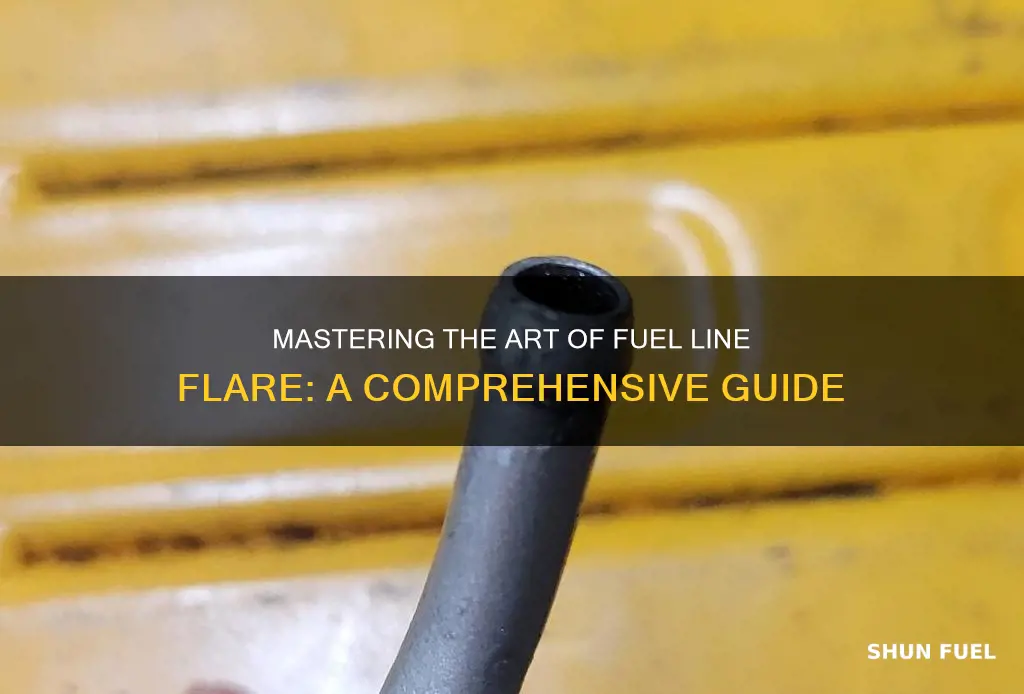
Flaring a fuel line is a crucial process in the maintenance and repair of fuel systems, ensuring optimal performance and safety. This technique involves the precise bending and shaping of fuel lines to direct fuel flow efficiently while maintaining structural integrity. It requires careful consideration of the fuel line's material, diameter, and the specific requirements of the vehicle's fuel system. By understanding the principles of flaring, technicians can ensure a secure and effective connection, preventing fuel leaks and enhancing overall engine performance. This guide will provide a step-by-step approach to mastering the art of flaring fuel lines.
What You'll Learn
- Identify the Fuel Line: Locate the fuel line, often a flexible tube, running from the fuel tank to the engine
- Prepare the Tools: Gather tools like a fuel line flare kit, wrenches, and a fuel line cleaner
- Clean the Connections: Ensure all connections are clean and free of debris for a secure flare
- Align the Flare Ports: Carefully align the flare ports on the fuel line and the fitting
- Apply Heat and Force: Use a heat source and apply force to create a tight, leak-free seal
Identify the Fuel Line: Locate the fuel line, often a flexible tube, running from the fuel tank to the engine
To begin the process of flaring a fuel line, it's essential to first identify the fuel line itself. This component is a crucial part of your vehicle's fuel system, responsible for transporting fuel from the tank to the engine. The fuel line is typically a flexible tube made of rubber or a similar material, designed to withstand the pressure and temperature changes that occur during engine operation.
Locate the fuel tank, which is usually found in the vehicle's rear or beneath the floor. From there, trace the path of the fuel line, which will run towards the engine compartment. The line may be hidden behind various components, such as the exhaust system or under the dashboard, so careful inspection is required. Look for any signs of damage, such as cracks, leaks, or kinks, as these could indicate a problem that needs addressing.
In some vehicles, the fuel line may be protected by a metal or plastic shield to safeguard it from potential impacts or damage. This shield can often be found running parallel to the fuel line, providing an additional layer of protection. Identifying this shield can help you understand the path of the fuel line more clearly.
Once you've located the fuel line, it's important to understand its various components. The line itself is connected to the fuel tank via a fitting, and it then continues towards the engine, where it connects to the fuel rail or the individual fuel injectors. Each connection point is critical and should be checked for tightness and any signs of corrosion or damage.
Identifying the fuel line is a crucial step in the flaring process, as it ensures that you are working on the correct component and allows you to assess the condition of the line before proceeding with any modifications or repairs. This initial inspection is a vital safety measure to ensure the integrity of your vehicle's fuel system.
Mastering the Art of Fuel Line Removal: A Step-by-Step Guide for Your 2006 Nissan Altima
You may want to see also
Prepare the Tools: Gather tools like a fuel line flare kit, wrenches, and a fuel line cleaner
Before you begin the process of flaring a fuel line, it's crucial to ensure you have the right tools and materials ready. This preparation will make the task more efficient and less prone to errors. Here's a step-by-step guide on what you need to gather:
Fuel Line Flare Kit: This is the primary tool you'll need for the job. A fuel line flare kit typically includes the flare tool itself, which is designed to create a flare connection on the fuel line. The kit usually comes with various sizes of flare nuts and sleeves to accommodate different fuel line diameters. Make sure to choose a kit that is compatible with the fuel line you are working on.
Wrenches: You will require a set of wrenches to tighten the flare nuts securely. Get a combination of different sizes, especially those that fit the threads of the flare nuts in your kit. Having a variety of wrenches will ensure you can apply the necessary force to create a tight seal.
Fuel Line Cleaner: Cleaning the fuel line is an essential step often overlooked. Before flaring, it's important to remove any dirt, debris, or old fuel residue from the line. Gather a fuel line cleaner, which is typically a solvent-based product designed to dissolve and remove contaminants. This step ensures a clean and smooth surface for the flare connection.
Additionally, consider having some rags or paper towels on hand to wipe away any spills or excess cleaner. It's also a good idea to wear protective gloves to avoid skin contact with the cleaner, especially if it's a strong solvent. With these tools and preparations, you'll be well-equipped to start the fuel line flaring process, ensuring a secure and reliable connection.
Oetiker Clamp Sizing Guide: Perfect Fit for 3/8" Fuel Lines
You may want to see also
Clean the Connections: Ensure all connections are clean and free of debris for a secure flare
When it comes to flaring a fuel line, ensuring that all connections are clean and free of debris is crucial for a secure and successful process. This step is often overlooked but can significantly impact the overall outcome. Here's a detailed guide on how to achieve this:
Start by identifying all the connections along the fuel line that you intend to flare. These connections typically include the fuel tank, fuel pump, and any intermediate lines or fittings. Carefully inspect each connection point for any signs of dirt, corrosion, or debris accumulation. Over time, fuel lines can accumulate contaminants from the fuel itself or environmental factors, leading to reduced performance and potential safety hazards.
The cleaning process should begin with a thorough inspection. Use a bright flashlight to examine the connections and look for any visible contaminants. Pay attention to small crevices and openings where debris might have accumulated. Once you've identified the problem areas, it's time to clean them. Start by removing any loose debris manually with a small brush or a compressed air gun. Ensure you don't apply excessive force to avoid damaging the connections.
For more stubborn deposits or corrosion, you might need to use a suitable cleaning agent. Choose a fuel line cleaner that is compatible with your fuel system materials. Apply the cleaner to the connections and let it sit for a recommended duration, which is usually specified by the manufacturer. After the specified time, use a clean cloth or a soft-bristled brush to wipe away the contaminants. Rinse the area thoroughly with clean fuel or a suitable solvent to remove any remaining cleaner.
After cleaning, it's essential to verify the effectiveness of your efforts. Re-inspect the connections to ensure they are now free of debris and corrosion. Check for any signs of damage or wear that might have occurred during the cleaning process. If everything looks good, proceed with the flaring process, ensuring that the connections are now ready for a secure flare. Remember, taking the time to clean the connections properly will contribute to a safer and more efficient fuel line flare operation.
Mastering Plastic Fuel Line Connections: A Step-by-Step Guide
You may want to see also
Align the Flare Ports: Carefully align the flare ports on the fuel line and the fitting
When working on flaring a fuel line, proper alignment of the flare ports is crucial to ensure a secure and leak-free connection. This process involves carefully positioning the ports to create a precise fit between the fuel line and the fitting. Here's a step-by-step guide to achieving this:
Start by ensuring you have the correct tools for the job, including a flare tool, which is specifically designed to create flares. Inspect the fuel line and the fitting you intend to connect. Look for any existing damage or defects that might affect the alignment process. Clean the flare ports on both the fuel line and the fitting to remove any debris or contaminants. This step is essential to ensure a clean and reliable connection.
Now, carefully align the flare ports. The ports should be positioned in a way that allows the flare tool to create a uniform and symmetrical flare. Take your time with this step, as precision is key. You can use a straight edge or a ruler to ensure the ports are aligned straight and true. The goal is to create a consistent and even surface for the flare to form.
Apply the flare tool to the aligned ports, following the manufacturer's instructions. Generate pressure and torque the tool in a controlled manner to create the flare. Ensure that the flare is formed evenly and without any uneven pressure points. Check the flare's integrity by examining it for any cracks or imperfections. A well-formed flare should be smooth and free of any visible defects.
Once the flare is complete, inspect the connection for any leaks. Use a soapy water solution or a specialized leak detection spray to identify any potential issues. If no leaks are found, your fuel line is now properly flared and ready for use. Remember, proper alignment of the flare ports is critical to the success of the flaring process and the overall reliability of the fuel line connection.
Arctic Cat 454 Fuel Line: The Ultimate Guide to Sizing
You may want to see also
Apply Heat and Force: Use a heat source and apply force to create a tight, leak-free seal
When working with fuel lines, creating a secure and leak-free connection is crucial to ensure the safety and efficiency of your vehicle's fuel system. One effective method to achieve this is by applying heat and force to the flare connection. This technique involves using a heat source and applying pressure to create a tight seal, which can be particularly useful when dealing with fuel lines that require a robust and reliable connection.
The process begins with preparing the fuel line and flare fitting. Start by cleaning the flare fitting and the end of the fuel line to remove any dirt, debris, or contaminants. Ensure that the surface is smooth and free from any obstructions. Then, apply a thin layer of thread seal tape or pipe compound to the male end of the flare fitting. This step provides a protective barrier and ensures a better grip when applying force.
Next, take a heat source, such as a heat gun or a torch, and apply it to the flare fitting. Heat the fitting until it becomes soft and pliable. The heat softens the material, allowing it to conform to the shape of the fuel line. Be cautious not to overheat the fitting, as it can damage the material. Maintain a steady heat application for a few seconds, ensuring that the entire surface is heated evenly.
While the flare fitting is still warm, quickly but firmly insert the fuel line into the fitting. Apply force in a downward motion, pushing the fuel line into the fitting until it is fully seated. The heat and pressure will cause the flare to expand and create a tight seal against the fuel line. Hold the connection in place for a few moments to ensure the seal is secure.
After the connection has cooled slightly, test it for leaks. If no leaks are detected, you have successfully created a leak-free flare connection. This method is a practical and reliable way to ensure a strong bond between fuel lines and flare fittings, providing peace of mind regarding the integrity of your vehicle's fuel system. Remember to always exercise caution when working with heat sources and tools to avoid any accidents or damage.
Optimal Diameter for Steel Fuel Lines: A Comprehensive Guide
You may want to see also
Frequently asked questions
Flaring a fuel line is a process used to repair or modify the fuel system in an engine. It involves creating a small, controlled flame at the end of the fuel line to melt and seal the fuel-carrying material, ensuring a tight and leak-free connection.
Before flaring, ensure you have the necessary tools and materials, including a flare tool, fuel line of the correct size, and a heat source. It's crucial to disconnect the fuel line from the fuel source and engine to prevent any accidents. Always wear protective gear, such as heat-resistant gloves and safety goggles, to safeguard yourself during the process.
Fuel lines can be damaged due to various reasons, such as age, corrosion, impact damage, or improper installation. Over time, fuel lines may develop cracks or leaks, leading to fuel leaks, engine misfires, or reduced performance. Additionally, physical damage from accidents or debris can also result in fuel line damage.
Absolutely! Safety is paramount when flaring a fuel line. Ensure you work in a well-ventilated area to avoid inhaling harmful fumes. Keep a fire extinguisher nearby in case of emergencies. Be cautious of hot surfaces and always allow the flared section to cool down before handling it. It's also essential to follow manufacturer guidelines and seek professional advice if you're unsure about any step.