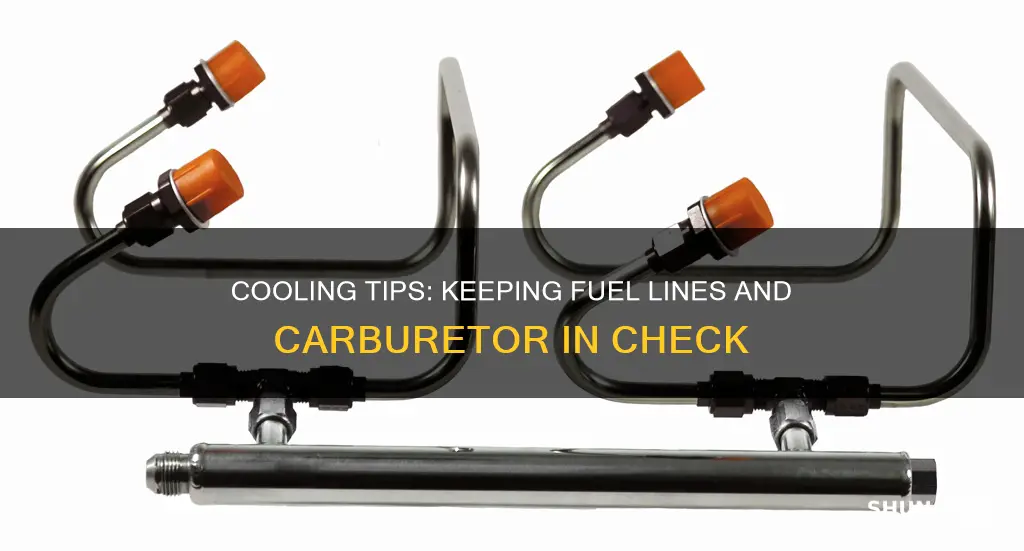
Maintaining the optimal temperature of fuel lines and the carburetor is crucial for the efficient operation of any engine. High temperatures can lead to fuel line degradation, reduced performance, and even engine failure. This guide will explore various methods to ensure these components remain cool, including the use of heat shields, proper insulation, and the benefits of a well-maintained engine bay. By implementing these strategies, you can ensure your engine runs smoothly and reliably, even in demanding conditions.
Characteristics | Values |
---|---|
Insulation | Use heat-resistant insulation materials such as rubber, plastic, or metal sleeves to cover fuel lines and the carburetor. Ensure proper fit and secure attachment to prevent movement. |
Shielding | Install heat shields made of metal or heat-resistant materials around the carburetor and fuel lines, especially if they are exposed to direct heat sources like exhaust systems or engine components. |
Coolant System | Implement an efficient cooling system for the engine, including radiators, fans, and coolant circulation. This helps maintain lower engine temperatures, indirectly keeping fuel lines and the carburetor cool. |
Airflow Management | Ensure proper airflow around the engine bay. Use baffles or air deflectors to direct air away from the carburetor and fuel lines, preventing heat buildup. |
Regular Maintenance | Periodically inspect and clean the fuel system, including lines and the carburetor. Remove any debris or deposits that may insulate the components, leading to overheating. |
Fuel Line Routing | Route fuel lines away from hot engine components and under the hood where temperatures are generally lower. Avoid tight bends or kinks that could restrict flow and cause localized heating. |
Material Selection | Choose fuel lines and carburetor components made from heat-resistant materials. Some manufacturers offer specialized parts designed to withstand higher temperatures. |
Engine Placement | Consider the engine's position in the vehicle. Engines mounted in the front or behind the firewall may have different cooling requirements, affecting the cooling of fuel lines and the carburetor. |
Thermal Barrier Coatings | Apply thermal barrier coatings to critical engine components, including the carburetor and fuel lines, to reduce heat absorption and transfer. |
Engine Tuning | Optimize engine performance and fuel injection settings to minimize excess heat generation. Proper tuning can improve overall engine efficiency and reduce the risk of overheating. |
What You'll Learn
- Insulation: Wrap fuel lines with heat-resistant material to prevent overheating
- Airflow: Ensure proper ventilation around the carburetor to dissipate heat
- Coolant Integration: Use a cooling system to maintain optimal engine temperature
- Fuel Line Length: Keep fuel lines short to minimize heat absorption
- Regular Maintenance: Inspect and replace worn-out components to prevent heat buildup
Insulation: Wrap fuel lines with heat-resistant material to prevent overheating
Insulating fuel lines is a crucial step in ensuring the longevity and optimal performance of your engine, especially in high-temperature environments. When fuel lines are exposed to excessive heat, they can overheat, leading to a variety of issues such as fuel degradation, reduced engine performance, and even potential fire hazards. One effective method to combat this is by wrapping the fuel lines with heat-resistant materials.
Heat-resistant insulation materials are designed to withstand high temperatures without compromising their structural integrity. These materials can be made from various compounds, including fiberglass, ceramic fibers, or specialized synthetic polymers. The key is to select an insulation that can effectively absorb and dissipate heat, preventing the fuel lines from overheating. Before applying the insulation, ensure that the fuel lines are clean and free of any debris or contaminants. This ensures a proper bond between the insulation and the fuel line.
The process of insulating the fuel lines involves carefully wrapping the heat-resistant material around the lines, ensuring complete coverage. Start by measuring the length of the fuel lines and cutting the insulation material accordingly. Begin wrapping at one end, applying enough pressure to create a snug fit. Continue wrapping in a spiral or zigzag pattern, overlapping the insulation slightly to ensure full coverage. Secure the insulation with ties or clips to prevent it from coming loose during engine operation.
For optimal results, consider using a heat-resistant tape or sleeve specifically designed for fuel lines. These products often provide a more professional finish and can be easily applied. When wrapping, ensure that the insulation is not twisted or kinked, as this can restrict fuel flow and cause further issues. Allow the insulation to settle and cure according to the manufacturer's instructions to ensure a long-lasting bond.
By implementing this insulation technique, you create a protective barrier around the fuel lines, effectively preventing overheating and maintaining the integrity of the fuel system. Regular maintenance and inspection of the insulated fuel lines are also recommended to identify and address any potential issues promptly. This simple yet effective method can significantly contribute to the overall health and performance of your engine, especially in demanding conditions.
Subaru Fuel Hanger Conundrum: Identifying the Right Lines
You may want to see also
Airflow: Ensure proper ventilation around the carburetor to dissipate heat
To maintain optimal performance and longevity of your fuel system, ensuring adequate airflow around the carburetor is crucial. Carburetors, being heat-sensitive components, require efficient cooling to prevent overheating, which can lead to performance issues and potential damage. Proper ventilation is the key to achieving this.
The primary method to enhance airflow is by ensuring the carburetor is positioned in a well-ventilated area. This can be achieved by installing a carburetor relocation kit, which allows for a more forward or side-mounted position, providing better access to cooler air. Alternatively, if your engine bay has limited space, consider using a carburetor air kit, which includes a small fan that blows air directly onto the carburetor, keeping it cool. These kits are especially useful in high-performance applications where heat dissipation is critical.
In addition to the carburetor's position, the overall engine bay ventilation plays a significant role. Ensure that the engine bay has sufficient air intakes and exhaust outlets to facilitate a smooth airflow. This can be done by checking and cleaning air filters regularly, as clogged filters restrict airflow, causing the carburetor and fuel lines to overheat. Proper ventilation in the engine bay also helps in maintaining a stable engine temperature, which is beneficial for overall engine health.
Another effective way to improve airflow is by adding additional cooling components. For instance, an engine oil cooler can help regulate the engine's temperature, which in turn keeps the carburetor and fuel lines cooler. Similarly, an intercooler or supercharger air cooler can be beneficial in high-boost applications, ensuring that the air entering the engine is at a lower temperature, thus reducing the overall engine temperature.
In summary, maintaining proper airflow around the carburetor is essential for keeping fuel lines and the carburetor cool. This can be achieved through careful positioning of the carburetor, ensuring good engine bay ventilation, and the addition of cooling components. By implementing these measures, you can optimize the performance and longevity of your fuel system, ensuring a reliable and efficient engine operation.
Por 15 Fuel Tank Liner: Protect Your Engine's Heart
You may want to see also
Coolant Integration: Use a cooling system to maintain optimal engine temperature
The integration of a cooling system is a crucial aspect of maintaining optimal engine temperature, especially when it comes to keeping fuel lines and the carburetor cool. These components are susceptible to overheating, which can lead to reduced performance and potential damage. By implementing an efficient cooling system, you can ensure that your engine operates at its best while also extending the lifespan of these critical parts.
One effective method is to utilize a liquid cooling system, often referred to as a radiator. This system involves a coolant, typically a mixture of water and ethylene glycol, that absorbs heat from the engine and carries it to the radiator. The radiator then dissipates this heat into the surrounding air, keeping the engine and its associated components, including the fuel lines and carburetor, at an optimal temperature. It is essential to use a high-quality coolant that provides excellent heat transfer properties and corrosion protection to ensure the longevity of the cooling system.
In addition to the radiator, consider installing a cooling fan assembly. These fans are strategically positioned to draw cool air over the engine and radiator, enhancing the cooling process. When the engine is under load or operating in hot conditions, the fans activate, providing an extra layer of protection against overheating. This simple yet effective addition can significantly improve the overall cooling capacity of your engine.
Furthermore, the design and placement of the fuel lines and carburetor play a vital role in their cooling. Ensure that these components are routed away from the engine's hot spots and are insulated to minimize heat transfer. Proper insulation can be achieved using materials like rubber or plastic sleeves, which provide a barrier between the hot engine components and the fuel lines/carburetor. This insulation helps maintain the desired temperature and prevents overheating, especially during prolonged operation.
Regular maintenance and monitoring of the cooling system are essential. Check the coolant level and condition regularly, as it can absorb contaminants and require replenishment or replacement over time. Additionally, inspect the radiator and cooling fans for any signs of damage or blockages, ensuring they function optimally. By staying proactive with maintenance, you can guarantee that your engine, fuel lines, and carburetor remain cool and perform at their peak efficiency.
Unleash the Power: NICOPP Lines for Fuel Efficiency
You may want to see also
Fuel Line Length: Keep fuel lines short to minimize heat absorption
The length of fuel lines plays a crucial role in maintaining the temperature of your fuel system, especially in high-performance engines. Longer fuel lines can lead to increased heat absorption, which can negatively impact the performance and longevity of your engine. Here's why keeping fuel lines short is essential and how it contributes to keeping your carburetor cool:
Reduced Heat Transfer: When fuel lines are long, they act as a conduit for heat transfer between the engine and the fuel. This is undesirable because it can cause the fuel to heat up, leading to several issues. Firstly, hot fuel can lead to vaporization, which may result in a lean fuel-air mixture and reduced engine performance. Secondly, excessive heat can cause the fuel to degrade, leading to the formation of harmful byproducts that can clog the carburetor and injectors. By keeping fuel lines short, you minimize the distance over which heat can be transferred, thus keeping the fuel cooler and more stable.
Improved Engine Efficiency: Short fuel lines ensure that the fuel is delivered to the carburetor at a cooler temperature, which is essential for optimal engine operation. Cooler fuel has a higher density, allowing for better atomization and mixing with air. This results in a more efficient combustion process, where the fuel-air mixture is properly burned, providing maximum power output. In contrast, long fuel lines can lead to a warmer fuel temperature, which may cause the fuel to become less dense, leading to poor atomization and reduced engine performance.
Preventing Carburetor Issues: Carburetors are sensitive to fuel temperature, and excessive heat can cause them to malfunction. Long fuel lines can lead to a warmer carburetor, which may result in the following problems:
- Vapor Lock: Hot fuel can turn into vapor, causing it to lock up the carburetor and temporarily shut down the engine.
- Fuel Contamination: High temperatures can cause fuel degradation, leading to the formation of varnish and other contaminants that can block the carburetor passages.
- Poor Throttle Response: A warm carburetor may struggle to maintain a consistent fuel-air mixture, resulting in erratic engine behavior and a lack of throttle response.
Design Considerations: When designing or modifying your fuel system, it's essential to consider the length of the fuel lines. Aim for the shortest possible route from the fuel tank to the carburetor, ensuring that the lines are routed away from hot engine components. Proper insulation and the use of heat-resistant materials can also help minimize heat absorption. Additionally, consider using a fuel cooler, especially in high-performance applications, to further reduce the temperature of the fuel before it reaches the carburetor.
In summary, keeping fuel lines short is a critical aspect of maintaining a cool fuel system and ensuring optimal engine performance. By minimizing heat transfer, you can maintain the integrity of the fuel, improve engine efficiency, and prevent various carburetor-related issues. Proper fuel line design and routing are essential considerations for any engine builder or enthusiast looking to optimize their fuel delivery system.
Mastering the Art of Fuel Line Connection: A Comprehensive Guide
You may want to see also
Regular Maintenance: Inspect and replace worn-out components to prevent heat buildup
Regular maintenance is crucial to ensuring the longevity and optimal performance of your fuel system, especially when it comes to keeping fuel lines and the carburetor cool. Over time, various components can wear out, leading to increased heat buildup, which can cause performance issues and potential damage. Here's a guide on how to tackle this through regular inspections and timely replacements:
Inspecting for Wear and Tear: Start by regularly examining the fuel lines and carburetor for any signs of deterioration. Look for cracks, brittleness, or any visible damage. Fuel lines should be flexible and free from kinks or bends that could restrict flow. Check for any leaks or moisture accumulation, as this could indicate a compromised seal or a potential issue with the fuel pump. The carburetor, being a critical component, requires careful inspection. Look for any blockages, deposits, or signs of corrosion inside the carburetor jetting and passages. Ensure that all gaskets and seals are intact and functioning properly to maintain a tight seal and prevent heat-related issues.
Replacing Worn-Out Parts: Regular maintenance involves promptly replacing any worn-out or damaged components. For instance, if you notice fuel lines with cracks or leaks, it's essential to replace them immediately. Worn-out fuel filters should be replaced to ensure clean fuel delivery and prevent contamination. Over time, carburetor jets and needles may wear out, affecting the fuel-air mixture. Cleaning or replacing these components is vital to maintaining optimal performance and preventing heat-related engine issues. Additionally, check the condition of the carburetor gasket and ensure it is securely in place to avoid leaks and maintain a cool operating temperature.
Addressing Heat-Related Issues: Heat buildup can lead to reduced engine performance and potential damage. If you notice any signs of overheating, such as excessive smoke, strange noises, or a burning smell, it's crucial to investigate further. Inspect the fuel lines and carburetor for any blockages or restrictions that might be causing the heat. Ensure that the fuel pump is functioning correctly and delivering fuel efficiently. Regularly cleaning and maintaining the fuel system can prevent the accumulation of debris and contaminants, which can lead to heat-related problems.
Preventive Measures: Implementing preventive measures can significantly reduce the risk of heat buildup. Consider using fuel line insulators to protect the lines from heat and vibration. These insulators provide an extra layer of defense, especially in high-temperature environments. Additionally, maintaining a clean and well-ventilated engine bay can improve airflow and help keep the fuel system cool. Regularly checking and adjusting the air-fuel mixture can also prevent overheating and ensure efficient combustion.
By incorporating these regular maintenance practices, you can effectively manage the temperature of your fuel lines and carburetor, ensuring optimal performance and longevity. Remember, early detection and replacement of worn-out components are key to preventing heat-related issues and maintaining a healthy fuel system.
Poulan Pro 4620 AVHD Fuel Line Size: Expert Guide
You may want to see also
Frequently asked questions
One effective method is to use a fuel line insulator kit. These kits typically consist of protective sleeves or jackets made from heat-resistant materials that slide over the fuel lines. They help absorb and reflect heat, preventing the fuel from overheating and maintaining optimal temperatures. Additionally, consider using a heat shield for the carburetor, which can be made of metal or heat-resistant materials, to protect it from direct heat sources.
Yes, you can apply specialized coatings or insulators to the fuel lines. For example, a heat-resistant silicone coating can be used to line the interior of the fuel lines, providing an extra layer of protection against heat transfer. This can be especially useful for high-performance engines where fuel temperatures might rise.
The air intake system is crucial for proper cooling. Ensure that the air filter is clean and free of debris, as a clogged filter can restrict airflow, reducing the cooling effect. Consider using a high-flow air filter or an intake system with a heat shield to direct cooler air to the carburetor. Proper air intake management can significantly contribute to maintaining the desired temperature for the carburetor and fuel lines.