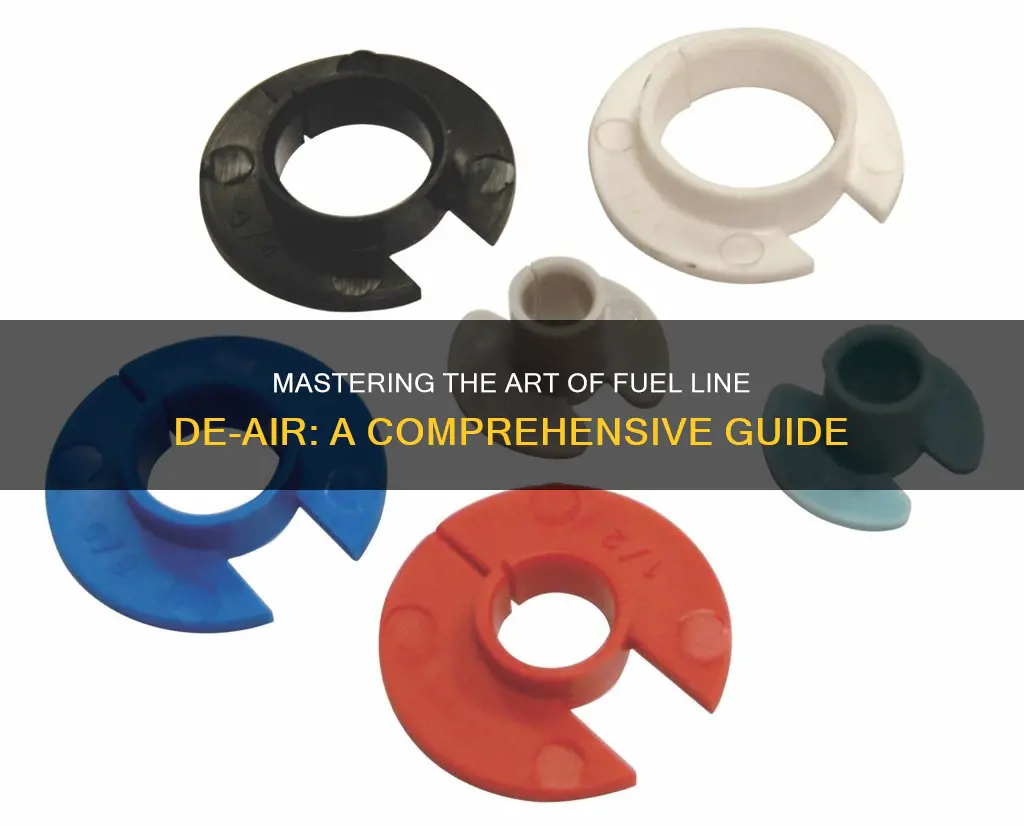
Getting air out of fuel lines is a crucial step in ensuring the efficient and safe operation of any vehicle's fuel system. This process, known as bleeding the fuel lines, involves removing any air bubbles that can cause performance issues and potential damage to the engine. By following a few simple steps, you can effectively eliminate air from the fuel lines, ensuring a smooth and reliable fuel supply to the engine.
What You'll Learn
- Bleeding the System: Use a hand pump or specialized tool to release air by opening and closing the valve
- Vacuum Pump Method: Employ a vacuum pump to create a low-pressure environment and draw out air
- Fuel Line Inspection: Check for any kinks or obstructions that might trap air
- Air Ventilation: Ensure all fuel tanks and lines have proper ventilation to prevent air buildup
- Fuel Filter Replacement: Regularly replace filters to prevent air from entering the fuel system
Bleeding the System: Use a hand pump or specialized tool to release air by opening and closing the valve
To effectively remove air from fuel lines, a process known as "bleeding the system" is essential. This method involves using a hand pump or a specialized tool to systematically release trapped air. Here's a step-by-step guide to ensure a successful outcome:
Start by locating the fuel lines and identifying the points where air can be released. Typically, these are the fuel lines that connect the fuel tank to the engine. Ensure you have the necessary tools, such as a hand pump or a specialized fuel line bleeding kit, which often includes a gauge and a flexible tube. These tools are designed to make the process easier and more efficient.
Next, locate the valve that controls the flow of fuel. This valve is usually positioned near the engine or the fuel tank. It is a critical component in the bleeding process. Open the valve to allow the air to escape. You might need to adjust the valve's position slightly to ensure it is fully open. This step is crucial as it provides an outlet for the air to be released.
Now, it's time to use the hand pump or specialized tool. Attach the tool to the fuel line, ensuring a secure connection. Apply pressure to the pump or tool, gradually increasing the force. As you do this, you should hear or feel the air being released from the system. The goal is to force the air out of the fuel lines and into the atmosphere. Take your time with this step, as it requires patience and a steady hand.
Continue this process of opening and closing the valve while applying pressure to the tool. Repeat this cycle until you no longer hear any air escaping. It's important to be thorough and consistent to ensure all air bubbles are eliminated. You may need to refer to your vehicle's manual for specific instructions on the location of the valve and the recommended procedure.
Once you've completed the bleeding process, carefully remove the tool and close the valve. Check for any leaks or unusual noises in the fuel system. If everything is functioning correctly, you should now have a fuel system free of air bubbles, ensuring optimal performance and fuel efficiency. Remember, this process may require some practice and adjustment to master, but it is a valuable skill for maintaining your vehicle's fuel system.
Understanding Fuel Impulse Lines: Their Role in Engine Performance
You may want to see also
Vacuum Pump Method: Employ a vacuum pump to create a low-pressure environment and draw out air
The vacuum pump method is an effective technique to eliminate air from fuel lines, ensuring optimal fuel delivery to the engine. Here's a step-by-step guide on how to achieve this:
Start by locating the fuel lines that need to be treated. These lines are typically found running from the fuel tank to the engine. It's crucial to identify the specific sections where air bubbles might be present, as these areas will be your primary focus. Once you've identified the target fuel lines, it's time to set up the vacuum pump.
Connect the vacuum pump to the fuel line, ensuring a secure and airtight connection. The pump should be positioned in a way that allows it to draw air out of the line effectively. Create a low-pressure environment by operating the vacuum pump. As the pump pulls air out of the system, it will create a vacuum, effectively drawing out any air bubbles present in the fuel lines. This process might take some time, so patience is key.
During the vacuum pumping process, keep an eye on the fuel line to ensure that the air is being extracted. You should notice a decrease in the line's pressure as the air is removed. If you encounter any resistance or difficulty in drawing out the air, it might indicate a blockage or a need for further inspection. In such cases, consider using a fuel line cleaner or a thin wire to clear any obstructions.
Once you've successfully drawn out the air, carefully disconnect the vacuum pump from the fuel line. Ensure that the connection is tight to prevent any air from re-entering the system. After disconnecting, start the engine and observe its performance. A well-executed vacuum pump method should result in a smooth and efficient engine operation, free from any air-related issues.
Remember, this method requires careful attention to detail and a systematic approach. It's an essential process for maintaining a healthy fuel system, ensuring that your engine receives clean, air-free fuel for optimal performance.
Finding the Perfect Fuel Line Fit for Your 2006 Scion TC
You may want to see also
Fuel Line Inspection: Check for any kinks or obstructions that might trap air
When inspecting fuel lines for air-related issues, it's crucial to look for any kinks or obstructions that could be trapping air and causing problems. Start by examining the fuel lines for any visible damage, such as cuts, punctures, or signs of corrosion. These issues can lead to air entering the lines, so any damage should be addressed promptly. Pay close attention to bends and fittings, as these areas are more susceptible to kinks and blockages. Ensure that all connections are secure and free from debris.
A common method to check for air is to use a fuel line inspection tool, often a flexible, bright-colored tube that can be inserted into the fuel line. This tool helps visualize any obstructions or air bubbles. Insert the tool into the fuel line, ensuring it is properly lubricated to avoid damaging the interior. As you push the tool through, feel for any resistance or changes in texture, which could indicate a kink or obstruction. If you encounter any issues, carefully straighten the line or remove the obstruction to restore proper flow.
Another technique is to listen for any unusual noises while the engine is running. Air in the fuel lines can cause a 'gurgling' or 'squeaking' sound, especially when the engine is idling or accelerating. If you notice these sounds, it may indicate the presence of air bubbles. To address this, you can try to bleed the fuel lines by removing the fuel filter and holding the line above the ground, allowing any air to escape.
Additionally, check for any signs of condensation or moisture in the fuel lines, as air can carry water vapor. Moisture in the fuel can lead to engine misfires and performance issues. If you find any moisture, consider using a fuel system drier or running the engine with the fuel line above the ground to expel any water.
Regular maintenance and inspections are key to preventing air-related problems in fuel lines. By being proactive and addressing any kinks, obstructions, or air bubbles, you can ensure optimal engine performance and longevity. Remember, proper fuel line care is essential for a reliable and efficient vehicle.
Mastering Autocraft Fuel Line Disconnect: A Step-by-Step Guide
You may want to see also
Air Ventilation: Ensure all fuel tanks and lines have proper ventilation to prevent air buildup
Air ventilation is a critical aspect of maintaining a healthy fuel system in vehicles, as it helps prevent air bubbles from forming and causing various performance issues. When air enters the fuel lines, it can lead to a host of problems, including engine misfires, reduced power, and even stalling. Ensuring that your fuel system is properly vented is a straightforward process that can be done at home with a few simple tools.
The primary goal of ventilation is to allow air to escape from the fuel system, particularly from the tank and lines, to prevent it from mixing with the fuel. This is essential because air is less dense than fuel, and when it enters the system, it can create bubbles, especially during the fueling process or when the engine is off. These bubbles can then rise through the lines, causing issues.
To ensure proper ventilation, you should start by checking the fuel tank's breathers. These are small openings usually located on the top of the tank, often with a small cover or mesh filter. Over time, these breathers can become clogged with dirt, dust, or debris, which can restrict airflow. Cleaning or replacing these breathers is a simple task and can be done with compressed air or a small brush to remove any obstructions. It's important to ensure that the breathers are secure and properly sealed to prevent any potential leaks.
In addition to the tank's breathers, the fuel lines themselves should also be checked for ventilation. If the lines are long or have multiple bends, they may require additional ventilation points. You can achieve this by installing small vents or bleeder valves along the length of the lines. These vents allow air to escape and can be easily installed using specialized fittings or by soldering small tubes into the lines. It's crucial to ensure that these vents are positioned correctly to allow air to escape without introducing any contaminants.
For vehicles with fuel tanks located in the trunk or rear of the vehicle, it's essential to check the ventilation of the fuel lines running from the tank to the engine. These lines may have built-in vents, but it's still a good practice to inspect and clean them periodically. If you notice any blockages or restrictions in the lines, you can use a fuel line brush or compressed air to clear them. Proper ventilation ensures that the fuel system operates efficiently, providing a clean and consistent fuel supply to the engine.
Quick Disconnect Fuel Line Removal: A Tool-Free Guide
You may want to see also
Fuel Filter Replacement: Regularly replace filters to prevent air from entering the fuel system
Fuel filters play a crucial role in maintaining the health and performance of your vehicle's fuel system. Over time, these filters can become clogged or damaged, allowing air to enter the fuel lines, which can lead to a host of problems. Regularly replacing the fuel filter is an essential part of vehicle maintenance to ensure optimal performance and prevent potential issues.
The primary function of a fuel filter is to trap contaminants, including water, dirt, and air bubbles, from the fuel before it reaches the engine. When a filter becomes dirty or worn, it may not effectively block these impurities, allowing them to pass through and enter the fuel lines. Air bubbles, in particular, can cause significant problems as they can lead to engine misfires, reduced power, and even stalling.
Replacing the fuel filter is a relatively straightforward process that can be performed by most vehicle owners. Here's a step-by-step guide to help you through the process:
- Locate the fuel filter: The filter is typically positioned along the fuel line, often near the engine or under the vehicle. Refer to your vehicle's manual for the exact location.
- Drain the fuel system: Before replacing the filter, it's essential to drain the fuel system to prevent any spills or mess. Turn the car off and locate the fuel drain valve, usually found under the vehicle near the fuel tank. Open the valve and allow the fuel to drain into a suitable container.
- Remove the old filter: Carefully detach the old filter by unscrewing or unclipping it from its mounting position. Take note of the filter's orientation to ensure you install the new one correctly.
- Install the new filter: Clean the mounting area and apply a thin layer of fuel filter sealant (if required) to the new filter. Slide the new filter into place, ensuring it is properly aligned and secured.
- Refill the fuel system: After replacing the filter, close the drain valve and allow the fuel to flow back into the system. Start the car and let it run for a few minutes to ensure the fuel is distributed evenly.
By regularly replacing the fuel filter, you can maintain a clean and efficient fuel system, preventing air from entering the lines and causing potential issues. This simple maintenance task can save you from costly repairs and ensure your vehicle runs smoothly. Remember to check your vehicle's manual for specific filter replacement intervals and recommendations.
Mastering the Art of Sealing Fuel Lines in Plastic Tanks
You may want to see also
Frequently asked questions
To eliminate air bubbles from fuel lines, you can start by locating the fuel pump and disconnecting the fuel line from it. Then, use a fuel line bleed valve or a small, sharp object to carefully create small punctures along the length of the line, allowing the air to escape. Ensure you bleed the system multiple times to ensure all bubbles are removed.
Air in fuel lines can lead to performance issues and potential damage to the engine. When air enters the fuel system, it can cause fuel to vaporize, leading to poor engine performance, reduced power, and even misfires. Removing air bubbles ensures a smooth and consistent fuel flow, allowing the engine to operate efficiently.
Yes, a fuel vacuum pump can be an effective tool for removing air from fuel lines. By creating a vacuum, the pump can draw out any air bubbles and ensure a positive fuel flow. Simply attach the pump to the fuel line and operate it for a few minutes to purge the system.
There are a few indicators that air bubbles might be present. These include engine misfires, reduced power, rough idling, and a noticeable decrease in fuel efficiency. If you notice any of these symptoms, it's essential to check for air in the fuel lines and take the necessary steps to remove it.