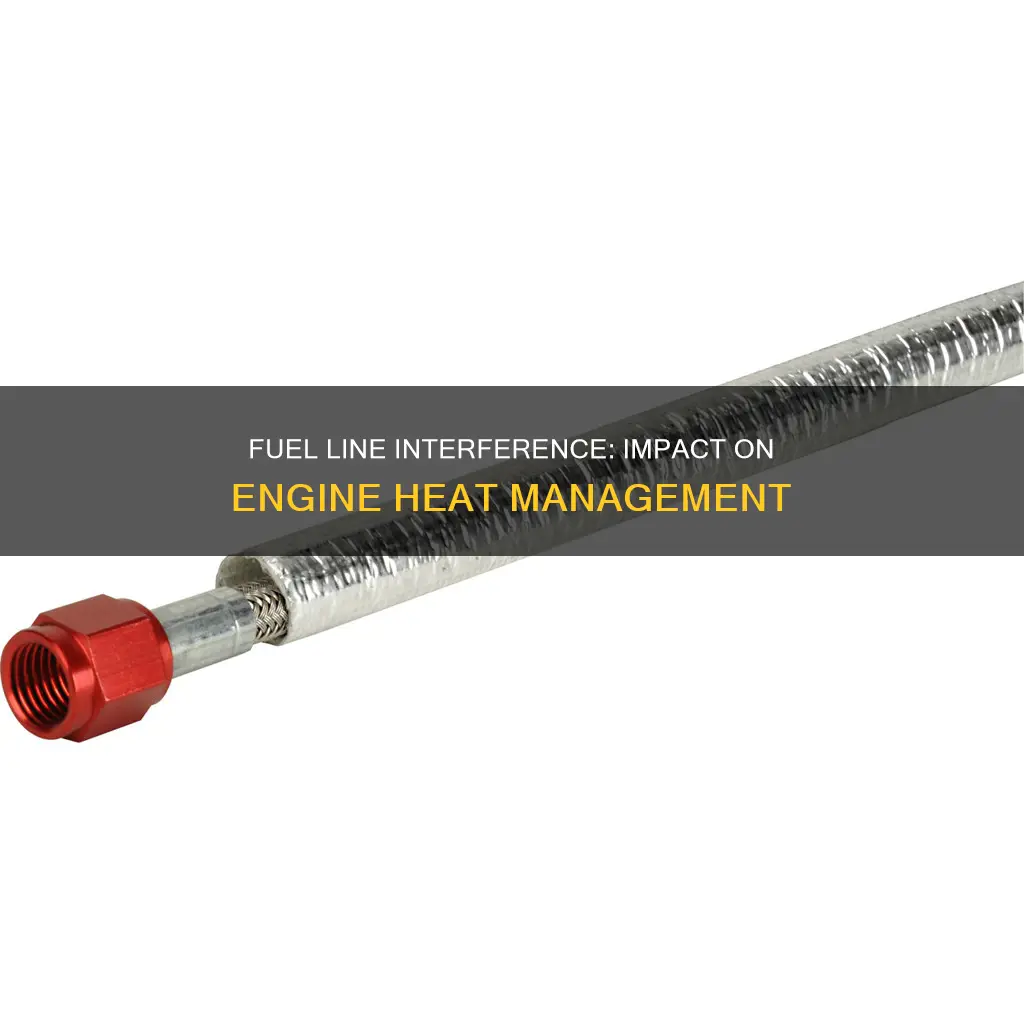
The relationship between fuel lines and heat is an important consideration in vehicle maintenance and performance. Fuel lines, which carry gasoline or diesel from the tank to the engine, can play a significant role in how efficiently a vehicle's engine operates. When fuel lines are in good condition, they allow for optimal fuel flow, ensuring that the engine receives the necessary fuel for combustion. However, if fuel lines are damaged or clogged, they can restrict fuel flow, leading to reduced engine performance and potentially causing overheating. This is because the engine may not receive enough fuel to maintain its ideal operating temperature, resulting in increased heat generation and potential engine damage. Understanding the impact of fuel lines on heat is crucial for maintaining a vehicle's performance and preventing costly repairs.
Characteristics | Values |
---|---|
Interference with Heat Transfer | The fuel line can interfere with the heat transfer process in a vehicle's engine. It may act as an insulator, reducing the efficiency of heat dissipation from the engine block to the cooling system. |
Material Impact | Different materials used for fuel lines can affect heat transfer. For example, rubber or plastic fuel lines might not conduct heat as efficiently as metal lines, potentially leading to localized overheating. |
Design and Placement | The design and placement of the fuel line can influence heat distribution. Proper routing and insulation can minimize interference, while incorrect placement may result in heat buildup. |
Engine Operating Conditions | Fuel line interference with heat can vary depending on engine load, speed, and temperature. Higher engine loads might exacerbate heat-related issues due to increased fuel flow and potential blockages. |
Maintenance and Condition | Regular maintenance, including checking for cracks, leaks, and proper insulation, is crucial to prevent fuel line-related heat interference. Age and wear can also impact heat transfer efficiency. |
What You'll Learn
- Fuel Line Placement: Proper positioning to avoid heat interference
- Insulation: Wrapping fuel lines to prevent heat transfer
- Engine Design: Optimizing engine layout to minimize fuel line exposure
- Temperature Control: Using heat shields to protect fuel lines
- Fuel Line Material: Choosing materials resistant to heat damage
Fuel Line Placement: Proper positioning to avoid heat interference
When it comes to vehicle maintenance, ensuring the proper placement of fuel lines is crucial, especially to prevent any potential interference with heat sources. The fuel line, a critical component in the fuel delivery system, can be susceptible to heat damage if not positioned correctly. This issue often arises in high-performance vehicles or those with modified engines, where heat management is a significant concern.
The primary goal is to maintain a safe distance between the fuel line and any heat-emitting components. Heat interference can lead to fuel line degradation, reduced fuel efficiency, and even potential fire hazards. To avoid these issues, it is essential to understand the optimal placement of the fuel line. One effective strategy is to route the fuel line away from areas with high temperatures, such as the exhaust manifold, catalytic converter, or engine block. By doing so, you minimize the risk of heat-induced damage.
In engine compartments, proper insulation and shielding are key. Insulating materials can be used to protect the fuel line from direct heat exposure. Additionally, ensuring that the fuel line is not in close proximity to any hot surfaces or components will significantly reduce the chances of interference. For instance, in some vehicles, the fuel line might be routed through a heat shield, providing an extra layer of protection.
Another important consideration is the flexibility of the fuel line. It should be able to move and adjust without being kinked or pinched, as this can restrict fuel flow and potentially cause heat buildup. Properly securing the fuel line with appropriate clamps or ties at regular intervals ensures it remains in an optimal position without being subjected to unnecessary stress.
Regular inspection and maintenance are vital to identifying and addressing any potential issues. Over time, fuel lines can deteriorate, and their ability to withstand heat may diminish. By keeping an eye on the fuel line's condition and ensuring it is correctly positioned, vehicle owners can avoid costly repairs and maintain optimal engine performance.
Kawasaki Brute Force 750 Fuel Line Sizing Guide
You may want to see also
Insulation: Wrapping fuel lines to prevent heat transfer
Insulating fuel lines is a crucial step in preventing heat transfer and maintaining the efficiency of your vehicle's fuel system. When fuel lines are exposed to high temperatures, they can expand and contract, leading to potential issues such as fuel leaks, reduced fuel pressure, and even engine damage. To mitigate these risks, it is essential to wrap the fuel lines with appropriate insulation materials.
The primary goal of insulation is to create a barrier between the fuel lines and the heat source, typically the engine or nearby hot components. This barrier helps to minimize the transfer of heat from the engine to the fuel lines, thus maintaining the fuel's stability and preventing unwanted reactions. Insulation also protects the fuel lines from physical damage, as it acts as a cushion against potential impacts or vibrations.
There are several materials that can be used for insulating fuel lines, each with its own advantages and disadvantages. One common choice is rubber or plastic insulation sleeves, which are flexible and easy to install. These sleeves provide a simple yet effective barrier against heat and can be cut to fit the specific length of the fuel line. Another option is to use specialized heat-resistant tape, which is often made from materials like aluminum foil or fiberglass. This type of tape offers excellent heat protection and can be wrapped tightly around the fuel lines for a secure fit.
When applying insulation, it is important to ensure complete coverage of the fuel lines. Start by cleaning the surface of the lines to remove any dirt or debris. Then, carefully wrap the insulation material around the fuel lines, making sure to overlap the layers slightly for added protection. Secure the insulation with tape or clips to prevent it from coming loose during vehicle operation. Regularly inspect the insulated areas for any signs of damage or wear and replace the insulation if necessary.
In addition to insulating the fuel lines, it is beneficial to consider the overall fuel system's design. Proper routing of fuel lines away from hot surfaces and using heat shields can further enhance the system's performance. By implementing these insulation techniques, you can effectively prevent heat transfer, ensuring the longevity and reliability of your vehicle's fuel system.
Honda XR50 Fuel Line: Understanding the OD and OEM Specs
You may want to see also
Engine Design: Optimizing engine layout to minimize fuel line exposure
When designing an engine, one crucial aspect often overlooked is the strategic placement of fuel lines to ensure optimal performance and longevity. The fuel lines, responsible for delivering gasoline to the engine's combustion chambers, can significantly impact the engine's overall efficiency and reliability. By optimizing the engine layout to minimize fuel line exposure to heat, engineers can enhance the engine's performance and reduce the risk of fuel-related issues.
In many engine designs, fuel lines are routed alongside the engine block or through the cylinder head, which can lead to several problems. Firstly, the proximity to hot engine components can cause the fuel to heat up, potentially leading to vaporization and reduced atomization during the combustion process. This results in less efficient fuel-air mixture and can negatively impact engine performance. Moreover, the heat from the engine can cause the fuel lines to expand and contract with temperature changes, leading to potential leaks or damage over time.
To address this issue, engineers should consider implementing a few design strategies. One approach is to route the fuel lines away from the hottest areas of the engine, such as the exhaust manifold and the cylinder head. By placing the fuel lines in a cooler region, the fuel remains at a more stable temperature, ensuring optimal combustion. Additionally, using flexible fuel lines with better heat resistance can help minimize the risk of damage due to temperature fluctuations.
Another effective method is to incorporate a fuel line insulation system. This involves wrapping the fuel lines with a heat-resistant material, such as ceramic or specialized insulation tape. By providing an insulating layer, the heat transfer from the engine to the fuel lines is significantly reduced, maintaining the fuel's temperature within an ideal range. This simple yet effective solution can improve engine performance and extend the lifespan of the fuel lines.
Furthermore, the use of fuel line protectors or shields can be beneficial. These protective covers can be made from materials like aluminum or heat-resistant plastic and are designed to fit around the fuel lines. By creating a barrier between the fuel lines and the hot engine components, these protectors minimize direct heat exposure, ensuring the fuel remains stable and efficient. This design consideration is particularly important in high-performance engines where fuel efficiency and reliability are critical.
In summary, optimizing engine layout to minimize fuel line exposure to heat is essential for enhancing engine performance and longevity. By implementing strategies such as routing fuel lines away from hot areas, using insulated materials, and incorporating protective covers, engineers can ensure that the fuel remains at an optimal temperature. These design considerations contribute to a more efficient and reliable engine, reducing the likelihood of fuel-related issues and improving overall engine health.
Mercury Outboard Fuel Line Sizing: 1992 150 HP Guide
You may want to see also
Temperature Control: Using heat shields to protect fuel lines
The concept of using heat shields to protect fuel lines is an important aspect of temperature control in various applications, especially in high-temperature environments. Fuel lines, which carry gasoline or diesel from the tank to the engine, are susceptible to damage from excessive heat, which can lead to reduced performance and potential safety hazards. Heat shields are designed to mitigate these risks by providing a protective barrier around the fuel lines.
In many vehicles, the fuel lines are routed through the engine compartment, where they are exposed to high temperatures from the engine, exhaust, and other heat sources. Over time, this exposure can cause the fuel lines to degrade, leading to potential fuel leaks, reduced engine performance, and even fire hazards. Heat shields offer a practical solution to this problem by encapsulating the fuel lines, thus preventing direct contact with hot surfaces.
These protective shields are typically made from materials with high-temperature resistance, such as stainless steel, aluminum, or heat-resistant polymers. The design and placement of the heat shield are crucial to its effectiveness. It should be securely mounted to ensure it remains in place, even under vibrations and temperature fluctuations. The shield's thickness and material properties should be sufficient to withstand the anticipated heat levels without compromising the fuel line's functionality.
One of the key advantages of using heat shields is their ability to maintain the integrity of the fuel lines, ensuring consistent fuel delivery to the engine. This is particularly important in high-performance vehicles or those operating in extreme conditions, where engine temperatures can soar. By protecting the fuel lines, heat shields contribute to the overall reliability and longevity of the vehicle's fuel system.
In summary, implementing heat shields as a temperature control measure is a practical and effective way to safeguard fuel lines from heat-related damage. This simple yet crucial component ensures the safe and efficient operation of fuel systems, especially in demanding environments. Proper installation and material selection are essential to achieving optimal protection, allowing fuel lines to function reliably without interference from heat.
Mastering Fuel Line Fixes: A Comprehensive Guide to Using Repair Kits
You may want to see also
Fuel Line Material: Choosing materials resistant to heat damage
When it comes to fuel lines in vehicles, the choice of material is crucial, especially in terms of heat resistance. Fuel lines are responsible for transporting gasoline or diesel from the tank to the engine, and they are exposed to various environmental conditions, including high temperatures. If the fuel lines are not made of materials that can withstand heat damage, it can lead to serious issues and potential safety hazards.
The primary concern with heat damage is the degradation of the fuel line's structural integrity. Over time, high temperatures can cause the material to become brittle, leading to cracks or even complete failure. This can result in fuel leaks, which are not only dangerous but also environmentally detrimental. Additionally, fuel leaks can cause engine misfires, reduced performance, and even potential fires if the fuel comes into contact with a spark or hot surface.
To ensure the longevity and reliability of fuel lines, it is essential to choose materials that offer excellent heat resistance. One of the most commonly used materials for fuel lines is steel, specifically a type known as "fuel-grade steel." This type of steel is designed to withstand the corrosive effects of fuel and the stresses caused by temperature fluctuations. It is known for its durability and ability to resist heat damage, making it an ideal choice for fuel lines.
Another material gaining popularity in the automotive industry is high-density polyethylene (HDPE). HDPE is a type of plastic that offers superior heat resistance compared to traditional materials like rubber. It can withstand higher temperatures without becoming brittle, making it less prone to cracking or leaking. HDPE fuel lines are also lightweight, flexible, and resistant to corrosion, making them a popular choice for modern vehicles.
When selecting fuel line material, it is crucial to consider the specific operating conditions of the vehicle. Factors such as engine power, ambient temperature, and the presence of other heat sources should be taken into account. Consulting the vehicle's manual or seeking advice from automotive experts can provide valuable insights into the recommended materials for fuel lines. By choosing the right material, vehicle owners can ensure the safety and efficiency of their fuel systems.
Fuel Line vs. Transmission Line: Which is More Rugged?
You may want to see also
Frequently asked questions
No, the fuel line itself does not directly interfere with the heat distribution. The primary function of the fuel line is to transport fuel from the tank to the engine, and it is designed to be a flexible component that allows for engine movement without restricting heat flow.
The fuel system plays a crucial role in engine temperature management. When the engine is running, the fuel injectors or carburetor spray fuel into the combustion chamber, where it mixes with air and ignites, producing power. The fuel system ensures the engine receives the correct amount of fuel, which helps maintain optimal operating temperatures.
A clogged fuel line can lead to engine overheating, but it is not a direct interference with heat distribution. Clogging can restrict fuel flow, causing the engine to run lean, which may result in increased engine temperatures. Additionally, a clogged fuel line can lead to poor fuel atomization, further exacerbating the overheating issue.
The position of the fuel line is generally not a significant factor in the engine's cooling system. The cooling system, including the radiator, coolant, and fans, is designed to maintain optimal engine temperatures regardless of the fuel line's placement. However, if the fuel line is positioned near the radiator or in a location that restricts airflow, it might indirectly impact cooling efficiency.
The location of the fuel pump is important to consider when discussing engine heat. If the fuel pump is located near the engine block, it can help dissipate heat, keeping the engine cooler. However, if the fuel pump is positioned in a confined space or away from the engine, it may generate additional heat, which could affect the overall engine temperature. Proper ventilation and heat management around the fuel pump are essential to prevent overheating.