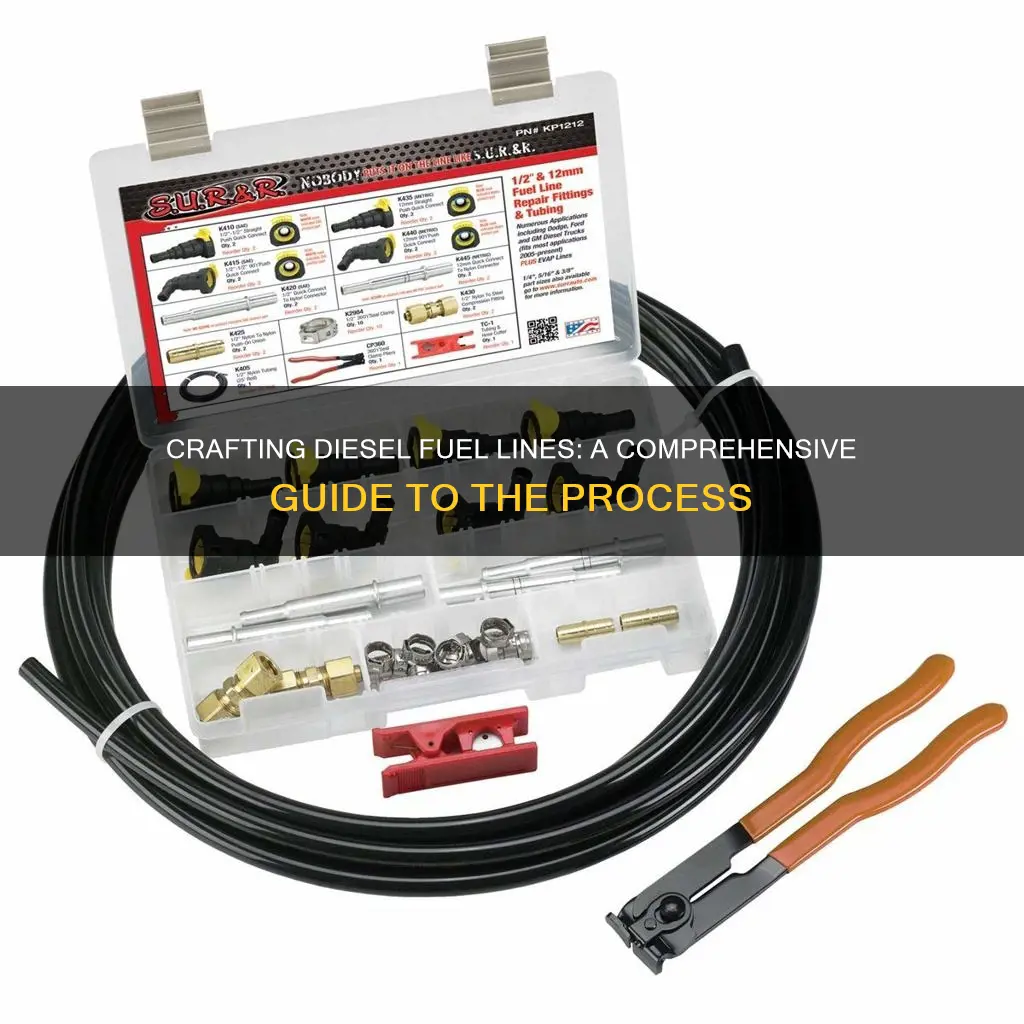
Making diesel fuel lines is a specialized process that requires careful attention to detail and adherence to specific guidelines. It involves the creation of high-quality fuel lines that can withstand the demanding conditions of diesel engines. The process typically starts with selecting the appropriate materials, such as durable rubber or synthetic compounds, and then involves precise manufacturing techniques like molding, extrusion, or welding to ensure the lines are free of defects. Proper assembly, including the use of high-quality fittings and seals, is crucial to prevent leaks and ensure optimal performance. This guide will provide a comprehensive overview of the steps involved in crafting reliable diesel fuel lines, covering everything from material selection to final testing and installation.
What You'll Learn
- Fuel Line Material Selection: Choose the right material for durability and compatibility
- Line Routing and Installation: Route and install lines to avoid damage and ensure proper flow
- Fuel Filter and Pump Maintenance: Regularly clean and maintain filters and pumps for optimal performance
- Pressure Testing: Test fuel lines for leaks and pressure to ensure safety
- Safety Precautions: Wear protective gear and follow safety protocols during fuel line work
Fuel Line Material Selection: Choose the right material for durability and compatibility
When it comes to crafting diesel fuel lines, the choice of material is a critical aspect that directly impacts the line's durability and compatibility with the fuel. The primary goal is to ensure the fuel lines can withstand the harsh conditions of diesel fuel, including its temperature variations and potential chemical properties. Here's a guide to selecting the appropriate material:
Consider the Fuel's Nature: Diesel fuel is known for its higher viscosity and potential for containing water and contaminants compared to gasoline. These factors can accelerate material degradation. Therefore, the chosen material should offer excellent resistance to these elements. Materials like high-density polyethylene (HDPE) or cross-linked polyethylene (PE-X) are often preferred due to their superior chemical resistance and ability to handle varying temperatures without compromising flexibility.
Evaluate Material Strength and Flexibility: Fuel lines need to be robust yet flexible to accommodate engine vibrations and potential route constraints. Materials such as rubber or silicone compounds are commonly used for their flexibility. However, it's essential to select a grade that can withstand the pressure and temperature fluctuations associated with diesel fuel. Reinforced rubber or silicone compounds with fiber reinforcement can provide the necessary strength while maintaining flexibility.
Check Compatibility and Standards: Ensure that the selected material is compatible with diesel fuel and adheres to industry standards. Some materials may react with the fuel over time, leading to degradation or contamination. For instance, certain plastics might not be suitable due to their potential to leach chemicals into the fuel. Always refer to manufacturer guidelines and industry standards to ensure compatibility and safety.
Consider Environmental Factors: Outdoor installations or vehicles exposed to varying weather conditions require materials that can withstand UV radiation, ozone, and temperature extremes. Materials like HDPE or UV-resistant rubber compounds are ideal for such applications, ensuring long-term durability and resistance to environmental degradation.
Testing and Quality Control: Before finalizing the material, conduct thorough testing to assess its performance. This includes subjecting the material to simulated diesel fuel conditions, checking for flexibility, and ensuring it meets the required pressure and temperature ratings. Quality control measures are essential to guarantee that the fuel lines meet the necessary standards and will perform reliably over their expected lifespan.
Dodge Hellcat Fuel Line Sizing: A Comprehensive Guide
You may want to see also
Line Routing and Installation: Route and install lines to avoid damage and ensure proper flow
When designing the route for your diesel fuel lines, it's crucial to prioritize safety and functionality. Here's a step-by-step guide to ensure proper installation:
- Planning the Route: Begin by carefully mapping out the path your fuel lines will take. Consider the vehicle's engine layout and the location of various components. Aim to route the lines away from high-temperature areas, such as exhaust manifolds and engine blocks, to prevent overheating and potential damage. Additionally, avoid areas prone to vibration, like engine mounts, to minimize the risk of line breakage.
- Protecting Against Damage: To safeguard your fuel lines, it's essential to use appropriate protective measures. Wrap the lines with heat-resistant insulation, especially where they pass close to hot surfaces. Consider using flexible metal hoses or rubber-reinforced lines to add strength and durability. Ensure that all connections are securely fastened and protected with clips or brackets to prevent chafing.
- Proper Support: Adequate support is vital to maintaining the integrity of the fuel lines. Install brackets or hangers at regular intervals along the route to keep the lines taut and prevent sagging. This support system will also help absorb vibrations, reducing the likelihood of leaks or damage.
- Clearances and Accessibility: Maintain sufficient clearance between the fuel lines and other components to allow for easy access during maintenance. Avoid tight spaces or areas where the lines might rub against moving parts. Proper clearance ensures that the lines can be inspected and serviced without disassembly, making maintenance more efficient.
- Secure Connections: When connecting the fuel lines, use high-quality fittings and ensure they are tightened correctly. Leaks can occur if connections are not secure. Consider using fuel-resistant tape or sealant around threads to create a reliable seal. Additionally, inspect all connections regularly to identify and address any potential issues.
- Testing and Inspection: After installation, thoroughly test the fuel system to ensure there are no leaks. Use a pressure gauge to check for any drops in pressure, indicating a potential leak. Visually inspect the lines for any signs of damage or wear. This testing phase is crucial to identifying and rectifying any issues before they lead to more significant problems.
Napa Auto's SAE30R9 Fuel Injection Line: A Comprehensive Guide
You may want to see also
Fuel Filter and Pump Maintenance: Regularly clean and maintain filters and pumps for optimal performance
Maintaining the fuel filter and pump system in your diesel engine is crucial for ensuring optimal performance and longevity. Regular maintenance can prevent issues and costly repairs down the line. Here's a guide on how to keep your fuel filter and pump in top condition:
Understanding the System: Begin by understanding the components involved. The fuel filter is designed to remove contaminants from the diesel fuel, ensuring clean fuel delivery to the engine. It typically consists of a filter element that traps dirt, water, and other impurities. The fuel pump, on the other hand, is responsible for delivering the required fuel pressure to the engine. It operates continuously and requires regular attention. Familiarize yourself with the specific make and model of your vehicle's fuel filter and pump to understand their unique characteristics.
Routine Inspection: Implement a routine inspection schedule. Visual inspections can reveal a lot about the health of your fuel system. Check for any signs of contamination, such as dirt or debris, in the filter housing. Look for leaks or damage to the fuel lines and connections. Inspect the pump for any unusual wear or damage. Regularly checking these components can help identify potential issues early on.
Filter Cleaning and Replacement: Cleaning and replacing the fuel filter is a critical aspect of maintenance. Over time, the filter becomes clogged with contaminants, reducing its effectiveness. Locate the filter and use the appropriate cleaning tools to remove any built-up dirt. Follow the manufacturer's guidelines for cleaning procedures. If the filter is reusable, ensure it is properly reinstalled. Otherwise, replace it with a new one to maintain optimal filtration. Remember to dispose of used filters responsibly.
Pump Maintenance: The fuel pump requires regular maintenance to function efficiently. Inspect the pump for any signs of wear, such as worn-out seals or damaged impellers. Check the pump's pressure to ensure it meets the manufacturer's specifications. If you notice any issues, such as reduced pressure or unusual noises, it may indicate a failing pump. In such cases, consider replacing the pump to prevent further complications. Proper pump maintenance ensures consistent fuel delivery and engine performance.
Regular Servicing: Incorporate regular servicing into your vehicle's maintenance schedule. This includes checking and replacing filters, inspecting fuel lines for damage, and testing pump performance. By following a consistent maintenance routine, you can identify and address potential problems before they escalate. Regular servicing will also help you stay on top of any specific requirements or recommendations provided by the vehicle manufacturer.
Remember, proper fuel filter and pump maintenance is essential for the overall health of your diesel engine. By following these steps, you can ensure that your fuel system operates efficiently, providing reliable performance and potentially extending the life of your vehicle.
Mastering Metal Fuel Lines: A Comprehensive Guide to Secure Connections
You may want to see also
Pressure Testing: Test fuel lines for leaks and pressure to ensure safety
Pressure testing is a critical step in ensuring the safety and reliability of diesel fuel lines. It involves applying pressure to the fuel lines and checking for any leaks or pressure drops, which can indicate potential issues. Here's a detailed guide on how to perform this test:
Preparation: Before starting the pressure test, ensure you have the necessary tools and equipment. You'll need a pressure gauge, a source of compressed air or nitrogen, and a leak detection solution (often a soapy water mixture). It is also essential to have a clear understanding of the fuel line system and its components. Familiarize yourself with the layout, connections, and any specific requirements of the diesel engine you are working on.
Procedure: Begin by disconnecting the fuel lines from the engine and any associated components. This step ensures that the lines are isolated and allows for a controlled test environment. Apply the leak detection solution to the interior of the fuel lines, ensuring an even coating. Then, using the compressed air or nitrogen, inflate the lines to a predetermined pressure, typically the operating pressure of the system. Observe the lines for any bubbles or foam, indicating potential leaks. If no leaks are found, the lines are likely intact.
Leak Detection: If leaks are detected, they can be identified by the presence of bubbles or foam at the connection points or along the length of the line. In such cases, you may need to temporarily seal the leak with a suitable compound or tape to prevent further issues. It is crucial to address any leaks promptly, as they can lead to fuel loss, reduced engine performance, and potential safety hazards.
Pressure Measurement: After ensuring no leaks, measure the pressure inside the fuel lines using the gauge. Record the initial pressure and then gradually increase it to the desired operating pressure. Monitor the gauge during this process to ensure the pressure stabilizes at the target value. If the pressure drops significantly, it may indicate a restriction or damage within the line.
Safety Considerations: When performing pressure testing, always prioritize safety. Wear appropriate personal protective equipment, such as gloves and safety goggles, to protect against potential fuel splashes or leaks. Ensure proper ventilation in the work area to avoid inhaling fuel vapors. Additionally, be cautious when handling high-pressure components to prevent injury.
By following these steps, you can effectively pressure test diesel fuel lines, ensuring they are leak-free and capable of withstanding the required pressure. Regular maintenance and testing are essential to maintain the integrity of the fuel system and the overall performance and safety of the diesel engine.
Mastering Metal Fuel Lines: A Comprehensive Guide to Installation and Maintenance
You may want to see also
Safety Precautions: Wear protective gear and follow safety protocols during fuel line work
When working with diesel fuel lines, it is crucial to prioritize safety to prevent accidents and ensure your well-being. Here are some essential safety precautions to keep in mind:
Protective Gear: Prioritize your safety by wearing appropriate personal protective equipment (PPE). This includes heat-resistant gloves, safety goggles, and a respirator mask to protect your skin, eyes, and lungs from potential hazards. Consider wearing a flame-resistant jacket and pants to shield yourself from sparks or flames. Additionally, ensure you have a suitable pair of work gloves to provide grip and protect your hands from sharp edges or hot surfaces.
Ventilation and Respiratory Protection: Diesel fuel and its derivatives can release harmful fumes, so proper ventilation is crucial. Work in a well-ventilated area or consider using a fume hood to minimize inhalation of toxic gases. If you are working in a confined space, a respirator mask is essential to filter out harmful particles and gases, ensuring your respiratory system remains safe.
Fire Safety: Diesel fuel is highly flammable, so fire safety measures are critical. Keep a fire extinguisher nearby and ensure it is suitable for class B fires (involving flammable liquids). Maintain a clear workspace, free of potential fire hazards like open flames, sparks, or hot surfaces. Always have a fire blanket or fire-resistant materials nearby in case of emergencies.
Training and Protocols: Familiarize yourself with the specific safety protocols and procedures for your work environment. This may include emergency response plans, hazard communication guidelines, and proper waste disposal methods. Ensure you are adequately trained in fuel line installation, repair, or maintenance to avoid accidents. Stay updated with industry best practices and regulations to ensure a safe working environment.
Regular Maintenance and Inspection: Implement a regular maintenance schedule for your fuel lines to identify and address potential issues promptly. Inspect the lines for cracks, leaks, or signs of damage. Regular maintenance can prevent fuel contamination, leaks, and potential fires. Keep a record of inspections and any necessary repairs to ensure the longevity and safety of your diesel fuel system.
DUCATI MONSTER Fuel Line Maintenance: A Step-by-Step Guide
You may want to see also
Frequently asked questions
Diesel fuel lines are typically made from durable materials such as rubber, plastic (like PVC or polyethylene), or metal (such as steel or aluminum). The choice of material depends on factors like temperature resistance, pressure requirements, and the specific application.
Compatibility is crucial to prevent fuel degradation and potential engine damage. Always use fuel lines that are designed for diesel fuel and meet industry standards. Check the manufacturer's specifications and ensure the material and additives in the fuel line are compatible with diesel.
Installation involves several steps. First, ensure the engine and fuel system are properly prepared and cleaned. Then, cut the fuel lines to the desired length, using a sharp, clean blade. Insert the lines into the fittings, ensuring a secure connection. Use fuel line connectors or clamps to hold the lines in place, and double-check for any leaks.
Leaks can be a significant issue. Before installation, inspect the fuel lines for any damage or defects. Use a fuel-resistant tape or sealant to cover any cuts or openings. Apply a suitable primer to the fuel line and fitting surfaces before connecting them. Tighten fittings securely, but be careful not to overtighten, as it can cause damage. Test the system for leaks after installation.
Regular maintenance is essential to ensure optimal performance. Inspect the fuel lines periodically for cracks, brittleness, or signs of deterioration. Check for any clogs or blockages and clean the lines as needed. Keep the fuel lines protected from extreme temperatures and direct sunlight to prevent degradation. Regularly replace fuel lines as part of routine maintenance, especially if they show signs of wear and tear.