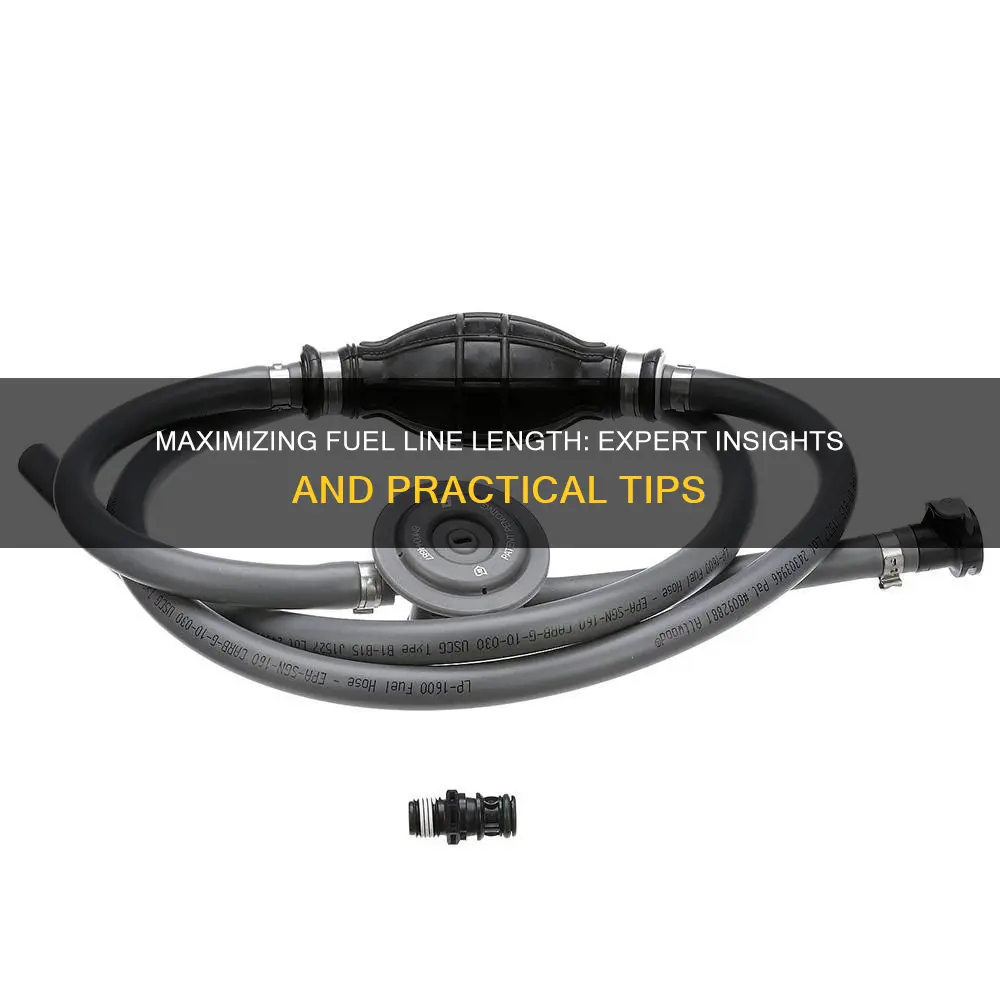
Fuel lines play a crucial role in the transportation of fuel from the tank to the engine, and their length can vary depending on the vehicle's design and specific requirements. Understanding the maximum length of fuel lines is essential for ensuring optimal performance and preventing fuel-related issues. This paragraph will explore the factors that determine the length of fuel lines and discuss the typical range, providing valuable insights for vehicle owners and mechanics alike.
What You'll Learn
- Fuel Line Length Limits: Industry Standards and Regulations
- Factors Affecting Fuel Line Length: Temperature and Pressure
- Flexibility and Durability: Material Choices for Long Fuel Lines
- Maintenance and Inspection: Ensuring Long-Term Performance of Long Fuel Lines
- Safety Considerations: Preventing Leaks and Hazards in Long Fuel Lines
Fuel Line Length Limits: Industry Standards and Regulations
When it comes to fuel lines, there are specific length limits that are crucial to adhere to in order to ensure safety and compliance with industry standards. These regulations are in place to prevent potential hazards and maintain the integrity of the fuel system. Understanding these limits is essential for anyone involved in the installation, maintenance, or repair of fuel lines.
Industry standards for fuel line length vary depending on the type of fuel and the application. For gasoline fuel lines, the maximum length is typically around 10 to 12 feet. This is because longer lines can lead to increased pressure drop, which may result in reduced fuel flow and potential engine performance issues. In contrast, diesel fuel lines often have longer acceptable lengths, sometimes up to 15 feet or more, due to the higher pressure and flow rates associated with diesel systems. It's important to note that these lengths are general guidelines, and specific applications may require shorter or longer lines based on factors such as engine power, fuel tank location, and system design.
Regulatory bodies, such as the Environmental Protection Agency (EPA) and the Department of Transportation (DOT), have also set guidelines to ensure fuel line safety. The EPA's regulations focus on preventing fuel leaks and emissions, and they specify that fuel lines should be designed and installed to minimize the risk of contamination. These regulations often include requirements for line material, diameter, and installation practices. The DOT, on the other hand, sets standards for transportation-related fuel systems, including fuel line length, to ensure the safe movement of vehicles and the prevention of fuel-related accidents.
In addition to industry standards and regulations, it's crucial to consider the materials used in fuel lines. Different materials have varying acceptable lengths due to their inherent properties. For example, steel fuel lines may have longer acceptable lengths compared to plastic lines because of their higher pressure resistance. The choice of material also depends on factors like temperature tolerance, flexibility, and compatibility with the fuel type.
When working with fuel lines, it is imperative to stay within the specified length limits to avoid potential issues. Exceeding these limits can lead to increased fuel pressure, which may cause line damage, fuel leaks, or even explosions in extreme cases. Regular inspections and maintenance are recommended to ensure that fuel lines remain in good condition and comply with the established length requirements.
Finding the Perfect Fit: Where to Buy Molded Fuel Line for Kx65
You may want to see also
Factors Affecting Fuel Line Length: Temperature and Pressure
The length of fuel lines is a critical consideration in the design and installation of fuel systems, especially in vehicles and aircraft. While the initial length of a fuel line is determined by the layout and design of the fuel system, several factors can influence how long a fuel line can effectively be used. Among these, temperature and pressure variations play a significant role.
Temperature has a profound impact on the performance and longevity of fuel lines. In general, fuel lines are designed to operate within a specific temperature range. When temperatures drop, the fuel can become more viscous, which increases the resistance to flow. This can lead to reduced fuel delivery, especially in systems where the fuel line is exposed to cold environments. For instance, in cold climates, fuel lines may need to be longer to ensure that the fuel can flow efficiently to the engine, even when the vehicle is stationary. Conversely, in hot environments, the fuel can become less viscous, reducing the flow resistance and potentially allowing for shorter fuel lines. However, excessive heat can also cause materials to degrade over time, so it's essential to consider the operating temperature range of the fuel line material.
Pressure is another critical factor affecting fuel line length. Fuel lines are designed to withstand a certain pressure, and exceeding this pressure can lead to damage or failure. High-pressure fuel systems, such as those used in racing cars or aircraft, require carefully designed fuel lines that can handle the increased stress. Longer fuel lines may be necessary to accommodate the pressure differentials and ensure that the fuel can be delivered efficiently to the engine. In contrast, in low-pressure systems, shorter fuel lines can be used, but the system must be designed to prevent pressure drops that could affect performance.
The interaction between temperature and pressure is particularly important. In many cases, fuel lines need to operate under varying temperature and pressure conditions. For example, during takeoff in an aircraft, the engine operates at high temperatures and pressures, which can affect the fuel line's performance. Similarly, in a vehicle, the engine's temperature and pressure can change with driving conditions, requiring fuel lines that can adapt to these changes. Engineers must consider these dynamic factors when designing fuel systems to ensure optimal performance and safety.
In summary, the length of fuel lines is influenced by temperature and pressure variations, which can impact the flow rate, material integrity, and overall system performance. Understanding these factors is crucial for designing efficient and reliable fuel systems, ensuring that fuel lines are long enough to deliver fuel effectively while also considering the operating environment and conditions. Proper consideration of these factors can lead to improved fuel system design and increased reliability in various applications.
Mastering the Art of Fuel Line Removal: A Comprehensive Guide
You may want to see also
Flexibility and Durability: Material Choices for Long Fuel Lines
The length of fuel lines is a critical consideration in vehicle design and maintenance, especially for those with extended fuel tanks or those operating in challenging environments. When it comes to flexibility and durability, the choice of material is paramount. Fuel lines must be able to withstand the rigors of the road, including vibrations, temperature fluctuations, and potential impacts.
One of the primary materials used for fuel lines is rubber, known for its inherent flexibility and resilience. Natural rubber, in particular, offers excellent resistance to abrasion and chemicals, making it ideal for fuel-carrying applications. It can accommodate slight bends and twists, ensuring a reliable connection between the fuel tank and engine. However, rubber fuel lines may become brittle over time, especially in low-temperature conditions, which can lead to cracking and potential fuel leaks.
To address this issue, manufacturers often use synthetic rubbers, such as neoprene or EPDM (ethylene propylene diene monomer). These materials provide improved flexibility and temperature resistance compared to natural rubber. EPDM, in particular, is highly durable and can withstand extreme temperatures, making it suitable for a wide range of automotive applications. The flexibility of these synthetic rubbers allows for longer fuel lines without compromising performance.
Another material gaining popularity in fuel line construction is polyurethane. This material offers superior flexibility and durability, making it an excellent choice for long fuel lines. Polyurethane fuel lines are known for their resistance to abrasion, chemicals, and UV radiation, ensuring long-lasting performance. Its flexibility allows it to navigate through tight spaces and accommodate various engine configurations without kinking or becoming brittle.
In addition to material selection, the design of fuel lines also plays a crucial role in their flexibility and durability. Engineers often incorporate protective layers, such as braided steel or polyester, to reinforce the fuel line and protect it from external damage. These protective layers add flexibility while maintaining the structural integrity required for long-term use. Properly designed fuel lines with appropriate materials can ensure reliable fuel delivery, even in demanding conditions.
Suburban Fuel Return Line: 2003 Model Mystery Solved!
You may want to see also
Maintenance and Inspection: Ensuring Long-Term Performance of Long Fuel Lines
When it comes to fuel lines, their length can vary significantly depending on the application and the vehicle they are designed for. While there isn't a universal standard for the maximum length, it's essential to understand that longer fuel lines may present unique challenges and require specific maintenance and inspection protocols to ensure optimal performance and longevity. Here's a comprehensive guide on how to maintain and inspect long fuel lines:
Regular Visual Inspections: One of the most straightforward yet effective ways to maintain long fuel lines is through regular visual inspections. Over time, fuel lines can develop cracks, leaks, or damage due to various factors like age, temperature fluctuations, and exposure to contaminants. Conducting routine checks can help identify these issues early on. Look for any signs of corrosion, brittleness, or discoloration along the fuel line's length. Pay close attention to bends, fittings, and areas where the line connects to other components. Keep an eye out for any visible leaks or moisture accumulation, as these could indicate potential problems.
Pressure Testing: Long fuel lines should be periodically pressure-tested to ensure their integrity. This process involves applying pressure to the fuel system and checking for any leaks or weaknesses in the lines. Pressure testing can help identify internal damage, such as punctures or cracks, that might not be visible during a visual inspection. It is recommended to consult the vehicle's manufacturer guidelines for the appropriate pressure and testing frequency. Regular pressure testing can prevent fuel leaks, which can be dangerous and cause engine performance issues.
Fuel Line Protection: To ensure the longevity of long fuel lines, consider implementing protective measures. This includes using fuel line guards or sleeves, especially in areas where the lines are more susceptible to damage, such as under the vehicle or near exhaust systems. These protective covers can shield the fuel lines from heat, debris, and potential impacts, reducing the risk of damage and the need for premature replacements. Additionally, maintaining a clean environment for the fuel lines is crucial. Regularly cleaning the fuel tank and filter can prevent the accumulation of contaminants that could potentially damage the lines over time.
Engine and System Maintenance: Proper engine and system maintenance play a vital role in the overall health of long fuel lines. Regular engine tune-ups, including fuel system cleanings, can help ensure that the fuel is clean and free from contaminants that might cause corrosion or damage to the lines. Additionally, maintaining the vehicle's overall performance and addressing any engine issues promptly can indirectly contribute to the longevity of the fuel lines.
Professional Inspection and Replacement: While regular maintenance can go a long way, it is essential to seek professional assistance for comprehensive inspections, especially for long fuel lines. Certified mechanics can use specialized tools and techniques to identify hidden issues and provide expert advice. If damage is detected, it may be necessary to replace the affected fuel line sections or the entire line, depending on the severity. Timely replacement ensures the continued safe operation of the vehicle and prevents potential safety hazards.
2003 Xterra Fuel Line Location: A Quick Guide
You may want to see also
Safety Considerations: Preventing Leaks and Hazards in Long Fuel Lines
When dealing with long fuel lines, safety is paramount to prevent potential leaks and hazards. The length of fuel lines can vary depending on the application and specific requirements, but it's essential to understand the potential risks associated with extended fuel lines. Firstly, longer fuel lines increase the chances of fuel leakage due to the higher surface area exposed to potential damage or wear. This is especially critical in environments where fuel lines are exposed to harsh conditions, such as extreme temperatures, UV radiation, or mechanical stress. To mitigate these risks, it is crucial to use high-quality, durable materials that can withstand the environmental conditions and potential impacts.
One key safety consideration is the proper installation and support of long fuel lines. Fuel lines should be securely fastened and supported at regular intervals to prevent sagging or excessive movement, which can lead to leaks or damage. Using appropriate clamps, brackets, or tie-downs can help maintain the integrity of the fuel lines and reduce the risk of leaks. Additionally, ensuring that the fuel lines are properly insulated can further enhance safety. Insulation helps protect against temperature extremes and prevents fuel from freezing or overheating, which could cause damage to the fuel lines or the engine.
Regular maintenance and inspections are vital to identifying and addressing potential issues in long fuel lines. Over time, fuel lines can develop cracks, corrosion, or other forms of deterioration, especially in areas prone to vibration or impact. Implementing a comprehensive maintenance schedule that includes visual inspections, pressure testing, and replacement of worn-out components can help ensure the long-term safety and reliability of the fuel system. It is also essential to train personnel on recognizing signs of potential leaks or damage, enabling prompt action to prevent hazardous situations.
In addition to installation and maintenance, the choice of fuel and its compatibility with the fuel lines is crucial. Different types of fuel may have varying properties and requirements, and using the correct fuel can prevent corrosion or degradation of the fuel lines. It is advisable to consult the manufacturer's guidelines and specifications to ensure the compatibility of the fuel with the fuel lines and overall system.
Lastly, implementing safety protocols and training programs can significantly contribute to leak prevention and hazard mitigation. This includes educating personnel on safe handling practices, emergency response procedures, and the importance of regular inspections. By fostering a culture of safety and providing comprehensive training, organizations can effectively manage the risks associated with long fuel lines and ensure the well-being of their operations.
Fixing Fuel Leaks: The Best Tape for Your Car's Safety
You may want to see also
Frequently asked questions
The standard length for fuel lines in vehicles is generally around 10 to 15 feet. However, this can vary depending on the specific make and model of the vehicle, as well as the fuel system design.
Yes, fuel lines can be extended, but it should be done with caution and proper considerations. Extending fuel lines beyond the recommended length may lead to increased fuel pressure and potential safety hazards. It is crucial to consult the vehicle's manual or seek professional advice to ensure any modifications comply with safety standards.
Absolutely. Different vehicle types, such as motorcycles, boats, or aircraft, may have unique fuel system designs and length requirements. For instance, motorcycles often have shorter fuel lines due to space constraints, while larger vehicles like trucks might have longer lines to accommodate the fuel tank's position.
The length of the fuel line can influence the efficiency of fuel delivery. Longer lines may result in increased fuel pressure drop, especially at higher speeds or during acceleration. This can affect engine performance and fuel economy. Properly sizing fuel lines according to the vehicle's specifications is essential for optimal performance.
Using fuel lines that are too long can pose several risks. Longer lines may increase the chances of fuel leakage or vaporization, leading to potential engine misfires or reduced performance. Additionally, longer lines can be more susceptible to damage from vibrations, temperature changes, or external factors, which could result in fuel system failures.