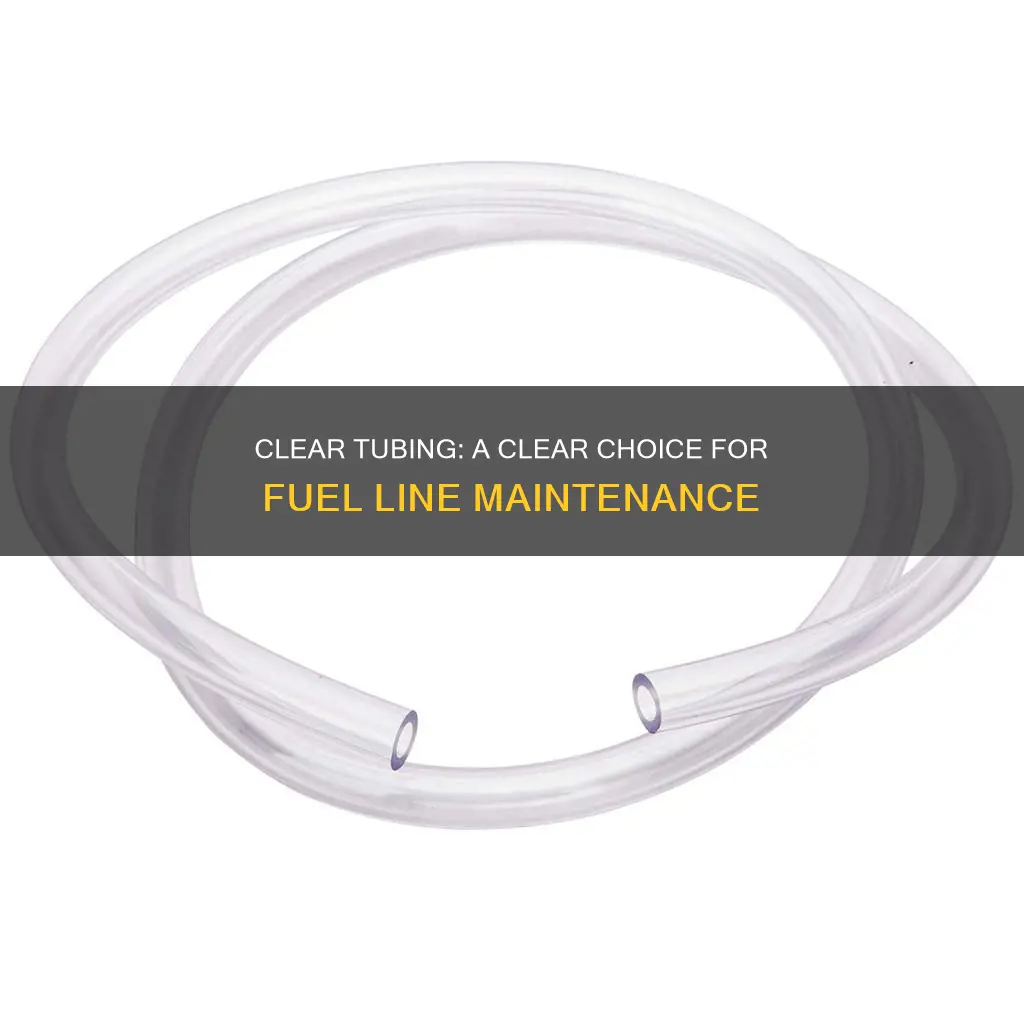
Clear tubing for fuel lines is an essential component in the maintenance and repair of fuel systems in vehicles. It serves as a protective barrier, ensuring that fuel remains contained and prevents contamination. This type of tubing is designed to be durable and flexible, allowing it to withstand the rigors of fuel transport while maintaining its structural integrity. Its clear material also enables easy inspection of the fuel line's condition, making it a valuable tool for both professional mechanics and DIY enthusiasts. Whether it's for a classic car restoration or a modern vehicle, clear tubing for fuel lines is a critical part of keeping engines running smoothly and efficiently.
Characteristics | Values |
---|---|
Product Type | Fuel Line Cleaner |
Application | Fuel Lines, Tanks, and Injectors |
Compatibility | Gasoline, Diesel, Ethanol, Biodiesel |
Form | Liquid |
Container Size | Varies (e.g., 16 oz, 32 oz) |
Key Ingredients | Ethanol, Isopropyl Alcohol, Surfactants |
Benefits | Removes deposits, improves fuel flow, enhances engine performance |
Usage | Direct application into fuel lines, no need to disconnect |
Safety | Non-toxic, biodegradable, safe for the environment |
Brand | Various (e.g., Sea-Dog, Marine-Grade, Fuel-Fix) |
Reviews | Positive feedback for engine performance improvement |
Availability | Automotive stores, online retailers |
What You'll Learn
- Fuel Line Material: Choose tubing made from compatible materials like PVC or rubber
- Size and Diameter: Ensure the tubing's size matches the fuel line's diameter for optimal flow
- Flexibility: Select tubing that can bend and stretch to accommodate fuel line routing
- Temperature Resistance: Opt for tubing that can withstand fuel temperature variations
- Chemical Compatibility: Verify the tubing is resistant to fuel chemicals to prevent degradation
Fuel Line Material: Choose tubing made from compatible materials like PVC or rubber
When it comes to choosing the right material for your fuel line tubing, compatibility is key. The material you select should not only be durable but also compatible with the fuel type and the overall system design. One of the most popular choices for fuel line tubing is PVC (polyvinyl chloride). PVC is an excellent option due to its chemical resistance, making it ideal for transporting various fuel types, including gasoline, diesel, and even biofuels. It is also known for its flexibility, allowing for easy installation around tight corners and curves. Additionally, PVC tubing is lightweight, making it a practical choice for fuel lines, especially in vehicles where weight is a concern.
Another compatible material is rubber, which offers a different set of advantages. Rubber tubing is highly flexible and can withstand the expansion and contraction that occurs with temperature changes, making it suitable for a wide range of temperatures. This flexibility is particularly beneficial for fuel lines that need to accommodate movement, such as in older vehicles or those with engine modifications. However, it's important to note that rubber may not be as resistant to certain chemicals as PVC, so it's crucial to ensure that the specific rubber type used is compatible with the fuel in question.
The choice between PVC and rubber often depends on the specific requirements of your fuel line system. For instance, if you're working with a high-pressure fuel system, PVC might be preferred due to its ability to handle increased pressure without compromising flexibility. On the other hand, if your fuel line needs to be installed in an area with varying temperatures, rubber could be the better choice.
In summary, when selecting fuel line tubing, consider the properties of different materials. PVC offers excellent chemical resistance and flexibility, making it versatile for various fuel types. Rubber, with its flexibility and temperature resistance, is ideal for systems that require adaptability. Understanding the compatibility of these materials with your fuel and system design will ensure a reliable and efficient fuel line setup. Always remember to consult manufacturer guidelines and seek professional advice when in doubt to make the best material choice for your specific application.
Chevy 49 Fuel Line: Size and Compatibility Guide
You may want to see also
Size and Diameter: Ensure the tubing's size matches the fuel line's diameter for optimal flow
When it comes to replacing or repairing fuel lines in a vehicle, one crucial aspect often overlooked is the size and diameter of the tubing. Ensuring that the tubing's dimensions match the fuel lines' specifications is essential for maintaining optimal fuel flow and overall system efficiency. This attention to detail can prevent various issues and ensure the vehicle's engine operates smoothly.
The size and diameter of tubing play a significant role in determining the rate of fuel delivery to the engine. Fuel lines are designed to carry a specific volume of fuel at a certain pressure, and using tubing that is too small or too large can lead to performance problems. If the tubing is too narrow, it may restrict fuel flow, causing the engine to run poorly or even stall. Conversely, using tubing that is too large can result in excessive fuel flow, leading to potential engine damage and reduced fuel efficiency.
To ensure compatibility, it is crucial to refer to the vehicle's manual or consult a professional mechanic. They can provide the exact measurements and specifications for the fuel lines in your particular make and model. These professionals often have access to specialized tools and knowledge to help identify the correct tubing size. By using the recommended dimensions, you can guarantee a proper fit and optimal performance.
In some cases, you might come across universal fuel line kits that offer various sizes to accommodate different vehicles. While these kits can be convenient, it is essential to double-check the specifications to ensure the selected size matches the fuel lines. Even with universal kits, it is advisable to cross-reference the measurements with the vehicle's manual or seek expert advice to avoid any potential issues.
In summary, paying attention to the size and diameter of the tubing is a critical step in fuel line maintenance and repair. By matching the tubing to the fuel lines' specifications, you can ensure a smooth and efficient fuel flow, promoting optimal engine performance and longevity. Always consult the vehicle's documentation or seek professional guidance to make informed choices when working with fuel lines.
Fuel Injector Line Maintenance: Is Cleaning Necessary?
You may want to see also
Flexibility: Select tubing that can bend and stretch to accommodate fuel line routing
When it comes to fuel line routing, flexibility is a crucial factor to consider. Fuel lines need to be able to navigate through various engine compartments, often with limited space and complex layouts. Selecting tubing that can bend and stretch is essential to ensure a reliable and efficient fuel delivery system. This flexibility allows the tubing to adapt to the engine's natural movements and vibrations, reducing the risk of damage and ensuring a long-lasting installation.
The ability to bend and stretch is particularly important when dealing with fuel lines that need to pass through tight spaces, such as under the hood or around engine components. Rigid tubing can become a hindrance, causing strain and potential damage to the fuel line or the surrounding areas. By choosing flexible tubing, you allow for a more natural and secure installation, reducing the chances of kinks, twists, or damage during the engine's operation.
Flexibility also plays a role in accommodating the dynamic nature of fuel line routing. As the engine operates, the fuel lines may need to move and adjust to maintain optimal performance. Flexible tubing can easily adapt to these changes, ensuring a consistent and reliable fuel supply. This is especially important in high-performance vehicles or applications where the engine's movement is more pronounced.
When selecting flexible tubing, consider the material and construction. Look for tubing made from durable materials that can withstand the harsh conditions of an engine compartment. Braided or reinforced flexible hoses are often ideal for fuel lines, offering the necessary flexibility while maintaining structural integrity. Additionally, ensure that the tubing has a suitable inner diameter to handle the fuel flow rate required for your application.
In summary, flexibility is a key consideration when choosing tubing for fuel line routing. By selecting tubing that can bend and stretch, you ensure a secure and reliable installation, accommodating the engine's movements and vibrations. This approach helps prevent damage, maintains optimal fuel delivery, and contributes to the overall longevity of the fuel system. Remember to choose the right material and construction to match the specific requirements of your fuel line application.
Prevent Rust: 5 Tips to Slow Down Fuel Line Degradation
You may want to see also
Temperature Resistance: Opt for tubing that can withstand fuel temperature variations
When it comes to choosing the right tubing for your fuel line, temperature resistance is a critical factor that should not be overlooked. Fuel temperatures can vary significantly, especially in different climates and operating conditions. For instance, fuel in a vehicle's tank can get extremely hot during idling or when the engine is running, while it can also freeze in colder climates. Therefore, selecting tubing that can withstand these temperature variations is essential to ensure the longevity and reliability of your fuel system.
The ideal tubing material should offer excellent thermal stability, meaning it can maintain its structural integrity and performance across a wide temperature range. Some materials, like certain types of rubber or plastic, may become brittle or lose flexibility when exposed to extreme cold, leading to potential cracks or leaks. In contrast, materials such as stainless steel or specialized polymers designed for fuel lines can handle both high and low temperatures without compromising their durability.
To ensure temperature resistance, consider the specific temperature range your fuel system will encounter. For most automotive applications, a tubing material that can withstand temperatures between -40°F to 250°F (-40°C to 121°C) is generally sufficient. However, if you operate in regions with more extreme temperature variations, you might need tubing that can handle even wider ranges. Always refer to the manufacturer's specifications to determine the temperature resistance of different materials.
Additionally, the design of the tubing can also impact its temperature resistance. For example, braided or reinforced tubing often provides better flexibility and resistance to kinking, which can be beneficial when dealing with temperature fluctuations. These designs can help maintain a consistent flow of fuel, even when the temperature changes.
In summary, when selecting tubing for your fuel line, prioritize materials and designs that offer superior temperature resistance. This ensures that your fuel system remains reliable and efficient, even in the face of varying temperatures. Always consult the manufacturer's guidelines and consider the specific operating conditions to make an informed decision.
Fuel Line Sizing for Gokart Performance: A Comprehensive Guide
You may want to see also
Chemical Compatibility: Verify the tubing is resistant to fuel chemicals to prevent degradation
When it comes to fuel line tubing, chemical compatibility is a critical factor to consider. Fuel lines are exposed to various chemicals, including gasoline, diesel, and other additives, which can lead to degradation and potential failure over time. Therefore, it is essential to verify that the tubing used is resistant to these fuel chemicals to ensure optimal performance and longevity.
One way to assess chemical compatibility is by referring to the manufacturer's specifications and data sheets. These documents often provide information on the materials used in the tubing and their resistance to specific chemicals. Look for tubing made from materials such as high-density polyethylene (HDPE), polyvinyl chloride (PVC), or fluoropolymers, as these are commonly used for fuel lines due to their inherent chemical resistance. For example, HDPE is known for its excellent resistance to gasoline and diesel, while PVC can withstand a wide range of fuel chemicals.
In addition to the material, the thickness and construction of the tubing also play a role in chemical compatibility. Thicker walls and multi-layer constructions can provide better protection against chemical penetration. Consider the operating conditions and the specific fuel types used in your application to choose the most suitable tubing.
To further ensure chemical compatibility, it is recommended to perform compatibility testing. This involves exposing the tubing to various fuel chemicals and monitoring for any signs of degradation, such as swelling, softening, or chemical breakdown. Standardized tests, such as those outlined in industry standards like ASTM D2854, can be used to evaluate the tubing's resistance to specific chemicals. By conducting these tests, you can verify that the chosen tubing meets the required standards and will not degrade when exposed to fuel chemicals.
In summary, when selecting tubing for fuel lines, it is crucial to prioritize chemical compatibility. Review manufacturer specifications, choose materials with inherent resistance to fuel chemicals, and consider the tubing's thickness and construction. Additionally, perform compatibility testing to ensure the chosen tubing can withstand the specific fuel chemicals it will encounter. By taking these steps, you can effectively verify the tubing's resistance to fuel chemicals, thereby preventing degradation and ensuring the long-term reliability of your fuel line system.
F250 Fuel Line Disconnect: Choosing the Right Tool Size
You may want to see also
Frequently asked questions
Clear tubing, often made from materials like PVC or polycarbonate, is used for fuel lines to provide a visual indicator of the fuel flow. Its transparency allows easy monitoring of the fuel level and any potential leaks, ensuring the system's integrity and safety.
Clear tubing stands out from regular fuel line tubing due to its translucent nature, offering enhanced visibility. This feature is particularly useful in applications where fuel levels and system performance need to be closely observed, such as in racing or aviation.
Yes, clear tubing is versatile and can be utilized for various fuel line applications. It is commonly employed in automotive, marine, and aviation industries, where the ability to inspect the fuel system is crucial for maintenance and troubleshooting.
The primary advantage of clear tubing is its ability to provide visual feedback, enabling quick identification of potential issues. This can lead to faster response times in addressing problems like fuel contamination, leaks, or blockages, ultimately improving overall system reliability.