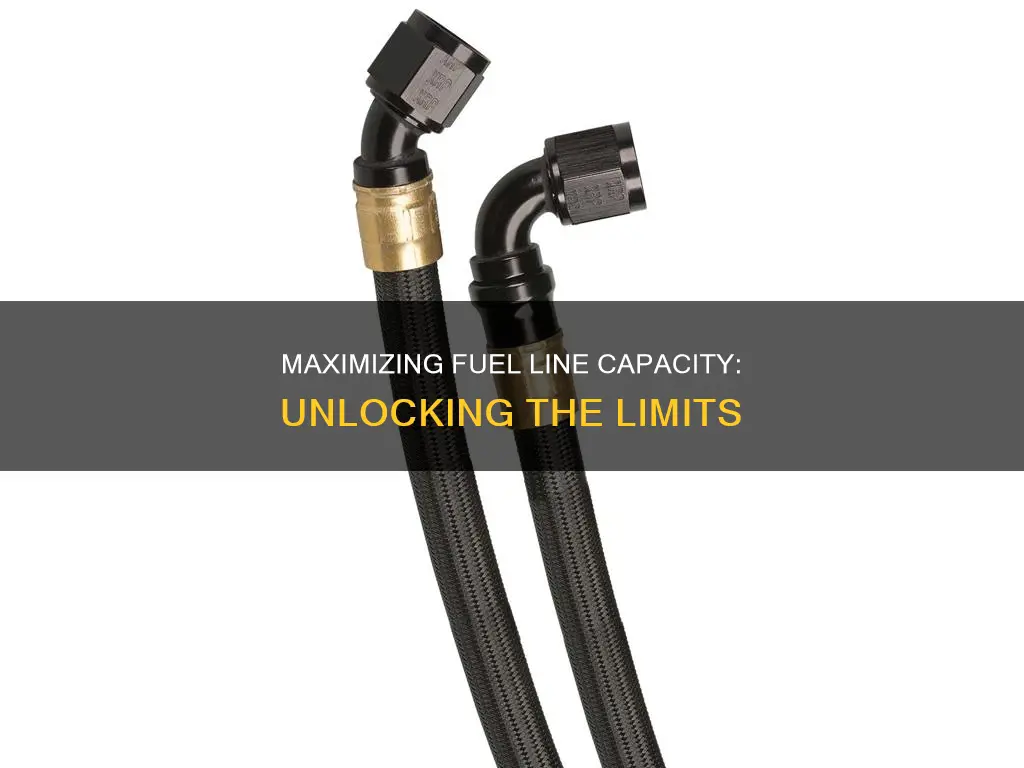
The capacity of a fuel line to store fuel is a critical aspect of vehicle performance and safety. Understanding the factors that determine how much time a fuel line can hold fuel is essential for optimizing fuel efficiency, ensuring reliable operation, and maintaining the overall health of a vehicle's engine. This paragraph will explore the various elements that influence the duration a fuel line can retain fuel, including the line's material, diameter, length, and the specific requirements of different vehicle models. By delving into these factors, we can gain valuable insights into the intricate relationship between fuel lines and fuel retention, ultimately contributing to more informed decisions in vehicle maintenance and design.
Characteristics | Values |
---|---|
Typical fuel line lifespan | 5-10 years |
Factors affecting lifespan | Material quality, temperature fluctuations, fuel type, maintenance |
Common causes of failure | Cracks, leaks, corrosion, excessive pressure |
Maintenance tips | Regular inspections, replacing old lines, using fuel stabilizers |
Replacement cost | Varies by vehicle model and fuel line length |
What You'll Learn
Fuel Line Capacity: Maximum Volume Before Pressure Build-Up
The capacity of a fuel line, in terms of the volume it can hold before pressure build-up occurs, is a critical factor in vehicle performance and safety. When a fuel line is filled, the fuel must be able to flow efficiently without causing excessive pressure in the system. This pressure can lead to several issues, including engine misfires, reduced performance, and even potential safety hazards. Understanding the maximum volume a fuel line can hold before pressure build-up is essential for maintaining optimal engine operation.
The time a fuel line can hold a certain volume of fuel before pressure increases is directly related to the design and specifications of the fuel line itself. Different fuel lines have varying capacities, often determined by their internal diameter, length, and material composition. For instance, a larger diameter fuel line can typically hold more fuel before pressure starts to rise. This is because a wider diameter provides a greater cross-sectional area for fuel flow, allowing for a higher volume of fuel to pass through without causing a significant pressure increase.
The material of the fuel line also plays a crucial role in its capacity. Some materials, like high-density polyethylene (HDPE) or polyvinyl chloride (PVC), are known for their ability to withstand higher pressures and temperatures, making them suitable for fuel lines. These materials can often handle larger volumes of fuel before pressure build-up occurs. In contrast, other materials may have lower pressure resistance and, therefore, a smaller capacity.
It's important to note that the time a fuel line can hold a specific volume of fuel is not just about the physical capacity but also the rate at which the fuel is being filled. If the fuel is being added to the line at a rapid rate, the pressure can increase more quickly, even if the line has a larger capacity. This is why it's recommended to fill fuel tanks at a moderate pace to avoid putting excessive pressure on the fuel line.
In summary, the maximum volume a fuel line can hold before pressure build-up is a critical consideration for vehicle maintenance. Factors such as the fuel line's diameter, length, material, and the rate at which fuel is added all contribute to its capacity. Understanding these factors can help ensure that the fuel system operates efficiently and safely, providing optimal performance for the vehicle.
Chevy Cobalt Fuel Lines: A Comprehensive Guide
You may want to see also
Fuel Line Material: Impact on Volume and Durability
The material composition of a fuel line plays a critical role in determining its volume capacity and overall durability. Different materials offer varying levels of flexibility, strength, and resistance to fuel-related degradation, all of which influence how much fuel a line can hold and transport over time. For instance, rubber fuel lines are commonly used due to their inherent flexibility, making them suitable for accommodating engine vibrations and movement. However, rubber's inherent properties can lead to swelling and degradation when exposed to fuel over extended periods, potentially reducing its volume capacity and overall lifespan.
In contrast, synthetic rubber, such as neoprene or EPDM, offers improved resistance to fuel-related degradation, making it a more durable option for fuel lines. These materials are less prone to swelling and are more resistant to the corrosive effects of fuel, ensuring that the fuel line can maintain its volume and structural integrity over a longer period. Additionally, synthetic rubber fuel lines often feature a braided design, providing enhanced flexibility and durability, further contributing to their longevity.
Another critical factor is the inner lining of the fuel line. Some materials, like vinyl or nitrile, are used for their ability to provide a protective barrier between the fuel and the outer material. This lining helps prevent fuel-related degradation and maintains the structural integrity of the fuel line, ensuring that it can hold and transport fuel effectively over time. The choice of inner lining material is crucial, as it directly impacts the fuel line's ability to withstand the corrosive nature of fuel and maintain its volume capacity.
Furthermore, the thickness and construction of the fuel line material also play a significant role in its volume capacity and durability. Thicker fuel lines generally offer increased resistance to fuel-related degradation and can hold more fuel. However, thicker lines may also be more rigid, which could impact their flexibility and ability to accommodate engine vibrations. Finding the right balance between thickness and flexibility is essential to ensure the fuel line can effectively manage fuel volume while maintaining its structural integrity.
In summary, the material composition of a fuel line significantly influences its volume capacity and durability. Synthetic rubbers, braided designs, and protective inner linings contribute to improved resistance to fuel-related degradation. Additionally, the thickness and construction of the fuel line material must be carefully considered to ensure a balance between volume capacity and flexibility. By selecting the appropriate material, engineers can design fuel lines that effectively manage fuel volume while ensuring long-lasting performance.
Bobcat Engine Issues: Leaking Return Fuel Line Concerns
You may want to see also
Fuel Line Length: Effect on Holding Capacity and Flow
The length of a fuel line is a critical factor in determining its ability to hold and deliver fuel efficiently. The capacity of a fuel line to hold fuel is directly related to its length, and this relationship is governed by the principles of fluid dynamics and the physical properties of the fuel itself. When considering the holding capacity of a fuel line, it's essential to understand that the longer the line, the more fuel it can accommodate. This is because the volume of a cylindrical object, such as a fuel line, increases with its length. As a result, a longer fuel line can hold more fuel, which is particularly important in applications where fuel needs to be transported over extended distances or stored for later use.
The flow rate of fuel through a line is another critical aspect influenced by its length. The flow rate refers to the volume of fuel that passes through the line per unit of time. When fuel flows through a line, it encounters resistance due to the line's internal surface and the pressure differences along its length. The longer the fuel line, the greater the resistance to flow, which can lead to a decrease in the overall flow rate. This is a crucial consideration, especially in high-performance applications where maintaining optimal fuel delivery is essential for efficient engine operation.
To optimize the performance of a fuel system, it is essential to strike a balance between the length of the fuel line and the desired flow rate. Engineers and designers often use calculations and simulations to determine the optimal length of the fuel line for a specific application. This involves considering factors such as fuel pressure, line diameter, and the required flow rate to ensure that the fuel line can efficiently hold and deliver the necessary amount of fuel without excessive pressure drops or flow restrictions.
In practice, fuel lines are often designed with a specific length to accommodate the fuel requirements of a particular vehicle or machine. For example, in automotive applications, fuel lines are carefully selected to ensure that the engine receives the required amount of fuel at the right pressure and flow rate. Longer fuel lines might be used in off-road vehicles or aircraft, where fuel tanks are located remotely from the engine, requiring extended lines to deliver fuel efficiently.
In summary, the length of a fuel line significantly impacts its holding capacity and flow rate. Longer fuel lines can hold more fuel, which is advantageous for certain applications, but they also introduce flow resistance, which can be managed through careful design and selection of line materials. Understanding these relationships is crucial for engineers and designers to create efficient fuel systems that meet the specific demands of various vehicles and machinery.
Craftsman Fuel Line Sizes: A Guide to the Perfect Fit
You may want to see also
Fuel Line Diameter: Relationship to Volume and Pressure
The diameter of a fuel line is a critical factor in determining its capacity to hold and deliver fuel efficiently. The relationship between fuel line diameter, volume, and pressure is a fundamental concept in fluid dynamics and is essential for optimizing fuel systems in various applications, from automotive to aviation.
When considering the volume of a fuel line, it is important to understand that the cross-sectional area of the line is directly proportional to its diameter. This means that as the diameter increases, the cross-sectional area also increases, allowing for a greater volume of fuel to pass through the line. For example, if you double the diameter of a fuel line, you will quadruple the cross-sectional area, enabling the line to carry four times the volume of fuel at a given pressure. This relationship is described by the formula: Volume = Cross-sectional Area × Velocity. Here, the velocity of the fuel flow is also influenced by the diameter, as a larger diameter provides a smoother flow, reducing the likelihood of turbulence and pressure drops.
Pressure is another critical aspect affected by fuel line diameter. According to the principles of fluid mechanics, the pressure drop across a pipe or fuel line is inversely proportional to its diameter. This means that a larger diameter fuel line will experience a lower pressure drop over the same length compared to a smaller diameter line. This is particularly important in fuel systems where maintaining consistent pressure is crucial for efficient combustion. A fuel line with a larger diameter can accommodate higher flow rates without significant pressure loss, ensuring that the fuel reaches the engine or combustion chamber at the desired pressure.
The relationship between volume and pressure in a fuel line is also influenced by the material and design of the line. Different materials have varying flow characteristics, and the design, including bends and fittings, can impact the flow dynamics. For instance, a fuel line with a larger diameter might be more susceptible to vibration-induced pulsations, which can affect pressure stability. Therefore, when selecting the diameter, it is essential to consider the overall system design and the specific requirements of the fuel application.
In summary, the diameter of a fuel line plays a pivotal role in determining its ability to hold and deliver fuel effectively. A larger diameter increases the volume capacity and reduces pressure drops, ensuring a steady and efficient fuel supply. Understanding this relationship is vital for engineers and designers to optimize fuel systems, ensuring reliable performance and compliance with the demands of various fuel-powered applications.
Hose Clamps on Fuel Lines: A Practical Guide
You may want to see also
Fuel Line Temperature: Influence on Volume and Flexibility
The temperature of a fuel line plays a critical role in determining its ability to hold and deliver fuel efficiently. This is particularly important in automotive applications, where fuel lines are responsible for transporting gasoline or diesel from the tank to the engine. The volume of fuel a line can hold and its flexibility are directly influenced by temperature, which can vary significantly depending on the environment and operating conditions.
At lower temperatures, fuel lines tend to contract, reducing their internal volume. This contraction can lead to a decrease in the line's capacity to hold fuel, potentially causing fuel starvation during cold starts or when the engine is idling. Additionally, the reduced volume may result in a higher pressure drop, requiring a more powerful pump to maintain adequate fuel flow. In extreme cases, the fuel line might not be able to hold enough fuel, leading to engine performance issues.
On the other hand, higher temperatures can cause fuel lines to expand, increasing their internal volume. This expansion can be beneficial as it allows the line to hold more fuel, which is advantageous during prolonged engine operation or when the vehicle is stationary in hot environments. However, excessive expansion can also lead to issues. The increased volume may cause the line to become less flexible, making it more susceptible to damage from vibrations or sharp bends. This flexibility is crucial to ensure the fuel line can navigate the engine's complex layout without kinking or breaking.
The temperature-volume relationship is further complicated by the fuel's own thermal expansion properties. Different fuels have varying coefficients of thermal expansion, meaning they will expand or contract by different amounts when exposed to temperature changes. This can lead to uneven pressure distribution within the fuel line, potentially causing damage over time. For instance, ethanol-blended fuels tend to expand more than conventional gasoline, requiring fuel lines with higher flexibility and volume capacity.
In summary, the temperature of a fuel line significantly impacts its volume and flexibility, which are essential factors in determining the line's ability to hold and deliver fuel effectively. Engineers and designers must consider these temperature-induced changes to ensure optimal engine performance and longevity, especially in diverse environmental conditions. Understanding these relationships is crucial for selecting the appropriate fuel line materials and dimensions for specific applications.
Choosing the Right Size: Steel Fuel Line for Your 1000cc Engine
You may want to see also
Frequently asked questions
The lifespan of a fuel line can vary depending on several factors, including the type of fuel line, its material, the operating conditions, and maintenance practices. Generally, a well-maintained fuel line can last for many years without significant issues. However, it is recommended to inspect the fuel lines regularly for any signs of wear, cracks, or leaks. If the fuel lines show signs of damage or deterioration, they should be replaced to prevent potential fuel leaks and ensure optimal engine performance.
Fuel line failure can occur due to several reasons. Some common causes include:
- Age and wear: Over time, fuel lines can degrade due to exposure to fuel, heat, and vibration, leading to cracks or leaks.
- Contamination: Fuel lines can become contaminated with water, dirt, or other impurities, causing corrosion or blockages.
- Mechanical damage: Fuel lines may be damaged by sharp edges, rodents, or other mechanical forces, resulting in punctures or tears.
- Poor installation: Incorrect installation or improper use of fuel lines can lead to premature failure.
Yes, early detection of fuel line issues is crucial to prevent major problems. Some signs that may indicate fuel line issues include:
- Engine misfires or poor performance: If the engine starts to misfire, lose power, or have difficulty starting, it could be due to a clogged or damaged fuel line.
- Strange noises: Hissing or roaring sounds near the fuel tank or engine may indicate a fuel line leak.
- Fuel leaks: Any visible signs of fuel leaking from the fuel lines or connections should be addressed immediately.
- Engine stalling: If the engine stalls frequently, it might be due to insufficient fuel supply caused by a faulty fuel line.
Preventive measures can help minimize the risk of fuel line issues. Here are some tips:
- Regular maintenance: Schedule routine inspections and maintenance checks to identify and address any potential issues.
- Use high-quality fuel: Ensure that you use clean and high-quality fuel to prevent contamination.
- Protect against mechanical damage: Park your vehicle in a safe location, away from sharp objects or potential collision risks.
- Proper installation: If replacing fuel lines, ensure professional installation or follow manufacturer guidelines for correct assembly.