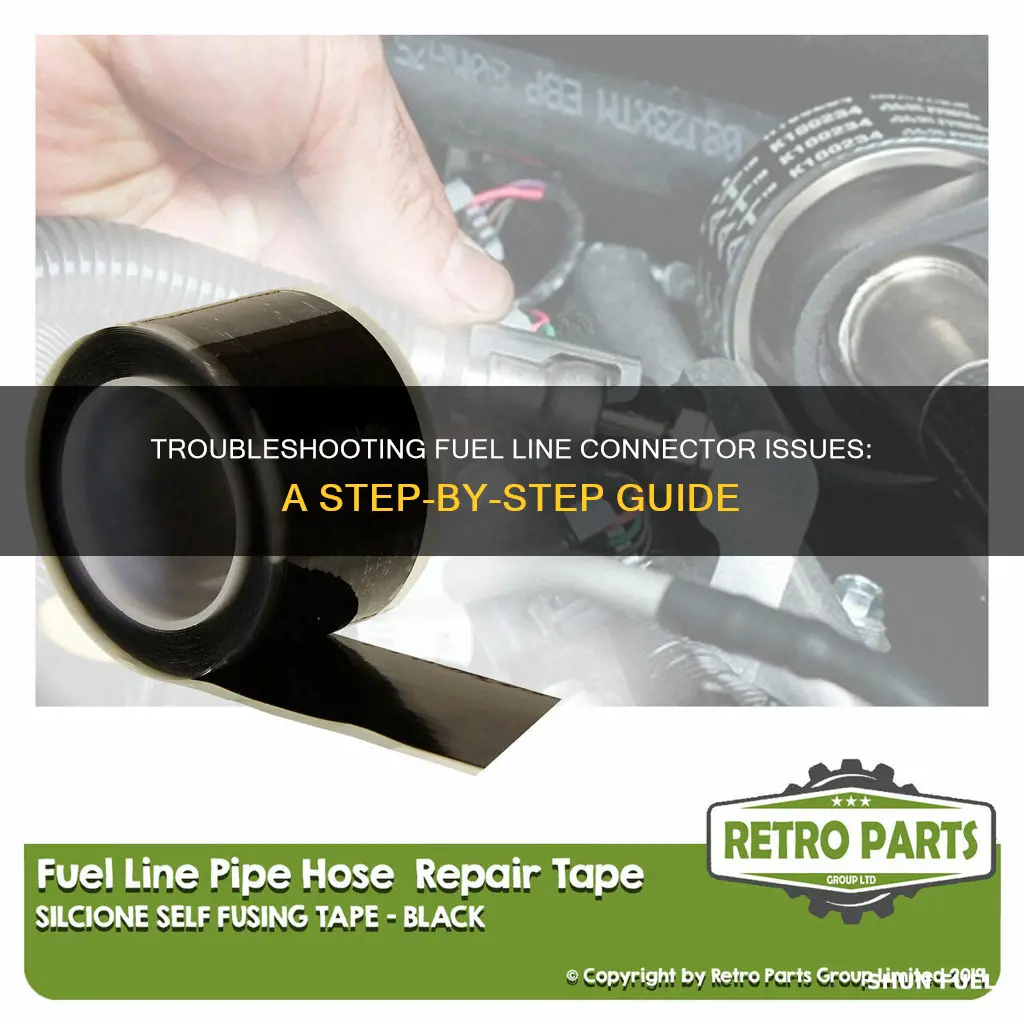
Fixing a fuel line connector can be a straightforward process if you follow the right steps. Start by ensuring you have the necessary tools, such as a fuel line repair kit, a wrench, and a new fuel line connector. Locate the damaged or disconnected fuel line connector, which is typically found under the hood or near the fuel tank. Carefully remove any debris or old connector material. Then, insert the new connector, ensuring it is aligned properly and securely tightened. Finally, test the system by starting the engine and checking for any leaks. This guide will provide a clear and concise approach to resolving fuel line connector issues.
What You'll Learn
- Locate the Fuel Line Connector: Identify the connector's location under the hood
- Inspect for Damage: Check for cracks, corrosion, or signs of damage
- Clean and Debris: Remove any dirt, rust, or debris using a brush
- Tighten Connections: Ensure all connections are secure and tightened properly
- Test Fuel Flow: Verify fuel flow by starting the engine and checking for leaks
Locate the Fuel Line Connector: Identify the connector's location under the hood
Locate the fuel line connector under the hood of your vehicle. This connector is typically a small, cylindrical component that connects the fuel pump to the engine. It is usually located near the front of the engine bay, often close to the firewall. The exact position can vary depending on the make and model of your car, but it is generally easy to spot once you know what to look for.
When you open the hood, take a moment to familiarize yourself with the various components. The fuel line connector is often surrounded by other engine parts, such as hoses, wires, and brackets. It might be secured in place with a small clip or bolt, so you may need to carefully remove any adjacent components to access it. Look for any signs of damage or corrosion around the connector, as these issues can often lead to fuel system problems.
The fuel line connector is designed to be easily accessible for maintenance and repairs. It is usually a simple task to locate and inspect it. If you have any doubts about its position, consult your vehicle's service manual, which will provide detailed diagrams and instructions specific to your car.
Once you've identified the connector, ensure you understand its function. The fuel line connector is responsible for directing the fuel from the fuel pump to the engine's fuel injectors or carburetor. It plays a crucial role in the proper functioning of your vehicle's fuel system. If the connector is damaged or disconnected, it can result in poor engine performance, reduced power, or even engine failure.
Remember, when working on any vehicle component, it's essential to exercise caution and follow proper safety procedures. If you're unsure about any step or encounter any difficulties, it's best to consult a professional mechanic to ensure the job is done correctly and safely.
Exploring the Feasibility of Rubber Fuel Lines: A Comprehensive Guide
You may want to see also
Inspect for Damage: Check for cracks, corrosion, or signs of damage
When inspecting a fuel line connector for damage, it's crucial to be thorough and methodical. Start by visually examining the connector and the surrounding area. Look for any visible cracks, chips, or fractures in the connector's housing. These defects can compromise the integrity of the connector and lead to fuel leaks or other issues. Inspect the threads and fittings for any signs of damage or wear. Corrosion is a common issue, especially in areas with high humidity or salt exposure. Check for white or green deposits around the connector, as these indicate the presence of corrosion. If corrosion is found, it's essential to clean and treat the affected areas to prevent further damage.
Pay close attention to the fuel line itself, as damage to the line can also affect the connector. Look for any kinks, bends, or cuts in the fuel line. These issues can cause restrictions in fuel flow and may lead to engine performance problems. Inspect the fuel line for any signs of deterioration, such as softening or brittleness, especially if the line is older or has been exposed to harsh conditions.
Additionally, check for any signs of impact damage or discolouration. If the connector has been subjected to physical stress or collision, it may show visible signs of damage. Inspect the connector's mounting points and brackets for any cracks or signs of loosening. Ensure that all fasteners are tight and secure to maintain the connector's stability.
If you notice any damage, it's essential to address it promptly. Clean and repair any corrosion, replace damaged fuel lines, and tighten or replace faulty connectors. Properly securing the connector and fuel line is vital to prevent further issues and ensure optimal engine performance. Remember, regular inspection and maintenance can help identify and rectify potential problems before they escalate.
Bleed Air from Outboard Fuel Line: A Step-by-Step Guide
You may want to see also
Clean and Debris: Remove any dirt, rust, or debris using a brush
When dealing with a fuel line connector, ensuring it is clean and free of debris is crucial for optimal performance and safety. Start by inspecting the connector and its surrounding areas for any visible dirt, rust, or debris. This might include dirt accumulation, corrosion, or even small pieces of debris that could interfere with the fuel flow.
Use a soft-bristled brush to gently clean the connector and its immediate vicinity. Soft bristles are essential to avoid scratching or damaging the connector's components. Focus on the threads, fittings, and any other intricate parts that might trap dirt or rust. Work carefully, ensuring you don't apply excessive force that could strip threads or damage the connector.
For stubborn dirt or rust, you might need to apply a small amount of fuel line cleaner or a mild detergent. These products can help dissolve and remove tough deposits. However, always follow the manufacturer's instructions to avoid any potential issues. After cleaning, rinse the area with clean water to ensure no residue remains.
Once you've removed the visible dirt and rust, it's important to inspect the connector further. Look for any signs of damage, such as cracks, bends, or corrosion that might have occurred despite your cleaning efforts. If you notice any significant issues, further investigation or professional assistance may be required.
Remember, proper maintenance and cleaning of the fuel line connector can prevent potential fuel system issues and ensure your vehicle's engine runs efficiently and safely. Regularly checking and cleaning the connector can save you from more complex and costly repairs in the future.
Fixing Fuel Lines: A Step-by-Step Guide for 93 Grand Marquis Owners
You may want to see also
Tighten Connections: Ensure all connections are secure and tightened properly
When dealing with fuel line connectors, ensuring that all connections are secure and tightened properly is crucial to maintaining a safe and efficient fuel system. This process involves a few key steps to guarantee a reliable fix. Firstly, locate the fuel line connector, which is typically found where the fuel line connects to the engine or fuel tank. It is important to inspect the connector for any signs of damage, corrosion, or wear. If you notice any issues, such as cracks or leaks, it is best to replace the connector rather than attempting to tighten it further.
Once you have identified the connector, you'll need to disconnect the fuel line. This may require removing a few screws or clips to access the connection. Carefully detach the fuel line from the connector, ensuring you have a clear view of the threads and fittings. Now, it's time to tighten the connections. Use a wrench or a specialized fuel line tool to apply firm pressure and tighten the fittings securely. The goal is to achieve a tight seal without overtightening, as this can cause damage to the fuel line or connector.
Pay close attention to the torque specifications for the particular connector you are working with. Over-tightening can lead to stripped threads or damaged components, so use the appropriate tool to measure and apply the correct amount of force. After tightening, ensure that all connections are snug and secure. Check for any leaks by gently pressing around the fittings and observing for any signs of fuel escaping. If you notice any leaks, you may need to re-tighten the connections or inspect the fuel line for further issues.
Additionally, consider using thread seal tape or pipe compound on the threads to provide an extra layer of protection against leaks. This is especially important if the connector has been previously tightened and loosened multiple times, as repeated use can wear down the threads. By taking the time to tighten connections properly, you can ensure that the fuel line connector functions optimally, preventing potential fuel leaks and engine performance issues.
Remember, when working with fuel systems, safety should always be a priority. If you are unsure about any step or encounter difficulties, it is recommended to consult a professional mechanic who can provide guidance and ensure the job is done correctly. Properly tightened connections will contribute to a reliable fuel system and help prevent potential hazards associated with fuel line failures.
Homelite Vac Attack 2: Running Fuel Lines - Expert Guide
You may want to see also
Test Fuel Flow: Verify fuel flow by starting the engine and checking for leaks
When troubleshooting a fuel line connector issue, it's crucial to test the fuel flow to ensure the system is functioning correctly. This process involves a systematic approach to identify and resolve any potential problems. Here's a step-by-step guide on how to verify fuel flow by starting the engine and checking for leaks:
Step 1: Engine Preparation
Before beginning the test, ensure the engine is in a safe and controlled environment. Park the vehicle on a level surface and engage the parking brake. Allow the engine to cool down if it has been recently used to prevent any potential hazards. Locate the fuel line connector, which is typically found near the engine's fuel pump or injection system. This connector is responsible for attaching the fuel pump to the engine and supplying fuel to the engine's combustion chambers.
Step 2: Fuel Flow Verification
Start the engine and allow it to idle for a few minutes. This initial running will help stabilize the fuel system and ensure proper pressure. Pay close attention to the engine's behavior and listen for any unusual noises. A well-functioning fuel system should provide a smooth and quiet operation. Next, check for any visible fuel leaks around the fuel line connector. Inspect the area for any signs of fuel seepage or dripping. Leaks can occur due to damaged seals, loose connections, or worn-out components. If you notice any leaks, it indicates a potential issue with the fuel line connector or its associated parts.
Step 3: Pressure Testing (Optional)
For a more comprehensive test, you can use a fuel pressure gauge to measure the engine's fuel pressure. This step is especially useful if you suspect a problem with the fuel pump or the fuel pressure regulator. Connect the gauge to the fuel line, ensuring a secure and tight connection. Start the engine and monitor the fuel pressure reading. A healthy fuel system should maintain a steady pressure within the specified range for your vehicle's engine. If the pressure is significantly lower or higher than the expected value, it may indicate a problem with the fuel line connector or the fuel pump.
Step 4: Visual Inspection
While the engine is running, visually inspect the fuel line connector for any signs of damage or wear. Look for cracks, corrosion, or any visible deterioration on the connector and its surrounding components. Also, check for any loose connections and ensure all bolts and fasteners are tightened to the manufacturer's specifications. A thorough visual inspection can help identify potential issues that might cause fuel leaks or reduced flow.
Step 5: Document and Troubleshoot
After completing the test, document any observations, including the presence of leaks, pressure readings, and visual defects. If you identified any issues, further troubleshooting may be required. This could involve checking the fuel pump's operation, inspecting the fuel filter, or examining the fuel injectors. Remember, each vehicle model may have specific requirements and procedures, so consulting the vehicle's manual or seeking professional advice is recommended for accurate diagnosis and repair.
W124 400E Fuel Line: An6 or Not? Unraveling the Mystery
You may want to see also
Frequently asked questions
A damaged or faulty fuel line connector can lead to various issues. Common signs include fuel leaks, engine misfires, reduced power, or a check engine light illumination. If you notice any of these symptoms, it's best to inspect the connector and consider seeking professional help if needed.
Yes, you can attempt to fix a loose connector yourself. Start by ensuring the engine is cool to avoid any burns. Locate the fuel line connector, which is typically a rubber or plastic fitting attached to the fuel rail or injectors. Use a fuel line connector kit, which includes a new o-ring or gasket, to secure the connector tightly. Make sure it is properly aligned and tightened to the recommended specifications.
You will likely need a few basic tools to fix the connector. These may include a socket or wrench set, a fuel line connector kit (if needed), a new o-ring or gasket, and possibly a fuel line cleaner or lubricant. It's always a good idea to have a service manual or repair guide specific to your vehicle for detailed instructions.
Yes, a few mistakes can make the issue worse. Avoid overtightening the connector, as this can damage the fuel line or cause internal engine damage. Ensure you have the correct tools and specifications for your vehicle to prevent errors. Also, be cautious when working with fuel to avoid spills and always follow safety guidelines.
Regular maintenance and inspections can help prevent future problems. Check the fuel lines and connectors for any signs of damage, cracks, or leaks during routine engine maintenance. Keep the fuel system clean and free of debris, and ensure all connections are tight and secure. Following the manufacturer's recommended service intervals can also help identify and address potential issues early on.