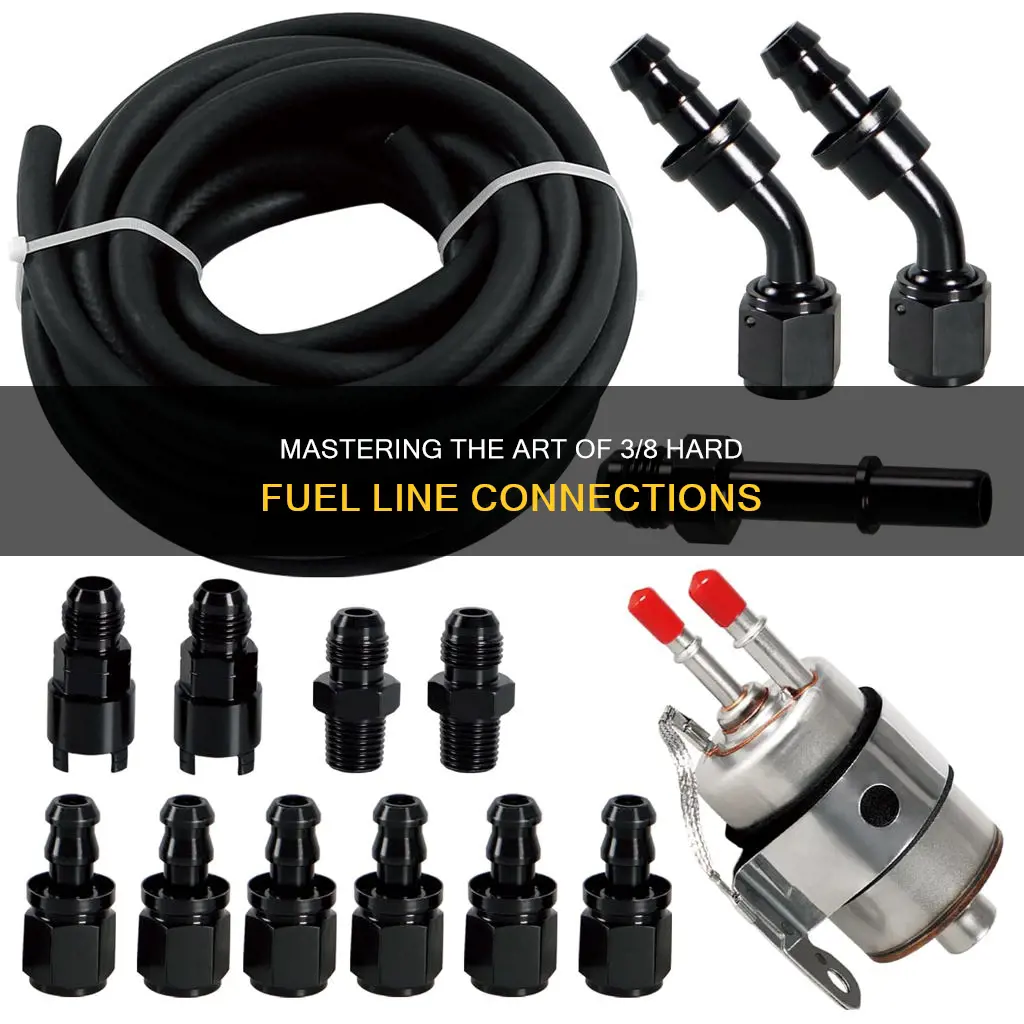
Connecting a 3/8 hard fuel line to an engine or fuel system can be a straightforward process if you follow the right steps. This guide will provide a step-by-step approach to ensure a secure and leak-free connection. You'll need the appropriate tools, such as fuel line connectors, and a basic understanding of fuel system components. The process involves cleaning the surfaces, inserting the fuel line into the connector, and using the right amount of fuel line adhesive to ensure a tight seal. With the right preparation and technique, you can successfully connect the fuel line and ensure your engine receives the necessary fuel efficiently.
What You'll Learn
- Preparation: Ensure you have the right tools and a clean workspace
- Fuel Line Routing: Route the line away from heat sources and sharp edges
- Connection Types: Choose the appropriate connection method for your engine
- Tightening Procedures: Follow manufacturer guidelines for torque and tightening sequence
- Leak Testing: Use a pressure gauge to check for leaks after installation
Preparation: Ensure you have the right tools and a clean workspace
Before you begin the process of connecting a 3/8-inch hard fuel line, it's crucial to prepare the necessary tools and ensure your workspace is clean and organized. This initial step is often overlooked but is essential for a smooth and efficient project. Here's a detailed guide on how to get ready:
Gather the Tools:
- The primary tool you'll need is a fuel line connector kit, which typically includes various sizes of fittings and adapters. Look for a kit that includes a 3/8-inch fitting suitable for your application.
- Get a pair of adjustable pliers and a set of pipe wrenches in different sizes. These will be used for tightening the fittings securely.
- Consider using a fuel line cutter or a sharp knife to ensure precise cuts. This tool will help you trim the fuel line to the desired length.
- Have a supply of clean rags or cloth ready for wiping down surfaces and cleaning up any spills.
- Safety equipment is a must; wear gloves to protect your hands, and consider safety goggles to shield your eyes from any potential debris or splashes.
Prepare Your Workspace:
- Find a well-lit area with a flat surface where you can lay out your tools and components. A clean, clutter-free workspace will make the process more manageable and safer.
- Ensure you have a stable workbench or a sturdy table where you can place the fuel line and fittings.
- If you're working in a confined space, consider using a work light to illuminate the area, making it easier to see the connections.
- Keep a trash bin nearby to dispose of any waste materials, ensuring a clean and organized environment.
Cleanliness is Key:
- A clean workspace is essential for a professional-looking installation. Wipe down any surfaces that will come into contact with the fuel line to remove dust, dirt, or debris.
- Check for any existing fuel lines or connections in the area and ensure they are secure and free from leaks.
- If you're working in a garage or outdoor space, cover any sensitive areas to prevent fuel line debris from falling into them.
- Ensure proper ventilation in the workspace to avoid inhaling any fumes, especially if you're working with fuel-related components.
By taking the time to prepare and organize your tools and workspace, you'll set the foundation for a successful fuel line connection. This preparation phase is often the most critical step, ensuring that the rest of the process runs smoothly and efficiently.
Mastering the Art of Splice: Nylon Fuel Line Repair Guide
You may want to see also
Fuel Line Routing: Route the line away from heat sources and sharp edges
When connecting a 3/8" hard fuel line to an engine or any other fuel system, proper routing is crucial to ensure optimal performance and longevity. One of the most important considerations is to route the fuel line away from heat sources and sharp edges to prevent damage and potential fuel leaks. Here's a detailed guide on how to achieve this:
Start by identifying the potential heat sources and sharp objects in the vicinity of the fuel line's path. This could include engine components, exhaust systems, hot pipes, or even sharp corners and edges of the vehicle's body. The goal is to create a clear and safe route for the fuel line, ensuring it doesn't come into contact with these hazards. Use protective sleeves or conduits to shield the fuel line from direct exposure to heat. This is especially important in areas where the fuel line passes close to hot surfaces, such as the engine block or exhaust manifold. Consider the material of the protective covering; it should be durable and capable of withstanding the temperatures involved.
As you route the fuel line, maintain a consistent and straight path whenever possible. Sharp bends and kinks can lead to fuel line damage and reduced flow efficiency. Aim for gentle curves and use flexible fuel line materials that can accommodate slight bends without compromising structural integrity. In areas where the fuel line must cross other components, ensure there is sufficient clearance to prevent rubbing or interference. This is crucial to avoid wear and tear on the fuel line and potential fuel leaks.
Pay close attention to the connection points and fittings. When joining the 3/8" hard fuel line to the engine or other components, ensure that the fittings are securely tightened to prevent any fuel leaks. Use the appropriate tools and torque specifications provided by the manufacturer to ensure a tight and reliable connection. Additionally, consider using fuel line connectors or fittings that offer a secure and leak-resistant seal.
By following these routing guidelines, you can ensure that the 3/8" hard fuel line is safely and efficiently connected to the fuel system, minimizing the risk of damage and maintaining optimal fuel delivery to the engine. Remember, proper routing is a critical aspect of fuel system maintenance and can contribute to the overall reliability and performance of your vehicle.
Fuel Line Size for 1970 Honda 90: A Guide
You may want to see also
Connection Types: Choose the appropriate connection method for your engine
When connecting a 3/8" hard fuel line to an engine, it's crucial to select the right connection type to ensure a secure and efficient fuel supply. The choice depends on various factors, including the engine's design, the fuel pressure, and the specific application. Here's a breakdown of the common connection types and their considerations:
- Quick-Connect Fittings: These are widely used due to their ease of installation and removal. Quick-connect fittings typically consist of a male thread on the fuel line and a female socket on the engine side. To connect, simply insert the fuel line into the socket, ensuring a snug fit. This method is convenient for tuning sessions or when frequent adjustments are required. However, it may not provide the tightest seal compared to other methods, so it's essential to use high-quality fittings to minimize fuel leakage.
- Threaded Connections: This traditional method involves threading the fuel line onto a corresponding port on the engine. It offers a secure and reliable connection, especially for high-pressure applications. Threaded connections are often preferred for permanent installations or when a more robust seal is needed. When using this method, ensure that the threads are clean and free of debris, and apply the correct amount of thread sealant to prevent leaks.
- Clamp-Style Connections: These connections use a clamp to secure the fuel line to the engine. They are simple to install and provide a good level of flexibility. Clamp-style connections are ideal for situations where the fuel line needs to be adjusted or moved. Make sure to use the appropriate size clamp for the fuel line diameter and ensure it is tightened securely without causing damage to the line.
- Union Connections: Unions offer versatility and ease of maintenance. They consist of a male thread on one end and a female thread on the other, with a union nut in the middle. By loosening the union nut, you can separate the fuel line, making it convenient for cleaning or replacing sections. This method is particularly useful when working with longer fuel lines or in applications where access to the fuel system may be limited.
When selecting a connection type, consider the engine's fuel requirements, the desired ease of maintenance, and the overall installation process. It's essential to follow manufacturer guidelines and use the appropriate tools to ensure a proper connection. Regularly inspecting and maintaining the fuel line connections will contribute to the longevity and reliability of your engine's performance.
Fuel Line Costs: A Breakdown of Expenses
You may want to see also
Tightening Procedures: Follow manufacturer guidelines for torque and tightening sequence
When connecting a 3/8" hard fuel line to an engine or component, it's crucial to follow the manufacturer's guidelines for tightening procedures to ensure a secure and reliable connection. These guidelines are designed to provide the optimal torque and sequence for tightening, which can vary depending on the specific application and design of the fuel line and its fittings.
The first step is to gather the necessary tools and equipment, including the appropriate torque wrench, which is essential for measuring the tightening force accurately. It's important to use a torque wrench that matches the required torque range for the specific application. Manufacturers often provide torque specifications in their installation manuals or on the fuel line itself.
Once you have the correct tools, locate the fuel line fittings and identify the specific torque and sequence requirements. These details are critical to ensure that the connection is neither overtightened, which can cause damage, nor undertightened, which can lead to leaks. Manufacturers typically provide these instructions to ensure the product's longevity and performance.
Proceed with the tightening process, applying the specified torque in a controlled manner. It is recommended to use a methodical approach, tightening each fitting in a sequential order as per the manufacturer's instructions. This ensures that the force is distributed evenly across the connection points, reducing the risk of damage to the fuel line or fittings.
After tightening, it's essential to inspect the connections for any signs of leakage or damage. Check for any visible cracks, bends, or deformations in the fuel line, and ensure that all fittings are secure and properly aligned. If any issues are identified, the connections should be tightened further or adjusted as per the manufacturer's recommendations. Following these procedures will help ensure a safe and efficient fuel system.
Fuel Flow: Inner Diameter's Impact on Carburetor Performance
You may want to see also
Leak Testing: Use a pressure gauge to check for leaks after installation
After connecting the 3/8-inch hard fuel line to your engine or fuel system, it's crucial to perform a thorough leak test to ensure there are no hidden issues. This step is often overlooked, but it's an essential part of the installation process to guarantee a safe and efficient fuel delivery system. Here's a detailed guide on how to conduct this test using a pressure gauge:
Preparation: Before you begin, ensure you have the necessary tools, including a pressure gauge, a source of compressed air or an air compressor, and some cleaning supplies. It's also a good idea to have some rags or paper towels ready to wipe down the connections. Make sure the fuel line is properly secured and all connections are tight to avoid any potential leaks during the test.
Step-by-Step Process: Start by applying a small amount of thread seal tape or pipe compound to the male and female ends of the fuel line connections. This extra layer of protection can help prevent leaks. Then, connect the fuel line to the pressure gauge, ensuring a secure and tight fit. The gauge should be set to read a specific pressure, typically the system's operating pressure, which can be found in your vehicle's manual. Turn on the air compressor and slowly apply pressure to the fuel line. Listen for any hissing sounds or feel for any signs of leakage around the connections. If you detect any leaks, immediately release the pressure and tighten the connections further.
Checking for Leaks: As you apply pressure, inspect the entire length of the fuel line, paying close attention to the connections. Look for any wet spots or signs of fuel seeping out. Even a small leak can lead to significant issues over time, so it's crucial to address any problems immediately. If you find a leak, you might need to re-tighten the connection or consider using a different type of connector or adhesive.
Pressure Release and Final Check: After ensuring there are no leaks, release the pressure from the gauge and double-check all connections. Make sure the fuel line is secure and that there are no visible signs of damage or wear. This final inspection is essential to catch any potential issues that might have arisen during the installation process.
By following these steps, you can effectively test the fuel line connections for leaks and ensure a reliable fuel supply to your engine. Remember, proper leak testing is a critical aspect of vehicle maintenance and can help prevent costly repairs and potential safety hazards.
Mastering Rubber Fuel Line Maintenance: A Step-by-Step Guide
You may want to see also