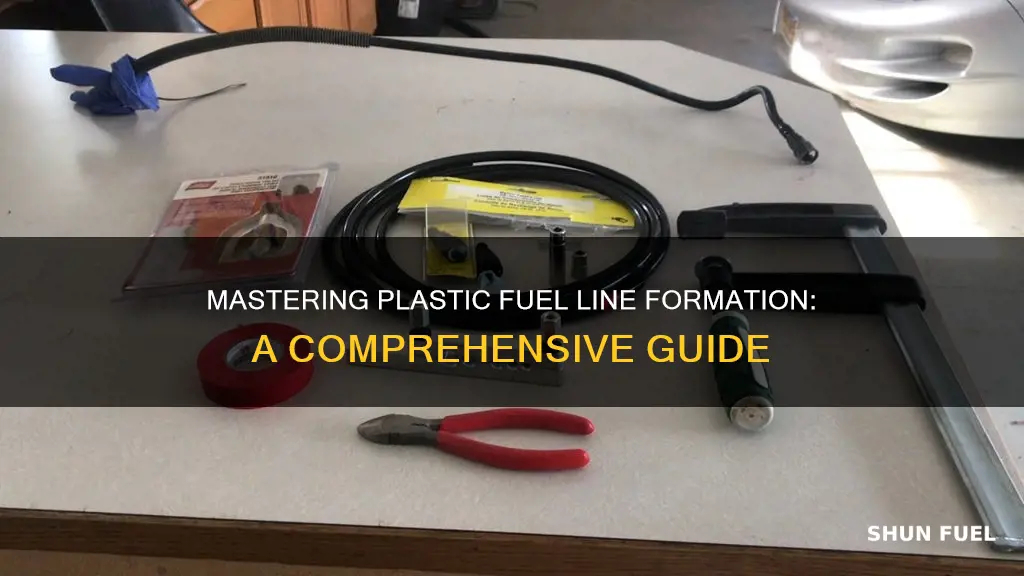
Forming plastic fuel lines is a crucial process in the automotive industry, ensuring the safe and efficient delivery of fuel to engines. This method involves creating custom fuel lines using plastic materials, which offer advantages such as flexibility, durability, and resistance to heat and chemicals. The process typically begins with designing the fuel line layout, considering factors like engine placement and fuel tank location. Engineers then select the appropriate plastic material, such as polyether ether ketone (PEEK) or polypropylene, based on its ability to withstand fuel pressure and temperature variations. The manufacturing process involves molding or extruding the plastic to the desired shape and size, ensuring precise fittings and connections. Proper assembly and sealing techniques are essential to prevent leaks and ensure a reliable fuel supply. This introduction sets the stage for a detailed exploration of the techniques and considerations involved in forming plastic fuel lines.
What You'll Learn
- Material Selection: Choose appropriate plastic materials for fuel lines based on durability and temperature resistance
- Design Considerations: Ensure lines have adequate bend radius and are free of sharp bends to prevent damage
- Fitting Techniques: Employ crimping, swaging, or welding methods for secure connections and leak-free joints
- Routing and Support: Route lines away from heat sources and secure with clips or brackets for stability
- Testing and Inspection: Conduct pressure tests and visual inspections to ensure lines are free of defects and leaks
Material Selection: Choose appropriate plastic materials for fuel lines based on durability and temperature resistance
When it comes to forming plastic fuel lines, material selection is a critical aspect that directly impacts the performance and longevity of the fuel system. The primary goal is to ensure that the chosen plastic materials can withstand the harsh conditions of fuel transport, including varying temperatures and the corrosive nature of gasoline or diesel. Here's a detailed guide on selecting the right plastics for this application:
Polyethylene (PE): This is a popular choice for fuel lines due to its excellent chemical resistance. High-density polyethylene (HDPE) is often preferred for its superior strength and durability. PE is known for its ability to resist fuel degradation and is less susceptible to cracking compared to other plastics. It can handle a wide range of temperatures, making it suitable for both hot and cold climates. However, it's important to note that PE may not be as flexible as some other materials, which could be a consideration for certain vehicle designs.
Polypropylene (PP): PP is another versatile plastic that offers good chemical resistance and temperature stability. It is often used in fuel lines due to its ability to withstand the effects of UV radiation, which is crucial for outdoor applications. PP fuel lines are known for their flexibility and ease of installation. Its low-temperature flexibility ensures that it can accommodate temperature fluctuations without becoming brittle. This material is also lightweight, making it a preferred choice for automotive applications where weight reduction is essential.
Polyvinyl Chloride (PVC): PVC is a robust material that has been traditionally used in fuel lines. It offers excellent chemical resistance and is known for its durability. Rigid PVC is commonly used in high-pressure applications due to its strength. However, it may become brittle at low temperatures, which could be a concern in colder climates. To address this, flexible PVC can be used, providing better temperature resistance and flexibility.
Polyethylene Terephthalate (PET): PET is primarily used for its excellent flexibility and impact resistance. While it may not offer the same level of chemical resistance as HDPE or PP, it is still suitable for fuel lines, especially in applications where flexibility is crucial. PET is often used in fuel lines for its ability to conform to the vehicle's contours, ensuring a secure and vibration-free installation.
Considerations for Selection: When choosing the material, it's essential to consider the specific requirements of your fuel system. Factors such as operating temperature, fuel type, and environmental conditions play a significant role. For high-temperature applications, materials like PP or HDPE are ideal. In colder climates, a combination of materials like PP and flexible PVC can provide the necessary temperature resistance. Additionally, the flexibility and ease of installation of the chosen material should align with the vehicle's design and manufacturing process.
Xterra Fuel Line Fitting Location: A Comprehensive Guide
You may want to see also
Design Considerations: Ensure lines have adequate bend radius and are free of sharp bends to prevent damage
When designing plastic fuel lines, one of the critical aspects to consider is the bend radius. Plastic materials, especially those used for fuel lines, can be susceptible to damage when subjected to sharp bends or tight turns. This is because the material can crack or even break when the bend radius is too small, leading to potential fuel leaks and system failures. Therefore, it is essential to ensure that the fuel lines have an adequate bend radius to prevent such issues.
The bend radius should be determined based on the specific requirements of the application. Factors such as the diameter of the fuel line, the type of plastic used, and the operating conditions need to be considered. As a general rule, the bend radius should be at least 10 times the diameter of the fuel line. For example, if the fuel line has a diameter of 0.5 inches, the minimum bend radius should be 5 inches. This ensures that the material can flex without excessive stress, reducing the risk of damage.
To achieve this, designers can employ various techniques. One approach is to use a gradual bend profile, where the line is bent in a smooth, continuous curve rather than a sharp angle. This can be accomplished by using a mandrel or a custom-made bending tool that guides the material through the desired bend radius. By avoiding sharp bends, the stress on the plastic material is distributed more evenly, minimizing the chances of cracking or breaking.
Additionally, it is crucial to consider the placement of the fuel lines within the vehicle or equipment. The lines should be routed in a way that avoids sharp corners and tight spaces where they might be subjected to excessive force or vibration. Proper routing ensures that the bend radius remains consistent throughout the length of the line, reducing the likelihood of damage during installation and operation.
In summary, when forming plastic fuel lines, designers must prioritize the implementation of adequate bend radii and the avoidance of sharp bends. This attention to detail is vital to ensure the longevity and reliability of the fuel system, preventing potential hazards associated with material damage. By adhering to these design considerations, engineers can create fuel lines that are robust, flexible, and capable of withstanding the demands of their intended applications.
Braided Fuel Line Clamping: A Comprehensive Guide
You may want to see also
Fitting Techniques: Employ crimping, swaging, or welding methods for secure connections and leak-free joints
When it comes to working with plastic fuel lines, ensuring secure connections and leak-free joints is paramount for the safety and efficiency of your vehicle's fuel system. Here, we explore various fitting techniques that can be employed to achieve this:
Crimping: This method involves using a specialized tool to compress the fuel line material around the fitting. It creates a mechanical bond between the line and the fitting, ensuring a tight seal. Crimping is ideal for plastic fuel lines as it provides a reliable connection without the need for adhesives or welding. Start by cleaning the fitting and fuel line to remove any debris. Then, carefully insert the fuel line into the fitting, ensuring proper alignment. Use the crimping tool to apply the necessary force, following the manufacturer's instructions for the specific tool and line material. The crimp should be firm but not overly tight to avoid damaging the line. After crimping, inspect the joint for any signs of leakage and ensure the connection is secure.
Swaging: Swaging is a process that involves forming the fuel line material around a fitting using a swaging tool. It creates a continuous mechanical bond, providing a strong and leak-resistant connection. This technique is particularly useful for larger fuel lines and fittings. Begin by preparing the fitting and fuel line, ensuring they are clean and free of any contaminants. Insert the line into the fitting, allowing for a slight overlap at the connection point. Use the swaging tool to apply pressure and form the line around the fitting, creating a series of folds or swages. The number and depth of swages can vary depending on the specific application and material. After swaging, inspect the joint for any defects and ensure the connection is secure.
Welding: Welding is a more advanced technique suitable for experienced professionals. It involves joining the fuel line and fitting using heat or an adhesive. This method creates a strong, permanent bond, making it ideal for critical applications. When welding, it is crucial to use the right welding material and technique for the specific plastic fuel line type. Start by cleaning the surfaces to be joined and ensuring they are free of any contaminants. Apply the welding material according to the manufacturer's instructions, following the recommended heat or pressure settings. Allow the weld to cool and cure as per the manufacturer's guidelines. After welding, inspect the joint for any defects and ensure it is leak-free.
Each of these fitting techniques offers a reliable way to secure plastic fuel lines, ensuring the integrity of the fuel system. It is essential to choose the appropriate method based on the specific requirements of the application, considering factors such as the type of fuel line material, fitting size, and environmental conditions. Proper preparation, precision, and adherence to manufacturer guidelines are key to achieving secure connections and leak-free joints.
Mastering the Art: Fuel Line Removal Guide for 05 WRX
You may want to see also
Routing and Support: Route lines away from heat sources and secure with clips or brackets for stability
When forming and installing plastic fuel lines, proper routing and support are crucial to ensure the system's reliability and longevity. Here's a detailed guide on how to achieve this:
Routing Away from Heat Sources: One of the primary considerations is to route the fuel lines away from any potential heat sources. Heat can cause plastic to degrade and become brittle, leading to potential leaks or failures. Identify and avoid areas where the engine, exhaust system, or other hot components are located. Route the lines through the engine bay, ensuring they are positioned away from the engine block, headers, and other heat-generating parts. This practice helps maintain the integrity of the fuel lines and prevents premature aging of the plastic material.
Securing with Clips or Brackets: Proper support is essential to prevent excessive movement and potential damage to the fuel lines. Utilize clips or brackets specifically designed for fuel line installation. These clips should be made of materials that are compatible with the fuel lines to avoid any adverse reactions. Secure the lines at regular intervals, typically every 6 to 12 inches, to maintain tension and prevent sagging. Ensure that the clips or brackets are firmly attached to the vehicle's body or frame to provide a stable anchor point. This method of support helps maintain the fuel lines' shape and prevents them from becoming damaged or dislodged during vehicle operation.
Consider using specialized clips or brackets that offer adjustable tension to accommodate different fuel line diameters and angles. This flexibility allows for a more customized and secure installation. Additionally, ensure that the clips or brackets are positioned in a way that does not interfere with the engine's operation or access to other components.
Best Practices: When routing the fuel lines, maintain a neat and organized layout to facilitate future maintenance and inspections. Avoid sharp bends or kinks that could restrict fuel flow or cause damage over time. Use a gentle radius when bending the lines to ensure a smooth transition. Regularly inspect the fuel lines during routine maintenance to identify any signs of wear, cracks, or damage, and replace them if necessary.
By following these guidelines, you can ensure that the plastic fuel lines are properly routed and supported, contributing to a safe and efficient fuel system in your vehicle. Remember, the goal is to protect the fuel lines from potential hazards while maintaining optimal performance.
Best Sources for Rubber Fuel Line: Your Ultimate Guide
You may want to see also
Testing and Inspection: Conduct pressure tests and visual inspections to ensure lines are free of defects and leaks
When forming plastic fuel lines, rigorous testing and inspection are essential to ensure the integrity and safety of the system. One critical aspect of this process is conducting pressure tests to verify the lines' ability to withstand fuel pressure without leaking. This test is crucial as it helps identify any potential weaknesses or defects in the material or manufacturing process. To perform the pressure test, you'll need specialized equipment such as a pressure gauge and a test rig that can simulate the conditions a fuel line would experience in a vehicle. Start by inflating the line with a controlled amount of pressure, gradually increasing it until you reach the expected operating pressure. Monitor the gauge closely for any drops in pressure, which could indicate a leak. It's important to note that the pressure should be held for a sufficient duration to ensure a thorough test.
Visual inspections are another vital part of the testing and inspection process. These inspections should be conducted at various stages of the manufacturing process to catch any issues early on. Begin by examining the raw materials used for the fuel lines. Check for any signs of contamination, such as foreign particles or moisture, as these can affect the line's performance and durability. Next, inspect the formed fuel lines for any visible defects. Look for cracks, bubbles, or any deviations from the desired shape and size. Pay close attention to the connections and fittings, ensuring they are secure and free from damage. Any visible defects should be documented and addressed immediately to prevent further issues during the assembly process.
During the assembly phase, visual inspections should be performed to ensure the lines are correctly installed and connected. Check for proper alignment and secure fastening of the lines to the vehicle's fuel system. Inspect the lines for any signs of stress or strain, especially at points where they are bent or routed around components. Additionally, verify that all connections are tight and free from any leaks. It is also beneficial to simulate real-world conditions during this inspection by applying slight vibrations or temperature changes to the assembled system to identify any potential weaknesses.
After assembly, a comprehensive pressure test should be conducted to validate the system's performance. This test should be performed under controlled conditions, simulating the fuel system's expected operating environment. By applying pressure and monitoring for leaks, you can ensure that the fuel lines meet the required specifications. Any leaks detected during this test should be traced back to their source and rectified before final installation.
In summary, testing and inspection are critical processes in forming plastic fuel lines. Pressure tests and visual inspections at various stages of manufacturing and assembly help identify defects, ensure proper connections, and validate the system's performance. By following these rigorous testing procedures, you can guarantee that the fuel lines are reliable, safe, and ready for use in vehicles.
The Lifespan of Rubber Fuel Lines: What You Need to Know
You may want to see also
Frequently asked questions
Plastic fuel lines are typically made from materials such as polyvinyl chloride (PVC), polypropylene (PP), or high-density polyethylene (HDPE). These materials are chosen for their durability, flexibility, and resistance to fuel degradation.
To achieve a secure fit, it is crucial to use the appropriate size and type of fuel line connectors. Measure the fuel line and connectors carefully to ensure they match. Additionally, apply a thin layer of fuel line adhesive or tape inside the connectors to create a tight seal. This will prevent fuel leaks and ensure a reliable connection.
Yes, plastic fuel lines can be used in certain high-temperature applications. However, it is essential to select the right type of plastic for the specific temperature range. Some plastics, like HDPE, offer better heat resistance compared to others. Always refer to the manufacturer's guidelines and choose a material that can withstand the expected temperature conditions to ensure safety and longevity.