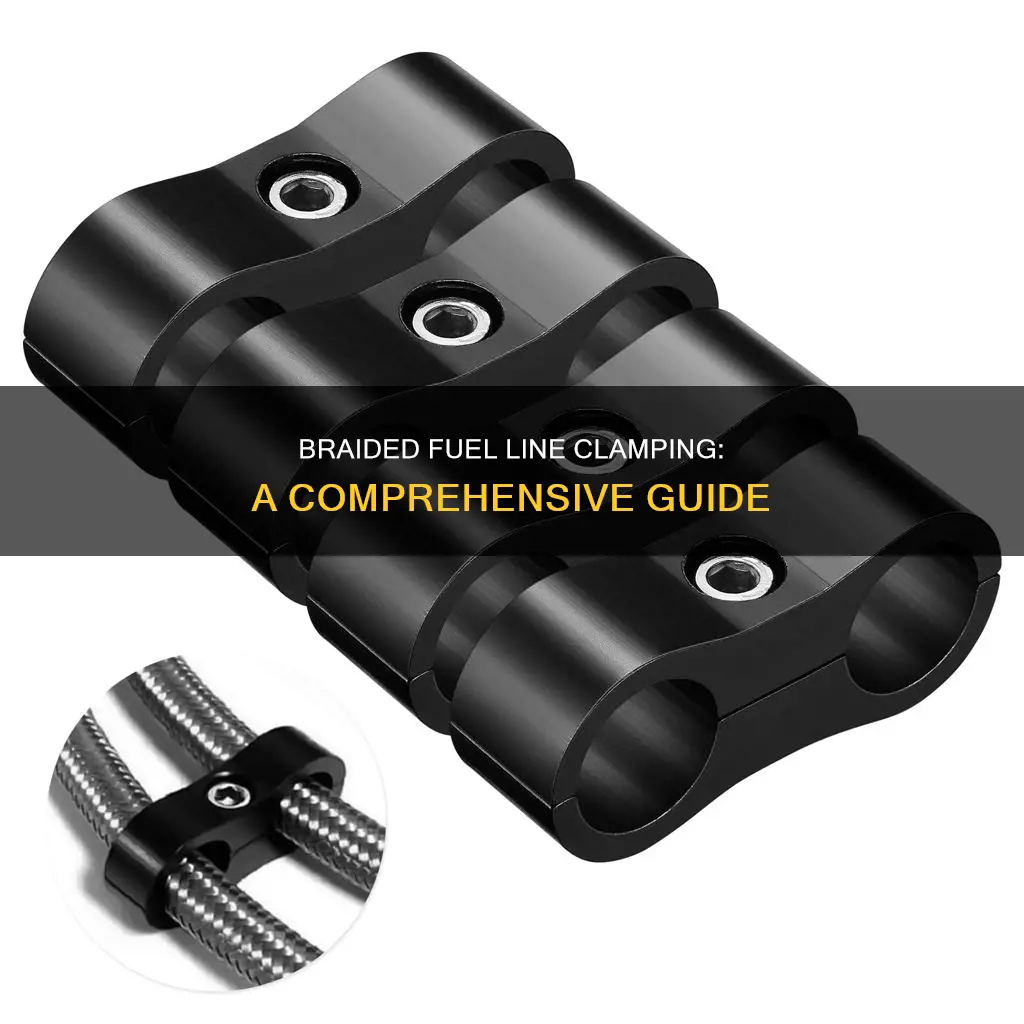
Can you clamp a braided fuel line? This is a common question for those working on fuel systems, especially in high-performance vehicles. Braided fuel lines are a popular choice for their flexibility and durability, but they require careful installation to ensure a secure and leak-free connection. Clamping is a critical step in this process, as it provides the necessary tension and support to keep the line in place. However, the specific clamping technique and tools may vary depending on the fuel line's design and the vehicle's requirements. Understanding the proper clamping methods is essential to ensure the fuel system's reliability and performance.
Characteristics | Values |
---|---|
Clamping braided fuel lines | Yes, it is possible and often recommended for fuel lines with a braided design. Braided fuel lines are flexible and can be clamped using specialized fuel line clamps or hose clamps. |
Clamping method | Use a fuel line clamp or a hose clamp designed for fuel lines. Ensure the clamp is the correct size and securely fits around the braided fuel line without damaging it. |
Considerations | Always refer to the manufacturer's guidelines for your specific fuel line and vehicle. Clamping should be done carefully to avoid restricting fuel flow or causing damage to the fuel line. |
Benefits | Clamping braided fuel lines can provide a secure connection, prevent fuel leaks, and offer a more customized fit compared to using factory-installed clamps. |
Compatibility | Braided fuel lines are commonly used in high-performance vehicles, racing applications, and classic car restoration projects. |
What You'll Learn
- Braided Fuel Line Material: Understand the properties of braided fuel lines and their suitability for clamping
- Clamping Techniques: Explore different methods for clamping braided fuel lines securely
- Fuel Line Diameter: Consider the diameter of the braided fuel line and its impact on clamping
- Clamping Tools: Identify the necessary tools for effective clamping of braided fuel lines
- Fuel Line Routing: Learn about proper routing and positioning for clamping braided fuel lines
Braided Fuel Line Material: Understand the properties of braided fuel lines and their suitability for clamping
Braided fuel lines are an essential component in the fuel delivery system of many vehicles, particularly those with high-performance engines. These lines are designed to withstand the challenges of fuel transport, including high pressure, temperature fluctuations, and mechanical stress. One of the key considerations when working with braided fuel lines is understanding the material properties that make them suitable for clamping.
Braided fuel lines are typically constructed using a combination of materials, with the most common being a synthetic fiber core, often made from materials like polyester or nylon. These fibers are then braided around a metal or synthetic core, creating a strong and flexible structure. The braiding process provides several advantages, including increased flexibility, resistance to kinking, and improved durability. The braided design allows the fuel line to bend and move with the vehicle's components without compromising the integrity of the fuel delivery system.
The material properties of braided fuel lines make them highly suitable for clamping. The synthetic fibers used in the construction are inherently heat-resistant, ensuring that the fuel lines can withstand the high temperatures generated by the engine. Additionally, the braided structure provides excellent resistance to abrasion and mechanical damage, making it ideal for clamping in areas with potential hazards, such as under the hood or near engine components. The flexibility of the braided design also allows for easy installation and adjustment, ensuring a secure and reliable clamp.
When clamping braided fuel lines, it is crucial to use the appropriate tools and techniques to ensure a proper seal and prevent damage to the fuel line. Clamps should be made of a compatible material, such as stainless steel or aluminum, to avoid corrosion and ensure longevity. The clamp should be applied firmly but carefully to avoid excessive force, which could lead to fuel line damage. Proper alignment of the clamp is essential to ensure an even distribution of pressure, preventing any potential leaks or fuel contamination.
In summary, braided fuel lines are an excellent choice for fuel delivery systems due to their flexibility, durability, and resistance to extreme conditions. The material properties, including heat resistance and abrasion, make them well-suited for clamping. When working with these fuel lines, it is important to use the right tools and techniques to ensure a secure and reliable clamp, ultimately contributing to the overall performance and longevity of the vehicle's fuel system. Understanding the characteristics of braided fuel lines is key to successful installation and maintenance.
Dual Fuel Lines: Unraveling the Mystery Behind the Extra Line
You may want to see also
Clamping Techniques: Explore different methods for clamping braided fuel lines securely
When working with braided fuel lines, it's crucial to employ the right clamping techniques to ensure a secure and reliable connection. Braided fuel lines are known for their flexibility and durability, making them ideal for fuel delivery systems in vehicles. However, their unique construction requires specific clamping methods to prevent leaks and ensure optimal performance. Here, we delve into various clamping techniques to achieve a tight and secure seal.
One popular approach is the use of specialized fuel line clamps, often made from durable materials like stainless steel or aluminum. These clamps are designed to accommodate the braided structure of the fuel line. The clamping process involves positioning the clamp around the fuel line, ensuring it covers the entire length of the line where it needs to be secured. It's essential to apply the right amount of pressure to create a snug fit without causing damage to the line. A common mistake is to overtighten the clamp, which can lead to crimping the braided fuel line and potentially causing fuel leaks.
Another technique is the use of compression fittings, which provide a reliable sealing mechanism. This method involves inserting the fuel line into a compression fitting and tightening it with a spanner or wrench. The compression fitting compresses the fuel line, creating a tight seal. It's crucial to follow the manufacturer's guidelines for the correct torque specifications to avoid over-tightening, which can damage the line. This technique is particularly useful for high-pressure fuel systems, as it ensures a secure and leak-free connection.
For a more permanent solution, some enthusiasts opt for welding the fuel line to the fitting. This method requires skill and precision to ensure a clean and secure joint. The process involves cleaning the fuel line and fitting, applying a suitable flux, and then welding the two together. While this method provides an extremely strong bond, it is more complex and time-consuming. It is recommended for experienced professionals or those with access to specialized equipment.
Additionally, using a combination of different clamping methods can be beneficial. For instance, you might use a compression fitting at one end and a specialized clamp at the other to provide a secure and versatile connection. This approach allows for flexibility in design and can accommodate various fuel line configurations. It's essential to consider the specific requirements of your fuel system and choose the clamping techniques accordingly.
Brake Fluid's Impact on Fuel Lines: A Comprehensive Guide
You may want to see also
Fuel Line Diameter: Consider the diameter of the braided fuel line and its impact on clamping
When it comes to clamping a braided fuel line, the diameter of the line is a critical factor to consider. The diameter directly influences the clamping process and the overall performance of the fuel line. Here's a detailed breakdown of why it matters:
Braided fuel lines are known for their flexibility and strength, which are achieved through the intricate weaving of multiple strands of material. The diameter of these strands determines the overall thickness and rigidity of the fuel line. Thicker braided fuel lines with larger diameters offer increased resistance to pressure and are less prone to kinking or bending under stress. This is particularly important in high-performance applications where fuel pressure can vary significantly.
During the clamping process, the goal is to secure the fuel line in place without causing damage or restricting fuel flow. The diameter of the fuel line plays a crucial role in determining the appropriate clamping force and the type of clamp required. For smaller diameter braided fuel lines, a gentle and precise clamping technique is necessary to avoid crushing the line. On the other hand, larger diameter fuel lines may require more robust clamps to ensure a secure and reliable connection.
It's essential to strike a balance when clamping braided fuel lines. If the clamp is too tight, it can restrict fuel flow, leading to potential performance issues or even engine damage. Conversely, if the clamp is too loose, the fuel line may become dislodged or vibrate excessively, causing potential leaks or damage over time. Therefore, understanding the specific requirements of your fuel line's diameter is vital to ensure a proper and secure clamp.
In summary, when dealing with braided fuel lines, the diameter is a key consideration for clamping. It influences the choice of clamp, the clamping force, and the overall reliability of the fuel line installation. Properly addressing the diameter ensures a secure connection without compromising the performance and longevity of the fuel system. Always refer to the manufacturer's guidelines and recommendations for the specific braided fuel line you are working with.
Leaky Fuel Line: Signs, Causes, and Repairs
You may want to see also
Clamping Tools: Identify the necessary tools for effective clamping of braided fuel lines
When it comes to clamping braided fuel lines, having the right tools is essential to ensure a secure and reliable connection. Braided fuel lines are commonly used in automotive applications due to their flexibility and resistance to fuel contamination. However, clamping these lines requires a specific set of tools to achieve a proper seal and prevent leaks. Here's an overview of the necessary tools for effective clamping:
Braided Fuel Line Clamps: The primary tool for clamping braided fuel lines is a specialized clamp designed for this purpose. These clamps are typically made of durable materials such as stainless steel or aluminum to withstand the harsh conditions of fuel systems. Look for clamps with a smooth, rounded inner surface to avoid damaging the fuel line. The clamp should have a secure locking mechanism to ensure it stays in place once tightened. Common types include quick-release clamps, which offer ease of installation and removal, and adjustable clamps for customized fitting.
Pliers or Wrenches: To tighten the clamp effectively, you'll need a set of pliers or a wrench. Pliers provide better grip and control, especially for smaller or more delicate clamps. Opt for adjustable pliers to accommodate various clamp sizes. Wrenches can be useful for larger clamps or when a more substantial force is required. Ensure you have a range of sizes to fit different clamp types and fuel line diameters.
Fuel Line Cutter: Before clamping, you'll need to cut the braided fuel line to the desired length. A fuel line cutter is specifically designed for this task and ensures a clean, precise cut. Look for cutters with adjustable settings to accommodate different fuel line thicknesses. This tool will help you achieve a professional finish and ensure a secure connection.
Measuring Tape or Caliper: Accurate measurement is crucial when working with fuel lines. A measuring tape or caliper will help you determine the correct length of the fuel line and ensure the clamp is applied at the right position. This step is essential to avoid clamping the fuel line in the wrong place, which could lead to fuel leaks or damage.
Safety Gear: When working with fuel lines, safety should always be a priority. Consider wearing safety goggles to protect your eyes from any potential fuel splashes. Gloves can also provide a better grip and protect your hands during the clamping process. Additionally, ensure you are working in a well-ventilated area and follow proper fuel handling procedures.
Having these tools readily available will enable you to clamp braided fuel lines effectively and safely. Remember, proper clamping is critical to maintaining the integrity of your fuel system and preventing costly repairs. Always refer to the manufacturer's guidelines for specific clamping requirements and best practices.
Condensation's Impact: Can Fuel Line Moisture Cause Car Sputters?
You may want to see also
Fuel Line Routing: Learn about proper routing and positioning for clamping braided fuel lines
Braided fuel lines are a popular choice for fuel delivery systems due to their flexibility, durability, and resistance to fuel-related degradation. When working with these lines, proper routing and clamping techniques are essential to ensure optimal performance and longevity. Here's a guide to help you understand the correct approach to routing and clamping braided fuel lines:
Routing Considerations:
- Start by referring to the vehicle's manual or manufacturer's guidelines for specific instructions tailored to your make and model. Different vehicles may have unique requirements due to their design and layout.
- Identify the path that the fuel line needs to take from the fuel tank to the engine. This path should be as direct as possible to minimize the length of the line, reducing potential flexing and stress.
- Consider the location of the fuel pump, as it is a critical component that requires a steady fuel supply. Ensure the fuel line is routed close to the pump to maintain a consistent pressure.
- Avoid routing the fuel line near heat sources, such as exhaust manifolds or under the hood, as high temperatures can accelerate the degradation of the line.
- Keep the fuel line away from sharp bends or kinks, as these can restrict flow and cause long-term damage.
Clamping Techniques:
- Clamps should be used to secure the braided fuel line at regular intervals, typically every 6 to 12 inches. This spacing helps distribute the line's weight and prevents excessive bending at any single point.
- When clamping, ensure the clamp is the correct size for the fuel line diameter. A proper fit is crucial to avoid leakage and potential fuel spillage.
- Avoid tight clamping as it can restrict flow and cause pressure buildup. Instead, use a gentle, firm grip to secure the line.
- For sharp bends or changes in direction, consider using a flexible clamp or a bend radius protector to minimize stress on the line.
- Always check for any signs of damage or wear on the fuel line and replace it if necessary before clamping.
Proper routing and clamping of braided fuel lines are critical to maintaining a reliable fuel supply to your engine. By following these guidelines, you can ensure that the fuel lines are positioned correctly, clamped securely, and protected from potential hazards, ultimately contributing to the overall performance and longevity of your vehicle's fuel system. Remember, each vehicle may have unique requirements, so always refer to the manufacturer's instructions for the best results.
Optimizing Performance: Choosing the Right Fuel Lines for Your Yamaha Waverunner 700
You may want to see also
Frequently asked questions
Compatibility depends on the specific make and model of your vehicle, as well as the year. It's crucial to consult your vehicle's manual or seek advice from a professional to ensure the correct size and type of braided fuel line is used.
Braided fuel lines offer several advantages, including increased flexibility, resistance to extreme temperatures, and reduced risk of fuel leaks due to their durable construction. They are an excellent choice for high-performance vehicles or those operating in harsh environments.
While some DIY enthusiasts may attempt to install braided fuel lines, it is generally recommended to have a professional mechanic handle the job. Proper installation requires specific tools and knowledge to ensure a secure and leak-free connection.
The lifespan of a braided fuel line can vary depending on usage, environmental factors, and maintenance. As a general guideline, it is advised to inspect and replace the fuel lines every 50,000 to 100,000 miles or as per the manufacturer's recommendations.
Yes, proper care is essential to ensure the longevity of braided fuel lines. Avoid using sharp objects that could damage the lines, and refrain from modifying or altering the fuel system. Regularly check for any signs of wear or damage and address issues promptly to prevent potential fuel leaks.