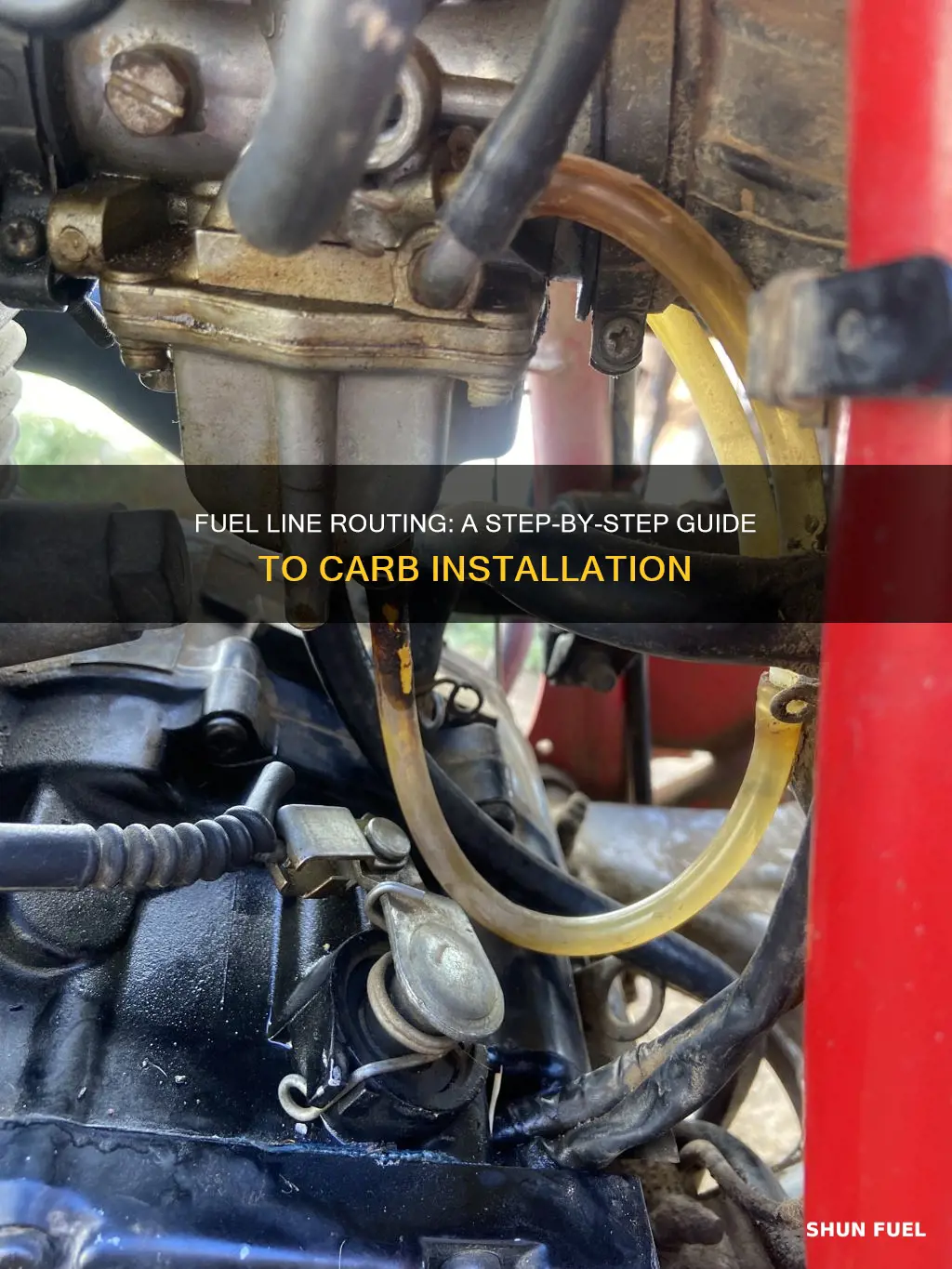
Running fuel lines to a carburetor is a crucial step in any engine build or repair project. It involves connecting the fuel source, typically a fuel pump or tank, to the carburetor's float bowl or jetting system. This process requires careful consideration of fuel line routing, material selection, and proper installation to ensure optimal performance and prevent fuel leaks. By following a step-by-step guide, you can effectively route the fuel lines, ensuring a reliable fuel supply to the carburetor and ultimately enhancing the engine's power and efficiency.
What You'll Learn
- Location: Choose optimal spots for fuel lines, considering engine space and accessibility
- Routing: Plan routes to avoid interference with other components
- Materials: Select appropriate materials for fuel lines and fittings
- Clamping: Use secure clamps to fasten lines to carb and engine
- Testing: Inspect fuel lines for leaks and ensure proper fuel flow
Location: Choose optimal spots for fuel lines, considering engine space and accessibility
When planning the route for your fuel lines, it's crucial to consider the engine's layout and the available space. The goal is to ensure that the lines are secure, well-protected, and easily accessible for maintenance. Here's a step-by-step guide to help you choose the optimal locations:
Under the Engine Bay: One of the most common and practical locations for fuel lines is beneath the engine bay. This area provides ample space and is typically less prone to damage from road debris or accidental impacts. Route the lines along the firewall, ensuring they are close to the engine but not directly in the way of any moving parts. This placement allows for easy access during inspections and maintenance.
Above the Engine Compartment: In some cases, running fuel lines above the engine compartment can be advantageous. This approach might be suitable if the engine is mounted low in the vehicle, providing more headroom. Secure the lines with rubber or plastic hangers to keep them off the ground and away from potential hazards. Ensure that the lines are routed away from any heat sources or exhaust components to prevent overheating and potential fuel degradation.
Consider Engine Mounting and Access Panels: The position of the engine and the presence of access panels can influence your fuel line routing. If the engine is mounted in a way that creates a confined space, you might need to carefully navigate the lines around the mounting points. Additionally, if there are access panels or hoods that need to be opened frequently, ensure that the fuel lines are not in the way, as they could get damaged or caught.
Accessibility and Maintenance: The chosen locations should prioritize accessibility for regular maintenance and inspections. Avoid areas where the lines might be difficult to reach, especially if the vehicle is used for off-road adventures or in challenging terrain. Properly securing the lines with clips, ties, or brackets will prevent them from becoming tangled or caught during operation.
Remember, the key is to balance the need for protection and accessibility. By carefully selecting the spots for your fuel lines, you ensure that your carburetor receives the necessary fuel while also maintaining the overall health and longevity of your engine.
Optimizing Fuel Delivery: Choosing the Right Size Fuel Line for LO206 Engines
You may want to see also
Routing: Plan routes to avoid interference with other components
When routing fuel lines to a carburetor, careful planning is essential to ensure optimal performance and reliability. The primary goal is to maintain a consistent fuel supply while avoiding any potential interference with other engine components. Here's a detailed guide on how to approach this task:
Assess the Engine Bay: Begin by thoroughly inspecting the engine bay and familiarizing yourself with its layout. Identify the positions of the carburetor, fuel tank, and other critical components such as the engine block, transmission, and exhaust system. Understanding the spatial arrangement will help you make informed decisions about the best routes for the fuel lines. Look for any obstacles or areas where the lines might need to be routed around or over.
Plan the Route: Design a route that ensures the fuel lines are as straight and direct as possible from the fuel tank to the carburetor. Avoid sharp bends or kinks, as these can restrict fuel flow and potentially cause damage over time. Aim for a path that minimizes the length of the lines, as longer routes increase the risk of fuel degradation and potential leaks. Consider the height and position of the carburetor; if it is mounted low, the lines should ideally be routed downwards to maintain a consistent fuel level.
Clearance and Interference: One of the critical aspects of routing is ensuring that the fuel lines have sufficient clearance from other engine parts. Check for any moving components, such as valves, camshafts, or gears, that could come into contact with the lines. Proper clearance will prevent damage and ensure the lines remain intact during engine operation. Additionally, avoid routing the lines too close to hot surfaces or under high-pressure areas to prevent potential fuel line damage.
Use Appropriate Support: To maintain the integrity of the fuel lines, consider using rubber or plastic supports. These can be strategically placed along the route to hold the lines in position and protect them from sharp edges or vibrations. Ensure that the supports are secure and do not restrict the movement of other engine parts. Regularly inspect and replace any worn-out supports to guarantee long-term reliability.
Consider Fuel Type and Quality: Different types of fuel may require specific considerations. For instance, ethanol-blended fuels can be more corrosive, so it's crucial to use appropriate materials for the fuel lines and fittings. Always refer to the fuel manufacturer's guidelines for optimal routing and protection. Proper fuel line maintenance will contribute to the overall performance and longevity of your engine.
Tygon Fuel Line: Unlocking the Secrets of High-Performance Fuel Delivery
You may want to see also
Materials: Select appropriate materials for fuel lines and fittings
When it comes to selecting materials for fuel lines and fittings, it's crucial to consider factors such as engine requirements, environmental conditions, and the overall performance and longevity of the system. Here's a detailed guide on the materials to choose for your fuel line setup:
Fuel Lines:
- Rubber: This is a traditional and widely used material for fuel lines due to its flexibility, durability, and resistance to fuel degradation. Natural rubber is commonly employed, offering good temperature and chemical stability. It is suitable for most fuel types, including gasoline and some alcohols. However, it may not be ideal for high-temperature environments or fuels with high water content.
- Synthetic Materials: Modern fuel lines often utilize synthetic compounds like EPDM (Ethylene Propylene Diene Monomer) or SBR (Styrene-Butadiene Rubber). These materials provide enhanced flexibility, temperature resistance, and improved fuel compatibility compared to natural rubber. They are less prone to cracking and offer better overall performance in various conditions.
- Braided Steel: For high-performance applications or where flexibility is not a primary concern, braided steel fuel lines are an excellent choice. These lines are known for their strength, rigidity, and resistance to fuel leaks. They are often used in racing or high-demand situations but may be less flexible than rubber or synthetic options.
Fittings and Connectors:
- Metal Fittings: Brass, bronze, and stainless steel are popular choices for fuel line fittings. These materials offer excellent corrosion resistance, ensuring a long-lasting connection. Brass fittings are commonly used due to their ease of installation and cost-effectiveness. Stainless steel provides superior durability and is ideal for marine or outdoor applications where corrosion is a concern.
- Rubber or Synthetic Gaskets: When connecting fuel lines, use gaskets made from compatible rubber or synthetic materials. These gaskets should provide a secure seal while allowing for some flexibility to accommodate minor vibrations and temperature changes. Ensure the gasket material is compatible with the chosen fuel type to prevent leaks and degradation.
- Clamps: Opt for sturdy metal clamps, such as stainless steel or aluminum, to secure fuel lines. These clamps should be adjustable to accommodate different line diameters and provide a tight, leak-free connection.
When sourcing materials, consider the specific requirements of your engine and the environmental conditions it will operate in. Always refer to the manufacturer's recommendations and specifications for the best results. Proper material selection will ensure a reliable and efficient fuel delivery system, contributing to optimal engine performance.
Powerful Engine Demands: Choosing the Right Fuel Line for 1000 HP
You may want to see also
Clamping: Use secure clamps to fasten lines to carb and engine
When connecting fuel lines to a carburetor, ensuring a secure and reliable clamp is essential for optimal performance and safety. Clamps play a critical role in maintaining a tight seal and preventing fuel leaks, which can lead to engine misfires, reduced power, and potential safety hazards. Here's a detailed guide on how to properly clamp fuel lines to the carburetor and engine:
Understanding the Clamp System:
Start by familiarizing yourself with the specific clamp system used in your vehicle. Different engines and carburetor designs may require unique clamp types and sizes. Typically, you'll use metal or plastic clamps, often with a spring-loaded or screw-type mechanism to secure the fuel lines. Identify the appropriate clamp size and material for your application.
Preparation and Tools:
Gather the necessary tools before beginning the clamping process. You'll need adjustable wrenches or pliers to tighten the clamps, ensuring a firm grip without damaging the fuel lines. Additionally, have a fuel line inspection tool or a similar device to check for leaks at the clamp connections.
Clamping Process:
- Position the Clamps: Locate the fuel lines that need to be connected to the carburetor. Position the clamps at the points where the lines attach to the carburetor and the engine block. Ensure the clamps are easily accessible for adjustment and inspection.
- Secure the Lines: Slide the clamp over the fuel line, ensuring it covers the entire diameter of the line. The clamp should be positioned so that the flat or smooth side faces the engine or carburetor, providing a secure base for the connection.
- Tighten the Clamp: Use your wrench or pliers to tighten the clamp securely. Apply firm pressure to ensure a tight seal, but be careful not to overtighten, as this can damage the fuel line. The goal is to create a snug fit without causing any bends or kinks in the line.
- Check for Leaks: After tightening, inspect the clamp connection for any signs of fuel leakage. Even a small leak can lead to significant issues over time. If you detect a leak, carefully loosen the clamp and re-tighten it, ensuring the fuel line is properly aligned and the clamp is secure.
Additional Tips:
- Always use the correct clamp size and type for your specific application.
- Ensure the fuel lines are clean and free of any debris before clamping.
- Regularly inspect the clamp connections, especially after any maintenance or repairs, to ensure they remain secure and leak-free.
- Consider using fuel line protectants or lubricants to reduce friction and prevent damage at the clamp points.
By following these clamping techniques, you can ensure a reliable and safe fuel supply to your engine, promoting optimal performance and longevity. Remember, proper clamping is a crucial step in the process of running fuel lines to a carburetor.
Ultimate Guide: Best Fuel Line Material for Maximum Performance
You may want to see also
Testing: Inspect fuel lines for leaks and ensure proper fuel flow
When testing the fuel lines connected to your carburetor, it's crucial to ensure there are no leaks and that the fuel is flowing correctly. This process involves a few key steps to guarantee optimal performance. Firstly, you'll need to locate the fuel lines, which are typically made of rubber or plastic and run from the fuel tank to the carburetor. These lines carry gasoline from the tank to the carburetor, where it mixes with air and is then fed into the engine.
The first step in testing is to inspect the fuel lines for any signs of damage or deterioration. Over time, fuel lines can crack, dry out, or become brittle, leading to potential leaks. Look for any visible cracks, punctures, or signs of swelling along the length of the lines. Additionally, check for any signs of fuel seepage around the connections and fittings. Even a small leak can lead to engine misfires, reduced performance, and potential damage over time.
To test for leaks, you can use a few methods. One common approach is to use a soapy water solution. Fill a spray bottle with a mixture of dish soap and water and spray it onto the fuel lines, especially at the connections and fittings. If you notice any bubbles forming on the surface, it indicates a leak, as the soap will create bubbles where fuel is escaping. Alternatively, you can use a pressure gauge to check for leaks by connecting it to the fuel lines and ensuring the pressure holds steady.
Once you've identified any potential issues, it's time to ensure proper fuel flow. Start the engine and listen for any unusual noises, such as hissing or roaring, which could indicate a restriction or leak in the fuel lines. You can also use a fuel pressure gauge to measure the pressure at the carburetor. The ideal pressure will vary depending on your engine and vehicle, but it should be within a specified range. If the pressure is too low, it may indicate a restriction or leak in the fuel lines or a problem with the fuel pump.
If you find any leaks or issues during the inspection, it's essential to address them promptly. Repair or replace the affected fuel lines to ensure your engine receives the necessary fuel for optimal performance. Regularly checking and maintaining your fuel lines will help prevent engine problems and ensure a reliable vehicle.
Fuel Line Routing: Connecting Cylinder Heads for Optimal Performance
You may want to see also
Frequently asked questions
The fuel line size depends on the carburetor's capacity and the engine's power output. As a general rule, a larger carburetor will require a thicker fuel line to handle the increased fuel flow. It's essential to consult the vehicle's manual or seek advice from a mechanic to ensure you choose the appropriate size.
No, it's crucial to use fuel lines designed specifically for automotive applications. Standard rubber fuel lines are commonly used and offer good flexibility and durability. Ensure the fuel line has a suitable inner diameter to allow for efficient fuel flow and consider the temperature range to which the line will be exposed.
Routing fuel lines should be done with care to avoid any sharp bends or kinks, as these can restrict fuel flow. Keep the lines as straight as possible and allow for some slack to accommodate engine movement. It's recommended to use fuel line clips or ties to secure the lines and prevent any interference with other engine components.
Start by cleaning the carburetor's fuel inlet and the fuel line's end with a solvent to remove any dirt or debris. Then, use a fuel line ferrule or clamp to secure the fuel line to the carburetor. Ensure a snug fit by tightening the ferrule or clamp firmly, but be careful not to overtighten, as it may damage the fuel line.
Yes, you'll need a few essential tools for the job. A fuel line cutter or a pair of sharp scissors will help you trim the fuel line to the desired length. A fuel line crimping tool or a pair of pliers can be used to attach the fuel line to the carburetor securely. Additionally, have a fuel line cleaner or solvent to ensure a clean connection.