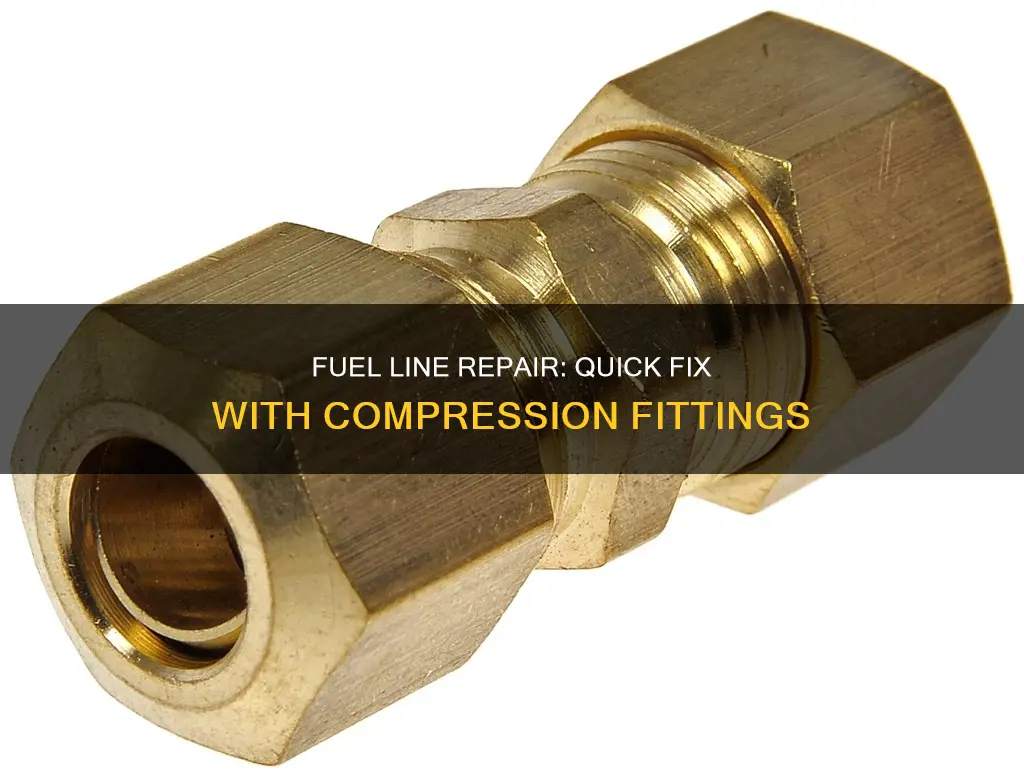
Fuel lines are essential components of a vehicle's fuel system, and over time, they can develop leaks or become damaged. Repairing a fuel line with a compression fitting is a practical solution to restore the integrity of the fuel system. This method involves using a compression fitting to seal the damaged area, ensuring a secure and reliable connection. By following a step-by-step process, you can effectively repair the fuel line, preventing fuel leaks and maintaining the vehicle's performance. This guide will provide a comprehensive overview of the process, ensuring a successful and long-lasting repair.
What You'll Learn
- Prepare the Fuel Line: Clean and inspect the line, ensuring it's free of debris and damage
- Choose the Right Fitting: Select a compression fitting compatible with fuel line material
- Connect the Fitting: Tighten the fitting securely, following manufacturer instructions
- Test for Leaks: Use a fuel line tester to check for any leaks at the connection
- Secure the Connection: Use clamps or tape to reinforce the fitting and prevent leaks
Prepare the Fuel Line: Clean and inspect the line, ensuring it's free of debris and damage
Before attempting to repair a fuel line with a compression fitting, it's crucial to thoroughly prepare the fuel line to ensure a successful and safe repair. Start by locating the fuel line that needs attention and inspect it carefully. Look for any signs of damage, such as cracks, punctures, or corrosion. Also, check for debris or obstructions that might have accumulated inside the line. This initial inspection will help you understand the extent of the issue and guide your next steps.
If you find any debris or small objects within the fuel line, it's essential to remove them carefully. You can use a small brush or a thin tool to gently dislodge and extract these foreign particles. Ensure that you don't apply excessive force to avoid damaging the fuel line further. Once you've cleared the debris, rinse the fuel line with a suitable cleaning agent to eliminate any remaining contaminants. This step is vital to ensure that the repair is effective and to prevent future issues.
For a more thorough cleaning, consider using a fuel line cleaner, which is specifically designed to remove built-up deposits and grime. Follow the instructions provided with the cleaner to ensure safe and effective use. After cleaning, thoroughly rinse the fuel line to remove any residual cleaning agents. This process will help you start fresh and ensure that the repair is not compromised by any leftover contaminants.
While cleaning, pay close attention to any areas where the fuel line connects to other components, such as the fuel pump or the engine. These connections should be checked for tightness and any signs of leakage. If you notice any issues, address them before proceeding with the repair. Ensuring that all connections are secure and leak-free is a critical part of the preparation process.
Once the fuel line is clean and free of debris, inspect it again to confirm that it is in good condition. Check for any remaining signs of damage or wear. If the fuel line shows significant deterioration, it might be necessary to consider replacing it instead of just repairing it. This decision will depend on the severity of the damage and the overall condition of the fuel system.
Understanding Fuel Line Sizes: A 250x44 Fuel Line Explained
You may want to see also
Choose the Right Fitting: Select a compression fitting compatible with fuel line material
When repairing a fuel line with a compression fitting, it's crucial to choose the right fitting to ensure a secure and reliable connection. The compatibility of the fitting with the fuel line material is a critical factor in the success of the repair. Here's a step-by-step guide to selecting the appropriate compression fitting:
Identify the Fuel Line Material: Start by identifying the material of your fuel line. Common materials include rubber, vinyl, or synthetic compounds. Different materials may require specific types of compression fittings to ensure a proper seal. For example, rubber fuel lines often use compression fittings with a rubber or synthetic sleeve to create a tight connection.
Research Fitting Compatibility: Once you know the fuel line material, research the compatible compression fittings. Manufacturers often provide detailed specifications and compatibility charts for their fittings. Look for fittings designed explicitly for the fuel line material you have. These fittings will typically have a specific sleeve or gasket made from a compatible material to ensure a secure seal.
Consider Size and Thread Type: Compression fittings come in various sizes and thread types. Ensure you select a fitting with the correct thread size that matches your fuel line. Measure the fuel line's inner diameter and compare it to the fitting's specifications to find a suitable match. Additionally, check if the fitting has the appropriate compression ratio to provide a tight seal.
Inspect the Fitting's Quality: Pay attention to the quality and construction of the compression fitting. High-quality fittings will have precise tolerances and robust materials to ensure a reliable connection. Look for fittings with a durable sleeve or gasket that can withstand fuel pressure and temperature variations. Avoid fittings with visible defects or those that appear worn out, as they may not provide an adequate seal.
By carefully selecting a compression fitting that is compatible with your fuel line material, you can ensure a successful repair, minimizing the risk of fuel leaks and maintaining the integrity of your fuel system. Remember to consult manufacturer guidelines and specifications to make an informed decision.
Fuel Line Removal Guide: 2008 RMZ450
You may want to see also
Connect the Fitting: Tighten the fitting securely, following manufacturer instructions
When connecting a compression fitting to a fuel line, it's crucial to ensure a tight and secure bond to prevent any leaks. Here's a step-by-step guide on how to achieve this:
Start by ensuring you have the right tools and materials. You'll need a wrench or a pair of pliers that can provide a firm grip on the compression fitting. It's essential to use the correct size to avoid over-tightening, which can damage the fitting or the fuel line. Gather the manufacturer's instructions specific to your fitting, as different brands may have unique requirements.
Position the compression fitting over the fuel line section you want to connect. Align the threads or the compression surface of the fitting with the fuel line. This process may require some maneuvering to ensure a proper connection. Once aligned, begin tightening the fitting by hand. This initial tightening helps to position the fitting correctly and ensures an even distribution of force when you start using the wrench.
Now, it's time to apply the force. Take your wrench and tighten the fitting further. Follow the manufacturer's guidelines for the recommended torque or tightness. Over-tightening can cause damage, so be cautious and use controlled pressure. The goal is to achieve a secure bond without applying excessive force. You should feel the fitting engage with the fuel line, and it should become increasingly difficult to turn by hand.
After reaching the specified tightness, it's essential to double-check your work. Remove the wrench and test the connection by gently trying to loosen the fitting. If it doesn't budge, you've successfully tightened it securely. However, if there's any play or looseness, you may need to apply more force or check for any obstructions that might be preventing a tight connection.
Remember, taking your time and following the manufacturer's instructions will ensure a reliable repair. Always prioritize safety and proper technique when working with fuel lines to avoid any potential hazards.
Understanding Fuel Lines: A1 vs. B1 Differences Explained
You may want to see also
Test for Leaks: Use a fuel line tester to check for any leaks at the connection
When repairing a fuel line with a compression fitting, it's crucial to ensure that the connection is secure and leak-free. One of the most effective ways to verify this is by using a fuel line tester, a specialized tool designed to detect even the smallest leaks. Here's a step-by-step guide on how to use a fuel line tester for this purpose:
Preparation: Before you begin, ensure that the fuel line is completely dry and free of any debris. If the line is still attached to the engine, disconnect it carefully to access the fitting. It's also a good idea to wear protective gear, such as gloves and safety goggles, to prevent any potential splashes or spills.
Step 1: Apply the Tester: Start by applying the fuel line tester to the connection where the compression fitting is located. The tester typically has a small, flexible tube with a nozzle at the end. Insert the nozzle into the fitting and ensure it is properly seated. The tester may use a chemical indicator or a pressure sensor to detect leaks.
Step 2: Introduce the Tester Fluid: Depending on the type of tester you're using, you might need to introduce a special fluid or a small amount of air. Follow the manufacturer's instructions for this step. The fluid or air will help identify any potential leaks by changing color or causing a pressure drop.
Step 3: Observe for Leaks: After applying the tester, carefully observe the connection area. If a chemical indicator is used, look for any color changes that indicate a leak. If a pressure sensor is employed, watch for any sudden drops in pressure, which could signify a breach in the system. Even the tiniest leak can be detected by these methods.
Step 4: Interpret Results: If no leaks are detected, you can proceed with the repair, confident that the connection is secure. However, if a leak is identified, you may need to tighten the fitting further or inspect the fuel line for any damage. In such cases, it's essential to address the issue promptly to prevent potential engine problems.
By following these steps and using a fuel line tester, you can effectively test for leaks at the connection, ensuring a successful repair. This method is a reliable way to verify the integrity of the fuel line and compression fitting, providing peace of mind for any vehicle owner.
Fuel Line Clog Symptoms: Engine Issues Revealed
You may want to see also
Secure the Connection: Use clamps or tape to reinforce the fitting and prevent leaks
When repairing a fuel line with a compression fitting, ensuring a secure and leak-free connection is crucial to prevent fuel leaks and potential engine damage. One effective method to achieve this is by using clamps or tape to reinforce the fitting. Here's a step-by-step guide on how to secure the connection:
Start by ensuring you have the right tools and materials. You'll need a suitable clamp or tape specifically designed for fuel line repairs. Clamps are often preferred as they provide a more secure and adjustable hold. Choose a clamp that matches the size of your fuel line and compression fitting. Alternatively, you can use electrical tape or duct tape, but specialized fuel line tape or clamp kits are generally more reliable for this purpose.
Next, locate the compression fitting on the fuel line. Ensure the fitting is clean and free of any debris or old tape. If there's any old tape or residue, carefully remove it to create a clean surface for the new reinforcement.
Now, apply the chosen reinforcement. For clamps, position the clamp around the compression fitting, ensuring it is centered and securely fits the fuel line. Tighten the clamp by hand, then use a wrench to apply firm pressure and secure it in place. Make sure the clamp is tight enough to hold the fitting securely but not so tight that it causes damage to the fuel line.
If you're using tape, wrap it tightly around the compression fitting, ensuring full coverage. Start from one end of the fitting and work your way around, overlapping the tape slightly with each wrap. Continue until the entire fitting is covered, creating a secure barrier against leaks.
Finally, test the connection by applying pressure to the reinforced area and checking for any leaks. If no leaks are detected, your repair is successful. Remember, regular maintenance and inspections are essential to ensure the longevity of your fuel system.
Fuel Tank Liner: Top Sources for Northern Purchases
You may want to see also
Frequently asked questions
A compression fitting is a type of coupling used to join two or more pipes or hoses together. It works by compressing the fitting onto the fuel line, creating a tight seal. This method is commonly used for fuel lines due to its reliability and ability to withstand high pressure.
Before installing a compression fitting, ensure the fuel line is clean and free of any debris or contaminants. Use a hose brush or a similar tool to scrub the line, removing any old fittings or deposits. Also, check the fitting for any damage or wear and ensure it is the correct size for your fuel line.
You will need a few essential tools for this task. A pair of adjustable pliers or a fuel line tool is crucial for gripping and turning the fitting. Additionally, a fuel line cutter or a pipe cutter will help you trim the fuel line to the desired length. It's also recommended to have a fuel line primer and solvent to ensure a secure connection.
It is generally not recommended to reuse old compression fittings, especially if they show signs of wear or damage. Over time, fittings can become brittle or develop cracks, compromising their sealing ability. It's best to replace them with new fittings to ensure a reliable and safe fuel line connection.
One common problem is an improper fit, where the fitting doesn't compress onto the fuel line tightly enough. This can be caused by using the wrong size fitting or not applying enough force. Another issue is contamination, where dirt or debris gets into the connection, leading to a poor seal. Always ensure a clean and dry environment during installation.