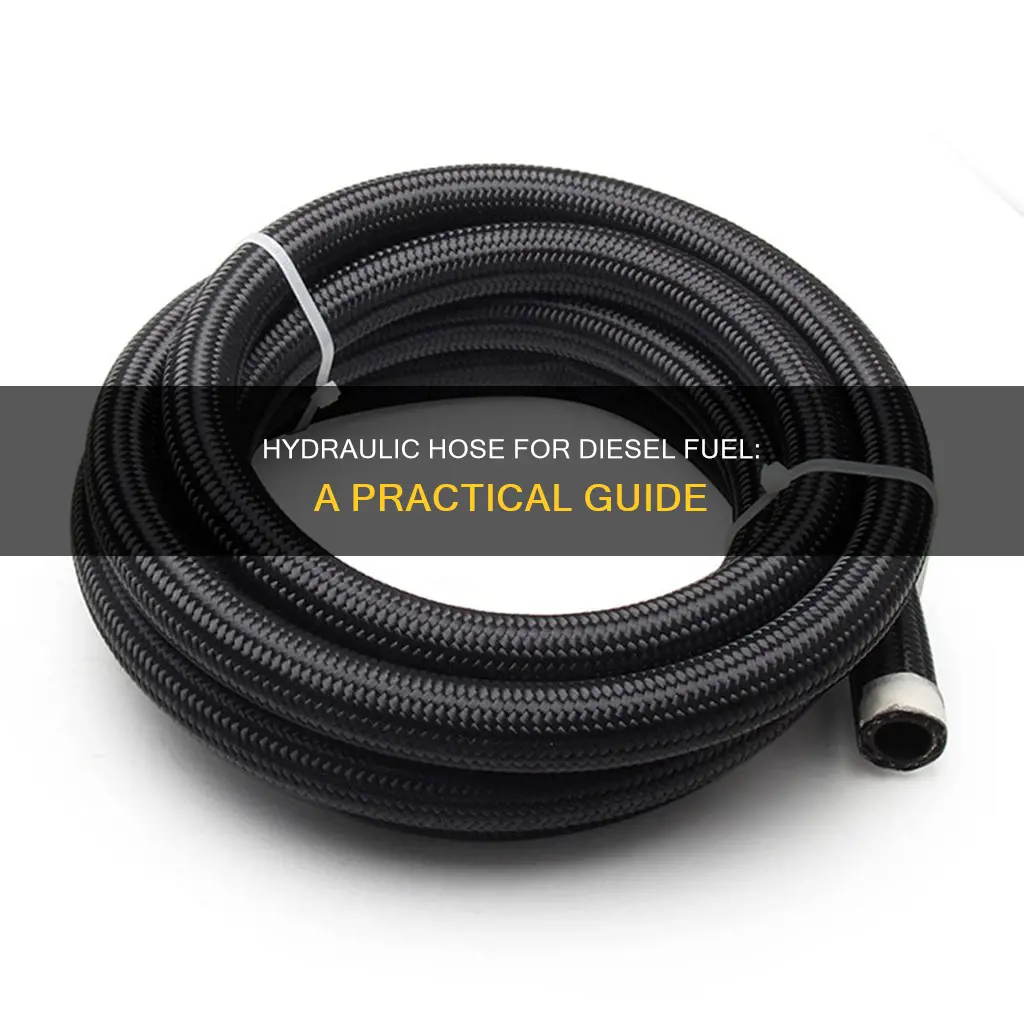
When considering the use of hydraulic hoses for diesel fuel lines, it's important to understand the specific requirements and compatibility of these two systems. Hydraulic hoses are designed to transmit fluid under pressure, while diesel fuel lines are specifically engineered to handle the unique properties of diesel fuel. This comparison explores the feasibility and potential challenges of using hydraulic hoses in place of traditional diesel fuel lines, considering factors such as pressure requirements, fluid compatibility, and the overall performance and safety of the system.
Characteristics | Values |
---|---|
Compatibility | Hydraulic hoses are generally not suitable for diesel fuel lines due to the different operating conditions and requirements. |
Temperature Range | Hydraulic hoses typically handle temperatures between -40°F and 212°F (-40°C and 100°C), while diesel fuel lines require a wider range of -40°F to 250°F (-40°C to 121°C). |
Pressure Rating | Hydraulic hoses are designed for high-pressure applications, often exceeding 3000 psi (pounds per square inch), whereas diesel fuel lines usually operate at much lower pressures, around 100-200 psi. |
Flexibility | While hydraulic hoses offer flexibility, diesel fuel lines require a more rigid design to withstand vibrations and movement during vehicle operation. |
Chemical Resistance | The materials used in hydraulic hoses may not be compatible with diesel fuel, which can lead to degradation over time. |
Cost | Hydraulic hoses are generally more expensive than standard fuel lines. |
Availability | Standard fuel lines are widely available, whereas specialized hydraulic hoses may require custom ordering. |
Installation | Installing hydraulic hoses might require more complex procedures compared to standard fuel lines. |
Maintenance | Regular maintenance and inspections are crucial for both hydraulic hoses and diesel fuel lines to ensure longevity and performance. |
Safety | Using hydraulic hoses for fuel lines may pose safety risks due to the potential for leaks and the high-pressure nature of hydraulic systems. |
What You'll Learn
- Material Compatibility: Ensure hydraulic hose materials can withstand diesel fuel's corrosive properties
- Pressure Rating: Choose a hose with sufficient pressure rating for diesel fuel's high pressure
- Flexibility: Opt for a flexible hose to accommodate engine vibrations and movement
- Temperature Tolerance: Select a hose that can handle diesel fuel's temperature range
- Installation Guidelines: Follow manufacturer instructions for proper installation and sealing
Material Compatibility: Ensure hydraulic hose materials can withstand diesel fuel's corrosive properties
When considering the use of hydraulic hoses for diesel fuel lines, material compatibility is a critical factor to ensure the longevity and reliability of the system. Diesel fuel is a harsh and corrosive substance, containing water, acids, and other contaminants that can degrade traditional rubber hoses over time. Therefore, it is essential to select hydraulic hose materials that can withstand the corrosive properties of diesel fuel.
One of the primary concerns with diesel fuel is its tendency to promote the growth of microorganisms, such as bacteria and fungi. These microorganisms can produce acids that corrode the hose's inner lining, leading to leaks and system failures. To combat this, hydraulic hoses designed for diesel fuel applications often incorporate antimicrobial additives or use materials with inherent antimicrobial properties. These specialized hoses can inhibit the growth of microorganisms, ensuring the fuel remains clean and the hose's integrity is maintained.
Additionally, the choice of hose material should consider the temperature and pressure requirements of the diesel fuel system. Diesel fuel can operate at elevated temperatures and pressures, especially in heavy-duty applications. Materials like synthetic rubber, such as neoprene or EPDM, offer excellent resistance to heat and chemicals, making them suitable for these demanding conditions. These materials can withstand the corrosive effects of diesel fuel without compromising their flexibility and durability.
Another important aspect is the hose's ability to resist abrasion and wear. Diesel fuel lines often encounter rough environments, especially in off-road or industrial settings. Hose materials like nylon or braided steel reinforcement can provide enhanced protection against abrasion, ensuring the hose's longevity in challenging conditions. These materials offer superior strength and flexibility, allowing the hose to withstand the rigors of diesel fuel transportation.
In summary, when using hydraulic hoses for diesel fuel lines, it is imperative to prioritize material compatibility. The chosen materials should be able to resist the corrosive nature of diesel fuel, including its microbial content and chemical composition. By selecting hoses with appropriate additives, reinforcements, and specialized compounds, you can ensure a reliable and long-lasting fuel delivery system, even in the most demanding applications.
Kawasaki X2 Direct Fuel Line: A Step-by-Step Guide to Tuning
You may want to see also
Pressure Rating: Choose a hose with sufficient pressure rating for diesel fuel's high pressure
When considering the use of hydraulic hoses for diesel fuel lines, one of the most critical factors to evaluate is the pressure rating. Diesel fuel systems operate under high-pressure conditions, and using a hose with an inadequate pressure rating can lead to dangerous consequences. The pressure in a diesel engine can range from 100 to 200 psi (pounds per square inch) or even higher, depending on the engine type and design. Therefore, it is essential to choose a hydraulic hose that can withstand these high-pressure levels to ensure the safety and reliability of the fuel system.
The pressure rating of a hydraulic hose is typically indicated by the manufacturer and is measured in psi. For diesel fuel applications, it is recommended to select a hose with a minimum pressure rating of 200 psi or higher. This ensures that the hose can handle the typical pressure fluctuations and surges associated with diesel engines. Using a hose with a lower pressure rating may result in premature failure, leaks, or even hose rupture, which can cause fuel spillage, engine damage, and potential safety hazards.
To determine the appropriate pressure rating, consider the specific requirements of your diesel engine and fuel system. Consult the vehicle's manual or manufacturer's guidelines to identify the recommended hose specifications. Different engines may have varying pressure needs, and using a hose that meets or exceeds these requirements is crucial. For instance, if your diesel engine operates at 150 psi, a hose with a 200 psi rating would provide a safety margin and ensure long-term reliability.
In addition to the pressure rating, pay attention to other hose characteristics that contribute to its suitability for diesel fuel lines. These include the hose's material, flexibility, and resistance to fuel degradation. High-quality hoses made from durable materials like synthetic rubber or polyurethane are often preferred for their ability to withstand the corrosive nature of diesel fuel. Ensure that the hose has sufficient flexibility to accommodate engine movement and has been tested for long-term fuel compatibility.
In summary, when using hydraulic hoses for diesel fuel lines, prioritizing the pressure rating is essential. Selecting a hose with a minimum pressure rating of 200 psi or higher ensures that it can handle the high-pressure conditions of diesel engines. Always refer to the manufacturer's guidelines and consult the vehicle's manual to choose the most appropriate hose for your specific diesel fuel system. By doing so, you can ensure the safety, efficiency, and longevity of your diesel engine's fuel delivery system.
Optimizing Performance: Choosing the Right Fuel Line for Your SBC 350
You may want to see also
Flexibility: Opt for a flexible hose to accommodate engine vibrations and movement
When considering the use of hydraulic hoses for diesel fuel lines, one crucial aspect to focus on is flexibility. This characteristic is essential to ensure the longevity and reliability of your fuel system, especially in the face of engine vibrations and movement. Here's why flexibility should be at the top of your list:
Engine Vibration and Movement: Diesel engines are known for their robust performance, but they also generate significant vibrations during operation. These vibrations can cause stress on rigid hoses, leading to potential cracks, leaks, or even hose failure over time. Flexible hoses, on the other hand, are designed to absorb and distribute these vibrations, ensuring a more stable and secure connection between the fuel pump and the engine. This is particularly important in applications where the engine is mounted in a non-ideal position or where there are frequent starts and stops.
Accommodating Engine Movement: Engines are not static; they move and shift with each revolution. A flexible hose allows for this natural movement without putting excessive strain on the fuel line. This is especially beneficial in older vehicles or those with less-than-perfect engine mounts, where the engine may not be perfectly aligned. By choosing a flexible hose, you're providing a buffer that can adapt to these movements, reducing the risk of damage to the fuel system.
Long-Term Reliability: The primary goal of using a flexible hose is to enhance the overall reliability of your diesel fuel system. Over time, rigid hoses can become brittle and lose their ability to withstand vibrations, leading to potential fuel leaks or system failures. Flexible hoses, made from materials like rubber or synthetic compounds, maintain their flexibility and resilience, ensuring a consistent and secure fuel supply. This is crucial for maintaining engine performance and preventing unexpected breakdowns.
Installation and Maintenance: Flexible hoses also make the installation and maintenance process easier. Their pliability allows for more straightforward routing, making it simpler to navigate around engine components and frame members. This can save time and effort during fuel system installations or repairs, ensuring a more efficient and cost-effective solution.
In summary, when using hydraulic hoses for diesel fuel lines, flexibility is a key consideration. It ensures that your fuel system can withstand the rigors of engine operation, providing a reliable and long-lasting solution. By choosing a flexible hose, you're investing in a system that can adapt to the unique challenges of diesel engines, ultimately improving the overall performance and longevity of your vehicle.
Understanding Flaring: A Fuel Line Emergency
You may want to see also
Temperature Tolerance: Select a hose that can handle diesel fuel's temperature range
When considering the use of hydraulic hoses for diesel fuel lines, one of the critical factors to evaluate is the temperature tolerance of the hose material. Diesel fuel can vary significantly in temperature, and it's essential to select a hose that can withstand these temperature fluctuations without compromising its integrity.
The temperature range of diesel fuel can vary depending on environmental conditions and the specific grade of diesel. Typically, diesel fuel can range from extremely cold temperatures, often below freezing, to hot temperatures when the fuel is heated or exposed to prolonged periods of high ambient temperatures. For example, in colder climates, diesel fuel can drop to -40°F (-40°C), while in warmer regions, it can reach temperatures of around 150°F (65°C).
To ensure the safe and efficient operation of your diesel fuel system, it is crucial to choose a hydraulic hose that can handle these temperature extremes. The hose should be able to maintain its flexibility, strength, and structural integrity across the entire temperature range of the diesel fuel. This is particularly important in applications where the hose is exposed to rapid temperature changes, such as in engines or fuel tanks with heating systems.
Hose materials designed for hydraulic systems often incorporate rubber or synthetic compounds that offer excellent temperature resistance. These materials can withstand the high temperatures associated with diesel fuel without becoming brittle or losing their sealing properties. Additionally, hoses with reinforced construction, such as those with braided or spiral-wound designs, can provide enhanced flexibility and durability, making them suitable for temperature-sensitive applications.
In summary, when using hydraulic hoses for diesel fuel lines, it is imperative to select a hose with a temperature tolerance that matches or exceeds the expected temperature range of the diesel fuel. This ensures the longevity and reliability of the fuel system, preventing potential issues caused by hose failure due to extreme temperatures. Always refer to the manufacturer's specifications and guidelines to choose the appropriate hose for your specific diesel fuel application.
Nylon Fuel Line: Safe Usage Guide for Your Vehicle
You may want to see also
Installation Guidelines: Follow manufacturer instructions for proper installation and sealing
When considering the use of hydraulic hoses for diesel fuel lines, it is crucial to adhere to the manufacturer's instructions for a successful and safe installation. Proper installation ensures the integrity of the fuel system and prevents potential issues. Here are some detailed guidelines to follow:
Pre-Installation Preparation: Before beginning the installation, ensure you have the correct hydraulic hose specified by the manufacturer for diesel fuel applications. Check the hose's compatibility with the fuel type and any additives present. Gather the necessary tools and materials, including fittings, clamps, and any additional components required for the specific application. Clean and inspect the fuel line and fittings to ensure they are free from debris and damage.
Installation Process: Start by laying out the hydraulic hose along the desired route, ensuring it is free from sharp bends or kinks that could restrict fuel flow. Connect the hose to the fuel line fittings, using the appropriate tools to tighten the connections securely. Follow the manufacturer's recommendations for torque specifications to avoid over-tightening, which can damage the hose or fittings. Use the provided clamps or other securing methods to fasten the hose in place, ensuring it remains stable and does not interfere with other components.
Sealing and Protection: Proper sealing is critical to prevent fuel leaks. Use the manufacturer's recommended sealing compounds or tape for hydraulic hose connections. Ensure that all connections are tight and free from any gaps that could allow fuel to seep out. Consider applying a protective coating or sleeve over the hose, especially in areas where it comes into contact with hot surfaces or sharp edges, to safeguard against potential damage.
Testing and Inspection: After the installation, perform a thorough inspection to identify any potential issues. Check for any visible signs of damage, such as cracks or bulges in the hose. Ensure that all connections are secure and that there are no leaks at the fittings. Test the fuel system by operating the vehicle or equipment and monitoring for any unusual noises or performance issues. If any problems are detected, refer to the manufacturer's troubleshooting guidelines or seek professional assistance.
By following the manufacturer's instructions and adhering to these installation guidelines, you can ensure a reliable and safe connection for your diesel fuel line using hydraulic hoses. Proper installation and sealing are essential to maintain the performance and longevity of the fuel system.
Simple Steps to Turn Off Fuel on Your Simplicity Mower
You may want to see also
Frequently asked questions
While hydraulic hoses and diesel fuel lines both involve the transportation of fluids, they serve different purposes and have distinct requirements. Hydraulic hoses are designed to handle high-pressure fluids and are typically used in hydraulic systems for machinery and equipment. On the other hand, diesel fuel lines are specifically engineered to carry diesel fuel from the tank to the engine, ensuring it meets the necessary standards for combustion. Due to the different operating conditions and fluid properties, it is generally not recommended to use hydraulic hose for a diesel fuel line.
Using hydraulic hose for a diesel fuel line can pose several risks. Firstly, hydraulic hoses are not designed to withstand the high temperatures and fuel properties of diesel, which can lead to degradation and potential failure over time. Secondly, the pressure requirements for hydraulic systems are much higher than those of a fuel line, and hydraulic hoses may not be able to handle the stress, potentially causing leaks or even hose rupture. Lastly, the materials used in hydraulic hoses might not be compatible with diesel fuel, leading to corrosion or contamination.
Yes, there are specific components designed for diesel fuel lines. These include fuel hoses, which are made from materials that can withstand the unique challenges of diesel fuel, such as its higher temperature and chemical composition. Additionally, fuel lines are often made from flexible metal tubing, which provides the necessary flexibility while maintaining structural integrity. It is crucial to use these specialized components to ensure the safe and efficient operation of the diesel fuel system.
To ensure compatibility, it is essential to choose a hose that meets the industry standards and specifications for diesel fuel lines. Look for hoses that are specifically designed for fuel applications and are made from materials resistant to diesel fuel degradation. Consulting the vehicle's manual or seeking advice from automotive experts can provide guidance on the appropriate hose type and size for your diesel engine. Regular inspections and maintenance can also help identify any potential issues and ensure the longevity of the fuel system.