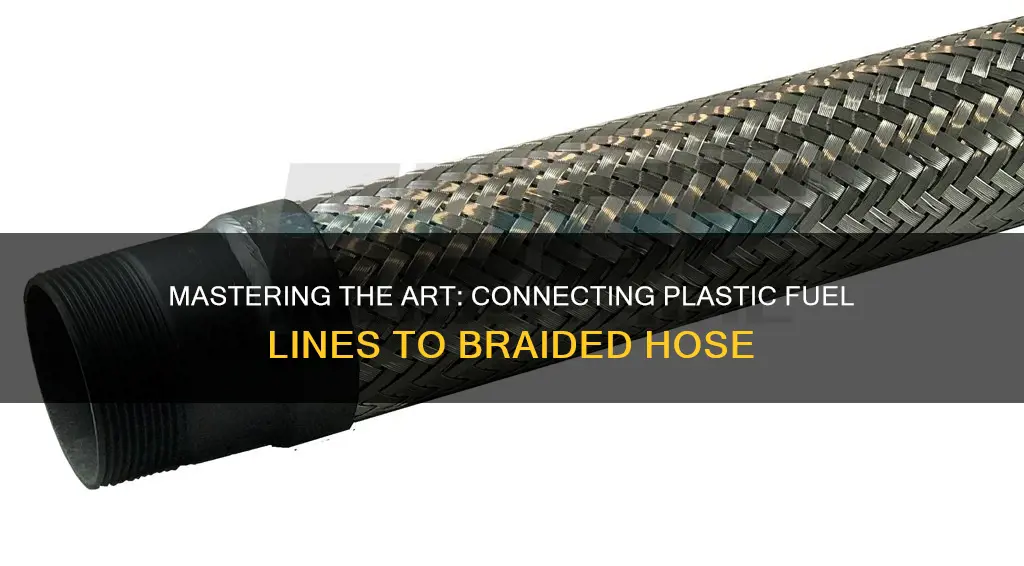
Connecting a plastic fuel line to a braided hose is a common task in automotive maintenance, especially when dealing with fuel systems. This process requires careful preparation and the right tools to ensure a secure and leak-free connection. The braided hose, known for its flexibility and durability, is often used in fuel lines due to its ability to withstand high pressure and temperature changes. When connecting these two components, it's essential to follow a step-by-step guide to ensure a proper seal. This involves cleaning the surfaces, using the appropriate adhesive or primer, and applying the correct amount of force to create a tight bond. By following these instructions, you can effectively join the plastic fuel line to the braided hose, ensuring optimal performance and safety in your vehicle's fuel system.
Characteristics | Values |
---|---|
Material | Plastic, Braided |
Connection Type | Clamping, Crimping, Fitting |
Compatibility | Fuel Lines, Engines |
Durability | Resistant to fuel, heat, and UV rays |
Flexibility | Allows for easy bending and routing |
Installation | Simple and straightforward |
Cost | Affordable |
Maintenance | Low maintenance required |
Safety | Reduces the risk of fuel leaks |
Environmental Impact | Environmentally friendly |
What You'll Learn
- Preparation: Clean and inspect both ends of the fuel line and braided hose
- Clamping: Use a suitable clamp to secure the connection, ensuring a tight fit
- Alignment: Align the fuel line and hose, ensuring they are straight and not kinked
- Bending: Gently bend the braided hose to match the fuel line's route
- Testing: Check for leaks and ensure the connection is secure before use
Preparation: Clean and inspect both ends of the fuel line and braided hose
Before attempting to connect the plastic fuel line to the braided hose, it is crucial to ensure a proper and secure attachment. The preparation process begins with meticulous cleaning and inspection of both ends of the fuel line and the braided hose. This step is essential to guarantee a tight and leak-free connection.
Start by thoroughly cleaning the ends of the fuel line. Over time, fuel lines can accumulate dirt, grease, and debris, which can interfere with the connection process. Use a mild detergent or fuel line cleaner to remove any contaminants. Rinse the fuel line thoroughly with water to ensure no residue remains. Pay attention to the threads or fittings at the ends, as these areas may require extra cleaning to ensure a proper seal.
Next, inspect the braided hose for any signs of damage or wear. Braided hoses can be susceptible to cracks, tears, or kinks, especially if they have been exposed to harsh conditions. Check for any visible damage, such as frayed edges or holes. If you notice any issues, it is best to replace the braided hose to ensure a reliable connection. Smooth out any creases or bends in the hose to ensure a straight and uniform surface for the connection.
When inspecting the fuel line, look for any bends, kinks, or cracks. Ensure that the fuel line is flexible and free from any obstructions. Check the fittings and connections for tightness and corrosion. If you find any issues, address them before proceeding. For example, if a fitting is loose, tighten it securely, and if there is corrosion, clean and lubricate the threads to ensure a proper seal.
By taking the time to clean and inspect the fuel line and braided hose, you are setting the foundation for a successful connection. This preparation step is often overlooked but is critical to the overall performance and safety of the fuel system. It ensures that the connection is not only secure but also free from potential leaks, which could lead to costly repairs and safety hazards.
Taping a Fuel Line: A Quick Fix or a Recipe for Disaster?
You may want to see also
Clamping: Use a suitable clamp to secure the connection, ensuring a tight fit
When connecting a plastic fuel line to a braided hose, clamping is a crucial step to ensure a secure and leak-free connection. The process involves using a specialized clamp designed to fit the specific dimensions of the fuel line and braided hose. Here's a detailed guide on how to achieve a tight and reliable clamp:
Start by laying out the materials you'll need: the plastic fuel line, the braided hose, and the appropriate clamp. Ensure that the clamp is the right size for the diameter of your fuel line. Clamps come in various sizes, so it's essential to choose the one that matches your line's specifications. A common type of clamp used for this purpose is a "fuel line clamp" or a "braided hose clamp." These clamps typically feature a sturdy metal construction with a smooth interior to prevent damage to the hose.
Position the clamp around the connection point. Place the clamp over the braided hose, ensuring it covers the entire length of the hose where it connects to the fuel line. The clamp should be centered and positioned securely, providing an even distribution of pressure. Use your hands or a pair of pliers to adjust the clamp, tightening it gently but firmly. The goal is to create a snug fit without applying excessive force, as this might damage the hose or fuel line.
To achieve a tight fit, you should hear a distinct 'click' or feel a noticeable resistance when tightening the clamp. This indicates that the clamp is secure and effectively sealing the connection. Ensure that the clamp is not twisted or misaligned, as this could compromise the integrity of the connection. A well-fitted clamp should have a smooth, continuous surface around the hose, with no sharp edges or protruding parts that could cause damage.
After clamping, inspect the connection thoroughly. Check for any signs of leakage by applying a small amount of pressure to the clamp and observing if any fuel escapes. Additionally, ensure that the clamp is not too tight, causing the hose to crimp or the fuel line to kink. The connection should feel secure and stable, providing confidence in the system's reliability.
Remember, the key to a successful connection is using the right clamp size and applying the appropriate amount of force. This ensures a tight, leak-free seal, promoting the efficient and safe operation of your fuel system.
Cub Cadet Fuel Line: Size Guide for Optimal Performance
You may want to see also
Alignment: Align the fuel line and hose, ensuring they are straight and not kinked
When connecting a plastic fuel line to a braided hose, proper alignment is crucial to ensure a secure and leak-free connection. Here's a detailed guide on how to achieve this:
Start by laying out the fuel line and the braided hose on a flat surface. Ensure that both components are straight and free from any bends or kinks. The goal is to create a smooth and continuous path for the fuel line to follow. Inspect the hoses for any damage or wear, especially at the connection points, and ensure they are in good condition.
Begin by positioning the fuel line along the length of the braided hose. The fuel line should be aligned in a way that allows for a smooth transition from one end of the hose to the other. It's important to maintain a consistent and straight path, avoiding any sharp bends that could restrict fuel flow or cause damage over time. Use your hands or a gentle tool to carefully guide the fuel line into the desired position.
Take your time to ensure the alignment is precise. You can use a straight edge or a ruler to verify that the fuel line is straight and parallel to the hose. If any adjustments are needed, gently manipulate the fuel line to achieve the correct alignment. Remember, the goal is to create a seamless connection where the fuel line and hose work together without any obstructions.
Once you're satisfied with the alignment, secure the connection. You can use hose clamps or specialized connectors designed for fuel lines and braided hoses. Ensure that the clamps or connectors are tightened securely but carefully, as excessive force can damage the hose. The connection should be tight enough to prevent any movement or leakage but not so tight that it causes crimping or damage to the hose.
By following these steps and paying close attention to alignment, you can create a robust and reliable connection between the plastic fuel line and the braided hose, ensuring optimal fuel delivery and performance.
Black Fuel Line: Is It Superior to Yellow?
You may want to see also
Bending: Gently bend the braided hose to match the fuel line's route
When connecting a plastic fuel line to a braided hose, one crucial step is bending the braided hose to match the fuel line's route. This process requires careful consideration and a gentle approach to ensure a secure and leak-free connection. Here's a detailed guide on how to achieve this:
Start by carefully examining the fuel line's path and identifying the specific areas where the braided hose needs to be bent. Take note of any sharp turns, angles, or obstacles the fuel line encounters. Understanding the layout will help you plan the bending process effectively. It's essential to work with the braided hose while it's still in its original coiled state, as this will make it easier to manipulate and bend without kinking or damaging the hose.
Gently grasp the braided hose with your hands and begin to bend it along the fuel line's route. Use smooth, controlled movements to avoid putting excessive pressure on the hose. The goal is to create a seamless transition between the braided hose and the fuel line. Take your time and be patient, as rushing the process might lead to mistakes or damage to the hose. Aim for a smooth, continuous curve that follows the natural flow of the fuel line.
As you bend the hose, ensure that the braiding remains intact and doesn't get caught or pinched. The braiding should allow for flexibility and movement, so be mindful of any tight bends that might restrict the hose's functionality. If you encounter a particularly challenging section, consider using a hose bending tool, which can provide the necessary leverage without causing damage.
Once you've successfully bent the braided hose to match the fuel line's route, inspect the connection thoroughly. Check for any sharp bends or kinks that might compromise the hose's performance. Ensure that the hose is securely attached to the fuel line without any gaps or loose connections. If everything looks good, you can proceed with the final steps of the installation process, confident that your connection is both functional and durable.
Fuel Line Repair: Quick Fix with Compression Fittings
You may want to see also
Testing: Check for leaks and ensure the connection is secure before use
When connecting a plastic fuel line to a braided hose, it's crucial to ensure a secure and leak-free connection to prevent any potential hazards. Here's a step-by-step guide on how to test and verify the integrity of the connection:
Preparation: Before beginning, ensure you have the necessary tools, including a fuel line connector kit, which typically includes various sizes of adapters and fittings. Also, have a suitable cleaning agent, such as a fuel line cleaner, to prepare the surfaces for a secure bond.
Assembly: Start by cleaning the ends of both the plastic fuel line and the braided hose. Use the cleaner to remove any dirt, grease, or debris that could interfere with the connection. Rinse the areas thoroughly and allow them to dry completely. Then, carefully insert the male end of the fuel line into the female connector, ensuring it is aligned properly. Apply thread seal tape or a suitable adhesive tape around the threads to create a secure bond. Tighten the connector by hand, then use a wrench to ensure it is tightened securely, following the manufacturer's specifications.
Leak Test: The critical step is to perform a leak test to ensure there are no gaps or imperfections in the connection. Fill the fuel line with a small amount of fuel or a non-toxic, fuel-safe test fluid. You can use a simple syringe for this purpose. Then, gently apply pressure to the connection and observe for any signs of leakage. Check all around the connection, including the threads and the braided hose. If you notice any seepage, it indicates a potential issue, and you should re-evaluate the connection.
Security Check: After the leak test, inspect the connection for any visible signs of damage or wear. Ensure that the threads are not stripped or damaged, as this could compromise the seal. Also, check that the braided hose is not kinked or pinched, as this might affect the flow and pressure. If everything appears secure, you can proceed with using the system.
Final Inspection: Before putting the system into service, perform a final visual inspection. Check for any visible signs of damage or deformation that might have occurred during the installation process. Ensure that all connections are tight and secure. This thorough testing process will help guarantee a safe and efficient fuel line connection.
Ethanol's Role in Diesel Fuel: A Comprehensive Overview
You may want to see also
Frequently asked questions
Connecting a plastic fuel line to a braided hose requires a few steps to ensure a secure and leak-free attachment. First, ensure both components are clean and free of any debris. Then, use a fuel line adapter or a barbed fitting that matches the inner diameter of the braided hose. Insert the fuel line into the adapter or fitting, and use a suitable adhesive or tape to secure it in place. Finally, wrap the connection with a layer of protective tape or hose wrap to provide additional insulation and prevent any potential leaks.
While a regular hose clamp might seem like a quick fix, it is not the most reliable method for connecting a plastic fuel line to a braided hose. Hose clamps can create excessive pressure and potentially damage the fuel line or hose over time. Instead, consider using a specialized fuel line clamp or a ferrule that is designed to provide a tight, yet gentle, grip without causing any harm to the components.
Achieving a tight connection without crushing the braided hose is crucial. Start by ensuring the hose is straight and not coiled. Then, use a fuel line clamp or ferrule that is slightly larger than the inner diameter of the hose. Wrap the clamp or ferrule around the hose, making sure it is centered and not twisted. Apply firm pressure to secure the connection, but be careful not to apply too much force that could damage the hose.
When it comes to adhesives for fuel line connections, it's best to use a product specifically designed for fuel line installations. These adhesives are typically solvent-based and provide excellent bonding strength. Apply a small amount of adhesive to the fuel line and the adapter/fitting, following the manufacturer's instructions. Allow it to dry completely before making the connection. This ensures a strong bond between the plastic fuel line and the braided hose.
Yes, there are a few pitfalls to watch out for. Firstly, avoid using excessive force when attaching the fuel line, as it may lead to damage or cracking. Secondly, ensure the connection is not twisted, as this can cause leaks. Additionally, never use a clamp that is too small, as it may not provide adequate grip. Lastly, always inspect the connection regularly for any signs of wear or damage, especially if the vehicle is used in harsh conditions.