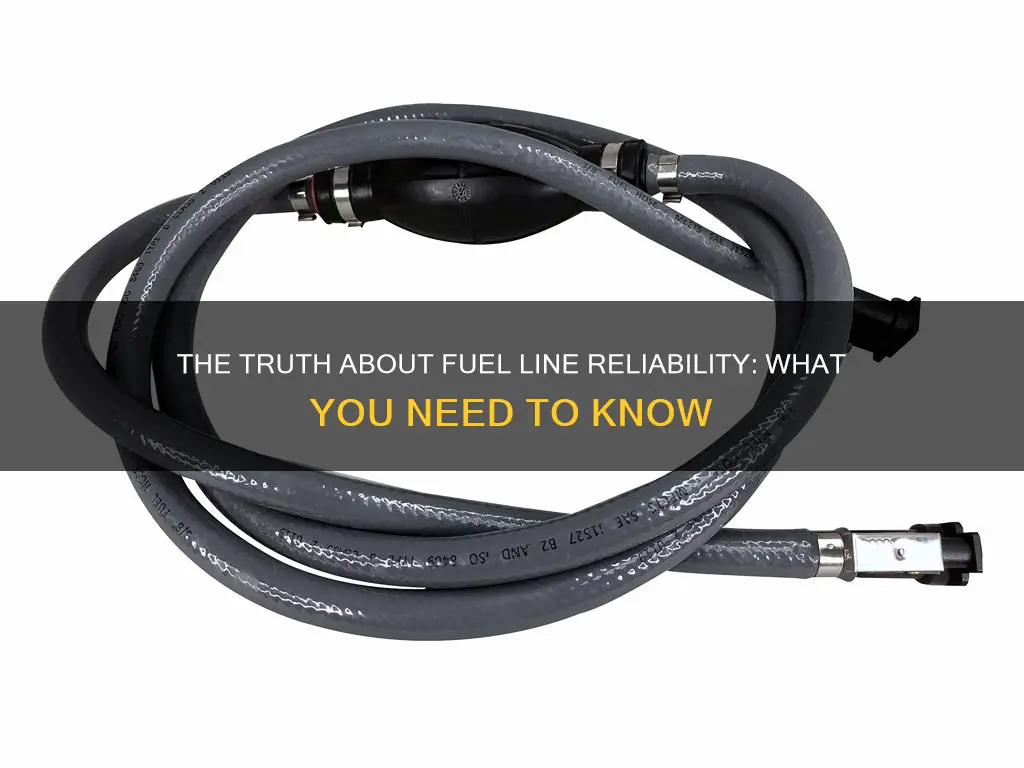
Fuel lines are a critical component of any vehicle's fuel system, responsible for transporting fuel from the tank to the engine. However, the reliability of fuel lines can vary significantly depending on several factors, including the type of fuel line, its material, construction, and installation. Some fuel lines are designed to withstand high pressure and temperatures, ensuring a consistent and reliable fuel supply. Others may be more susceptible to damage from heat, cold, or mechanical stress, leading to potential leaks or blockages. Understanding the specific characteristics and vulnerabilities of different fuel line types is essential for ensuring optimal vehicle performance and longevity.
What You'll Learn
- Material Quality: Different materials affect fuel line reliability
- Design and Construction: Well-designed lines with robust construction enhance durability
- Temperature Resistance: Fuel lines must withstand varying temperatures without cracking
- Flexibility and Rigidity: Balancing flexibility for movement and rigidity for support is crucial
- Corrosion Resistance: Protecting against corrosion ensures long-term reliability and safety
Material Quality: Different materials affect fuel line reliability
The material used in the construction of fuel lines is a critical factor in determining their reliability and performance. Different materials offer varying levels of durability, flexibility, and resistance to fuel-related degradation, which can significantly impact the overall longevity of the fuel system. Here's an overview of how material quality influences fuel line reliability:
Metal vs. Rubber: One of the most common debates in fuel line construction is the choice between metal and rubber materials. Metal fuel lines, typically made of stainless steel, offer superior strength and resistance to corrosion. They are less susceptible to fuel-related degradation and can withstand higher pressure, making them ideal for high-performance vehicles. However, metal lines can be more rigid and less flexible, which might lead to installation challenges and potential damage during vehicle movement. On the other hand, rubber fuel lines are more flexible and easier to install, especially in tight spaces. They are commonly used in everyday vehicles due to their cost-effectiveness and ease of use. Rubber's flexibility reduces the risk of damage during vehicle operation but may not be as durable as metal in the long term, especially when exposed to certain types of fuel.
Reinforced Construction: To enhance reliability, some fuel lines are constructed with reinforced layers. For instance, braided fuel lines use a metal or synthetic fiber core wrapped in rubber or a composite material. This design provides excellent flexibility while maintaining structural integrity. The braided construction ensures that the fuel line can withstand the constant expansion and contraction caused by temperature changes and engine vibrations. Reinforced fuel lines are often preferred in high-performance applications where fuel lines need to handle rapid acceleration and deceleration without compromising reliability.
Temperature and Chemical Resistance: The reliability of fuel lines is also closely tied to their resistance to temperature and chemical changes. Materials like synthetic rubber compounds and certain types of plastic can maintain their flexibility and structural integrity over a wide temperature range. This is crucial for vehicles operating in diverse climates. Additionally, fuel lines should be resistant to the chemicals present in different types of fuel, such as ethanol blends, to prevent degradation and cracking over time.
Longevity and Maintenance: Material quality directly impacts the long-term reliability of fuel lines. High-quality materials can withstand the rigors of everyday use, including exposure to fuel, engine heat, and mechanical stress. This results in longer-lasting fuel lines with reduced maintenance requirements. For instance, fuel lines made from advanced synthetic materials might not require replacement as frequently as those made from traditional rubber, especially in high-mileage vehicles.
In summary, the choice of material is a critical consideration when evaluating fuel line reliability. Each material has its advantages and trade-offs, and the right selection depends on the specific application, vehicle type, and performance requirements. Understanding these material properties ensures that fuel lines are chosen appropriately, contributing to a more reliable and efficient fuel system.
Unveiling the Material Secrets of Micro Fuel Lines
You may want to see also
Design and Construction: Well-designed lines with robust construction enhance durability
The design and construction of fuel lines play a critical role in determining their reliability and longevity. Well-designed lines are built to withstand the rigors of fuel transport, ensuring that they remain intact and functional over time. This involves careful consideration of various factors to ensure optimal performance and safety.
One key aspect of design is the choice of materials. Fuel lines should be constructed using high-quality materials that can resist corrosion, abrasion, and the effects of fuel itself. Common materials include rubber, vinyl, and braided steel, each offering different advantages. Rubber and vinyl are flexible and resistant to fuel degradation, while braided steel provides excellent strength and durability, making it ideal for high-pressure applications. The material selection ensures that the fuel lines can withstand the harsh conditions they encounter, such as temperature fluctuations and mechanical stress.
Robust construction techniques are equally important. This includes proper reinforcement at bends and joints to prevent damage and ensure flexibility. Reinforcement can be achieved through the use of metal braids, steel wire, or additional layers of protective material. Well-designed lines will also feature secure fittings and connections to prevent leaks and ensure a tight seal. The construction process should adhere to industry standards and best practices to guarantee the overall integrity of the fuel system.
In addition to material and construction choices, the design should also consider the specific application and environment. For example, fuel lines in high-temperature environments may require materials with superior heat resistance. Similarly, lines used in racing or high-performance applications might need to accommodate higher fuel pressures and faster fuel flow rates. Customized designs can address these unique requirements, ensuring the fuel lines are reliable and efficient in their intended role.
By focusing on design and construction, engineers can create fuel lines that are not only reliable but also tailored to specific needs. This attention to detail contributes to the overall performance and safety of vehicles and equipment, ensuring that fuel is delivered efficiently and securely. Well-designed and constructed fuel lines are a testament to the importance of precision in engineering, ultimately enhancing the durability and dependability of fuel systems.
Cub 3235 Fuel Line Size: Expert Guide
You may want to see also
Temperature Resistance: Fuel lines must withstand varying temperatures without cracking
Fuel lines are a critical component in any vehicle's fuel delivery system, and their reliability is essential for safe and efficient operation. One of the most significant factors affecting fuel line reliability is temperature resistance. Fuel lines must be able to withstand the extreme temperature variations that engines experience without compromising their structural integrity.
The internal combustion process in an engine generates a significant amount of heat, which can cause the fuel lines to expand and contract rapidly. This thermal expansion and contraction can lead to stress on the fuel line material, potentially causing it to crack or fail over time. To ensure reliability, fuel lines are typically made from materials that have a high temperature resistance, such as rubber compounds reinforced with synthetic fibers. These materials can maintain their flexibility and structural integrity even when exposed to extreme temperatures, ensuring that the fuel lines can withstand the demands of the engine without cracking or leaking.
In addition to the engine's operating temperature, fuel lines must also be able to handle the temperature changes that occur during different seasons and driving conditions. For example, fuel lines need to resist the cold temperatures that can occur during winter, as this can cause the fuel to thicken and flow more slowly, putting additional stress on the fuel lines. Similarly, they must handle the hot temperatures that can arise during summer, where the fuel can expand and potentially damage the fuel lines if they are not temperature-resistant enough.
To further enhance temperature resistance, some fuel lines are designed with specialized coatings or protective layers. These additional layers can provide insulation and protection against heat, ensuring that the fuel lines remain flexible and crack-free even in the most demanding conditions. For instance, some fuel lines may have a rubber-like coating that acts as a thermal barrier, preventing the fuel from coming into direct contact with the metal fuel line, which could lead to corrosion and cracking.
In summary, temperature resistance is a critical aspect of fuel line reliability. Fuel lines must be able to withstand the extreme temperatures encountered in various driving conditions without cracking or failing. By using appropriate materials and design techniques, engineers can ensure that fuel lines provide a reliable and safe fuel delivery system, contributing to the overall performance and longevity of the vehicle.
Fuel Line Installation: A Step-by-Step Guide to Installing a Fuel Ring
You may want to see also
Flexibility and Rigidity: Balancing flexibility for movement and rigidity for support is crucial
The concept of flexibility and rigidity is essential when considering the reliability of fuel lines in vehicles. These lines play a critical role in delivering fuel from the tank to the engine, and their design must strike a delicate balance between allowing movement and providing structural support.
Flexibility is a key requirement for fuel lines as it enables the lines to navigate the intricate network of components within a vehicle's engine bay. The lines must be able to bend and twist to accommodate the various angles and curves of the engine, transmission, and other nearby structures. This flexibility ensures that the fuel lines can maintain their integrity without being damaged by sharp turns or tight spaces. For example, the fuel lines in a modern vehicle may need to traverse under the engine block, around the transmission, and even over the firewall, requiring a certain level of pliability.
However, flexibility alone is not sufficient; fuel lines also need to possess a degree of rigidity to ensure their structural integrity. Rigidity provides the necessary strength and stability to withstand the forces exerted by the engine and other moving parts. Without adequate rigidity, fuel lines could become susceptible to damage from vibrations, impacts, or even the pressure of fuel flow. For instance, a fuel line with insufficient rigidity might collapse under the weight of the engine or break due to excessive bending during engine operation.
The challenge lies in finding the optimal balance between flexibility and rigidity. Fuel lines should be flexible enough to navigate the vehicle's architecture without compromising their structural integrity. This often involves using materials that offer a combination of flexibility and strength. Modern fuel lines are typically made from high-quality rubber or synthetic materials that provide the necessary flexibility while also being resistant to wear and tear. These materials are carefully selected to ensure they can withstand the harsh conditions inside the engine bay, including temperature fluctuations and exposure to fuel vapors.
In summary, the reliability of fuel lines depends on their ability to strike a balance between flexibility and rigidity. Flexibility allows the lines to navigate the vehicle's complex architecture, while rigidity ensures they can withstand the mechanical stresses and strains encountered during operation. Engineers must carefully consider these factors when designing fuel lines to ensure optimal performance and longevity, ultimately contributing to the overall reliability of the vehicle's fuel system.
Mastering Plastic Fuel Lines: The Ultimate Seal for Long-Lasting Performance
You may want to see also
Corrosion Resistance: Protecting against corrosion ensures long-term reliability and safety
Corrosion resistance is a critical aspect of ensuring the long-term reliability and safety of fuel lines in various applications, from automotive to industrial settings. Fuel lines are susceptible to corrosion due to their exposure to harsh environments, including fuel vapors, moisture, and contaminants. Over time, these corrosive elements can lead to the degradation of the fuel line material, resulting in reduced performance and potential safety hazards.
One of the primary methods to enhance corrosion resistance is the selection of appropriate materials. Fuel lines are often made from materials like steel, aluminum, or specialized polymers. For instance, stainless steel is renowned for its inherent corrosion resistance due to its chromium content, which forms a protective oxide layer on the surface. Similarly, certain polymers, such as polyetheretherketone (PEEK) or fluoropolymers, offer excellent resistance to corrosion and chemical attacks, making them ideal for fuel line applications.
Coating and plating techniques can also significantly improve corrosion resistance. Applying a protective coating or plating to the fuel line's surface creates a barrier between the material and the corrosive environment. For example, zinc plating can be used to protect steel fuel lines, as zinc acts as a sacrificial anode, corroding instead of the steel. Similarly, polymer coatings, such as those made from polyimide or fluoropolymers, can provide a protective layer, preventing corrosive substances from coming into direct contact with the fuel line material.
In addition to material selection and coating, proper design and installation practices play a vital role in corrosion resistance. Fuel lines should be designed to minimize the use of sharp bends and kinks, as these can create stress concentrations that accelerate corrosion. Smooth transitions and gentle curves help reduce the likelihood of material failure due to stress-corrosion cracking. Furthermore, ensuring proper ventilation and drainage in the fuel system can prevent the accumulation of moisture and corrosive byproducts.
Regular maintenance and inspection are essential to identify and address any signs of corrosion promptly. Visual inspections should be conducted to look for discoloration, pitting, or any visible damage on the fuel line. Non-destructive testing methods, such as ultrasonic testing, can be employed to detect internal corrosion without causing damage to the fuel line. Timely maintenance, including cleaning and replacement of corroded sections, ensures the continued reliability and safety of the fuel system.
Fuel Line Magnets: Myth or Magic? Unveiling the Truth
You may want to see also
Frequently asked questions
Fuel lines play a crucial role in delivering fuel from the tank to the engine. They ensure a consistent and efficient supply of fuel, which directly impacts engine performance. Well-maintained fuel lines prevent fuel leaks and ensure that the engine receives the correct amount of fuel at the right pressure, resulting in optimal power output and fuel efficiency.
A failing fuel line may exhibit several symptoms. One of the most noticeable signs is a decrease in engine performance, such as reduced power, acceleration, or fuel efficiency. You might also notice hissing or whistling sounds coming from the fuel system, indicating a potential leak. Engine misfires, rough idling, or difficulty starting the engine are other indicators of a failing fuel line. Regular inspections and maintenance can help identify these issues early on.
Yes, fuel line issues can lead to significant engine damage if left unattended. Fuel leaks can cause corrosion and contamination of engine components, especially if the fuel contains ethanol or other additives. Over time, this can result in engine misfires, reduced performance, and even permanent engine damage. It is essential to address fuel line problems promptly to prevent costly repairs.
Regular maintenance and inspection of fuel lines are vital for their longevity and reliability. It is recommended to inspect fuel lines during routine engine maintenance checks, typically every 30,000 to 50,000 miles or as advised by the vehicle manufacturer. Fuel lines should be replaced if they show signs of wear, damage, or corrosion. Proper fuel line maintenance ensures a reliable fuel supply and helps prevent unexpected breakdowns.