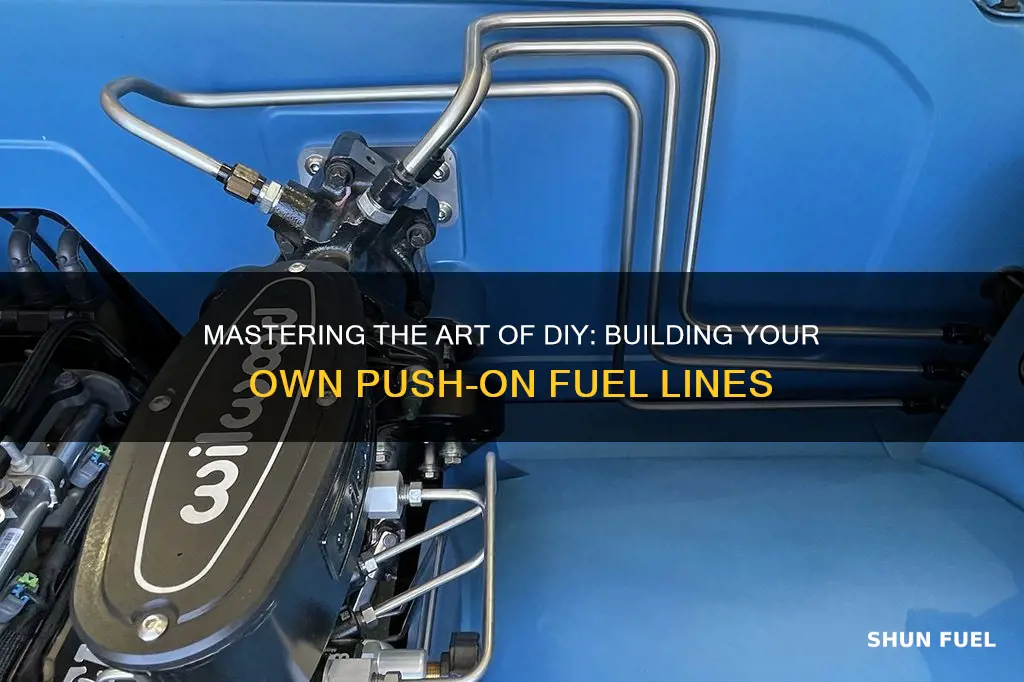
Building your own push-on fuel lines can be a rewarding project for those looking to customize or repair their vehicle's fuel system. This guide will provide a step-by-step approach to creating a reliable and efficient fuel line, ensuring a seamless installation process. From selecting the right materials to mastering the assembly techniques, you'll learn how to create a robust fuel line that meets your specific needs. Whether you're a seasoned mechanic or a DIY enthusiast, this tutorial will equip you with the knowledge to construct a high-quality fuel line, enhancing your vehicle's performance and reliability.
What You'll Learn
- Materials and Tools: Gather necessary supplies like fuel line, fittings, and tools
- Cutting and Measuring: Accurately measure and cut fuel line to desired length
- Fitting Installation: Securely attach fittings to fuel line using appropriate methods
- Testing and Inspection: Check for leaks and ensure proper functionality
- Safety Precautions: Follow guidelines to prevent fires and ensure safe installation
Materials and Tools: Gather necessary supplies like fuel line, fittings, and tools
Before you begin the process of building your own push-on fuel lines, it's crucial to gather all the necessary materials and tools to ensure a successful and safe installation. Here's a comprehensive guide on what you need:
Materials:
- Fuel Line: The primary component is high-quality fuel line specifically designed for automotive applications. Choose a material that is compatible with the fuel type you will be using (e.g., gasoline, diesel, or ethanol). Consider the diameter of the fuel line based on your engine's requirements and the desired flow rate.
- Fittings: You will require various fittings to connect the fuel line to the fuel tank, fuel pump, and other components. Common fittings include quick-connect fittings, barbed fittings, and compression fittings. Ensure they are made from durable materials like brass or stainless steel to withstand fuel pressure.
- Hose Clamps: These are essential for securing the fuel line to the frame or other mounting surfaces. Get a set of adjustable hose clamps that can provide a tight and secure grip.
- Fuel Filter (Optional): If you plan to filter the fuel, consider adding a small in-line fuel filter to ensure clean fuel delivery.
- Fuel Pump (if not integrated): If your vehicle doesn't have a built-in fuel pump, you'll need to source a compatible pump for your engine.
Tools:
- Fuel Line Cutter: A specialized tool for cutting fuel lines to the desired length. This ensures a clean and precise cut.
- Pipe Cutter or Utility Knife: For cutting the fuel line to fit your specific needs.
- Pliers: Essential for gripping and manipulating fittings and fuel line connectors.
- Wrenches: Various sizes of wrenches will be needed to tighten fittings and secure connections.
- Socket Set: A set of sockets for accessing hard-to-reach bolts and nuts.
- Fuel Line Bender: A useful tool for bending the fuel line to fit around obstacles or engine components.
- Tape Measure: To ensure accurate measurements during the installation process.
- Safety Gear: Include safety goggles, gloves, and a respirator to protect yourself during the project.
Having all these materials and tools ready will ensure that you can proceed with the installation process efficiently and effectively. It's important to double-check the compatibility of the parts and tools with your specific vehicle and fuel system to avoid any issues during the build.
Mastering Fuel Line Clip Removal: A Step-by-Step Guide
You may want to see also
Cutting and Measuring: Accurately measure and cut fuel line to desired length
Before you begin the cutting process, it's crucial to ensure you have the right measurements. Start by carefully examining the fuel line and identifying the sections that need to be cut. Measure the length required for each section, taking into account any bends or adjustments needed to fit the fuel line to your specific setup. It's essential to be precise here, as even a small error can lead to issues with fuel flow and potential leaks.
Use a tape measure or a flexible measuring tool to get accurate readings. Wrap the measuring tool around the fuel line, ensuring it's snug but not overly tight. Mark the desired length on the fuel line with a permanent marker or a piece of tape. This step is critical to ensure you don't cut off too much or too little of the fuel line.
Once you've marked the length, it's time to cut. You can use a sharp utility knife or a fuel line cutter, which is a specialized tool designed for this purpose. Place the cutting tool along the marked line and apply firm pressure to make a clean cut. Take your time and be steady to avoid any uneven cuts that could compromise the integrity of the fuel line.
After cutting, inspect the ends of the fuel line to ensure they are smooth and free of any debris. If necessary, use a file or sandpaper to create a smooth surface. This is important to ensure a proper connection when attaching the fuel line to the pump or other components.
Remember, accurate measuring and cutting are fundamental to the success of your DIY fuel line project. Take your time, double-check your measurements, and don't rush the cutting process. This attention to detail will contribute to a reliable and safe fuel system for your vehicle.
Mastering the Art of Fuel Line Clip Removal: A Guide
You may want to see also
Fitting Installation: Securely attach fittings to fuel line using appropriate methods
When installing fittings to your fuel line, it's crucial to ensure a secure and leak-free connection. Here's a step-by-step guide to achieving this:
Preparation: Before you begin, ensure you have the necessary tools and materials, including the appropriate fittings, fuel line, and a solvent-based adhesive or epoxy specifically designed for fuel line applications. Clean the fuel line and fittings thoroughly to remove any dirt or debris. This step is essential to ensure a strong bond.
Fitting Selection: Choose fittings that are compatible with your fuel line material. Common types include barbed fittings, compression fittings, and quick-connect fittings. Each type has its advantages, so select the one that best suits your project's requirements. For example, barbed fittings are easy to use but may not be as secure as compression fittings.
Assembly: Start by inserting the fuel line into the fitting, ensuring it is centered. For barbed fittings, slide the barb onto the fuel line and secure it with the provided clip or crimp. For compression fittings, thread the fitting onto the line and tighten it securely, being careful not to overtighten to avoid damage. Quick-connect fittings often require a special tool for assembly.
Adhesive or Epoxy Application: After assembly, apply the chosen adhesive or epoxy along the fuel line and inside the fitting. Follow the manufacturer's instructions for the correct amount and application method. Allow the adhesive to set according to the manufacturer's guidelines. This step creates a strong bond between the fuel line and fitting, ensuring a leak-free connection.
Testing: Once the adhesive or epoxy has set, test the fitting's integrity. Apply pressure to the connection and check for any leaks. If no leaks are detected, your fitting installation is secure. It's essential to test thoroughly, especially if the fuel line will be under pressure or exposed to varying temperatures.
Remember, proper preparation and the use of the right tools and materials are key to a successful fitting installation. Always refer to the manufacturer's instructions for specific guidelines and safety precautions.
Fuel Line Magnets: Myth or Magic? Unveiling the Truth
You may want to see also
Testing and Inspection: Check for leaks and ensure proper functionality
When you've constructed your push-on fuel lines, it's crucial to thoroughly test and inspect them to ensure they are leak-free and functional. Start by visually inspecting the connections and fittings for any signs of damage or debris. Look for any visible cracks, corrosion, or signs of wear and tear that could compromise the integrity of the system. Pay close attention to the threads of the push-on fittings; they should be clean, smooth, and free of any damage that could lead to leaks.
The next step is to perform a leak test. This can be done using a simple procedure: fill the fuel lines with a suitable fuel type and then use a soapy water solution as a leak detection method. Start at the fuel tank and work your way along the lines, ensuring that each connection is properly sealed. Bubble-free soap water indicates no leaks, while bubbles suggest a potential issue. If you do find a leak, carefully disassemble the affected section and re-tighten the connections, ensuring they are secure and free of any debris.
Additionally, it's important to check the functionality of the push-on fuel lines. This involves ensuring that the fuel flows smoothly through the lines when the system is under pressure. You can use a fuel pressure gauge to measure the pressure at different points along the lines, comparing it to the expected values for your specific fuel system. If the pressure is inconsistent or too low, it may indicate a blockage or a faulty connection that needs to be addressed.
For added safety, consider using a fuel line inspection camera to get a clear view of the interior of the lines. This can help identify any internal damage, blockages, or potential issues that might not be visible to the naked eye. By combining visual inspection, leak testing, and functionality checks, you can ensure that your custom-built push-on fuel lines are reliable and safe for use. Remember, thorough testing and inspection are essential to maintaining the performance and longevity of your fuel system.
NPT Sizes: Unraveling the Mystery of 5/16 Fuel Lines
You may want to see also
Safety Precautions: Follow guidelines to prevent fires and ensure safe installation
When embarking on the project of building your own push-on fuel lines, safety should be your top priority. The process involves working with flammable substances and high-pressure systems, so it's crucial to follow guidelines to prevent fires and ensure a safe installation. Here are some essential safety precautions to keep in mind:
Ventilation and Fire Safety: Ensure you are working in a well-ventilated area, preferably outdoors, to minimize the risk of fire. Gasoline and other fuels are highly flammable, and any spark or flame could lead to a dangerous situation. Avoid using open flames or heat sources near the fuel or the work area. Consider wearing protective gear, such as heat-resistant gloves and a respirator, to safeguard against potential hazards.
Fuel Handling and Storage: Handle fuel with care and store it in approved containers. Always use containers designed for fuel storage, ensuring they are clean, dry, and sealed properly. Never store fuel in containers with damaged seals or near ignition sources. When transferring fuel, use a funnel to prevent spills and always be cautious of any potential leaks. Keep the fuel away from direct sunlight and extreme temperatures to maintain its stability.
Pressure Testing and Safety Devices: Before and after installation, perform pressure testing to ensure the system is leak-free. Use a pressure gauge and a soapy water solution to identify any potential leaks. Install safety devices like pressure relief valves and fuel filters to prevent excessive pressure buildup and contamination. These devices act as safeguards, releasing excess pressure or filtering out contaminants to maintain the system's integrity.
Proper Tool Usage and Electrical Safety: Utilize the appropriate tools for the job, ensuring they are in good condition. Avoid using electrical tools or equipment near fuel lines, as sparks from faulty wiring or switches can ignite fuel. Keep a safe distance from any electrical sources and consider using ground-fault circuit interrupters (GFCIs) to protect against electrical hazards.
Training and Professional Guidance: If you are new to this process, consider seeking guidance from professionals or experienced individuals. They can provide valuable insights and ensure you follow the correct procedures. Proper training will help you understand the potential risks and enable you to make informed decisions during the installation process.
Remember, safety should always be the primary focus when working with fuel systems. By adhering to these guidelines, you can minimize the risks associated with fire, explosions, and other hazards, ensuring a successful and safe installation of your push-on fuel lines.
Unclogging Boat Fuel Lines: A Step-by-Step Guide to Getting Your Engine Running Again
You may want to see also
Frequently asked questions
To create a push-on fuel line, you will require a few essential components. These include a length of fuel line tubing, a fuel line fitting kit with the appropriate sizes for your application, and a fuel pump or source to connect to. Additionally, you might need tools like a fuel line cutter, crimping tools, and a fuel line inspection mirror for a thorough setup.
Achieving a secure and leak-free connection is crucial. Start by cleaning the ends of the fuel line tubing and the fittings with a solvent to remove any dirt or debris. Then, use a fuel line cutter to ensure precise lengths. Apply a thin layer of fuel line adhesive to the tubing and fittings, following the manufacturer's instructions. Finally, crimp the connections using the appropriate tools to create a tight seal.
Absolutely! One of the advantages of building your own push-on fuel line is the flexibility to customize the length. Measure the distance you need between the fuel source and the engine, ensuring you have a few extra inches for any potential adjustments. Cut the fuel line tubing to the desired length, and then connect it to the fittings using the crimping method mentioned above.
During the installation, keep an eye out for potential problems. Ensure that the fuel line is not twisted or kinked, as this can restrict fuel flow and cause issues. Check for any sharp bends or turns that might lead to stress on the tubing. Also, verify that all connections are tight and secure, as loose fittings can result in fuel leaks. Regularly inspect the fuel line for any signs of damage or wear over time.