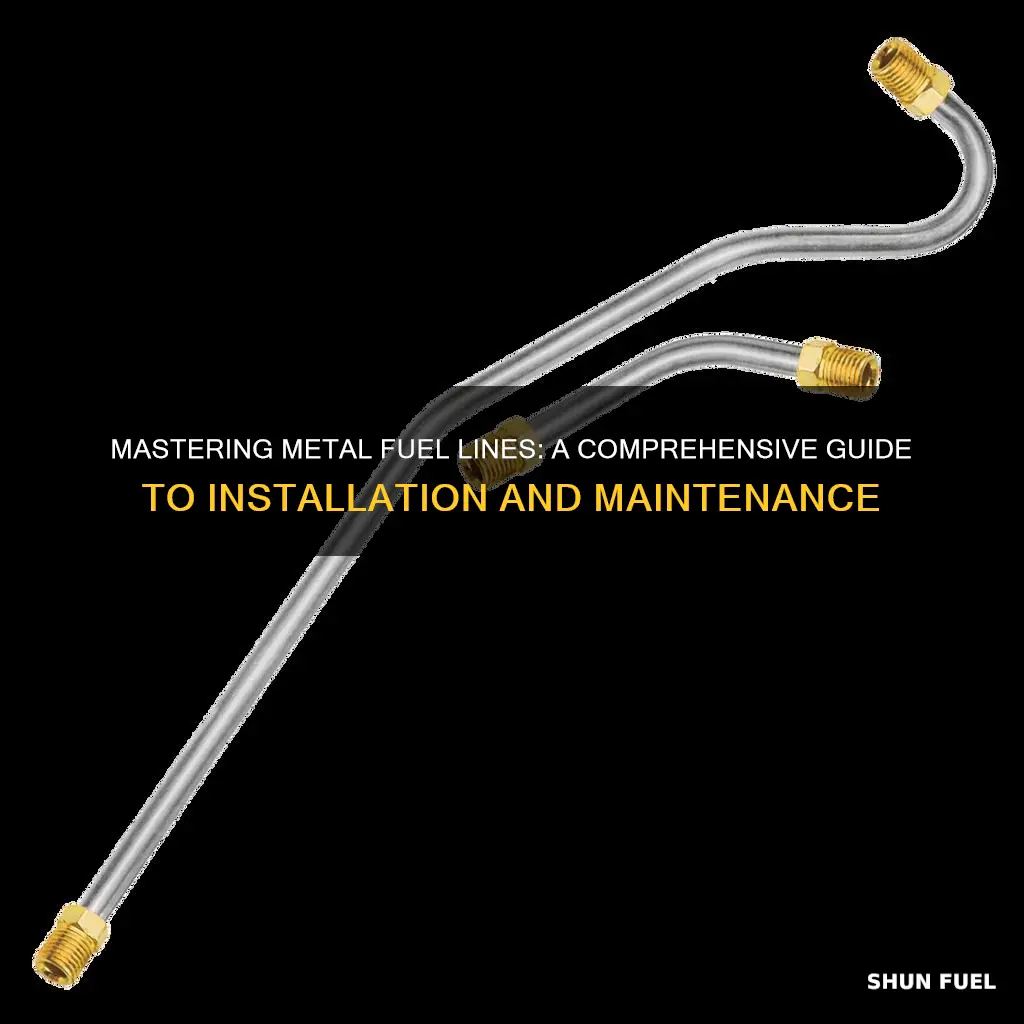
Running metal fuel lines is a crucial step in any vehicle's fuel system, ensuring efficient and safe fuel delivery. This process involves careful planning and execution to avoid potential issues. It's essential to understand the specific requirements of your vehicle and the type of metal fuel lines you're using. The process typically includes selecting the appropriate size and type of fuel line, ensuring it's compatible with your vehicle's fuel system, and properly securing it to prevent leaks. This guide will provide a comprehensive overview of the steps involved, from preparation to installation, ensuring your fuel lines are installed correctly and securely.
What You'll Learn
- Material Selection: Choose appropriate metal fuel lines based on temperature and pressure requirements
- Routing and Support: Securely route lines, using brackets and clips for stability
- Fittings and Connections: Ensure tight, leak-free fittings with proper torque and sealing
- Inspection and Maintenance: Regularly check for corrosion, damage, and leaks
- Safety Precautions: Wear protective gear and follow safety protocols during installation and repairs
Material Selection: Choose appropriate metal fuel lines based on temperature and pressure requirements
When it comes to selecting the right metal fuel lines for your application, considering the temperature and pressure requirements is crucial. The choice of material directly impacts the performance, safety, and longevity of the fuel lines. Here's a detailed guide on how to choose the appropriate metal fuel lines based on these critical factors:
Temperature Considerations:
Different metals have varying temperature limits, and it's essential to match the material to the operating temperature range of your fuel system. For high-temperature environments, materials like stainless steel or Inconel alloys are excellent choices. These metals offer excellent heat resistance, ensuring the fuel lines can withstand extreme temperatures without degradation or failure. For lower-temperature applications, consider materials such as aluminum or copper, which provide good thermal stability within their respective temperature ranges.
Pressure Requirements:
The pressure at which the fuel lines will operate is another critical factor. High-pressure fuel systems demand materials with exceptional strength and durability. Materials like carbon steel or brass alloys can handle moderate to high pressures, making them suitable for various applications. However, for extremely high-pressure environments, consider specialized alloys like Monel or Hastelloy, which offer superior strength and resistance to corrosion under intense pressure conditions.
Material Selection Process:
- Identify Operating Conditions: Begin by understanding the specific temperature and pressure requirements of your fuel system. Consider the maximum and minimum temperatures it will encounter and the pressure differentials involved.
- Research Material Properties: Study the properties of various metal alloys. Look for data on their melting points, tensile strength, ductility, and resistance to corrosion. This information will help you match the material to the expected operating conditions.
- Consider Industry Standards: Adhere to industry standards and guidelines for fuel line materials. For instance, in the automotive industry, certain alloys might be recommended for their proven performance and reliability.
- Consult Manufacturers' Data: Refer to manufacturers' specifications and data sheets for their fuel line products. These sources provide valuable insights into the materials used and their performance characteristics.
- Test and Validate: If possible, conduct material testing to ensure the chosen metal fuel lines meet the required specifications. This step is especially important for critical applications where safety is paramount.
By carefully considering temperature and pressure requirements, you can select metal fuel lines that are not only durable but also reliable, ensuring optimal performance and safety in your fuel system. Remember, the right material choice is fundamental to the long-term success and efficiency of your metal fuel line installation.
Fuel Line Fix: A Guide to Repairing Poulan Chainsaw Lines
You may want to see also
Routing and Support: Securely route lines, using brackets and clips for stability
When running metal fuel lines, proper routing and support are crucial to ensure the system's safety and longevity. Here's a detailed guide on how to achieve this:
Routing the Lines: Begin by carefully planning the path of the fuel lines. Metal fuel lines should be routed in a way that avoids sharp bends and tight spaces, as this can lead to damage and reduced flexibility. Aim for a straight and smooth route, allowing for some slack to accommodate potential temperature changes and vehicle movement. Use a flexible metal conduit or a custom-made metal sleeve to protect the lines from sharp edges and potential impacts. This conduit should be securely attached to the vehicle's body or frame using appropriate brackets.
Securing with Brackets: Brackets are essential for providing structural support and maintaining the correct positioning of the fuel lines. Use metal brackets specifically designed for fuel line applications, ensuring they are made from corrosion-resistant materials. Attach the brackets to the vehicle's frame or relevant components, positioning them at regular intervals along the line's length. This spacing will help distribute the weight and reduce stress on any single point, preventing potential leaks or damage. Ensure the brackets are tightened securely to provide a rigid support structure.
Using Clips for Additional Support: In addition to brackets, consider using metal clips to further secure the fuel lines. These clips can be attached to the vehicle's body or other stable structures, providing additional support points. Space the clips evenly along the route, especially in areas where the line might experience more strain or vibration. Metal clips offer a quick and effective way to keep the lines in place, preventing them from sagging or becoming damaged.
Flexibility and Accessibility: While providing support, it's important to maintain the flexibility of the fuel lines. Allow for slight bends and movement to accommodate engine operation and vehicle dynamics. Regularly check for any tight spots or areas where the lines might rub against other components, and adjust the routing as needed. Additionally, ensure that the lines are easily accessible for maintenance and inspections, as this will facilitate quick identification and resolution of any potential issues.
By following these routing and support techniques, you can ensure that the metal fuel lines are securely installed, providing efficient fuel delivery while minimizing the risk of damage or leaks. Regular inspections and adjustments will further contribute to the overall reliability of the fuel system.
Clogged Fuel Line: How It Affects Your Car's Performance
You may want to see also
Fittings and Connections: Ensure tight, leak-free fittings with proper torque and sealing
When working with metal fuel lines, ensuring tight and secure connections is crucial to prevent leaks and maintain the integrity of your fuel system. Here's a detailed guide on how to achieve leak-free fittings:
Understanding the Importance of Proper Connections:
Metal fuel lines are designed to transmit fuel efficiently and safely. However, any compromise in the connections can lead to fuel leaks, which may result in engine performance issues, potential fires, or environmental hazards. Therefore, it's essential to follow the correct procedures for fittings and connections.
Gathering the Right Tools and Materials:
Before beginning the installation, ensure you have the necessary tools and materials. This includes wrenches or torque wrenches of the appropriate size for the fittings, sealing compounds or tape, and any specific tools required for the type of fittings you are using. Having the right tools will make the process easier and more efficient.
Steps for Tight and Secure Fittings:
- Prepare the Fittings: Start by cleaning the male and female ends of the fuel lines. Remove any debris or old sealing compounds. Ensure the threads are smooth and free from damage.
- Apply Sealing Compound: Use a suitable sealing compound or tape specifically designed for fuel lines. Apply a thin layer around the male fitting, ensuring it covers the threads. This provides an additional layer of protection against leaks.
- Thread Alignment: When connecting the fittings, align the male and female ends carefully. Ensure the threads are properly engaged and aligned. Over-tightening can damage the fittings, so use a torque wrench to apply the correct amount of force.
- Torque and Tightening: Tighten the fittings using the appropriate torque specifications provided by the manufacturer. This ensures a secure connection without causing damage. Follow the recommended torque values to the letter to achieve a leak-free seal.
- Final Check: After tightening, inspect the connections for any signs of leakage. Apply pressure to the fittings and observe for any fuel escaping. If everything is secure, your fuel lines should now have tight and leak-free connections.
Remember, taking the time to properly prepare and tighten the fittings will contribute to the overall reliability and safety of your fuel system. Always refer to the manufacturer's guidelines for specific torque values and fitting instructions to ensure compatibility and optimal performance.
Mastering the Art of GM Fuel Line Clip Removal: A Step-by-Step Guide
You may want to see also
Inspection and Maintenance: Regularly check for corrosion, damage, and leaks
Regular inspection and maintenance of metal fuel lines are crucial to ensure the safe and efficient operation of any vehicle or equipment that relies on a fuel system. Metal fuel lines are susceptible to various issues over time, including corrosion, damage, and leaks, which can lead to costly repairs and potential safety hazards. Here's a comprehensive guide on how to inspect and maintain these vital components:
Visual Inspection: Start by performing regular visual inspections of the metal fuel lines. Look for any visible signs of deterioration, such as rust, pitting, or discoloration. Check for bends, kinks, or any physical damage that may have occurred during installation or due to road debris. Pay close attention to the connections and fittings, as these areas are prone to wear and tear. Inspect the lines for any signs of leakage, especially around the fittings and where the lines connect to the fuel tank and engine. Even a small leak can lead to fuel wastage and potential engine issues.
Corrosion Detection: Corrosion is a common enemy of metal fuel lines, especially in marine or outdoor environments. Use a magnifying glass or a flashlight to examine the lines for any signs of corrosion. Look for a white or blueish-green powdery substance, which indicates the presence of rust. Corrosion can weaken the metal over time, leading to potential failures. If you notice any corrosion, it's essential to address it promptly. You can use specialized corrosion inhibitors or, in severe cases, replace the affected sections of the fuel lines.
Leak Testing: Ensuring the integrity of the fuel lines is crucial to prevent fuel leaks. One effective method is to use a fuel line pressure tester. This tool applies pressure to the fuel lines and listens for any hissing sounds, indicating a potential leak. Alternatively, you can temporarily disconnect the fuel lines and use a soapy water solution to check for bubbles, which would signify a leak. If a leak is detected, immediately secure the line or replace it to prevent fuel loss and potential engine damage.
Regular Maintenance: Implement a regular maintenance schedule to keep your metal fuel lines in optimal condition. This includes periodic cleaning to remove any built-up fuel residue or contaminants. Use a fuel line cleaner and a brush to scrub the lines, ensuring you reach all areas. Additionally, consider using a fuel stabilizer, especially for long-term storage, to prevent fuel degradation. Regular maintenance will help extend the life of the fuel lines and reduce the risk of unexpected failures.
By following these inspection and maintenance procedures, you can ensure that your metal fuel lines remain reliable and efficient. Regular checks will help identify issues early on, allowing for prompt repairs or replacements, ultimately saving you from potential breakdowns and costly repairs. Remember, proper maintenance is key to keeping your vehicle or equipment running smoothly and safely.
Fuel Line Blow-Off Filter: Causes, Fixes, and Prevention Tips
You may want to see also
Safety Precautions: Wear protective gear and follow safety protocols during installation and repairs
When working with metal fuel lines, prioritizing safety is paramount. The process involves handling high-pressure fuel, which can be dangerous if not managed properly. Here are some essential safety precautions to adhere to:
Protective Gear: Prior to beginning any installation or repair work, ensure you are adequately protected. Wear safety goggles to shield your eyes from potential splashes or debris. Gloves are crucial to prevent direct contact with fuel, as it can be harmful if ingested or absorbed through the skin. Consider wearing a respirator mask to avoid inhaling any fumes or vapors that may be released during the process. Additionally, don't underestimate the importance of ear protection; the sound of fuel being pumped can be loud, and prolonged exposure can lead to hearing damage.
Safety Protocols: Familiarize yourself with the specific safety guidelines provided by the manufacturer of the fuel lines and the equipment you are using. These protocols often include instructions on proper ventilation, especially when working in enclosed spaces. Ensure that the work area is well-ventilated to minimize the risk of fuel vapor accumulation, which can be highly flammable. Keep a fire extinguisher nearby, specifically rated for fuel or flammable liquid fires, and ensure all personnel are trained in its use.
During the installation or repair process, maintain a clear and organized workspace. This reduces the risk of accidents caused by tripping or falling objects. Use appropriate tools and ensure they are in good condition to avoid any sharp edges or protruding parts that could cause injury. Regularly inspect the fuel lines for any signs of damage or wear, and replace them if necessary to prevent potential leaks and ensure the safety of the fuel system.
Remember, safety should always be the top priority when dealing with fuel lines. By wearing the right protective gear and adhering to strict safety protocols, you can significantly reduce the risks associated with this work, ensuring a safer environment for both yourself and those around you.
F150 Fuel Line: Understanding Proper Ratings and Safety
You may want to see also
Frequently asked questions
Metal fuel lines, often made from materials like stainless steel or aluminum, offer several advantages over traditional rubber hoses. They are more durable and can withstand higher temperatures, making them ideal for high-performance vehicles or those operating in extreme conditions. Metal lines also provide better flexibility and resistance to corrosion, ensuring a longer-lasting and more reliable fuel delivery system.
Selecting the appropriate metal fuel line depends on various factors. Consider the vehicle's engine size, fuel requirements, and the desired performance level. You should also check the compatibility with your vehicle's fuel system, including the fuel pump and injectors. It's recommended to consult a professional or refer to the manufacturer's guidelines to ensure you choose the right diameter, material, and length to match your specific needs.
Installing metal fuel lines may require some specialized tools and techniques. Due to the rigid nature of metal, you might need a fuel line cutter or a tube cutter to ensure precise and clean cuts. It's important to have the necessary plumbing tools, such as crimping tools or line connectors, to securely attach the lines. Additionally, understanding the vehicle's layout and having experience with fuel system installations will make the process smoother. Proper sealing and sealing compounds should also be used to prevent fuel leaks.