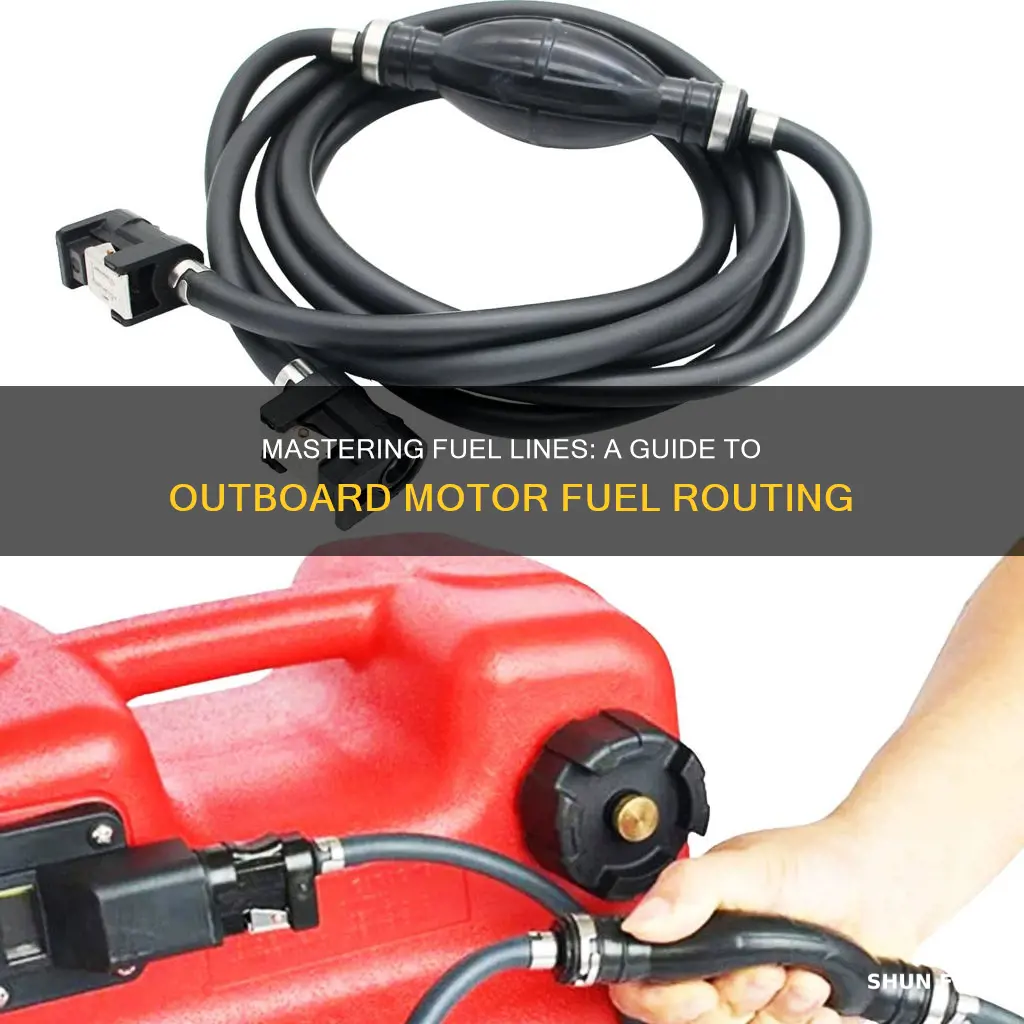
Determining the correct fuel line connection to an outboard motor is a crucial step in ensuring the engine's proper functioning and longevity. This process involves understanding the specific make and model of the motor, as well as the type of fuel system it employs. By following a step-by-step guide tailored to your motor, you can efficiently connect the fuel line, ensuring a steady and reliable fuel supply to the engine. This guide will provide clear instructions on identifying the correct fuel line, connecting it to the motor, and verifying the setup for optimal performance.
Characteristics | Values |
---|---|
Fuel Line Material | Typically made of rubber, vinyl, or a flexible plastic material like polyurethane. |
Fuel Line Diameter | Varies depending on the engine size and fuel requirements, commonly ranging from 3/8" to 1/2" in diameter. |
Length | The length of the fuel line depends on the distance between the fuel tank and the engine, often measured in feet. |
Clamps | Used to secure the fuel line to the engine and tank, ensuring a tight and leak-free connection. |
Fuel Filter | Often integrated into the fuel line or connected to it, to filter contaminants and ensure clean fuel delivery. |
Color Coding | Some fuel lines are color-coded to indicate the direction of fuel flow (e.g., red for return, blue for prime). |
Flexibility | Fuel lines need to be flexible to accommodate engine movement and vibrations. |
Pressure Rating | Fuel lines should be rated to handle the pressure of the fuel system, typically gasoline or diesel. |
Compatibility | Ensure the fuel line is compatible with the fuel type (gasoline, diesel, ethanol) and engine requirements. |
Installation | Proper installation is crucial, including correct routing, securing, and using the appropriate fuel line connectors. |
What You'll Learn
- Engine Type: Identify engine type (e.g., 2-stroke, 4-stroke) to match fuel line specifications
- Fuel System: Understand the fuel system (carburetor, fuel injection) to route fuel correctly
- Fuel Pump Location: Locate the fuel pump to ensure proper fuel flow to the motor
- Fuel Filter: Check and replace the fuel filter regularly to prevent contamination
- Fuel Tank: Ensure the fuel tank is compatible and properly connected to the motor
Engine Type: Identify engine type (e.g., 2-stroke, 4-stroke) to match fuel line specifications
When it comes to outboard motors, understanding the engine type is crucial for selecting the appropriate fuel line. The engine type, whether it's a 2-stroke or 4-stroke, significantly influences the fuel line's design and functionality. Here's a detailed guide on how to identify the engine type and match the fuel line specifications accordingly.
2-Stroke Engine:
2-stroke engines are known for their simplicity and power-to-weight ratio. They power many smaller boats and recreational watercraft. In a 2-stroke engine, the fuel and air mixture is ignited directly in the cylinder, and the exhaust is often routed through a small pipe or port. When identifying a 2-stroke engine, look for the following characteristics: a single cylinder, a spark plug, and a carburetor that mixes fuel and air. The fuel line for a 2-stroke engine is typically designed to handle a higher flow rate due to the engine's power output. It usually has a larger diameter and a more flexible material to accommodate the engine's unique requirements.
4-Stroke Engine:
4-stroke engines are more common in larger boats and offer several advantages, including better fuel efficiency and lower emissions. In a 4-stroke engine, the fuel and air mixture is ignited in a separate chamber, and the exhaust is expelled through a dedicated pipe. 4-stroke engines often feature a more complex design with multiple cylinders, a crankcase, and an air intake system. When identifying a 4-stroke engine, you'll notice a larger number of cylinders, a crankcase breather, and a more intricate fuel injection system. The fuel line for a 4-stroke engine is generally designed to be more precise and controlled, as it often relies on electronic fuel injection for optimal performance.
Matching Fuel Line Specifications:
Once you've identified the engine type, it's essential to match the fuel line specifications accordingly. For 2-stroke engines, the fuel line should be designed to handle the higher fuel flow and pressure, often requiring a larger diameter and more robust construction. In contrast, 4-stroke engines may benefit from a fuel line with a more precise diameter to ensure efficient fuel delivery and accurate injection. Additionally, consider the engine's operating temperature and the fuel's properties to choose a fuel line material that can withstand these conditions.
Remember, proper identification of the engine type is the first step in ensuring your outboard motor receives the correct fuel line. This will not only optimize performance but also contribute to the longevity of your engine and overall boating experience. Always refer to the manufacturer's guidelines or consult a marine mechanic for specific recommendations based on your outboard motor model.
Fuel Line Attachment: A Guide to Priming Your McCulloch Chainsaw
You may want to see also
Fuel System: Understand the fuel system (carburetor, fuel injection) to route fuel correctly
The fuel system of an outboard motor is a crucial component that ensures the engine receives the correct amount of fuel for efficient operation. Understanding the fuel system, whether it's a carburetor or fuel injection setup, is essential for proper maintenance and troubleshooting. Here's a breakdown of how to approach this:
Carburetor Fuel System: In older outboard motors, carburetor systems are common. A carburetor mixes air and fuel, creating a combustible mixture that is then delivered to the engine. The fuel line in this setup is typically a simple tube that connects the fuel tank to the carburetor. It's important to note the position of the carburetor and the orientation of the fuel line to ensure proper routing. The fuel line should be routed away from hot engine components to prevent overheating and potential fuel degradation. Additionally, check for any clogs or restrictions in the fuel line, as a restricted flow can lead to poor engine performance.
Fuel Injection System: Modern outboard motors often feature fuel injection technology, which provides a more precise and efficient fuel delivery system. In this setup, the fuel line is usually a high-pressure line that connects the fuel tank to the fuel injectors. Each injector has its own dedicated fuel line, ensuring individual control over fuel delivery to each cylinder. Understanding the layout of the fuel injectors and their respective fuel lines is crucial. The fuel lines should be routed to maintain a consistent pressure and flow rate, ensuring optimal engine performance. Regularly inspect the fuel injectors and lines for any signs of damage or contamination, as this can lead to poor fuel atomization and engine misfires.
To ensure correct routing, it's essential to consult the outboard motor's manual, which provides detailed diagrams and specifications for the fuel system. These diagrams will show the exact locations of the carburetor or fuel injectors and the recommended path for the fuel lines. By following these guidelines, you can ensure that the fuel is directed to the correct components, promoting efficient combustion and optimal engine performance.
When working on the fuel system, always exercise caution and wear appropriate personal protective equipment (PPE) to avoid any potential hazards associated with fuel handling. Regular maintenance and cleaning of the fuel system can also help prevent issues, ensuring your outboard motor operates smoothly and reliably.
Mastering the Art of Fuel Line Disconnects: A Guide to Using the Lisle Tool
You may want to see also
Fuel Pump Location: Locate the fuel pump to ensure proper fuel flow to the motor
Locate the fuel pump, which is a critical component in ensuring the proper flow of fuel to the outboard motor. The pump's primary function is to increase the pressure of the fuel, allowing it to travel efficiently through the fuel lines to the engine. To find it, start by consulting your outboard motor's manual, as the specific location can vary depending on the make and model. Typically, it is positioned near the fuel tank, often mounted on the side or bottom of the tank or in a dedicated fuel module.
In some cases, the pump might be integrated into the fuel tank itself, where it draws fuel from the tank and pumps it to the engine. If your motor has a separate fuel module, it will usually be located beneath the motor or in a compartment accessible by removing the motor cover. Inspect the module for any signs of damage or wear, as a faulty pump can lead to poor fuel delivery and potential engine issues.
When accessing the pump's location, consider the following: Ensure the motor is cooled down and parked on a level surface to avoid any accidents. Disconnect the negative battery cable to prevent the motor from starting unexpectedly. Inspect the pump for any visible signs of damage, corrosion, or debris buildup. Check for proper fuel flow by temporarily disconnecting the fuel line and observing the flow rate. A weak or inconsistent flow may indicate a clogged or damaged pump.
If you're unsure about the pump's location or its condition, consult a qualified marine mechanic or refer to online resources specific to your motor's make and model. Proper pump placement and functionality are essential for optimal engine performance and longevity. Regular maintenance, including checking the pump's condition and ensuring it is securely mounted, will help prevent fuel-related issues and ensure a reliable outboard motor.
Fuel Pump Ball Location: A Guide to Finding the Perfect Spot
You may want to see also
Fuel Filter: Check and replace the fuel filter regularly to prevent contamination
Checking and replacing the fuel filter is an essential maintenance task for any outboard motor to ensure optimal performance and longevity. Over time, fuel filters can become clogged or damaged, leading to potential issues with fuel flow and engine operation. Here's a step-by-step guide on how to inspect and replace the fuel filter:
- Locate the Fuel Filter: Start by familiarizing yourself with the location of the fuel filter on your outboard motor. The filter is typically connected to the fuel line, which supplies fuel from the tank to the engine. It can be found along the fuel line, often near the engine or in the bilge area. Refer to your motor's manual if you're unsure about its exact position.
- Inspect for Contamination: Before replacing the filter, check for any signs of contamination or damage. Remove the fuel filter and examine it for clogs, debris, or cracks. If you notice any blockages or visible contaminants, it's a clear indication that the filter needs to be replaced. Additionally, look for any signs of fuel leakage around the filter connections, as this could indicate a faulty o-ring or gasket.
- Cleaning and Reusing (Optional): In some cases, you might be able to clean and reuse the fuel filter if it's not severely damaged. Carefully remove any debris or contaminants using a soft brush or compressed air. Ensure that you clean the filter housing and the filter element itself. However, it's important to note that not all filters are reusable, and some may require replacement even after cleaning.
- Replacing the Fuel Filter: If the filter is clogged, damaged, or shows signs of contamination, it's time to replace it. Purchase a new fuel filter that is compatible with your outboard motor model. When installing the new filter, ensure a tight connection and secure it in place. Use a fuel line connector if necessary to make the installation process easier. After replacing the filter, run the engine for a few minutes to ensure proper fuel flow and verify that there are no leaks.
Regularly checking and replacing the fuel filter is crucial to maintain a clean fuel supply to the engine, preventing potential engine damage caused by contaminated fuel. By following these steps, you can ensure that your outboard motor operates efficiently and reliably, extending its lifespan. Remember, proper maintenance and timely replacements can save you from costly repairs and keep your motor running smoothly.
Mastering Fuel Efficiency: A Guide to Bypassing the Return Line
You may want to see also
Fuel Tank: Ensure the fuel tank is compatible and properly connected to the motor
When it comes to maintaining an outboard motor, ensuring that the fuel tank is compatible and properly connected is a crucial aspect of the setup. This process involves several key steps to guarantee optimal performance and prevent potential issues. Firstly, identify the specific fuel tank designed for your outboard motor model. Each motor typically requires a fuel tank with the right dimensions, capacity, and mounting configuration to fit seamlessly. Check the manufacturer's specifications or consult the motor's manual to find the recommended fuel tank type. This ensures compatibility in terms of size, thread sizes, and mounting points, allowing for a secure and reliable connection.
Once you've identified the compatible fuel tank, inspect it for any signs of damage or wear. Look for cracks, leaks, or any structural issues that could compromise its functionality. Ensure that the fuel tank is clean and free from debris or contaminants that might affect the fuel's quality. Proper cleaning can be done using a fuel filter or by running a fuel stabilizer through the system. This step is essential to maintain the motor's performance and longevity.
The next step is to carefully connect the fuel tank to the motor. Start by securing the tank in its designated position, ensuring it is tightly mounted to avoid any movement during operation. Then, attach the fuel lines, which should be made of compatible materials such as rubber or plastic, to the appropriate ports on both the fuel tank and the motor. Tighten the connections securely, but be cautious not to overtighten, as this can lead to damage. The fuel lines should be routed away from moving parts to prevent damage and ensure a smooth flow of fuel.
After the physical connections, it's crucial to test the setup. Start the motor and monitor its performance, checking for any leaks or unusual noises. Ensure that the fuel is flowing correctly and that the motor is running smoothly. If any issues arise, it may indicate a problem with the fuel tank or lines, requiring further investigation and potential adjustments.
In summary, ensuring the fuel tank's compatibility and proper connection is a vital part of maintaining an outboard motor. By following the manufacturer's guidelines, inspecting the tank for damage, and securely connecting it to the motor, you can optimize performance and prevent potential fuel-related problems. Regular maintenance and attention to these details will contribute to the overall reliability and longevity of your outboard motor.
Motorcycle Fuel Line: Top Stores for Quality Parts
You may want to see also
Frequently asked questions
Determining the right fuel line for your outboard motor involves a few steps. First, consult the manufacturer's manual or specifications for your motor, as it will provide the recommended fuel line type and size. Look for the engine's model number and year, as different models may require specific fuel lines. You can also measure the existing fuel line (if any) to ensure a proper fit. Common fuel lines used are rubber or vinyl, and they come in various diameters, typically ranging from 3/8" to 1/2" ID.
When selecting a fuel line, consider the motor's power output, operating conditions, and the fuel's type. Higher-performance motors may require larger-diameter fuel lines to handle increased pressure and fuel flow. Operating in rough waters or with a heavy load might necessitate a more flexible and durable fuel line. Additionally, ensure the fuel line material is compatible with the fuel type, whether it's gasoline or diesel.
Using a different diameter fuel line is generally not recommended unless specifically advised by the manufacturer. The original fuel line is designed to handle the motor's fuel flow and pressure requirements. A smaller diameter line may restrict fuel delivery, leading to performance issues, while a larger one could cause unnecessary fuel wastage and potential engine damage due to increased pressure.
Proper installation is crucial for optimal motor performance. Start by cleaning the fuel line ends and ensuring they are free of debris. Use fuel line connectors or clamps that match the line's material. Route the fuel line away from hot engine components to prevent damage. Secure the line using the appropriate mounting hardware, ensuring it's tight enough to prevent slippage but not overly tight, causing damage to the line or motor. Regularly inspect the fuel line for any signs of wear or damage during maintenance checks.