and then carefully scraping away any remaining contaminants. Be cautious when using heat, as it can damage the material if applied incorrectly. A hairdryer on a low setting can be used for this purpose, but always test a small area first to ensure it doesn't cause any discoloration or damage.
Once the tubing is clean and dry, you can consider adding a primer or adhesive to enhance the bond. This step is especially useful if you're joining multiple pieces of tubing or if the environment is particularly harsh. There are specialized primers and adhesives available for nylon, which can provide a strong and durable bond. Apply the primer or adhesive according to the manufacturer's instructions, ensuring complete coverage of the cut ends.
Finally, inspect the prepared tubing for any defects or imperfections. Look for any cracks, chips, or uneven surfaces that could compromise the integrity of the fuel line. If any issues are found, address them promptly to ensure a professional-grade finish. By following these steps, you'll have prepared the nylon tubing effectively, ensuring a secure and reliable fuel line for your project.
Air in Fuel Line: Throttle Lag or Performance Boost?
You may want to see also
Apply Caulk: Squeeze caulk into the tubing, ensuring an even layer
When creating nylon fuel lines using a caulk gun, the application of caulk is a crucial step to ensure a secure and durable connection. Here's a detailed guide on how to apply the caulk effectively:
Start by ensuring you have the right amount of caulk. Squeeze a small amount of caulk from the tube, enough to cover the area you intend to seal. The goal is to create a consistent and even layer, so take your time with this step. You can use a caulk gun's tip to control the flow of the material, allowing for precise application. Apply the caulk in a smooth, continuous motion, moving along the length of the tubing. Avoid any gaps or uneven patches, as these can compromise the integrity of the seal. Press the caulk into the tubing's interior, ensuring it fills any existing voids or crevices. This step is essential to create a tight bond between the tubing and the surrounding surface.
For an even layer, consider the following technique. Hold the caulk gun at a slight angle, approximately 45 degrees, and apply the caulk in a consistent, linear motion. This technique ensures an even distribution and prevents any bulging or uneven appearance. If you're working with a curved section of tubing, adjust your grip and angle accordingly to maintain the even layer. Remember, the goal is to create a seamless and smooth finish.
Once you've applied the caulk, inspect the work. Ensure there are no visible gaps or areas where the caulk hasn't filled the tubing's interior. If you notice any imperfections, gently remove the excess caulk with your finger or a small tool, and reapply it for a neater finish. Allow the caulk to set according to the manufacturer's instructions, as this will ensure the material hardens and provides the necessary strength and flexibility.
This process of applying caulk is a critical step in the creation of nylon fuel lines, as it ensures a robust and reliable connection, capable of withstanding fuel pressures and temperatures. By taking the time to apply the caulk evenly, you'll achieve a professional-looking and functional result.
Thawing Fuel Lines: Time to Defrost Winter's Hold
You may want to see also
Secure Connections: Use a gun to press connections firmly for a tight seal
When working with nylon fuel lines, ensuring secure connections is crucial to prevent leaks and maintain the integrity of your fuel system. One effective method to achieve this is by using a caulk gun to press the connections firmly, creating a tight seal. Here's a step-by-step guide on how to accomplish this:
Start by preparing the nylon fuel lines and the components you intend to connect. Ensure that the ends of the fuel lines are clean and free of any debris or contaminants. You can use a wire brush or a small scraper to remove any dirt or old sealant, ensuring a clean surface for the connection.
Next, apply a suitable sealant or adhesive to the connection points. A small amount of thread seal tape or a specialized fuel line adhesive can be used for this purpose. The sealant acts as a barrier, preventing the fuel from seeping through any gaps and providing a reliable seal. Take care to apply the sealant evenly and avoid over-application, as excess adhesive can lead to messiness and potential leaks.
Now, it's time to use the caulk gun to press the connections firmly. Position the caulk gun so that it aligns with the connection point, ensuring a direct and even pressure application. Squeeze the trigger of the caulk gun to release a controlled amount of sealant, which will fill the gap between the two surfaces. This process ensures that the connection is sealed tightly, minimizing the risk of fuel leakage.
For added security, consider using a ferrule or a crimping tool in conjunction with the caulk gun technique. A ferrule is a metal sleeve that slips over the fuel line and is then compressed, creating a tight seal. By combining the caulk gun method with a ferrule, you can achieve an even more robust and reliable connection. This two-pronged approach provides a mechanical bond, ensuring the fuel lines are securely fastened.
Remember, when using a caulk gun, apply steady and even pressure to ensure the sealant is distributed correctly. Take your time with each connection to guarantee a professional finish. With practice, you'll master the art of creating secure and leak-free nylon fuel lines using this simple yet effective technique.
Mastering the Art of Fuel Line Removal: A Guide to HFMC
You may want to see also
Test and Finish: Inspect the lines for leaks and complete the installation
Once you've completed the process of creating your nylon fuel lines using a caulk gun, it's crucial to thoroughly test and finish the installation to ensure optimal performance and safety. Here's a step-by-step guide to inspecting the lines for leaks and completing the installation:
Testing for Leaks:
- Pressure Test: After the initial installation, it's essential to perform a pressure test to identify any potential leaks. Fill the fuel lines with a suitable fuel-safe pressure gauge. Apply pressure gradually, starting at a low setting and increasing it. Listen carefully for any hissing sounds, which indicate a leak. If you hear any, carefully inspect the connections and the line's surface for any visible damage or gaps.
- Visual Inspection: Carefully examine the entire length of the nylon fuel lines for any signs of damage, cracks, or bulges. Look for any areas where the material might have been compromised during the installation process. Ensure that all connections are secure and free from any debris or contaminants that could cause leaks over time.
- Use a Soapy Water Solution: For a more comprehensive leak test, prepare a soapy water solution. Spray or pour this solution along the length of the fuel lines, ensuring you cover all connections and bends. Any bubbles forming on the surface indicate a potential leak. If you detect any leaks, address them immediately by tightening connections or applying additional nylon to seal the area.
Completing the Installation:
- Secure Connections: After ensuring there are no leaks, double-check all connections to guarantee a secure fit. Use appropriate fuel-resistant tape or sealant to protect the joints and prevent future leaks.
- Routeing and Support: Carefully plan the route for your fuel lines, ensuring they are protected from potential damage during vehicle operation. Route them away from heat sources, sharp edges, or areas where they could be accidentally damaged. Consider using protective sleeves or clips to safeguard the lines.
- Final Inspection: Conduct a final visual inspection to ensure everything is in place and functioning correctly. Check for any obstructions or kinks in the lines that could affect fuel flow. Verify that all connections are tight and secure, and that there is no excessive movement or rubbing that could lead to wear and tear.
- Fuel System Bleed: If your fuel system has been drained or modified, it's essential to bleed the system to remove any air bubbles. Start the engine and allow it to idle, ensuring the fuel pump is running. This process helps to ensure a smooth fuel flow and proper engine operation.
By following these testing and finishing steps, you can be confident that your nylon fuel lines are installed correctly, leak-free, and ready to provide reliable fuel delivery to your vehicle's engine. Remember, proper installation and testing are critical to maintaining a safe and efficient fuel system.
Fuel Line Cleaning: Essential Tune-Up Component?
You may want to see also
Frequently asked questions
Nylon fuel lines are an excellent alternative to traditional rubber or vinyl lines due to their superior flexibility, durability, and resistance to fuel-related chemicals. They are commonly used in high-performance vehicles, racing applications, and classic car restoration projects.
Before installing the nylon fuel line, ensure it is the correct size and length for your application. Cut the line with a sharp knife or a dedicated fuel line cutter, leaving a small overlap at the ends for a secure connection. Clean the ends and apply a thin layer of fuel line adhesive or primer to facilitate a strong bond.
Yes, a caulk gun can be a useful tool for installing nylon fuel lines, especially when working with smaller-diameter lines. The caulk gun helps to apply the appropriate amount of fuel line adhesive or sealant, ensuring a tight and leak-free connection. Simply insert the fuel line into the caulk gun's nozzle, apply the adhesive, and quickly insert it into the fitting or hose.
For nylon fuel lines, it is recommended to use a high-temperature, fuel-resistant adhesive or sealant. Silicone-based adhesives or fuel line sealants are commonly used and provide excellent bonding strength. Always follow the manufacturer's instructions for the specific product you choose to ensure proper installation and compatibility.