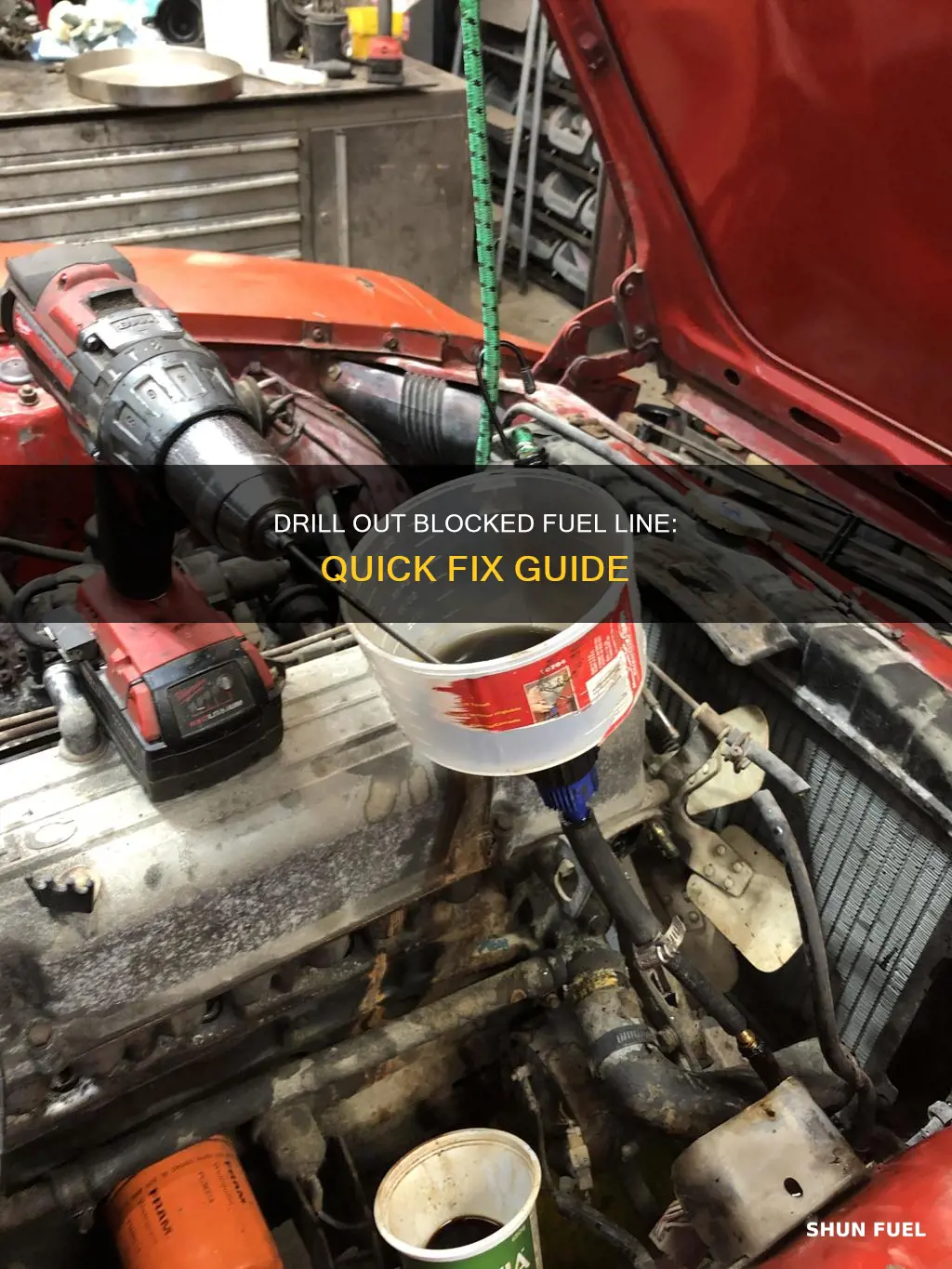
Drilling out a blocked fuel line can be a necessary step to resolve fuel system issues in vehicles. This process involves carefully removing the blockage to ensure the engine receives the necessary fuel for optimal performance. It requires a systematic approach, including identifying the blocked section, using the right tools, and following safety protocols to avoid damage to the fuel system and potential engine issues. Understanding the steps and techniques involved in this procedure is essential for anyone attempting to fix fuel line blockages.
What You'll Learn
- Safety Gear: Wear safety glasses, gloves, and a respirator to protect from debris and fumes
- Fuel Line Location: Identify the blocked fuel line using a fuel line diagram or a visual inspection
- Drill Bit Selection: Choose a drill bit with a diameter slightly larger than the fuel line
- Drill Bit Orientation: Angle the drill bit at a 45-degree angle to the fuel line to avoid damage
- Drill Speed and Pressure: Use a slow, steady drilling speed and moderate pressure to avoid cracking the fuel line
Safety Gear: Wear safety glasses, gloves, and a respirator to protect from debris and fumes
When attempting to drill out a blocked fuel line, prioritizing safety is crucial. The process involves working with potentially hazardous materials and equipment, so it's essential to take the necessary precautions to protect yourself. Here's a detailed guide on the safety gear you should wear:
Safety Glasses: Protecting your eyes is paramount. Fuel lines can release small particles or debris during the drilling process, which can fly off at high speeds. These particles can cause eye irritation, injury, or even blindness. Wearing safety glasses designed to withstand impact and debris will shield your eyes from any potential hazards. Look for glasses that offer side protection to cover the entire eye area and ensure they fit comfortably over your prescription glasses or contact lenses.
Gloves: Your hands and arms are vulnerable to injury during this task. The drilling process may generate heat, sparks, or sharp debris, which can cause cuts, burns, or other injuries. Wearing heavy-duty gloves made from durable materials like leather or synthetic blends will provide a protective barrier. Choose gloves with a good grip to ensure you have control over the drilling tool. Look for gloves that are heat-resistant and offer protection against sharp objects to ensure your hands stay safe.
Respirator: Working with fuel lines can expose you to harmful fumes and vapors. These substances can be toxic and cause respiratory issues if inhaled. A respirator mask will filter out the harmful particles and fumes, ensuring that you breathe clean air. Select a respirator that fits snugly over your nose and mouth, covering both the upper and lower parts of your face. Look for models with a high filtration efficiency and a comfortable design to ensure you can work without discomfort.
Additionally, consider wearing a full-body protective suit or apron to safeguard your skin from any potential splashes or spills. It's also a good idea to work in a well-ventilated area or set up a temporary exhaust system to remove fumes from the immediate vicinity. Remember, taking these safety precautions will not only protect you but also ensure that the job is done efficiently and without unnecessary risks.
Optimizing Engine Performance: Choosing the Right Fuel Line for 6Y2-24360-60-00 Primer
You may want to see also
Fuel Line Location: Identify the blocked fuel line using a fuel line diagram or a visual inspection
When dealing with a blocked fuel line, the first step is to locate the specific line that is causing the issue. This can be done by referring to a fuel line diagram, which is a visual representation of the fuel system in your vehicle. The diagram will show the various components, including the fuel tank, fuel pump, injectors, and the lines connecting them. By studying this diagram, you can identify the exact path of the fuel line that is blocked.
Start by examining the diagram and tracing the fuel line from the fuel tank to the engine. Look for any intersections or connections where the line might be blocked. Often, fuel lines are color-coded or labeled for easy identification, making it simpler to pinpoint the issue. If you have access to the physical fuel system in your vehicle, a visual inspection can be more straightforward.
Under the hood, locate the fuel tank and identify the fuel pump, which is responsible for sending fuel to the engine. Follow the fuel lines from the pump to the injectors or carburetor. Inspect each line for any signs of damage, kinks, or blockages. Look for any visible obstructions, such as dirt, debris, or even a small object that might have entered the line.
In some cases, the fuel line might be hidden behind other components or difficult to access. If this is the case, you may need to remove certain parts to gain better visibility. Take your time and be gentle when removing any parts to avoid further damage. Once you've identified the blocked fuel line, you can proceed with the appropriate repair or replacement.
Remember, proper identification of the fuel line is crucial before attempting any repairs. It ensures that you target the correct issue and prevents unnecessary damage to other components. If you're unsure about the location or the fuel system's complexity, consulting a professional mechanic is always a wise decision. They can provide expert guidance and ensure the job is done safely and effectively.
Mastering the Art of Bending Auto Fuel Lines: A Kink-Free Guide
You may want to see also
Drill Bit Selection: Choose a drill bit with a diameter slightly larger than the fuel line
When dealing with a blocked fuel line, the goal is to carefully and precisely remove the obstruction without causing further damage to the fuel system. One effective method to achieve this is by using a drill bit to create a new passageway. The key to success lies in selecting the right drill bit, ensuring it is slightly larger than the original fuel line.
The diameter of the drill bit is crucial as it needs to be just large enough to accommodate the fuel flow while also being manageable to insert and remove. A common approach is to choose a drill bit with a diameter that is approximately 1/8 inch (3.175 mm) larger than the original fuel line. This extra clearance allows for a smooth passage for the fuel, ensuring it flows freely without any restrictions. For instance, if the original fuel line has a diameter of 0.25 inches, a drill bit with a diameter of 0.3125 inches would be an appropriate choice.
It's important to consider the material of the fuel line as well. Different materials may require specific drill bit sizes. For example, if the fuel line is made of rubber or plastic, a slightly larger drill bit might be needed to account for the material's flexibility. In contrast, a stiffer material like steel may require a more precise fit.
When selecting the drill bit, ensure it is made of high-quality materials to withstand the drilling process and the fuel's corrosive properties. Carbide or high-speed steel drill bits are excellent choices for this task due to their durability and ability to cut through various materials. Additionally, consider the length of the drill bit, ensuring it is long enough to reach the blockage but not so long that it becomes difficult to control.
Remember, the goal is to create a clean and precise hole, so take your time and use a steady hand. Drilling with the correct bit size will ensure a successful fuel line repair, allowing your vehicle to run smoothly again.
Moped Fuel Line Cleaning: A Step-by-Step Guide to Fresh Performance
You may want to see also
Drill Bit Orientation: Angle the drill bit at a 45-degree angle to the fuel line to avoid damage
When attempting to clear a blocked fuel line, it's crucial to approach the task with precision and care to avoid any further damage to the vehicle's fuel system. One of the most critical aspects of this process is the orientation of the drill bit. Here's a detailed guide on how to angle the drill bit correctly:
Angle the Drill Bit at a 45-Degree Angle: The key to successful and safe drilling is to maintain a precise angle. Aim to angle the drill bit at approximately 45 degrees to the surface of the fuel line. This angle allows for a controlled and gradual approach to the blockage, reducing the risk of damaging the fuel line or causing any sudden, forceful entry into the line. By using this angle, you can ensure that the drill bit cuts through the blockage without applying excessive pressure, which could lead to cracks or tears in the fuel line material.
To achieve this angle, hold the drill in a way that your arm forms a 45-degree angle to the line of the fuel line. This might require some practice and a steady hand to maintain the desired orientation. It's important to keep the drill bit as straight as possible to avoid any unintended movement or damage to the surrounding components.
Additionally, consider the direction of the fuel line. If it runs along the side of the engine or under the vehicle, you might need to adjust your position and the drill's angle accordingly to access the blockage without causing any unintended consequences. Always be mindful of the fuel line's path to ensure your drilling efforts are directed accurately.
Remember, the goal is to create a clean and precise cut through the blockage without causing any unnecessary damage. This technique, combined with the right drill bit and a steady hand, will significantly increase your chances of successfully clearing the blocked fuel line.
Fuel Line Installation: From Tank to Engine in 5 Steps
You may want to see also
Drill Speed and Pressure: Use a slow, steady drilling speed and moderate pressure to avoid cracking the fuel line
When tackling a blocked fuel line, it's crucial to employ the right drilling technique to ensure a successful and safe outcome. One of the most critical aspects is controlling the drilling speed and pressure. Here's a detailed guide on how to approach this:
Drilling at a slow and steady pace is essential. Rushing the process can lead to several issues. Firstly, it may cause the drill bit to wander or veer off the desired path, potentially damaging the fuel line further. A slow speed allows for better control and precision, ensuring that the hole is drilled straight and accurately. Imagine the fuel line as a delicate structure; applying too much force too quickly can result in cracking or breaking, which would be a costly mistake.
Moderate pressure is the key to success. The fuel line is a relatively thin and flexible component, so excessive force can cause it to kink, bend, or even rupture. By using moderate pressure, you maintain control over the drilling process. This controlled approach ensures that the drill bit cuts through the blockage without causing unnecessary damage to the surrounding areas or the fuel line itself. It's a delicate balance, requiring patience and a steady hand.
The technique described above is particularly useful when dealing with hardened deposits or corrosion that might require more force to remove. By applying slow, deliberate movements and moderate pressure, you can effectively break through these obstructions without compromising the integrity of the fuel line. This methodical approach is often more reliable than using high-speed drilling, which can lead to uncontrolled and potentially dangerous outcomes.
In summary, when drilling out a blocked fuel line, remember that speed and pressure are critical factors. A slow, steady drilling speed, combined with moderate pressure, will help you navigate the fuel line's delicate nature and increase the chances of a successful repair without causing further damage. Always prioritize control and precision to ensure a safe and effective solution.
Mastering Carburetor Fuel Flow: A Guide to Running Return Lines
You may want to see also
Frequently asked questions
To tackle this task, you'll need a few essential tools. Firstly, a fuel line drill guide or a mandrel is crucial to ensure a clean and precise hole. This tool acts as a guide for the drill bit, preventing it from wandering. Additionally, a high-speed drill bit specifically designed for fuel lines is recommended. It's important to choose a bit with the appropriate diameter to match the fuel line. Don't forget to have a fuel line cutter or a pair of sharp scissors to trim the damaged section of the line.
Locating the blocked fuel line can be a challenging task. Start by inspecting the fuel tank and lines for any visible signs of damage or blockages. Often, fuel lines are routed through engine compartments, so accessing these areas may be necessary. You can use a fuel pressure gauge to check for pressure drops, indicating a potential blockage. If the line is difficult to access, consider using a fuel line inspector or a camera-equipped scope to visualize the interior of the line and identify the blockage.
Absolutely, safety should always be a top priority. Before starting, ensure the engine is cool to avoid burns. Wear protective gear, including safety goggles and gloves, to shield your eyes and hands from debris and potential fuel splashes. It's crucial to work in a well-ventilated area to avoid inhaling fuel vapors. Additionally, be cautious of nearby electrical components to prevent any accidental damage.
Here's a step-by-step guide: Start by disconnecting the fuel line from the fuel tank and the engine. Use the fuel line cutter to trim any damaged or blocked sections. Attach the drill guide to the fuel line, ensuring it's securely in place. Select the appropriate drill bit and insert it into the guide, starting the drilling process. Keep the drill steady and follow the line's path. Once the hole is drilled, carefully remove the drill bit and insert a new fuel line, ensuring a tight connection. Test the system to ensure proper fuel flow.