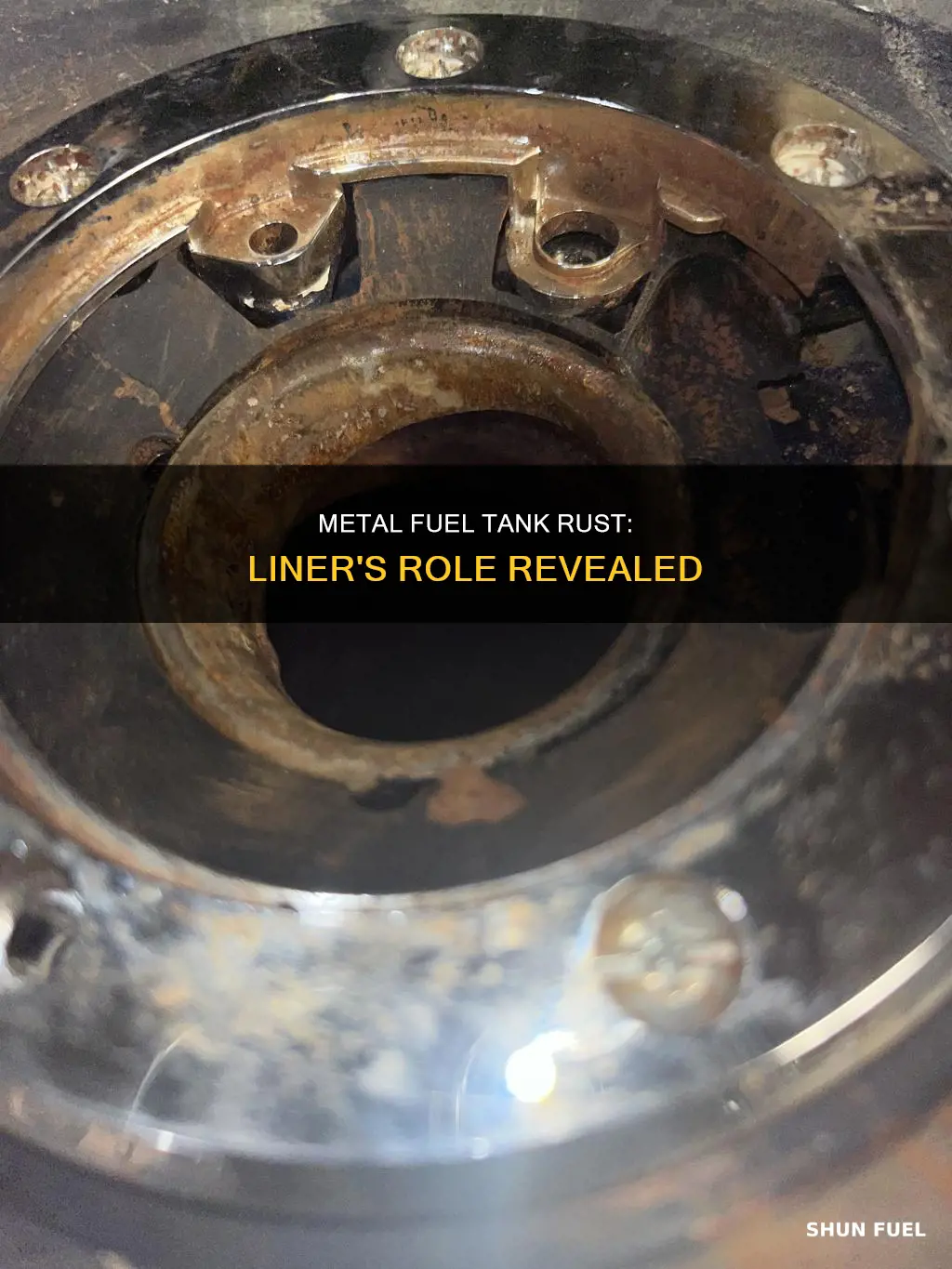
Metal fuel tanks, often used in vehicles and industrial applications, are susceptible to corrosion and rust without proper protection. The absence of a liner or coating can lead to rapid deterioration, especially in environments with high humidity or exposure to corrosive substances. Rusting not only weakens the tank's structural integrity but also poses a risk of fuel contamination, potentially affecting engine performance and safety. Understanding the impact of rust on metal fuel tanks is crucial for implementing effective preventive measures.
What You'll Learn
- Material Selection: Choosing corrosion-resistant metals for fuel tanks
- Coating Techniques: Applying protective coatings to prevent rust
- Environmental Factors: Impact of temperature, humidity, and chemicals on rusting
- Liner Alternatives: Exploring non-metal solutions for rust prevention
- Maintenance Practices: Regular inspections and cleaning to prevent corrosion
Material Selection: Choosing corrosion-resistant metals for fuel tanks
When designing fuel tanks, especially for vehicles or industrial applications, the choice of material is critical to ensure long-term durability and performance. One of the primary concerns is corrosion, which can significantly impact the tank's integrity and, consequently, the safety and efficiency of the system. Metal fuel tanks, without proper protection, are susceptible to rusting, especially in environments with high humidity or exposure to saltwater. This is where the concept of using corrosion-resistant metals becomes essential.
The primary goal is to select materials that can withstand the corrosive effects of fuel, moisture, and the surrounding environment. Stainless steel, for instance, is a popular choice due to its inherent corrosion resistance. It contains a high percentage of chromium, which forms a protective oxide layer on the surface, preventing further corrosion. This makes stainless steel an excellent option for fuel tanks, especially in marine or outdoor settings where exposure to moisture and saltwater is common. Another advantage of stainless steel is its strength and durability, ensuring the tank can withstand the pressures and stresses associated with fuel storage.
Aluminum alloys are also considered for fuel tank applications. These alloys offer excellent corrosion resistance, particularly in the presence of fuel and moisture. The natural oxide layer that forms on aluminum provides a protective barrier, making it suitable for fuel storage. Additionally, aluminum is lightweight, which can be a significant advantage in vehicles, reducing overall weight and improving fuel efficiency. However, it is essential to note that aluminum may not be as strong as stainless steel, so proper design and reinforcement might be required to ensure structural integrity.
For more specialized applications, such as those involving specific fuel types or extreme environmental conditions, other corrosion-resistant metals can be considered. For example, certain alloys of copper, nickel, and titanium offer excellent resistance to corrosion and can be tailored to meet specific requirements. These materials are often used in high-performance or specialized fuel systems where traditional steel or aluminum may not suffice.
In summary, the selection of corrosion-resistant metals for fuel tanks is a critical aspect of design and engineering. Materials like stainless steel, aluminum alloys, and specialized alloys provide the necessary protection against rust and corrosion, ensuring the longevity and reliability of fuel storage systems. Each material has its advantages and considerations, and the choice should be based on the specific needs of the application, including environmental factors, fuel type, and structural requirements.
Perfect Fuel Line Size for 7kW Onan Generator
You may want to see also
Coating Techniques: Applying protective coatings to prevent rust
Protecting metal fuel tanks from rust is crucial, especially when they lack a liner. Rust, or corrosion, can significantly weaken the tank's structural integrity and compromise its ability to store fuel safely. Here's an overview of various coating techniques to prevent rust and ensure the longevity of your metal fuel tank:
- Electrostatic Spray Coating: This method is highly effective for fuel tanks due to its ability to provide a uniform, thick coating. The process involves spraying a specialized coating material onto the tank's surface while it is grounded and connected to a power supply. The coating material is typically an epoxy or polyester resin, which is electrostatically charged and attracted to the grounded tank. This technique ensures complete coverage, even in hard-to-reach areas, and creates a strong bond with the metal surface. Electrostatic spray coating is durable and resistant to chipping, making it ideal for fuel tanks that require long-lasting protection.
- High-Temperature Baking: After the coating material is applied, it needs to be cured through a process called baking. This involves heating the coated tank to a specific temperature in an oven-like environment. The heat initiates a chemical reaction, hardening the coating and creating a robust, protective layer. High-temperature baking is commonly used for epoxy and polyurethane coatings, ensuring they adhere firmly to the tank's surface. This method is particularly useful for larger fuel tanks, as it provides excellent coverage and a seamless finish.
- Liquid Coating Application: Another effective technique is the application of liquid coatings, which can be brushed, sprayed, or dipped onto the tank's surface. This method is versatile and can be used for various coating materials, including zinc, aluminum, and specialized rust-inhibiting paints. Liquid coatings are easy to apply and can be tailored to specific tank shapes and sizes. For instance, a zinc coating can be applied through a process called galvanizing, where the tank is submerged in a bath of molten zinc, creating a protective zinc layer. This method is cost-effective and provides excellent corrosion resistance.
- Powder Coating: Powder coating is a popular choice for metal fuel tanks due to its durability and aesthetic appeal. The process involves spraying dry polymer particles onto the tank's surface, which then melt and bond to the metal under heat. This technique offers a wide range of color options and provides a smooth, uniform finish. Powder coating is highly resistant to chipping and peeling, making it an excellent long-term solution for fuel tanks. It also creates a non-porous barrier, preventing moisture and corrosive elements from reaching the metal surface.
When applying these coating techniques, it is essential to follow manufacturer guidelines and industry standards to ensure optimal protection. Proper surface preparation, including cleaning and priming, is crucial before applying any coating. Additionally, regular maintenance and inspections can help identify and address any potential rust issues early on, ensuring the fuel tank's longevity and safety.
Reagle Fuel Line Connections: A Comprehensive Guide
You may want to see also
Environmental Factors: Impact of temperature, humidity, and chemicals on rusting
The presence of a liner in a metal fuel tank is crucial for preventing rust, especially in environments exposed to moisture and chemicals. However, understanding the environmental factors that contribute to rusting is essential to fully grasp the implications of a metal fuel tank without a liner. Temperature, humidity, and chemical exposure are key elements that significantly influence the rate and extent of rust formation.
Temperature plays a critical role in the rusting process. Higher temperatures accelerate the oxidation of metal, leading to faster rust formation. In a fuel tank without a liner, the metal surface is directly exposed to the environment. When temperatures rise, the metal's surface becomes more susceptible to corrosion, especially in areas with poor ventilation. This is particularly relevant for fuel tanks used in vehicles or industrial settings, where temperature variations are common.
Humidity, the amount of water vapor in the air, is another significant factor. Moisture is a primary contributor to rusting as it provides the necessary water for the corrosion process. In regions with high humidity, a metal fuel tank without a liner would be at a higher risk of rusting. The water vapor condenses on the metal surface, creating an environment conducive to rust formation. Over time, this can lead to significant deterioration of the tank's structural integrity.
Chemical exposure is yet another critical aspect. Fuel tanks, especially those used for storing gasoline or diesel, are in contact with various chemicals. These chemicals can include additives, impurities, and even the fuel itself. When a metal tank lacks a protective liner, these chemicals directly interact with the metal surface. Certain chemicals can accelerate rusting, while others may form protective layers, depending on their composition and concentration. For instance, sulfur compounds in gasoline can promote rusting, while some fuel additives might provide a degree of protection.
In summary, the absence of a liner in a metal fuel tank leaves it vulnerable to environmental factors. Temperature, humidity, and chemical exposure collectively contribute to the rate and severity of rusting. Understanding these factors is essential for implementing effective preventive measures, such as choosing appropriate materials, using protective coatings, or ensuring proper ventilation and maintenance, especially in regions with challenging environmental conditions.
EFI Fuel Line Options: Exploring the Best Choices for Performance
You may want to see also
Liner Alternatives: Exploring non-metal solutions for rust prevention
The concept of using metal fuel tanks without liners is an intriguing one, especially in the context of rust prevention. While metal tanks are robust and durable, they are inherently susceptible to corrosion, especially when exposed to moisture and oxygen. This is where the idea of liners comes into play, providing an additional layer of protection against rust. However, exploring alternative methods to achieve rust prevention without a liner is an innovative approach.
One non-metal solution gaining traction is the use of specialized coatings. These coatings, often applied through electroplating or thermal spraying, create a protective barrier on the metal surface. Zinc plating, for instance, is a common method to prevent rust. It involves electroplating zinc onto the metal tank, forming a protective layer that sacrifices itself to the environment, thus protecting the underlying metal. This process is widely used in the automotive industry and can significantly extend the lifespan of fuel tanks.
Another innovative approach is the utilization of polymeric coatings. These coatings are designed to adhere to the metal surface and create a robust, non-porous barrier. Polymeric coatings can be applied through various methods, including spray painting or dip coating. They offer excellent resistance to corrosion and can be tailored to specific environmental conditions. For instance, a coating designed for marine environments might include additives to enhance its protective properties against saltwater corrosion.
Additionally, the concept of using composite materials as a protective layer is emerging. Composite materials, such as those made from glass fibers and resins, can be engineered to provide exceptional strength and corrosion resistance. These materials can be applied as a protective layer over the metal tank, creating a hybrid system that combines the benefits of both metal and non-metal solutions. The composite layer can be designed to withstand harsh conditions, ensuring the longevity of the fuel tank.
In conclusion, exploring non-metal solutions for rust prevention in metal fuel tanks opens up exciting possibilities. From specialized coatings to composite materials, these alternatives offer effective ways to protect against corrosion without the need for a traditional liner. Each method has its unique advantages and can be tailored to specific applications, ensuring that fuel tanks remain reliable and durable in various environments. This approach not only enhances the performance of fuel tanks but also contributes to more sustainable and innovative solutions in the automotive and energy sectors.
Unveiling Destiny 2's Fuel Line: Location Guide
You may want to see also
Maintenance Practices: Regular inspections and cleaning to prevent corrosion
Regular maintenance and inspections are crucial for preventing corrosion in metal fuel tanks, especially those without liners. The absence of a protective layer means that the metal surface is directly exposed to the elements, making it susceptible to rust and deterioration over time. Here are some essential practices to ensure the longevity and safety of your fuel tank:
Routine Inspections: Implement a regular inspection schedule to identify any signs of corrosion early on. Visual inspections should be thorough, covering all surfaces of the tank, including hard-to-reach areas. Look for any discolored or flaky paint, rust stains, or signs of deterioration. Pay close attention to joints, seams, and areas where the metal is bent or folded, as these spots are more prone to corrosion. Keep a record of your inspections, noting any issues found and the date of discovery. This documentation will help track the tank's condition and provide valuable information for maintenance planning.
Cleaning and Debris Removal: Regular cleaning is essential to remove contaminants that could accelerate corrosion. Use a mild detergent or a specialized cleaner designed for metal surfaces. Ensure the cleaning agent is compatible with the tank material to avoid any adverse reactions. After cleaning, thoroughly rinse the tank to eliminate any residue. Pay attention to removing debris and dirt, especially in areas where fuel accumulation might occur. Keep the tank's interior and exterior surfaces clear of any foreign matter that could contribute to corrosion.
Corrosion Inhibitors: Consider using corrosion inhibitors, which are chemical compounds that prevent or slow down the corrosion process. These inhibitors can be applied as a spray or coating to the metal surface. They work by forming a protective layer on the metal, reducing its exposure to corrosive elements. When choosing an inhibitor, select one suitable for the specific metal type and fuel used. Regularly reapply the inhibitor as per the manufacturer's instructions to maintain its effectiveness.
Environmental Considerations: Different environments have varying levels of corrosion potential. Tanks located in areas with high humidity, salt spray, or extreme temperatures may require more frequent maintenance. For instance, coastal regions with salty air will accelerate corrosion. In such cases, more aggressive cleaning and protective measures might be necessary. Understanding the environmental factors at play will help tailor your maintenance practices accordingly.
Professional Maintenance: While regular inspections and cleaning are essential, it is also beneficial to engage professional maintenance services periodically. Certified technicians can provide expert advice and perform specialized tasks. They can offer recommendations based on the tank's condition and environment, ensuring the best maintenance practices are followed. Professional maintenance can include power washing, specialized coatings, and comprehensive inspections.
Poulan PP3516AVX Fuel Line Length: Expert Guide
You may want to see also
Frequently asked questions
Yes, a metal fuel tank without a liner is susceptible to rusting, especially in environments with high humidity and exposure to moisture. Rust can form on the metal surface, leading to corrosion and potential damage to the tank over time.
A liner, typically made of a corrosion-resistant material like steel or aluminum, acts as a protective layer inside the fuel tank. It prevents direct contact between the fuel and the metal surface, reducing the likelihood of rust formation. Liners are designed to withstand the corrosive effects of fuel and moisture, ensuring the longevity of the tank.
Rusting in a metal fuel tank without a liner can be identified by visual inspection. Look for discolored or flaky areas on the tank's interior surface, which may indicate the presence of rust. Over time, rust can lead to reduced tank capacity, fuel contamination, and potential leaks. Regular maintenance and inspection are recommended to prevent extensive corrosion.