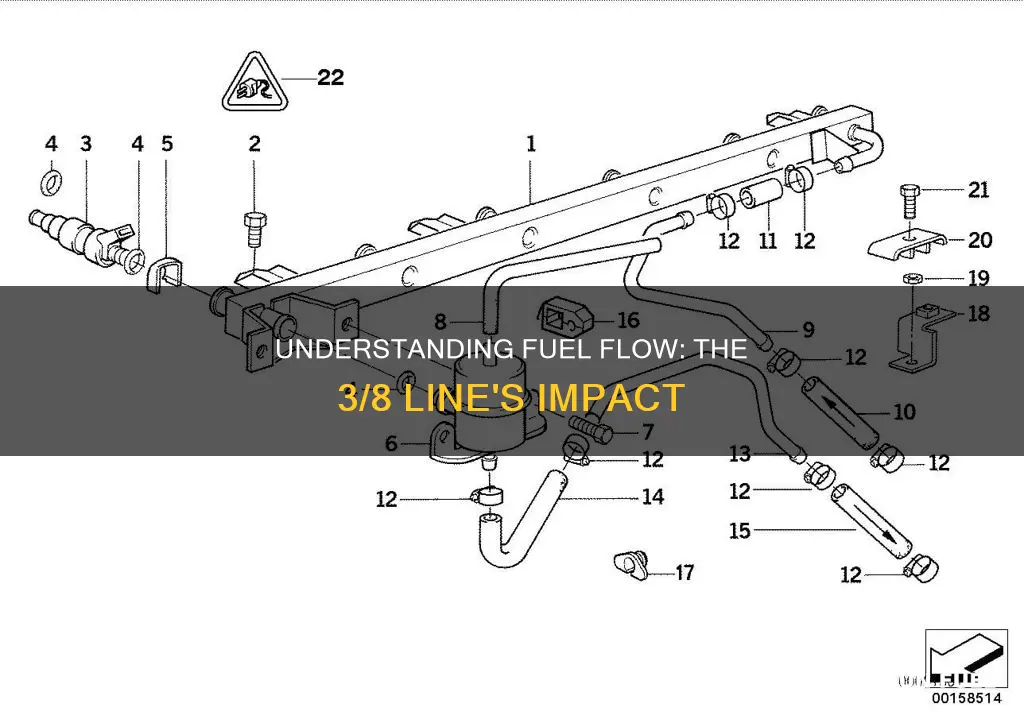
How much fuel can pass through a 3/8-inch line? This question delves into the capacity of a specific-sized fuel line, which is crucial in various applications, from automotive to industrial settings. Understanding the flow rate and volume of fuel through such a line is essential for optimizing performance, ensuring safety, and maintaining efficiency in fuel-dependent operations. The answer to this query can provide valuable insights for engineers, technicians, and anyone involved in fuel management and distribution systems.
What You'll Learn
- Fuel Flow Rate: Calculate the rate of fuel passing through a 3/8-inch line
- Pressure Drop: Understand how pressure affects fuel flow in a 3/8-inch line
- Line Diameter: Determine fuel flow based on the 3/8-inch line's diameter
- Temperature Impact: Explore how temperature changes affect fuel flow through a 3/8-inch line
- Flow Control: Learn methods to regulate fuel flow in a 3/8-inch line
Fuel Flow Rate: Calculate the rate of fuel passing through a 3/8-inch line
To calculate the fuel flow rate through a 3/8-inch line, you need to understand the concept of flow rate and the factors that influence it. The flow rate is essentially the volume of fuel passing through a given area per unit of time. In this case, we're dealing with a specific diameter of the line, which is 3/8 inches.
The first step is to determine the cross-sectional area of the 3/8-inch line. The formula for the area of a circle (which is the shape of the line's cross-section) is A = π * (d/2)^2, where 'd' is the diameter of the circle. For a 3/8-inch line, the diameter is 0.375 inches. Plugging this into the formula, you get A = π * (0.375/2)^2 = approximately 0.0707 square inches. This is the area through which the fuel is flowing.
Next, you need to consider the pressure and temperature of the fuel, as these factors can significantly impact the flow rate. The fuel's viscosity, which is a measure of its resistance to flow, also plays a crucial role. Higher pressure and lower viscosity generally result in a higher flow rate. You can use the Darcy-Weisbach equation to estimate the pressure drop across the line and then calculate the flow rate based on the pressure, temperature, and viscosity of the fuel.
Additionally, the length of the line and the fuel's density should be taken into account. Longer lines or higher fuel densities may require adjustments to your calculations. Once you have all the necessary data, you can use the formula Q = A * (P1 - P2) / (ρ * g * L), where Q is the flow rate, A is the cross-sectional area, P1 and P2 are the pressures at the start and end of the line, ρ is the fuel density, g is the acceleration due to gravity, and L is the length of the line.
Remember, these calculations provide an estimate and may require further refinement depending on the specific application and environmental conditions. It's essential to consider the unique characteristics of the fuel and the system in which it is being used to ensure accurate and safe operation.
Understanding Saturn Fuel Line Inner Diameter: A Comprehensive Guide
You may want to see also
Pressure Drop: Understand how pressure affects fuel flow in a 3/8-inch line
The flow of fuel through a 3/8-inch line is a critical aspect of engine performance and efficiency, and understanding pressure drop is essential to optimizing this process. When fuel is supplied to an engine via a narrow line, it encounters resistance, which is directly related to the pressure drop across the line. This phenomenon is a result of the fuel's tendency to flow more easily in areas of lower pressure, creating a pressure gradient that drives the fuel through the system.
In a 3/8-inch line, the pressure drop is a significant factor because the small diameter restricts the flow. As fuel moves through the line, it experiences a pressure decrease, which can lead to several issues. Firstly, a higher pressure drop may result in reduced fuel flow, affecting the engine's performance and power output. This is particularly critical in high-performance applications where every drop of fuel matters. Secondly, excessive pressure drop can cause fuel to vaporize, especially at higher temperatures, leading to potential engine misfires and reduced combustion efficiency.
To manage pressure drop, engineers employ various strategies. One approach is to use fuel injectors with precise flow control, ensuring that the fuel exits the injector at the desired rate, compensating for any pressure variations. Another method is to incorporate pressure regulators, which maintain a consistent pressure throughout the system, minimizing the pressure drop across the 3/8-inch line. These regulators are designed to adjust the fuel pressure based on engine load, ensuring optimal performance across different operating conditions.
Additionally, the material and design of the fuel line play a role in managing pressure drop. Lines made from materials with low-friction coefficients, such as certain plastics or specialized coatings, can reduce internal friction, allowing fuel to flow more freely. The line's design should also consider minimizing sharp bends and kinks, as these can create localized pressure increases, further exacerbating the pressure drop issue.
In summary, understanding and managing pressure drop in a 3/8-inch fuel line is crucial for maintaining engine performance and efficiency. By employing appropriate design considerations, such as precise fuel injectors and pressure regulators, and choosing suitable materials, engineers can ensure that fuel flows optimally through these lines, delivering the required power and responsiveness in various engine applications.
Volvo VNL Fuel Line Sizing: Expert Guide
You may want to see also
Line Diameter: Determine fuel flow based on the 3/8-inch line's diameter
When considering the flow of fuel through a 3/8-inch line, it's essential to understand the relationship between the line's diameter and the fuel's flow rate. The diameter of the line plays a crucial role in determining how much fuel can pass through it in a given time. A 3/8-inch line, with a diameter of 0.375 inches, offers a specific cross-sectional area that influences the fuel's velocity and volume.
The flow rate of fuel is directly proportional to the cross-sectional area of the line. In this case, a 3/8-inch line provides a relatively small cross-sectional area compared to larger lines. As a result, the fuel flow rate through this line will be lower than that of a larger diameter line. This is because the smaller area restricts the amount of fuel that can pass through simultaneously.
To calculate the fuel flow, you can use the formula: Flow Rate (Q) = A * V, where A is the cross-sectional area and V is the velocity of the fuel. For a 3/8-inch line, the cross-sectional area (A) can be calculated using the formula for the area of a circle: A = π * (d/2)^2, where d is the diameter. Plugging in the value of 0.375 inches for the diameter, you can find the area and then use it to determine the flow rate.
It's important to note that the flow rate is also influenced by the pressure and viscosity of the fuel. Higher pressure and lower viscosity will generally allow for a higher flow rate through the 3/8-inch line. However, the line's diameter remains a critical factor in this calculation.
Understanding the relationship between line diameter and fuel flow is crucial in various applications, such as fuel injection systems in engines or fluid distribution networks. By considering the diameter of the 3/8-inch line, engineers and technicians can design and optimize systems to ensure efficient and controlled fuel delivery.
Onan Genset Fuel Line: One-Way Valve Mystery Solved
You may want to see also
Temperature Impact: Explore how temperature changes affect fuel flow through a 3/8-inch line
Temperature plays a critical role in determining the flow rate of fuel through a 3/8-inch line, and understanding its impact is essential for optimizing fuel delivery systems. When the temperature of the fuel and the surrounding environment changes, it directly affects the pressure and density of the fuel, which in turn influences its flow characteristics.
In colder temperatures, the fuel's viscosity increases, making it thicker and more resistant to flow. This results in a reduced flow rate through the 3/8-inch line. As the fuel passes through the line, it encounters resistance due to the increased viscosity, leading to a slower movement of the liquid. For example, if you have a fuel system designed for optimal performance at a specific temperature range, lowering the temperature could cause the fuel to flow at a slower rate, potentially leading to inadequate fuel supply to the engine.
Conversely, in warmer conditions, the fuel's viscosity decreases, allowing it to flow more freely. This temperature change enables a higher flow rate through the 3/8-inch line. The reduced viscosity means the fuel molecules move more easily, resulting in a faster and more efficient transfer of fuel. However, it's important to note that extremely high temperatures can also have negative effects, such as fuel evaporation and potential damage to the fuel system components.
The temperature impact on fuel flow is particularly crucial in applications where precise fuel metering is required, such as in automotive or aviation systems. Engineers and designers must consider the operating temperature range of the fuel system to ensure optimal performance. By understanding the relationship between temperature and fuel flow, they can select appropriate materials, design efficient fuel lines, and implement control mechanisms to maintain consistent fuel delivery regardless of environmental conditions.
In summary, temperature variations significantly influence the flow of fuel through a 3/8-inch line. Cold temperatures increase viscosity, reducing flow, while warmer temperatures decrease viscosity, allowing for better flow. Recognizing these temperature-related effects is vital for maintaining efficient and reliable fuel systems across various industries.
Winterizing Your Boat: A Guide to Fuel Line Shutdown
You may want to see also
Flow Control: Learn methods to regulate fuel flow in a 3/8-inch line
Flow control is an essential aspect of managing fuel systems, especially when dealing with smaller-diameter lines like a 3/8-inch line. This size of line is commonly used in various applications, including automotive fuel injection systems and small-scale industrial processes. Regulating fuel flow through such a line is crucial to ensure optimal performance and prevent issues like fuel starvation or excessive pressure. Here are some methods to effectively control fuel flow in a 3/8-inch line:
One of the primary methods to regulate fuel flow is by using a fuel pressure regulator. This device is designed to maintain a consistent fuel pressure within the system. It works by reducing the high-pressure fuel from the pump to a lower, more manageable pressure suitable for the engine or application. When selecting a fuel pressure regulator, consider the specific requirements of your system, including the desired pressure output and the fuel's properties. Properly calibrated pressure regulators are key to ensuring a steady and controlled fuel supply.
Another effective approach is to employ a fuel flow meter or restrictor. These components are strategically placed in the fuel line to measure and limit the volume of fuel passing through. Flow meters provide real-time data on fuel flow rates, allowing for precise adjustments. Restrictors, on the other hand, are designed to reduce the cross-sectional area of the fuel line, thereby limiting the flow. This method is particularly useful when dealing with high-pressure systems or when fine-tuning fuel delivery for specific engine conditions.
In some cases, a combination of fuel pressure regulators and flow restrictors can be utilized for enhanced control. This dual approach ensures both pressure and volume regulation, providing a comprehensive solution for fuel flow management. By carefully selecting and positioning these components, you can optimize fuel delivery, improve engine performance, and maintain a stable operating environment.
Additionally, consider the use of fuel filters as a means of flow control. Filters not only remove contaminants but also act as a restriction, slightly reducing the flow rate. This is especially beneficial in preventing fuel-borne contaminants from causing issues in the fuel system. Regular maintenance and replacement of filters are essential to maintaining their effectiveness.
Lastly, understanding the specific requirements of your fuel system and engine is crucial. Factors such as engine displacement, power output, and fuel consumption rate will influence the necessary flow control measures. Consulting the manufacturer's guidelines and specifications will provide valuable insights into the optimal fuel flow rates and the appropriate control methods for your particular application.
Fuel Pump Line Removal: A Guide for 2005 Dodge Durango Owners
You may want to see also
Frequently asked questions
The fuel flow rate through a 3/8-inch line can vary depending on several factors, including the engine's requirements, fuel pressure, and line length. As a general guideline, a 3/8-inch line can handle a fuel flow rate of around 1-2 gallons per minute (gpm) for most automotive applications.
To determine the exact fuel flow rate, you can use the engine's specifications and the following formula: Fuel Flow Rate (gpm) = (Engine Displacement x Engine Speed) / (Fuel Pressure x Line Diameter). Adjust the values based on your engine's unique characteristics.
While a 3/8-inch line can accommodate many high-performance engines, it's essential to consider the engine's power output and fuel requirements. For more powerful engines, a larger fuel line or additional fuel management components might be necessary to ensure optimal performance and prevent fuel starvation.
Some potential problems with a 3/8-inch line include fuel leaks, blockages, or pressure drops. Leaks can occur at connections or fittings, while blockages may result from contaminants or debris. Regular maintenance and inspections can help identify and resolve these issues.
To optimize performance, consider using a fuel filter, ensuring proper fuel pressure, and maintaining a clean fuel system. Upgrading to a larger fuel line or adding a fuel pump can also enhance flow rates and overall engine efficiency.