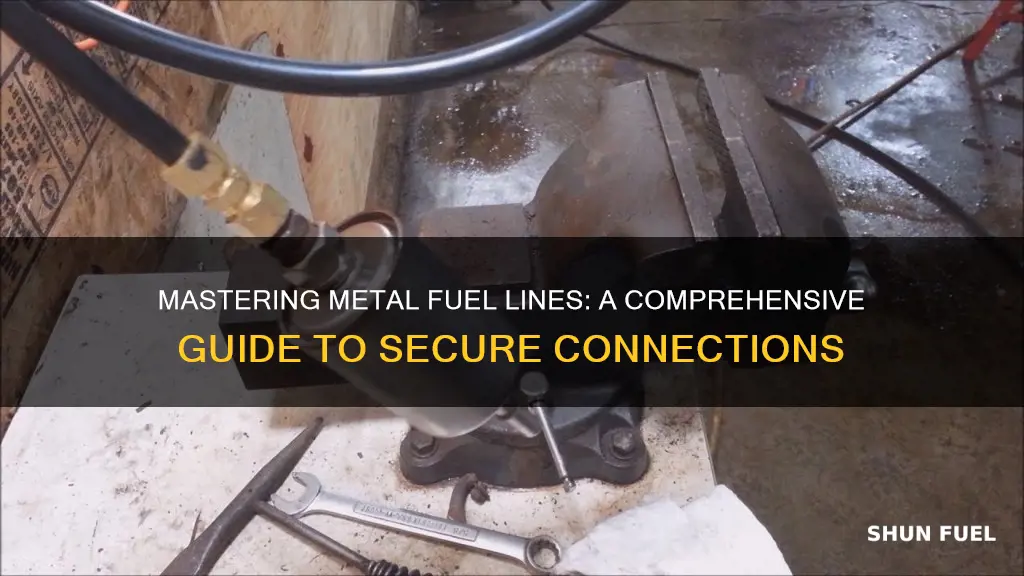
Connecting metal fuel lines requires careful preparation and adherence to safety guidelines. Before beginning, ensure you have the necessary tools and materials, including fuel line, fittings, and a suitable solvent or adhesive. Start by cleaning the ends of the fuel lines and fittings to remove any dirt or debris. Then, apply the solvent or adhesive as per the manufacturer's instructions, allowing sufficient time for it to take effect. Carefully insert the fuel line into the fitting, ensuring a snug fit, and use a wrench to tighten the connection securely. Finally, inspect the connection for any leaks and make adjustments if necessary. Properly connecting metal fuel lines is crucial for maintaining a safe and efficient fuel system in vehicles or equipment.
What You'll Learn
- Prepare Tools: Gather necessary tools like fuel line connectors, wrenches, and cleaning supplies
- Inspect Lines: Check for damage, bends, and proper length before connecting
- Clean Surfaces: Ensure metal surfaces are free of dirt, rust, and debris
- Connect Securely: Tighten connections firmly, following manufacturer's guidelines
- Test for Leaks: After installation, check for any fuel leaks using a soapy water solution
Prepare Tools: Gather necessary tools like fuel line connectors, wrenches, and cleaning supplies
Before you begin the process of connecting metal fuel lines, it's crucial to ensure you have the right tools and supplies ready. This preparation will make the task more efficient and help you avoid any unnecessary complications. Here's a step-by-step guide on what you need to gather:
Fuel Line Connectors: These are essential components that allow you to join the metal fuel lines together securely. Look for high-quality connectors that are designed for the specific size and type of fuel line you are working with. Ensure they are compatible with the material to prevent any leaks or damage.
Wrenches: You will require various wrenches to tighten the connectors and ensure a proper seal. Get a set of adjustable wrenches that can accommodate different sizes of nuts and bolts. This will enable you to work with various fuel line fittings and ensure a tight connection.
Cleaning Supplies: Cleaning is an often-overlooked but crucial step in the process. Gather some cleaning agents specifically designed for fuel systems. These products will help remove any dirt, corrosion, or contaminants from the fuel lines, ensuring a clean and reliable connection. Additionally, have some rags or cleaning cloths ready for wiping down the surfaces.
Safety Gear: While not strictly a tool, it's essential to prioritize safety. Wear protective gloves to shield your hands from any sharp edges or potential hazards. Safety goggles are also recommended to protect your eyes during the process, especially when handling fuel lines and connectors.
Having these tools and supplies prepared beforehand will make the fuel line connection process smoother and safer. It ensures that you have everything readily available, allowing you to focus on the task at hand without interruptions. Remember, proper preparation is key to a successful and leak-free fuel line installation.
Polaris Fuel Line Connector: Unlocking the Mystery of Bundy Compatibility
You may want to see also
Inspect Lines: Check for damage, bends, and proper length before connecting
Before attempting to connect any metal fuel lines, it is crucial to thoroughly inspect them to ensure optimal performance and safety. Start by visually examining the lines for any signs of damage, including tears, punctures, or corrosion. Metal fuel lines can be susceptible to wear and tear over time, especially in areas where they are exposed to the elements or under the vehicle. Look for any visible signs of deterioration that could compromise the integrity of the line.
Next, check the flexibility and bendability of the fuel lines. Metal lines should be able to conform to the natural contours of the engine bay without excessive bending or kinking. If you encounter sections that are overly rigid or prone to bending, it may indicate a potential issue with the line's material or previous damage. Ensure that the lines can move freely without causing strain on the connections or the vehicle's components.
Proper length is another critical aspect of inspection. Measure the fuel lines to confirm they are the correct length for your specific vehicle and engine setup. Inadequate length can result in poor fuel delivery, while lines that are too long may create unnecessary drag and potential hazards. Compare the measured length with the manufacturer's specifications to ensure accuracy.
During the inspection, pay attention to any existing bends or kinks in the lines. Metal fuel lines should maintain a smooth and straight path, avoiding sharp bends that could restrict fuel flow or cause damage over time. If you notice any unusual bends, consider straightening them carefully using a gentle, steady force. Avoid forcing the lines into unnatural positions to prevent potential damage or stress on the connections.
By thoroughly inspecting the metal fuel lines for damage, flexibility, length, and bends, you can ensure a secure and efficient connection. This process is essential for maintaining the vehicle's performance and safety, as well as preventing potential fuel leaks or system failures. Remember, proper inspection and attention to detail are key to a successful fuel line installation or repair.
Mastering Ford Fuel Line Connector Removal: A Step-by-Step Guide
You may want to see also
Clean Surfaces: Ensure metal surfaces are free of dirt, rust, and debris
When preparing to connect metal fuel lines, it's crucial to start with clean and prepared surfaces. This step is often overlooked but is essential for a secure and reliable connection. Here's a detailed guide on how to ensure your metal surfaces are free of dirt, rust, and debris:
Surface Preparation: Begin by thoroughly cleaning the metal surfaces that will be in contact with the fuel lines. Use a mild detergent or a specialized metal cleaner to remove any dirt, grease, or grime. Scrub the surfaces gently but effectively to ensure no residue remains. Rinse the area with water to eliminate any cleaning product and allow the metal to dry completely.
Rust Removal: Rust can be a significant issue when connecting metal fuel lines, as it can lead to corrosion and potential leaks. To address this, use a wire brush or a specialized rust remover to scrub away any rust deposits. Pay close attention to any existing holes or imperfections, as these areas may require extra care. For more severe rust, consider using a wire wheel or an abrasive pad to remove the affected layer of metal, ensuring a clean and smooth surface.
Debris and Contaminants: After cleaning and rust removal, inspect the surfaces for any remaining debris or contaminants. Use a fine-tipped tool or a small brush to carefully remove any small particles that might interfere with the connection. Ensure that the entire surface is free from any foreign matter before proceeding.
Drying and Inspection: Once the cleaning and preparation process is complete, allow the metal surfaces to dry thoroughly. Moisture can affect the bonding process and the overall integrity of the connection. After drying, inspect the surfaces again to ensure they are clean, smooth, and free from any contaminants.
By following these steps, you create an optimal environment for connecting metal fuel lines, ensuring a strong bond and minimizing the risk of leaks or corrosion. Proper surface preparation is a critical aspect of any fuel system installation or repair, promoting safety and longevity.
Mastering the Art of Draining Gas: A Step-by-Step Guide
You may want to see also
Connect Securely: Tighten connections firmly, following manufacturer's guidelines
When connecting metal fuel lines, ensuring a secure and tight connection is crucial to prevent fuel leaks and potential hazards. Here's a step-by-step guide to achieving a reliable connection:
Start by preparing the fuel lines and fittings. Clean the surfaces to remove any dirt, corrosion, or debris. This ensures a proper bond between the metal components. Use a suitable solvent or cleaner specifically designed for fuel line maintenance to ensure a clean and dry surface.
Next, inspect the fittings and lines for any signs of damage or wear. Look for cracks, bends, or any imperfections that might compromise the integrity of the connection. If any issues are found, replace the affected parts to ensure a safe and functional setup.
Now, it's time to tighten the connections. Follow the manufacturer's guidelines for the specific fuel line system you are using. Typically, you will need a wrench or a specialized tool to apply the correct amount of force. Start by tightening the fittings hand-tight, ensuring they are secure but not overly tight. Then, use the appropriate tool to make final adjustments, applying firm pressure to create a tight seal.
Remember, the goal is to achieve a secure connection without over-tightening, which can cause damage to the metal components. Use a torque wrench if available to ensure you are applying the correct amount of force as per the manufacturer's specifications. This precision will help prevent fuel line failure and potential engine issues.
After tightening, inspect the connections again to ensure they are intact. Check for any leaks by applying a small amount of fuel to the joints and observing for any signs of leakage. If everything is secure, your fuel lines should now be safely connected and ready for use.
Mastering the Art of Fuel Line Removal: A 1966 Mustang Guide
You may want to see also
Test for Leaks: After installation, check for any fuel leaks using a soapy water solution
After completing the installation of metal fuel lines, it is crucial to conduct a thorough leak test to ensure the system's integrity and prevent potential hazards. This step is often overlooked, but it is an essential safety measure to guarantee that no fuel escapes and that the system is leak-free. Here's a detailed guide on how to perform this test effectively:
Prepare the necessary materials: You will need a soapy water solution, a spray bottle or a small pump sprayer, and a clean cloth. Mix a few drops of dish soap with water to create the soapy mixture. The soap acts as a visual indicator, making it easier to spot any leaks. Ensure the soapy water is not too concentrated, as it might not be as effective.
Start the test by disconnecting the fuel lines from the fuel tank and any other connected components temporarily. This step is important to isolate the system and ensure that any potential leaks are contained. Use a wrench or pliers to carefully loosen the connections, being mindful not to damage the threads or fittings.
Now, apply the soapy water solution to all the connections and joints of the metal fuel lines. Pay close attention to the areas where the lines connect to the fuel tank, pumps, and any other fuel-related components. Spray or carefully pour the soapy water onto these points, ensuring an even coverage. The soap will create a lather if there is a leak, making it visible.
Observe the fuel lines and the surrounding areas for any signs of fuel escaping. Look for bubbles or a soapy lather forming around the connections. If you notice any, it indicates a potential leak. Additionally, check for any wet spots or stains on the ground or nearby surfaces, as these could also be signs of fuel leakage.
If you detect any leaks, immediately shut off the fuel supply and address the issue. Tighten loose connections, replace damaged fittings, or seek professional assistance if the problem persists. Ensuring a leak-free system is vital for safety and to maintain the efficiency of your fuel system.
Remember, this test is a critical step in the process of connecting metal fuel lines, and it should not be skipped. By following these instructions, you can effectively identify and rectify any potential issues, ensuring a secure and reliable fuel system.
Mastering Husqvarna's Fuel Line: A Step-by-Step Guide
You may want to see also
Frequently asked questions
Connecting metal fuel lines requires careful preparation and the right tools to ensure a secure and leak-free connection. Here's a step-by-step guide: First, ensure both ends of the fuel lines are clean and free of any debris. Use a wire brush or a cleaning tool to remove any dirt or corrosion. Then, apply a thin layer of fuel line tape or a suitable adhesive to the male end of the fuel line. Insert the male end into the female connector, ensuring it is fully seated. Tighten the connector securely using a fuel line tool or a wrench, being careful not to overtighten. Finally, inspect the connection for any leaks by applying pressure and checking for any signs of fuel escaping.
While a regular hose clamp might seem like a quick fix, it is not the most reliable method for securing metal fuel lines. Hose clamps are designed for rubber or flexible materials and may not provide the necessary grip and strength for metal lines. Instead, consider using a fuel line clamp specifically designed for metal fuel lines, which offers a more secure and durable connection. These clamps are typically made of sturdy materials and provide a tight grip, reducing the risk of leaks.
Corrosion can be a concern when working with metal fuel lines, especially in environments with high moisture content. To prevent corrosion, it's essential to clean and prepare the fuel lines properly. Use a wire brush to remove any existing corrosion and ensure a clean surface. Applying a thin layer of anti-corrosion paint or a suitable lubricant can also help protect the metal. Additionally, consider using fuel line tape or a protective sleeve to further shield the connection from moisture and contaminants.
Yes, you'll need a few specialized tools to ensure a proper connection. A fuel line tool, also known as a fuel line crimper, is essential for tightening the connectors securely. This tool applies the right amount of force to create a tight seal. You may also require a wire brush, cleaning tools, and fuel line tape or adhesive to prepare the lines and ensure a leak-free connection. It's a good idea to have these tools readily available before starting the connection process.
If you come across a kink or bend in the metal fuel line, it's important to address it immediately. Kinks can restrict fuel flow and potentially cause leaks. Carefully straighten the line by gently pulling and adjusting it. Avoid forcing the line, as it may lead to damage. If the bend is significant or persistent, consider replacing the affected section of the fuel line to ensure optimal performance and safety. Regularly inspect the lines for any damage during and after the installation process.