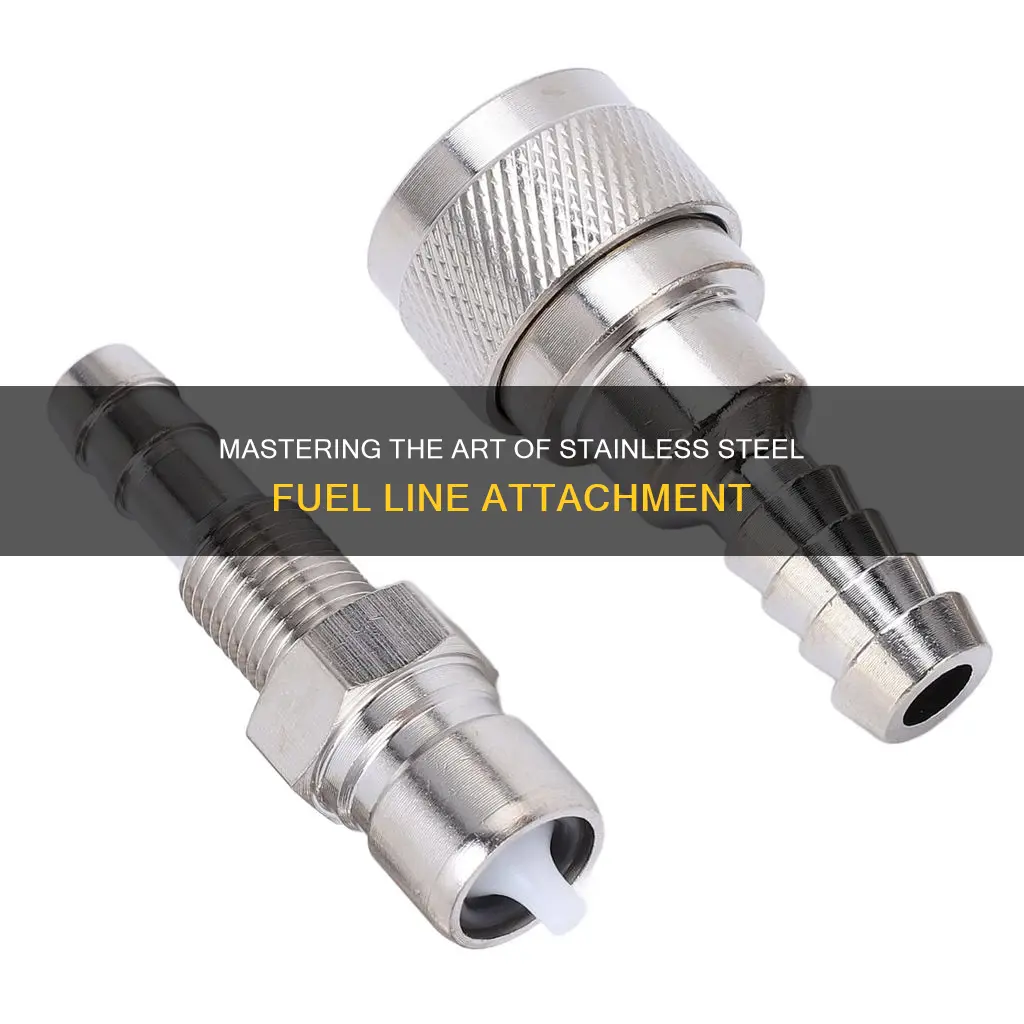
Attaching stainless steel fuel lines is a crucial step in any vehicle's fuel system installation or repair. This process requires precision and attention to detail to ensure a secure and reliable connection. In this guide, we will explore the step-by-step process of attaching these fuel lines, covering the necessary tools, preparation techniques, and best practices to ensure a professional-grade finish. From understanding the different types of fittings and their uses to mastering the art of soldering and compression fittings, this guide will provide a comprehensive overview to help you achieve a safe and efficient fuel line setup.
What You'll Learn
- Prepare Materials: Gather necessary tools and stainless steel fuel lines, ensuring compatibility and proper gauge
- Clean Surfaces: Use a degreaser to remove contaminants, ensuring a strong bond and preventing leaks
- Fitting Selection: Choose appropriate fittings, considering fuel type and line diameter for a secure connection
- Assembly Technique: Follow a step-by-step process, tightening fittings securely without over-tightening to avoid damage
- Testing Integrity: Inspect for leaks and ensure proper flow, confirming the system's reliability and safety
Prepare Materials: Gather necessary tools and stainless steel fuel lines, ensuring compatibility and proper gauge
When preparing to attach stainless steel fuel lines, it's crucial to gather the right materials and tools to ensure a successful and secure installation. Here's a detailed guide on how to prepare your materials:
Gather the Essential Tools: Before you begin, make a comprehensive list of the tools you'll need. This includes basic hand tools such as a wrench, pliers, and a utility knife. You might also require a fuel line cutter or a tube cutter, which is essential for precise and clean cuts. Additionally, consider using a fuel line primer and a fuel line adhesive to ensure a strong bond between the fuel lines and any existing connections. Having these tools ready will make the installation process much smoother.
Select the Right Stainless Steel Fuel Lines: Compatibility is key. Ensure that the stainless steel fuel lines you choose are compatible with your vehicle's fuel system and the type of fuel it uses. Check the specifications and dimensions to match the fuel lines with the existing connections. It's important to select the correct gauge as well; a thicker gauge will provide more durability but might be less flexible. Consider the length of the fuel lines needed and measure carefully to avoid any excess or shortage.
Prepare the Fuel Lines: Once you have the fuel lines, inspect them for any defects or damage. Ensure they are free from bends, kinks, or any visible imperfections. If you notice any issues, replace the fuel lines with new ones. It's also a good practice to lubricate the fuel lines slightly to make them more flexible during installation. This step is especially useful if you're working with thicker gauge lines.
Ensure Proper Gauge and Compatibility: Double-check the gauge of the stainless steel fuel lines to ensure it matches the requirements. If you're replacing existing lines, compare the gauge and dimensions to ensure a perfect fit. Proper gauge ensures that the fuel lines can withstand the pressure and temperature changes associated with the fuel system. Compatibility with the vehicle's fuel system is vital to prevent any potential issues or leaks.
By following these steps, you'll have a well-prepared setup for attaching stainless steel fuel lines, ensuring a professional and reliable installation. Remember, taking the time to gather the right materials and tools, and verifying compatibility, will contribute to a successful and long-lasting fuel line system.
Radiator Hose as Fuel Line: A Creative Fix or a Recipe for Disaster?
You may want to see also
Clean Surfaces: Use a degreaser to remove contaminants, ensuring a strong bond and preventing leaks
When preparing to attach stainless steel fuel lines, it's crucial to ensure a clean and contaminant-free surface for a secure and leak-free connection. The process begins with a thorough understanding of the importance of cleanliness in this application. Contaminants such as grease, oil, and dirt can compromise the integrity of the bond between the fuel lines and the fittings, leading to potential leaks and system failures.
To achieve a clean surface, start by gathering the necessary tools and materials. You will need a degreaser, which is a powerful cleaning agent specifically designed to break down and remove stubborn contaminants. Choose a degreaser that is compatible with stainless steel to avoid any potential damage to the material. Additionally, have a clean cloth or rag, and a suitable solvent or cleaner to assist in the cleaning process.
Begin by disconnecting the fuel lines from their current fittings, if applicable. This step ensures that you are working with bare metal surfaces that need to be cleaned. Once disconnected, inspect the surfaces of the fuel lines and fittings. Look for any visible contaminants such as grease or residue. If present, use the degreaser generously and ensure it covers the entire area. Allow the degreaser to sit for a few minutes to effectively break down the contaminants.
After the degreaser has done its work, rinse the surfaces thoroughly with clean water. Ensure that all traces of the degreaser and contaminants are removed. Use a soft cloth or rag to wipe away any remaining moisture, leaving the surfaces dry and ready for the next step. It is essential to remove all traces of degreaser and contaminants to ensure a strong bond.
Finally, reattach the fuel lines to the fittings, ensuring a tight and secure connection. The clean surfaces will promote a strong bond, reducing the risk of leaks. Regularly inspect and maintain the connections to ensure the longevity of the fuel system. By following these steps and paying close attention to surface cleanliness, you can effectively attach stainless steel fuel lines, creating a reliable and safe fuel system.
Understanding Fuel Line Seals: A Comprehensive Guide
You may want to see also
Fitting Selection: Choose appropriate fittings, considering fuel type and line diameter for a secure connection
When working with stainless steel fuel lines, selecting the right fittings is crucial for a secure and reliable connection. The choice of fittings depends on several factors, including the type of fuel being used and the diameter of the fuel line. Here's a detailed guide on how to choose the appropriate fittings:
Consider Fuel Type: Different fuels have varying properties, and this should influence your fitting selection. For example, if you're dealing with gasoline, you might opt for fittings designed specifically for this fuel type. Gasoline fittings are typically made from materials that can withstand the volatility and potential corrosive effects of gasoline. On the other hand, if you're working with diesel, you'll need fittings that can handle the higher pressure and different chemical composition of diesel fuel. Understanding the fuel's characteristics will help you choose fittings that offer the necessary protection against corrosion, heat, and pressure.
Line Diameter and Fitting Compatibility: The diameter of your stainless steel fuel line is a critical factor. Fittings come in various sizes, and it's essential to match the fitting's bore to the fuel line's diameter. If the fitting is too small, it may restrict fuel flow, leading to potential performance issues. Conversely, a fitting that's too large might not provide a tight seal, compromising the system's integrity. Always refer to the manufacturer's specifications or consult a fuel system expert to ensure you select fittings that are compatible with the specific fuel line diameter.
Material Compatibility: Stainless steel fuel lines often require fittings made from similar materials to ensure a secure and corrosion-resistant connection. Common materials for stainless steel fuel line fittings include 304 or 316 stainless steel, brass, and aluminum. These materials offer excellent corrosion resistance and durability, ensuring a long-lasting connection. When choosing fittings, look for those made from compatible materials to avoid any potential degradation or failure over time.
Thread and Connection Type: Consider the thread type and connection mechanism of the fittings. Common thread types include NPT (National Pipe Thread), BSPT (British Standard Pipe Thread), and metric threads. Ensure that the thread size and pitch match the fuel line and fittings you are using. Additionally, choose between compression, quick-connect, or flare fittings based on your application's requirements. Compression fittings provide a tight seal using a ferrule, quick-connect fittings offer ease of assembly and disassembly, while flare fittings use a flared end to create a secure connection.
Testing and Quality Assurance: Before finalizing your fitting selection, ensure that the chosen fittings undergo rigorous testing to meet industry standards. Look for fittings that have been pressure-tested, burst-tested, and checked for leaks to guarantee a secure and reliable connection. High-quality fittings will provide peace of mind and ensure the longevity of your fuel system.
Poulan Prolink P335 Fuel Line Size: Essential Guide for Optimal Performance
You may want to see also
Assembly Technique: Follow a step-by-step process, tightening fittings securely without over-tightening to avoid damage
When attaching stainless steel fuel lines, a meticulous assembly process is crucial to ensure a secure and reliable connection. Here's a step-by-step guide to achieving this:
- Prepare the Components: Begin by laying out all the necessary parts, including the fuel lines, fittings, and any necessary tools. Ensure that the stainless steel fuel lines are clean and free of any debris or contaminants. Inspect the fittings for any signs of damage or wear, replacing them if necessary.
- Positioning: Carefully position the fuel line where it needs to be attached. Ensure that it is aligned correctly with the fitting, allowing for a smooth and secure connection. Take note of any bends or kinks in the line to avoid potential issues during installation.
- Inserting the Fitting: Slide the fitting onto the fuel line. Ensure that the threads of the fitting are aligned with the line's end. This step requires precision to create a tight seal without damaging the line's integrity.
- Tightening the Fitting: Use a wrench or a suitable tool to tighten the fitting securely. The goal is to achieve a tight connection, but be cautious not to over-tighten. Apply steady pressure, ensuring the fitting is snug without forcing it. Over-tightening can lead to damage to the fuel line or threads, so take your time and use controlled force.
- Final Adjustments: After tightening the fitting, make any necessary adjustments to ensure a proper seal. Check for any leaks around the connection by applying a small amount of fuel or a suitable sealant. If there are any leaks, re-tighten the fitting slightly and recheck.
- Documentation: Once all connections are secure, document the process with notes or photographs. This documentation will be valuable for future reference, especially if any adjustments or replacements are needed.
Remember, the key to successful assembly is patience and precision. Take your time with each step, ensuring a secure and damage-free connection for your stainless steel fuel lines.
Locate the Fuel Line: 2001 Monte Carlo Guide
You may want to see also
Testing Integrity: Inspect for leaks and ensure proper flow, confirming the system's reliability and safety
When dealing with fuel systems, ensuring the integrity and safety of the setup is paramount. After attaching the stainless steel fuel lines, the next crucial step is to thoroughly test the system for any potential leaks and to confirm that the fuel is flowing correctly. This process is essential to guarantee that the fuel lines are secure, the connections are tight, and there are no vulnerabilities that could lead to fuel leaks or system failures.
Start by applying a small amount of diesel fuel or a suitable sealant along the length of the fuel lines, especially at the connections and fittings. This step is critical as it helps to identify any potential leaks. Then, use a soapy water solution, a common method for leak detection, and carefully inspect the entire system. Look for any bubbles forming on the surface of the soapy water, as these bubbles indicate the presence of a leak. Even the tiniest bubble can signal a potential issue, so pay close attention to every inch of the fuel lines.
If you identify any leaks, it's essential to address them immediately. Tighten any loose fittings or connections and ensure that all components are properly secured. In some cases, you might need to re-attach certain parts or even replace damaged components to ensure a leak-free system. This process requires patience and a keen eye for detail to ensure that the system is robust and reliable.
Once you've addressed any leaks, it's time to test the flow of fuel. Start the engine and monitor the fuel gauge to ensure it rises steadily, indicating proper fuel flow. Listen for any unusual noises, such as hissing or gurgling, which could suggest a restricted flow or a potential issue with the fuel pump. If the engine starts and runs smoothly, you've successfully confirmed the system's reliability. However, if the engine struggles to start or runs erratically, further investigation is required to identify the root cause.
In summary, testing the integrity of the fuel system is a critical step in the process of attaching stainless steel fuel lines. By applying a sealant, using soapy water for leak detection, and carefully monitoring the engine's performance, you can ensure that the system is safe, reliable, and ready for use. This meticulous approach to testing is essential to prevent potential hazards and maintain the overall health of the vehicle's fuel system.
Fixing Fuel Line Hose: A Guide for 1995 Chevy 1500 Owners
You may want to see also
Frequently asked questions
Attaching stainless steel fuel lines requires a careful process to ensure a tight and reliable bond. Start by cleaning the surfaces of both the fuel line and the fitting with a suitable solvent to remove any dirt or contaminants. Then, use a fuel line primer specifically designed for stainless steel to create a bonding agent. Apply the primer to the fuel line and fitting, ensuring an even coat. Allow the primer to dry according to the manufacturer's instructions. Next, insert the fuel line into the fitting, pushing it firmly until it is fully seated. Use a fuel line clamp or ferrule to secure the connection, tightening it by hand first to avoid over-tightening, and then using a wrench to ensure a snug fit. Finally, wipe away any excess primer and ensure the connection is free of any debris.
While you can use various types of clamps and ferrules for stainless steel fuel lines, it's essential to choose the right one for the job. Stainless steel fuel lines often require a ferrule that is compatible with the material to ensure a secure and leak-free connection. Common choices include stainless steel or 316L ferrules, which offer excellent corrosion resistance. When selecting a ferrule, ensure it matches the fuel line's diameter and thickness. Additionally, consider the type of clamp, such as a compression or quick-connect style, depending on your application's requirements. Always refer to the manufacturer's guidelines for the best results.
Preventing damage to the fuel lines is crucial during installation. Here are some tips to avoid any harm: always wear protective gloves to prevent abrasion and ensure a clean grip. Avoid using excessive force when inserting the fuel line into the fitting; instead, apply steady pressure. Be mindful of sharp edges or tools that could scratch the fuel line's surface. Consider using a fuel line protector or sleeve, especially in areas where the line passes through tight spaces or vibrations are present. Regularly inspect the fuel lines for any signs of damage and replace them if necessary before attaching.
Yes, having the right tools can make the attachment process smoother. You'll typically need a fuel line cutter or a pair of sharp scissors to ensure a clean and precise cut on the fuel line. A fuel line primer applicator or a small brush can help evenly apply the primer. A wrench or a specialized fuel line tool is essential for tightening the clamp or ferrule securely. Additionally, consider using a fuel line crimping tool if you're working with quick-connect fittings. These tools will ensure a professional and secure attachment.