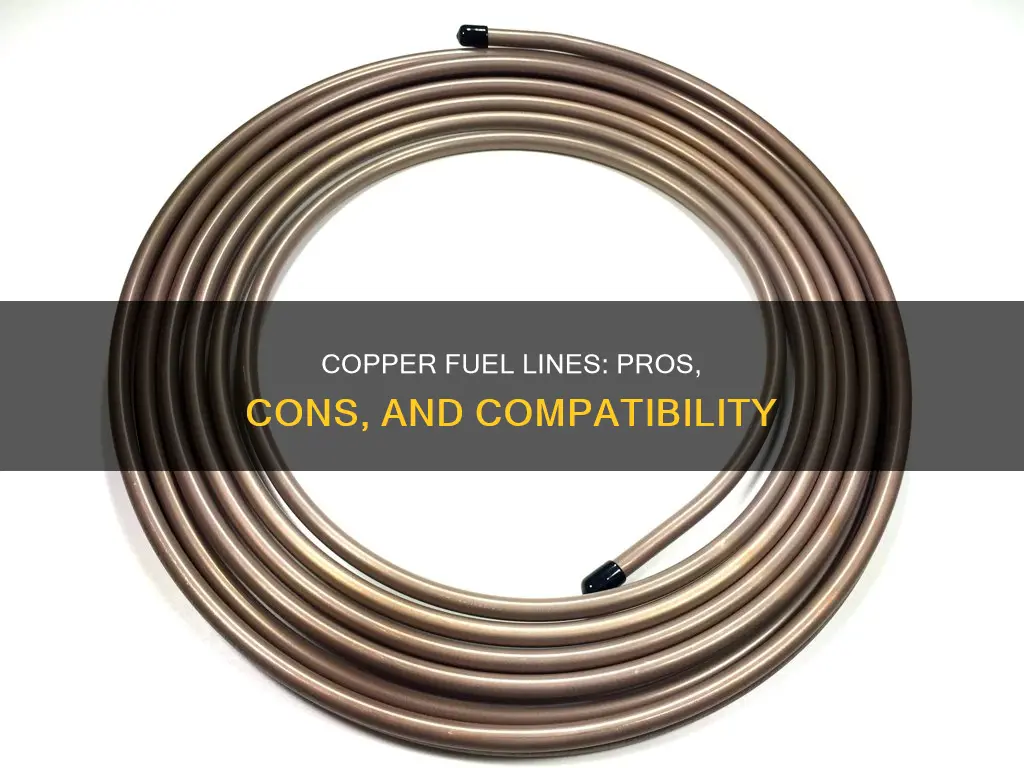
Copper is a popular material for various applications due to its excellent conductivity and durability. When it comes to fuel lines, the question arises: Can copper be used as a viable material? This paragraph will explore the feasibility and considerations of using copper for fuel lines, examining its advantages and potential challenges in this specific context.
Characteristics | Values |
---|---|
Corrosion Resistance | Excellent resistance to corrosion from fuel, especially when protected by an appropriate coating or plating. |
Flexibility | Good flexibility, allowing for some movement without kinking or breaking. |
Temperature Tolerance | Can withstand moderate temperatures, but may become brittle at very low or high temperatures. |
Pressure Rating | Typically rated for fuel line pressures, ensuring it can handle the typical pressure in a vehicle's fuel system. |
Cost | Generally more expensive than some other materials, but its durability and performance can justify the cost. |
Availability | Widely available and easy to source, making it a common choice for fuel lines. |
Installation | Can be easily bent and joined, facilitating installation and repair. |
Maintenance | Requires minimal maintenance, with no need for frequent replacement or cleaning. |
Compatibility | Compatible with most fuels, including gasoline, diesel, and biofuels, when properly selected and installed. |
Health and Safety | Non-toxic and non-reactive, making it safe for use in fuel systems. |
Environmental Impact | Can be recycled, contributing to sustainable practices. |
What You'll Learn
- Copper's Corrosion Resistance: Copper's natural protective oxide layer makes it suitable for fuel lines
- Copper's Conductivity: Copper's high thermal and electrical conductivity can improve fuel system efficiency
- Copper's Flexibility: Copper's flexibility allows it to bend and move with the vehicle's structure
- Copper's Strength: Copper's strength and durability make it suitable for fuel lines under pressure
- Copper's Cost: Copper's cost can be a factor, but its longevity may offset initial expenses
Copper's Corrosion Resistance: Copper's natural protective oxide layer makes it suitable for fuel lines
Copper is an excellent choice for fuel lines due to its natural corrosion resistance, which is primarily attributed to its unique ability to form a protective oxide layer. This natural process is a fascinating aspect of copper's chemistry, and it plays a crucial role in its suitability for various applications, including fuel systems.
When exposed to air, copper undergoes a process called 'patination,' where it reacts with oxygen and other elements in the environment to create a thin, green layer known as the patina. This patina is not just aesthetically pleasing but also highly protective. It acts as a barrier, preventing further oxidation and corrosion of the underlying copper material. In the context of fuel lines, this natural protective layer is highly advantageous.
The protective oxide layer formed on copper surfaces provides several benefits. Firstly, it significantly reduces the metal's reactivity with its surroundings, including fuels and other chemicals. This is essential for fuel lines, as it ensures that the copper material does not react with the fuel, potentially leading to contamination or performance issues. The oxide layer also makes copper highly resistant to corrosion, which is a critical factor in the longevity of fuel lines.
Moreover, the natural corrosion resistance of copper is particularly useful in fuel systems where the material is in constant contact with various substances. Copper's ability to form a protective oxide layer means that it can withstand the corrosive effects of fuels, ensuring that the fuel lines remain intact and functional over extended periods. This property is especially valuable in automotive and marine applications, where fuel lines are exposed to harsh environments and varying fuel compositions.
In summary, copper's natural corrosion resistance, facilitated by its protective oxide layer, makes it an ideal material for fuel lines. This unique characteristic ensures that copper fuel lines are durable, reliable, and capable of withstanding the challenges posed by different fuel types and environmental conditions. As a result, copper is a preferred choice for fuel line applications, offering both performance and longevity benefits.
Optimizing Performance: Choosing the Right Fuel Line for Your Honda GX 630
You may want to see also
Copper's Conductivity: Copper's high thermal and electrical conductivity can improve fuel system efficiency
Copper is an exceptional material for fuel lines due to its remarkable thermal and electrical conductivity. These properties are crucial in optimizing the performance of fuel systems, especially in high-performance vehicles and industrial applications. When considering the use of copper for fuel lines, it's essential to understand the role of conductivity in this context.
The high thermal conductivity of copper allows it to efficiently transfer heat, which is particularly beneficial in fuel systems where managing temperature is critical. In fuel lines, the flow of fuel can generate heat, especially during high-performance driving or when operating in hot environments. Copper's ability to quickly conduct and dissipate this heat helps prevent overheating, ensuring the fuel system operates within safe temperature limits. This is especially important in preventing fuel degradation and maintaining the overall efficiency of the engine.
Electrical conductivity is another key advantage of copper. Fuel systems often involve complex wiring and electronic components, and any electrical resistance in the fuel lines can lead to energy losses and reduced system efficiency. Copper's low electrical resistance ensures that the fuel system can transmit power and signals efficiently, reducing the risk of energy wastage and improving overall performance. This is particularly relevant in modern vehicles with advanced fuel injection systems and electronic controls.
Furthermore, the conductivity of copper contributes to the overall durability and reliability of the fuel system. Copper's ability to quickly transfer heat and manage electrical currents helps prevent the buildup of pressure and corrosion, which are common issues in fuel lines. This makes copper an ideal choice for fuel lines, especially in harsh operating conditions, as it can withstand temperature fluctuations and provide long-lasting performance.
In summary, copper's high thermal and electrical conductivity make it an excellent material for fuel lines. Its ability to manage heat and electrical currents efficiently contributes to improved fuel system efficiency, better performance, and increased durability. When considering fuel line materials, copper stands out as a reliable and high-performance option, ensuring optimal fuel delivery and engine operation.
Unveiling the Mystery: What Are Fuel Line Connectors Called?
You may want to see also
Copper's Flexibility: Copper's flexibility allows it to bend and move with the vehicle's structure
The flexibility of copper is a key advantage when considering its use for fuel lines in vehicles. Copper's inherent pliability allows it to adapt to the natural movement and shifting of a vehicle's structure during operation. This is particularly important in the automotive industry, where fuel lines need to withstand the rigors of the road and the various stresses placed on the vehicle's components.
When a vehicle is in motion, the engine, fuel tank, and associated components experience constant vibration and movement. Copper's flexibility ensures that the fuel lines can accommodate these movements without compromising the integrity of the fuel supply. Unlike rigid materials, copper can bend and adjust to the vehicle's contours, reducing the risk of damage or breakage. This is especially crucial in high-stress areas, such as the engine compartment, where fuel lines are exposed to extreme temperatures and mechanical forces.
The ability of copper to move with the vehicle's structure is a significant benefit in terms of long-term reliability. Over time, fuel lines made from less flexible materials may become brittle and prone to cracking or splitting. Copper, with its superior flexibility, can better resist fatigue and wear, ensuring a more durable and long-lasting fuel system. This is particularly important for vehicles that undergo frequent starts and stops, as well as those that operate in challenging environmental conditions.
Furthermore, copper's flexibility contributes to easier installation and maintenance. Its pliable nature allows for more straightforward routing of fuel lines, making the installation process less complex and time-consuming. This simplicity in installation can lead to cost savings and reduced labor time, which are essential considerations in the automotive manufacturing process. Additionally, when it comes to maintenance or repairs, copper's flexibility simplifies the task of replacing or adjusting fuel lines without causing unnecessary damage to the surrounding components.
In summary, copper's flexibility is a critical factor in its suitability for fuel lines in vehicles. Its ability to bend and move with the vehicle's structure ensures a more reliable and durable fuel system, capable of withstanding the various stresses and vibrations encountered during operation. This property, combined with its ease of installation and maintenance, makes copper an attractive material for fuel line applications in the automotive industry.
Unraveling the Mystery: The Perfect Wrench Size for Massey Ferguson Fuel Lines
You may want to see also
Copper's Strength: Copper's strength and durability make it suitable for fuel lines under pressure
Copper is an excellent choice for fuel lines due to its exceptional strength and durability, which are crucial for withstanding the pressures and demands of fuel transportation and distribution systems. The inherent strength of copper allows it to handle the rigorous conditions often encountered in fuel lines, ensuring a reliable and long-lasting solution.
One of the key advantages of copper is its ability to maintain structural integrity under pressure. Copper's high tensile strength means it can resist the forces exerted by the fuel flowing through the lines, preventing any potential damage or leaks. This is particularly important in fuel systems where pressure fluctuations can occur, ensuring that the fuel lines remain intact and functional.
The durability of copper is another critical factor in its suitability for fuel lines. Copper's resistance to corrosion and oxidation makes it highly durable, even in the presence of fuel chemicals and environmental factors. This durability ensures that the fuel lines will not deteriorate over time, maintaining the integrity of the fuel supply and reducing the risk of fuel contamination or system failures.
Furthermore, copper's flexibility and ease of installation contribute to its effectiveness in fuel line applications. Copper can be easily bent and shaped to fit various routes and layouts, allowing for efficient and customized fuel line designs. This flexibility, combined with its strength, ensures a secure and reliable connection, minimizing the chances of fuel leaks or system malfunctions.
In summary, copper's exceptional strength and durability make it an ideal material for fuel lines. Its ability to withstand pressure, resist corrosion, and offer flexibility during installation ensures a reliable and long-lasting fuel distribution system. When considering fuel line options, copper's performance and characteristics make it a top choice for professionals in the fuel industry.
Leaking Fuel Line: A Hidden Cause of Low Engine Idle
You may want to see also
Copper's Cost: Copper's cost can be a factor, but its longevity may offset initial expenses
The cost of copper can indeed be a significant consideration when deciding whether to use it for fuel lines. Copper is a premium material, and its price can vary depending on market fluctuations and the current demand. However, it's important to remember that copper's initial cost may be justified by its exceptional durability and longevity. While it might be more expensive upfront compared to some other materials, copper's resistance to corrosion and its ability to withstand high temperatures and pressures make it an excellent choice for fuel lines. This is especially true in marine or outdoor applications where exposure to the elements is a concern.
Over time, copper fuel lines can prove to be a cost-effective solution. Its durability ensures a longer lifespan, reducing the need for frequent replacements. This is particularly advantageous in high-demand or harsh environments where traditional fuel lines might fail prematurely. Copper's natural resistance to corrosion means it can handle the corrosive effects of fuel, ensuring a longer-lasting installation. While the initial investment might be higher, the long-term savings on maintenance and replacements can be substantial.
Additionally, copper's versatility allows for easy customization and fitting. It can be easily bent and shaped to accommodate various fuel line configurations, ensuring a secure and efficient installation. This flexibility can save time and labor during the installation process, further contributing to cost savings. Despite the initial expense, the overall cost-effectiveness of copper fuel lines becomes apparent when considering the reduced maintenance and replacement requirements.
In summary, while the cost of copper may be a factor, its longevity and durability make it a wise investment for fuel lines. The initial higher cost is often offset by the long-term benefits of reduced maintenance and increased lifespan. Copper's natural properties and ease of use also contribute to its appeal as a reliable and efficient material for fuel line applications.
Blower Fuel Lines: Location and Installation Guide
You may want to see also
Frequently asked questions
Copper is not typically recommended for fuel lines due to its reactivity with certain fuels, especially ethanol-blended gasoline. Copper can corrode and react with the fuel, leading to potential performance issues and contamination.
Copper has excellent thermal conductivity, making it efficient for heat dissipation. However, its primary drawback for fuel lines is its susceptibility to corrosion and reaction with fuels, which can compromise the integrity of the fuel system.
It is generally not advised to use copper fuel lines in vehicles. Copper's reactivity can cause fuel leaks, engine misfires, and potential damage to the fuel injection system. It's best to use materials like steel, stainless steel, or specialized fuel line compounds.
Copper is not compatible with most fuels. It is especially problematic with ethanol-containing fuels, as the ethanol can accelerate corrosion. Always refer to the manufacturer's guidelines and use materials approved for the specific fuel type.
To minimize corrosion, consider using a protective coating or lining on copper fuel lines. Some manufacturers offer specialized fuel line compounds that provide a barrier between the copper and the fuel. Regular maintenance and inspections can also help identify and address any potential issues.