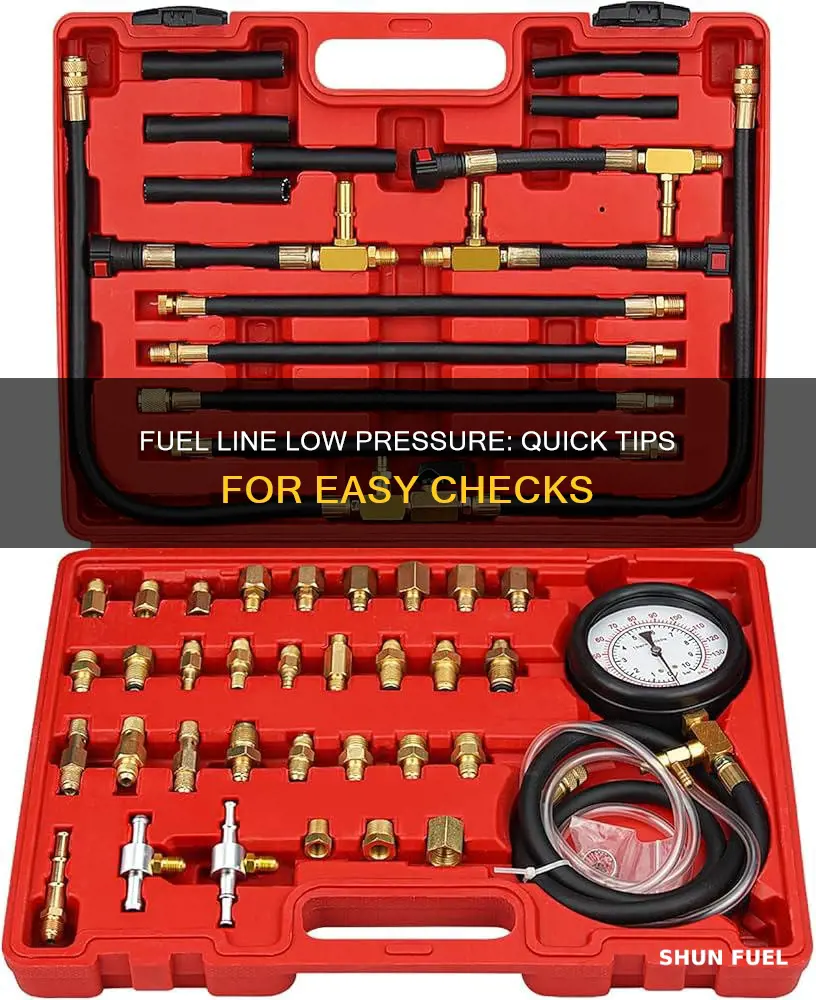
Checking for low pressure in a fuel line is an important maintenance task for vehicle owners to ensure optimal engine performance and fuel efficiency. This process involves identifying potential issues with the fuel system, which can lead to engine misfires, poor fuel economy, or even engine failure if left unattended. By understanding how to check for low pressure, you can take proactive measures to address any problems and maintain your vehicle's reliability. This guide will provide a step-by-step approach to inspecting the fuel line for low pressure, offering valuable insights for both DIY enthusiasts and professional mechanics.
What You'll Learn
- Visual Inspection: Check for any visible damage, cracks, or leaks along the fuel line
- Pressure Gauge: Use a gauge to measure pressure at various points in the line
- Fuel Pump Test: Ensure the pump is functioning properly by testing its output
- Fuel Filter Check: Inspect the filter for clogs or debris that might restrict flow
- Engine Diagnostics: Use diagnostic tools to monitor engine performance and identify pressure issues
Visual Inspection: Check for any visible damage, cracks, or leaks along the fuel line
A visual inspection is a crucial step in identifying potential issues with your fuel line, especially when it comes to low pressure. This method allows you to quickly pinpoint visible damage, cracks, or leaks that might be causing the problem. Here's a detailed guide on how to perform this inspection:
Start by locating the fuel line, which is typically a black or dark-colored hose that runs from the fuel tank to the engine. Carefully examine the entire length of the fuel line for any signs of damage. Look for cuts, punctures, or tears in the hose material. Even small tears can lead to fuel leaks, which can cause significant engine issues. Inspect the connections between the fuel line and the fuel tank, as well as any fittings or clamps that secure the line to the engine. Ensure that these connections are tight and secure, as loose fittings can lead to fuel leaks.
Pay close attention to any visible cracks or brittleness in the fuel line. Over time, fuel lines can degrade due to heat, sunlight, and chemical exposure. Cracks or a brittle appearance may indicate that the fuel line is no longer capable of withstanding the pressure and temperature changes it experiences. In such cases, replacement is necessary to prevent fuel leaks and potential engine damage.
Additionally, check for any signs of corrosion or rust along the fuel line, especially if it is exposed to the elements. Corrosion can weaken the fuel line and lead to leaks. If you notice any corrosion, it's important to clean and protect the affected areas to prevent further deterioration.
During your visual inspection, also look for any signs of fuel leakage. Even a small leak can cause a dangerous buildup of fuel vapor, leading to potential fire hazards. If you notice any fuel dripping or pooling around the fuel line, it's a clear indication of a serious issue that requires immediate attention.
Remember, a thorough visual inspection is a simple yet effective way to identify low pressure issues in your fuel line. By regularly checking for visible damage, cracks, leaks, and other signs of deterioration, you can ensure the longevity and reliability of your engine's fuel system.
Honda Small Engine Fuel Line: Understanding the Fuel System
You may want to see also
Pressure Gauge: Use a gauge to measure pressure at various points in the line
Using a pressure gauge is a crucial step in identifying and addressing low pressure issues in a fuel line. This tool allows you to measure the pressure at different points along the line, helping you pinpoint the exact location of the problem. Here's a step-by-step guide on how to effectively use a pressure gauge for this purpose:
Preparation: Before you begin, ensure you have the necessary tools and equipment. You'll need a pressure gauge specifically designed for fuel lines, which typically has a range suitable for measuring fuel pressure. It's important to choose a gauge with a suitable scale, often indicated in pounds per square inch (PSI) or bars. Additionally, you'll require a fuel line disconnect tool to safely access the fuel line without causing any damage.
Locate the Fuel Line: Start by locating the fuel line that you suspect might have low pressure. This line typically runs from the fuel tank to the engine, often near the fuel pump. It's essential to identify the correct line to ensure accurate measurements.
Connect the Pressure Gauge: Once you've located the fuel line, use the disconnect tool to safely remove any obstructions or attachments. Then, carefully connect the pressure gauge to the fuel line. Ensure a tight and secure connection to avoid any leaks. The gauge should be positioned in a way that allows for easy reading of the pressure.
Measure Pressure: With the gauge connected, you can now measure the pressure. Start by reading the initial pressure, which should be close to the expected value for a healthy fuel system. If the pressure is significantly lower than expected, it indicates a potential issue. Take multiple readings at different points along the fuel line to identify any variations or drops in pressure. This process helps isolate the problem area.
Interpret Results: After taking pressure readings, analyze the data. Look for consistent low pressure readings at specific points, as this could indicate a blockage, a faulty fuel pump, or a damaged fuel line. If the pressure drops significantly from one point to another, it may suggest a restriction or leak in that particular section. This information is vital in diagnosing the cause of low pressure.
Troubleshooting: Based on your pressure gauge readings, you can now take targeted actions to resolve the issue. If a specific section of the fuel line has consistently low pressure, you may need to inspect that area for damage or blockages. Consider using a fuel line cleaner or replacing damaged sections. Consulting the vehicle's manual or seeking professional advice can provide further guidance tailored to your specific make and model.
Can Transmission Oil Cooler Line Be Used for Fuel Line?
You may want to see also
Fuel Pump Test: Ensure the pump is functioning properly by testing its output
To ensure your fuel pump is functioning properly and delivering the correct pressure to your engine, a simple yet effective test can be performed. This test involves measuring the pump's output pressure and comparing it to the expected value. Here's a step-by-step guide on how to conduct this test:
First, locate the fuel pump, which is typically positioned near the fuel tank. It is often a small, electric motor-driven pump. You might need to remove some panels or access panels to get to it, depending on your vehicle's make and model. Once you have access to the pump, you'll need a fuel pressure gauge. This gauge measures the pressure in the fuel line and provides an accurate reading. Ensure you have a gauge with a suitable range for your vehicle's fuel system.
Next, disconnect the negative battery cable to ensure the engine doesn't start unexpectedly during the test. This is an important safety precaution. Then, locate the fuel line that connects the pump to the engine. Carefully remove the fuel line from the pump, being mindful of any fuel that might spill. Attach the fuel pressure gauge to the fuel line, ensuring a secure connection. The gauge should have a clear view of the fuel flow to provide an accurate reading.
Now, start the engine and allow it to idle. With the engine running, you should see a steady pressure reading on the gauge. If the pressure is within the specified range for your vehicle, the pump is likely functioning correctly. However, if the pressure is significantly lower than expected, it could indicate a problem with the pump or the fuel line. In this case, further investigation is required to identify the issue.
If the pressure is too high, it might suggest a restriction in the fuel line or a malfunctioning pump. In such cases, you should consult a mechanic to ensure the fuel system is safe and properly functioning. This test is a valuable tool for diagnosing fuel pump issues and can help prevent potential problems with your vehicle's engine. Remember, regular maintenance and testing of the fuel system can contribute to the overall reliability and performance of your car.
The Ultimate Guide to Choosing the Best 1-2 Fuel Line
You may want to see also
Fuel Filter Check: Inspect the filter for clogs or debris that might restrict flow
Checking the fuel filter is a crucial step in ensuring your vehicle's engine runs efficiently and avoids potential issues related to fuel supply. Over time, fuel filters can become clogged with debris, dirt, and contaminants, which can restrict the flow of fuel to the engine. This restriction can lead to a variety of performance problems, such as reduced power, poor acceleration, and even engine stalls. Here's a detailed guide on how to inspect the fuel filter for clogs or debris:
Locate the Fuel Filter: The first step is to locate your vehicle's fuel filter. This component is typically found under the car, often near the engine or the fuel tank. It is usually a cylindrical or rectangular unit with a few connections: an inlet, an outlet, and sometimes a drain valve. Refer to your vehicle's manual if you're unsure of its exact location.
Remove the Fuel Filter: Once you've identified the filter, you'll need to remove it. This process may vary slightly depending on your vehicle's make and model. Generally, you'll need to drain the fuel system to prevent spills. Start by disconnecting the negative battery terminal (if applicable) and then locate the fuel pump fuse or relay to cut power to the fuel pump. After ensuring the fuel has been drained, carefully remove the filter by unscrewing or unclipping it from its mounting position.
Inspect the Filter: With the filter removed, you can now examine it for any signs of clogging or debris. Look for any visible dirt, rust, or contaminants that might have accumulated inside. Check the filter's exterior for any damage or signs of corrosion. If you notice any significant buildup or if the filter appears discolored, it's a strong indicator that it needs to be replaced.
Clean or Replace the Filter: If the filter is clogged but not severely damaged, you can attempt to clean it. Use a fuel filter cleaner or a compressed air gun to blow out any debris. Ensure you follow the manufacturer's instructions for the cleaning process. However, if the filter is heavily clogged or damaged beyond repair, it's best to replace it. New filters are readily available at auto parts stores and can be installed using the same steps as removing the old one.
Reinstall and Test: After cleaning or replacing the filter, carefully reinstall it, ensuring all connections are secure. Then, reconnect the fuel pump and restore power. Start the vehicle and let it idle for a few minutes to allow the fuel system to stabilize. Check for any unusual noises or vibrations, and ensure the engine runs smoothly. If you've replaced the filter, it's a good idea to have the fuel system inspected by a professional to ensure there are no further issues.
By regularly checking and maintaining your fuel filter, you can prevent potential fuel-related problems and ensure your vehicle's engine operates at its best. Remember, if you're unsure about any part of this process, consulting a professional mechanic is always an option.
Mastering the Art of Linking Rubber Fuel Lines: A Comprehensive Guide
You may want to see also
Engine Diagnostics: Use diagnostic tools to monitor engine performance and identify pressure issues
When it comes to engine diagnostics, monitoring engine performance and identifying pressure issues is crucial, especially when dealing with fuel lines. Low fuel pressure can lead to a variety of engine problems, from reduced power and fuel efficiency to complete engine failure. Here's a guide on how to use diagnostic tools to identify and address these issues:
Fuel Pressure Tester: One of the primary tools for diagnosing low fuel pressure is a fuel pressure tester. This device is designed to measure the pressure of the fuel in the line. Start by disconnecting the negative battery cable to ensure safety. Then, locate the fuel pump and disconnect the fuel line. Attach the tester to the fuel line, ensuring a secure connection. Turn on the engine and observe the pressure reading. A healthy fuel pressure should typically range between 40-60 psi (pounds per square inch). If the reading is significantly lower, it indicates a potential issue with the fuel pump, filter, or the fuel line itself.
Engine Code Readers: Modern vehicles are equipped with onboard diagnostic systems (OBD-II) that can provide valuable information about engine performance. Connect a code reader to your vehicle's OBD-II port, which is usually located under the dashboard. Turn on the engine and check for error codes related to the fuel system. These codes can provide insights into potential issues, such as a faulty fuel pump, clogged fuel injectors, or problems with the fuel pressure regulator. For example, code P0299 might indicate a low fuel pressure sensor problem, while code P0191 could suggest a fuel pressure regulator malfunction.
Engine Compression Tester: While not directly related to fuel pressure, a compression tester is essential for engine diagnostics. It measures the engine's compression, which is crucial for efficient combustion. Start by removing the spark plugs and connecting the tester to the cylinder head. Rotate the engine's crankshaft by hand or using a crank handle to measure the compression in each cylinder. Low compression can be caused by various issues, including worn piston rings, damaged valves, or a leaking head gasket. Addressing these problems is essential to ensure optimal engine performance and prevent further complications.
Visual Inspection: In addition to using diagnostic tools, a thorough visual inspection is essential. Check the fuel line for any signs of damage, cracks, or leaks. Inspect the fuel pump for proper operation and ensure that the fuel filter is clean and free of debris. Look for any signs of contamination or moisture in the fuel tank, as these can lead to fuel system issues.
Professional Assistance: If you're unsure about using diagnostic tools or if the issues persist, it's advisable to consult a professional mechanic. They have the expertise and specialized equipment to accurately diagnose and repair fuel pressure problems. A mechanic can also provide valuable advice on maintaining your engine's overall health and performance.
Fuel Injector Linearity: A Matter of Efficiency and Precision
You may want to see also
Frequently asked questions
Checking for low fuel pressure is a relatively simple process that can be done with basic tools. First, ensure the engine is off and the vehicle is in a secure location. Locate the fuel pressure gauge, which is typically connected to the fuel rail or the fuel pump. Attach the gauge securely and start the engine. If the gauge reads below the recommended pressure (usually around 6-9 psi for most cars), it indicates low pressure. You can then check for any visible signs of damage or leaks in the fuel line.
Low fuel pressure can be caused by several factors. One common issue is a clogged fuel filter, which restricts the flow of fuel to the engine. Over time, debris and contaminants can accumulate in the filter, leading to reduced pressure. Another potential cause is a faulty fuel pump, which may not be delivering enough fuel at the required pressure. Additionally, issues with the fuel injectors or the engine's management system can also result in low pressure. It's important to diagnose the root cause to ensure proper repairs.
For minor issues, such as a dirty fuel filter, you can replace it yourself as it is a straightforward process. However, if the low pressure is due to a more complex problem, like a faulty fuel pump or injectors, it is recommended to consult a professional mechanic. They have the expertise and tools to accurately diagnose and repair the issue, ensuring your vehicle's optimal performance and safety. Always refer to your vehicle's manual for specific guidance on maintenance and troubleshooting.