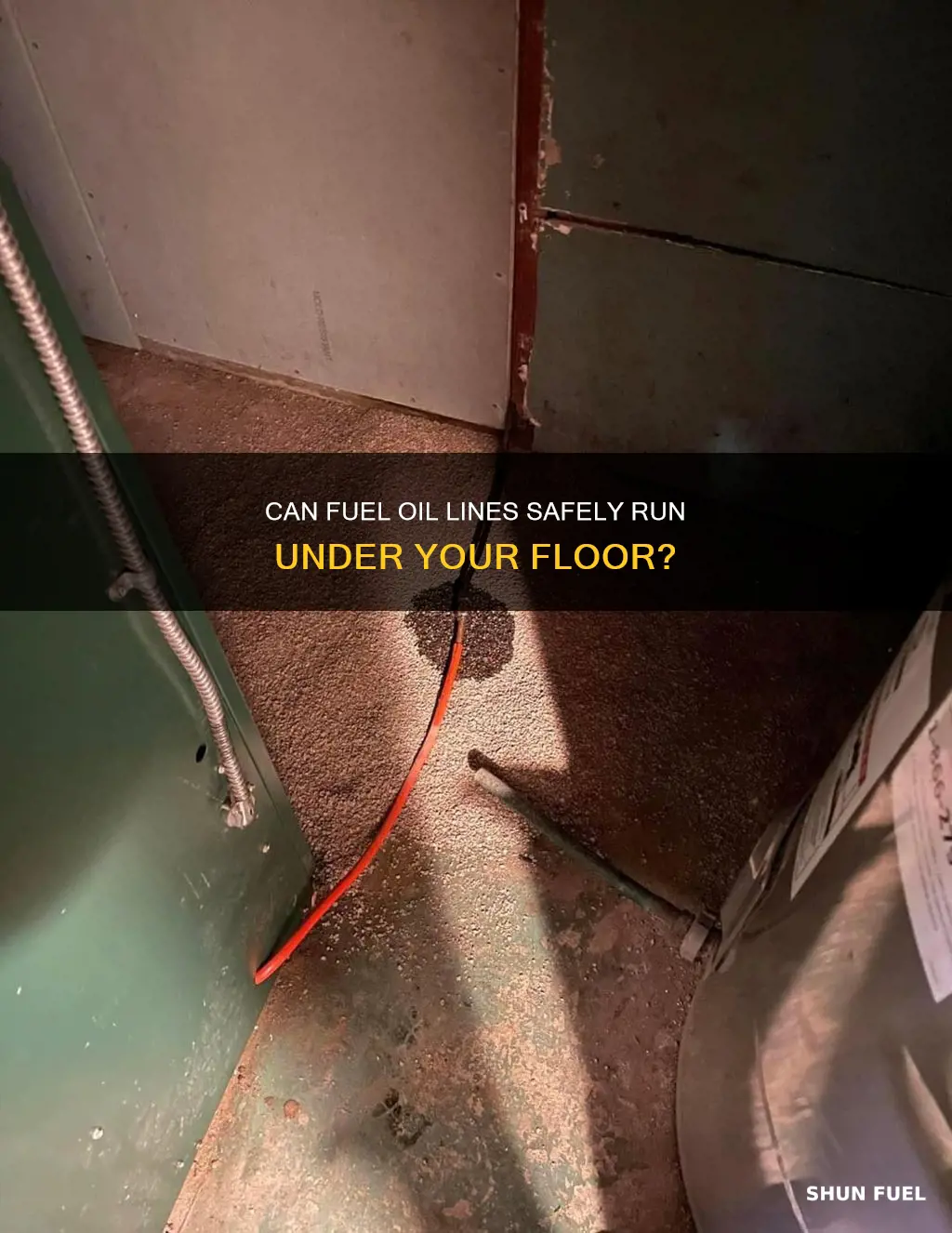
When considering the installation of fuel oil lines, a common question arises: can fuel oil lines go under the floor? This is a crucial aspect of any fuel oil system, especially in residential settings, as it directly impacts safety and maintenance. Understanding the proper placement of these lines is essential to ensure the efficient and safe operation of the system, preventing potential hazards and costly repairs. The following discussion will explore the considerations and best practices for placing fuel oil lines under the floor, addressing key factors such as insulation, protection, and compliance with building codes.
What You'll Learn
- Safety: Fuel oil lines under floors pose risks; proper installation and maintenance are crucial
- Regulations: Local building codes may require specific standards for fuel oil lines in floors
- Materials: Choose appropriate materials for fuel oil lines to withstand floor conditions
- Ventilation: Ensure adequate ventilation to prevent gas buildup and potential hazards
- Inspections: Regular inspections can identify issues with fuel oil lines under floors
Safety: Fuel oil lines under floors pose risks; proper installation and maintenance are crucial
The idea of running fuel oil lines under a floor might seem like a discreet and efficient way to transport fuel, but it actually presents a multitude of safety risks that cannot be overlooked. These risks are primarily associated with the potential for leaks, which can have severe consequences. Fuel oil is a highly flammable substance, and any leak, no matter how small, can quickly escalate into a dangerous situation. The floor, being a solid structure, provides no natural barrier to contain a spill, meaning that any leak could spread rapidly and potentially damage the surrounding area and pose a fire hazard. Furthermore, the tight spaces under floors can make it difficult to detect and repair leaks, as they may go unnoticed until significant damage has occurred.
Proper installation is the first line of defense against these risks. Fuel oil lines should be carefully planned and installed by qualified professionals who are familiar with the specific requirements and regulations for fuel oil systems. This includes using the correct type of pipe and ensuring that all connections are secure and leak-tight. The pipes should be positioned in a way that allows for easy access during maintenance and inspections, as regular checks are essential to identify and rectify any potential issues before they become major problems.
Maintenance is another critical aspect of ensuring the safety of fuel oil systems. Regular inspections should be conducted to check for any signs of wear, corrosion, or damage to the lines. This is particularly important in areas where the lines are exposed to moisture or where there is a risk of physical impact, such as in busy households or commercial settings. Any issues found during these inspections should be addressed promptly to prevent further deterioration and potential leaks.
In addition to installation and maintenance, it is also important to be aware of the signs of a potential leak. These can include a strong, distinct smell of fuel, discolouration or moisture on the floor, or a sudden drop in the fuel level in the tank. If any of these signs are noticed, immediate action should be taken, such as contacting a professional to inspect and repair the system.
In summary, while it might be tempting to hide fuel oil lines under floors to save space, the potential risks far outweigh any perceived benefits. Proper installation and regular maintenance are essential to ensure the safety of the system and those around it. By being proactive and addressing any issues promptly, the likelihood of a major accident can be significantly reduced.
Locate the Fuel Line: A Guide to Craftsman Chain Saw Maintenance
You may want to see also
Regulations: Local building codes may require specific standards for fuel oil lines in floors
When it comes to installing fuel oil lines in residential or commercial buildings, local building codes and regulations play a crucial role in ensuring safety and compliance. These codes are designed to protect occupants and the environment, especially in areas where fuel oil is used for heating. One specific aspect that often requires careful consideration is the placement of fuel oil lines within the building's floor structure.
Local building codes may mandate specific standards for fuel oil lines running through floors to prevent potential hazards and ensure proper maintenance. These regulations are in place to address concerns such as fire safety, leak detection, and the overall integrity of the building's infrastructure. For instance, some jurisdictions might require that fuel oil lines be installed in a manner that minimizes the risk of damage or disruption to the floor's structural integrity. This could involve using appropriate insulation or protective materials to safeguard the lines from potential impacts or vibrations.
In certain regions, building codes may specify that fuel oil lines must be placed in a specific depth or location within the floor. This is often done to ensure that the lines are not easily accessible, reducing the risk of accidental damage or unauthorized access. By requiring these standards, local authorities aim to prevent potential leaks or spills that could lead to environmental contamination or health hazards. Proper placement also facilitates easier maintenance and inspection, allowing technicians to work on the lines without causing significant disruption to the building's occupants.
Compliance with these regulations is essential for both new construction projects and existing buildings undergoing renovations. Building owners and contractors must carefully review the local building code requirements to ensure that fuel oil lines are installed or modified according to the specified standards. Failure to adhere to these guidelines can result in legal consequences, including fines or even the requirement to rectify the non-compliance at the expense of the responsible party.
Understanding and following local building codes for fuel oil lines in floors is vital for maintaining a safe and efficient heating system while adhering to legal requirements. It is recommended that building professionals and homeowners consult the relevant local regulations to ensure that their fuel oil installations meet the necessary safety and structural standards.
Signs of a Clogged Fuel Line: What to Look For
You may want to see also
Materials: Choose appropriate materials for fuel oil lines to withstand floor conditions
When it comes to installing fuel oil lines under floors, choosing the right materials is crucial to ensure safety, efficiency, and longevity. The floor environment can present unique challenges, including moisture, temperature fluctuations, and potential physical damage. Here's a detailed guide on selecting appropriate materials:
- PVC (Polyvinyl Chloride): PVC is a popular choice for fuel oil lines due to its excellent resistance to chemicals, moisture, and abrasion. It is a lightweight and flexible material, making it easy to install and maneuver through tight spaces. Look for high-density PVC, often referred to as HDPE or uPVC, which offers superior durability and is less susceptible to cracking over time. This material is commonly used in underground applications and can withstand the harsh conditions often found beneath floors.
- HDPE (High-Density Polyethylene): HDPE is another robust option, known for its impact resistance and ability to handle both hot and cold temperatures. It is less flexible than PVC but provides excellent chemical resistance, making it ideal for fuel oil lines. HDPE is often used in underground plumbing and can be buried without the risk of degradation. Its durability ensures that the fuel oil lines will remain intact even in challenging floor conditions.
- Stainless Steel: For applications requiring the highest level of durability and corrosion resistance, stainless steel is an excellent choice. This material is ideal for fuel oil lines in areas with high moisture content or where there is a risk of chemical exposure. Stainless steel is known for its strength and ability to withstand extreme temperatures, making it a reliable option for long-term use. However, it is more expensive and less flexible than PVC or HDPE, so careful consideration of the installation environment is necessary.
- Consider the Floor Material: Different floor materials may require specific considerations. For example, if the floor is made of concrete, ensure that the chosen material can adhere well to the concrete surface. Some materials may require a primer or specific installation techniques to ensure a secure bond. Additionally, consider the potential for moisture in the floor, especially if it is a basement or crawl space, and select materials with excellent water resistance.
- Insulation and Protection: Depending on the floor conditions, you might need to add insulation or protective layers to the fuel oil lines. For cold floors, insulation can help maintain the temperature of the fuel oil, preventing freezing. In areas with potential physical hazards, consider using protective sleeves or jackets to shield the lines from damage. This additional layer of protection ensures the longevity of the installation.
Choosing the Right Size: Steel Fuel Line for Your 1000cc Engine
You may want to see also
Ventilation: Ensure adequate ventilation to prevent gas buildup and potential hazards
Ventilation is a critical aspect of any fuel oil system, especially when considering the placement of fuel oil lines under floors. Inadequate ventilation can lead to a dangerous buildup of fuel vapor, which poses significant health and safety risks. When fuel oil lines are installed beneath floors, the confined space can trap and accumulate fuel vapor, creating a hazardous environment. This is particularly concerning as fuel vapor is highly flammable and can easily ignite, leading to fires or explosions.
To prevent such hazards, it is essential to ensure that the ventilation system is properly designed and installed. The primary goal is to facilitate the rapid dispersion of fuel vapor and other potentially harmful gases. This can be achieved through the use of exhaust fans, vents, and properly sized ventilation ducts. These components work together to create a continuous flow of air, pulling in fresh air and expelling the accumulated fuel vapor and other contaminants.
One effective method is to install a dedicated ventilation system specifically designed for fuel oil applications. This system should include a powerful exhaust fan that can quickly remove the fuel vapor and other gases from the confined space. The fan should be connected to a network of ventilation ducts that are strategically placed to ensure optimal air circulation. Additionally, consider using a mechanical ventilation system that is automatically controlled, ensuring that the ventilation process is consistent and reliable.
Another important aspect is the placement of vents. Vents should be positioned at regular intervals along the fuel oil line, allowing for the release of accumulated gases. These vents should be designed to handle the specific challenges of fuel oil ventilation, such as the potential for high-pressure gas buildup. Properly sized vents will ensure that the gas is released efficiently without causing any damage to the surrounding structure.
Furthermore, it is crucial to regularly maintain and inspect the ventilation system. Over time, vents and ducts can become blocked or damaged, compromising their effectiveness. Regular cleaning and inspection can help identify and rectify any issues, ensuring that the ventilation system remains efficient and reliable. By taking these preventive measures, you can significantly reduce the risks associated with fuel oil lines installed under floors.
Boat Fuel Line Length: When Too Much Can Be a Problem
You may want to see also
Inspections: Regular inspections can identify issues with fuel oil lines under floors
Regular inspections of fuel oil lines running under floors are crucial for maintaining a safe and efficient heating system. Over time, these lines can develop various issues that may go unnoticed without proper examination. One of the primary reasons for conducting these inspections is to identify potential problems early on, preventing costly repairs or replacements.
During an inspection, it is essential to look for any signs of damage, corrosion, or leaks. Fuel oil lines are susceptible to wear and tear due to their position beneath the floor, where they may be exposed to moisture, pests, or physical damage from foot traffic or construction. Inspectors should carefully examine the lines for any visible cracks, holes, or discolouration, which could indicate internal damage or the presence of contaminants. Additionally, checking for any signs of moisture or water intrusion around the line is vital, as this could lead to corrosion and reduced line integrity.
Another critical aspect of the inspection process is to verify the proper installation and securement of the fuel oil lines. Over time, lines may become loose or disconnected, leading to potential safety hazards and reduced efficiency. Inspectors should ensure that all connections are tight and secure, using the appropriate tools and techniques to make any necessary adjustments. Properly secured lines reduce the risk of leaks and ensure optimal fuel flow to the heating system.
Furthermore, regular inspections allow for the identification of any blockages or clogs that may have formed within the fuel oil lines. These blockages can occur due to sediment buildup, debris, or the presence of contaminants in the fuel. By clearing these obstructions, the system can operate efficiently, ensuring consistent heat output and potentially reducing fuel consumption. It is recommended to use specialized cleaning tools and techniques to remove blockages without causing further damage to the lines.
In summary, regular inspections of fuel oil lines under floors are essential for maintaining a safe and efficient heating system. These inspections help identify damage, corrosion, leaks, improper installation, and blockages, allowing for timely repairs or replacements. By prioritizing these maintenance tasks, homeowners can ensure the longevity and reliability of their fuel oil heating systems.
Fuel Line Size for Predator Generators: A Quick Guide
You may want to see also
Frequently asked questions
Running a fuel oil line under the floor can be risky and is generally not recommended. The line could be damaged by foot traffic, furniture, or other objects, leading to potential leaks and safety hazards. It's best to keep fuel lines above ground and well-protected to ensure the safety of your home and family.
The main concern is the risk of leaks. Over time, the line could develop cracks or be damaged, leading to fuel spills. These spills can cause environmental damage, health hazards, and even fires. Additionally, the line might be difficult to access for maintenance or repairs, making it challenging to address issues promptly.
Yes, many building codes and regulations have specific guidelines regarding the installation of fuel lines. These codes often require fuel lines to be above ground and properly insulated to prevent leaks. It's essential to consult local building codes and ensure your fuel line installation complies with these standards to avoid legal issues and potential dangers.
When installing a fuel oil line, it's crucial to follow best practices for safety. Use appropriate insulation and protective materials to safeguard the line from potential impacts. Keep the line above ground, away from high-traffic areas, and ensure it is properly vented to prevent the buildup of dangerous gases. Regular maintenance and inspections can also help identify and address any issues promptly.