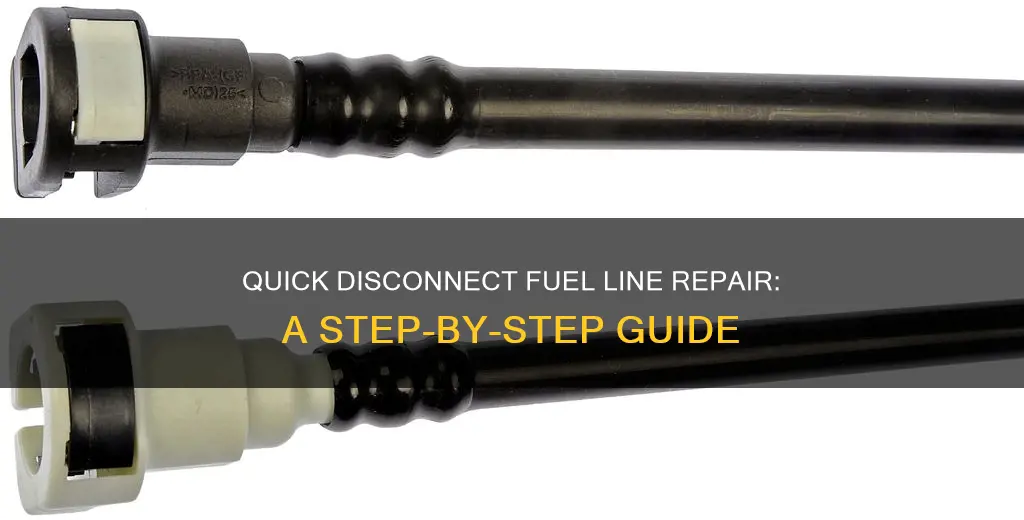
Quick disconnect fuel lines are essential components in vehicle fuel systems, allowing for easy fueling and maintenance. However, they can be prone to leaks and damage over time. Repairing a quick disconnect fuel line involves a systematic approach to ensure a secure and leak-free connection. This guide will provide a step-by-step process to repair a damaged quick disconnect fuel line, covering the necessary tools, safety precautions, and techniques to restore its functionality.
What You'll Learn
- Tools and Materials: Gather necessary tools like fuel line cutters, crimping pliers, and replacement lines
- Safety Precautions: Wear protective gear and ensure a well-ventilated workspace to avoid fuel inhalation
- Fuel Line Inspection: Check for cracks, corrosion, or damage before attempting any repairs
- Cutter and Crimping: Carefully cut and crimp the fuel line to ensure a secure connection
- Testing and Reassembly: Test the system and reassemble, ensuring proper alignment and functionality
Tools and Materials: Gather necessary tools like fuel line cutters, crimping pliers, and replacement lines
To effectively repair a quick disconnect fuel line, it's crucial to have the right tools and materials on hand. Here's a detailed guide on what you'll need:
Tools:
- Fuel Line Cutters: These specialized tools are designed to cleanly and precisely cut fuel lines. Look for cutters that can handle the diameter of your fuel line.
- Crimping Pliers: Crimping pliers are essential for securely attaching the new fuel line to the quick disconnect fitting. They create a tight, leak-proof connection.
- Pipe Wrench or Fuel Line Wrench: A wrench will be helpful for tightening connections and ensuring a snug fit.
- Sandpaper or Emery Cloth: Gently abrasive materials can be used to smooth any rough spots on the fuel line or fitting before assembly.
- Safety Gear: Safety glasses and gloves are essential to protect your eyes and hands during the repair process.
Materials:
- Replacement Fuel Line: Obtain a replacement fuel line that is compatible with your vehicle's specifications. Ensure it has the correct diameter and length to fit your existing setup.
- Quick Disconnect Fitting: Select a replacement quick disconnect fitting that matches the original in terms of size and thread type.
- Fuel Line Adhesive (Optional): Some repair kits include adhesive specifically designed for fuel lines. This can provide extra security and prevent leaks.
Important Considerations:
- Safety First: Always prioritize safety when working with fuel lines. Ensure your workspace is well-ventilated, and be cautious of sparks or open flames, as fuel is flammable.
- Disassembly: Carefully disconnect the damaged fuel line from the engine and any other components it connects to. Take note of the connection points for proper reassembly.
- Cleaning: Before installing the new fuel line, clean the existing connections and fittings to remove any debris or old adhesive.
Fuel Line Removal Guide: 2008 RMZ450
You may want to see also
Safety Precautions: Wear protective gear and ensure a well-ventilated workspace to avoid fuel inhalation
When working on fuel line repairs, prioritizing safety is paramount. Always wear protective gear, including gloves and safety goggles, to shield your skin and eyes from potential fuel splashes or spills. Fuel can be harmful if inhaled, so it's crucial to work in a well-ventilated area or outdoors to prevent inhalation risks. Ensure proper ventilation by opening windows or using fans to disperse any fumes.
In the event of a fuel leak, it's essential to act quickly and calmly. Avoid creating sparks or open flames, as they can ignite the fuel and lead to dangerous explosions. Keep a fire extinguisher nearby and be familiar with its use to address any potential fire hazards. Additionally, have a supply of clean rags or absorbent materials ready to contain and clean up any spills promptly.
During the repair process, be cautious of sharp tools and components to prevent injuries. Keep your work area tidy and organized to minimize tripping hazards. It's also advisable to wear long sleeves and pants to protect your skin from any accidental contact with fuel or cleaning agents.
Remember, taking these safety precautions is non-negotiable when dealing with fuel lines. By being prepared and cautious, you can ensure a safe and successful repair, minimizing the risks associated with fuel handling. Always prioritize your well-being and that of those around you.
Yamaha XT225 Fuel Line: Size and Specs Revealed
You may want to see also
Fuel Line Inspection: Check for cracks, corrosion, or damage before attempting any repairs
Fuel lines are an essential component of your vehicle's fuel system, and ensuring their integrity is crucial for optimal performance and safety. Before attempting any repairs or replacements, a thorough inspection is imperative to identify potential issues. Here's a step-by-step guide to inspecting your fuel lines for cracks, corrosion, or damage:
- Visual Inspection: Start by visually examining the fuel lines for any visible signs of deterioration. Look for cracks, splits, or punctures along the length of the line. These defects can be caused by age, chemical degradation, or physical damage. Pay close attention to bends and fittings, as these areas are more susceptible to wear and tear. Check for any signs of rust or corrosion, especially if the fuel lines are exposed to the elements. Corrosion can weaken the material and lead to leaks or complete failure.
- Flexibility Test: Fuel lines should be flexible to accommodate engine movement. Test the flexibility by gently bending the lines at various angles and observing if they return to their original shape. If a line becomes stiff or breaks during this test, it may indicate internal damage or the presence of a crack.
- Pressure Test (Optional): For a more comprehensive assessment, consider using a fuel pressure gauge and a small amount of compressed air to test the lines. Attach the gauge to the fuel line and apply pressure. Listen for any hissing sounds, which could indicate a leak. This test is particularly useful for identifying internal damage or small pinholes that might not be visible during a visual inspection.
- Route Inspection: Examine the fuel lines' routing for any signs of damage or excessive wear. Ensure that the lines are not pinched, kinked, or rubbing against sharp edges or components. The fuel lines should be securely fastened and not show any signs of strain or damage from the mounting process.
- Document and Compare: Take detailed notes and photographs of any issues found during the inspection. Compare these observations with the vehicle's service manual or previous inspection records to identify any changes or worsening conditions. This documentation will be valuable for determining the necessary repairs or replacements.
Remember, regular maintenance and prompt attention to any issues will help ensure the longevity of your fuel system and prevent costly repairs. If you notice any significant damage or are unsure about the inspection process, it is always best to consult a professional mechanic for assistance.
Step-by-Step Guide: Removing Fuel Lines from Ford Explorer Fuel Pump
You may want to see also
Cutter and Crimping: Carefully cut and crimp the fuel line to ensure a secure connection
When it comes to repairing a quick-disconnect fuel line, one of the most crucial steps is the cutting and crimping process. This technique ensures a secure and reliable connection, allowing for efficient fuel transfer without the risk of leaks or disconnections. Here's a detailed guide on how to master this repair task:
Preparation: Begin by gathering the necessary tools and materials. You'll need a high-quality fuel line cutter, preferably one designed for the specific diameter of your fuel line. Additionally, obtain a crimping tool suitable for the connector type you're using. It's essential to have the right-sized crimping dies or inserts for a perfect fit. Ensure you have a steady hand and a well-lit workspace to facilitate the process.
Cutting the Fuel Line: Locate the damaged section of the fuel line and mark its length, ensuring it's slightly longer than the required length for the connector. Carefully cut through the fuel line using the cutter, maintaining a straight and clean cut. Take your time with this step to avoid any uneven edges that could compromise the connection. A precise cut is vital to ensure a proper fit during the crimping process.
Crimping Technique: Now, it's time to crimp the fuel line onto the connector. Start by inserting the fuel line into the connector, ensuring it's aligned correctly. Apply the crimping tool with firm pressure, following the manufacturer's instructions for the specific connector type. The goal is to create a secure and tight connection. Use the crimping tool's dies or inserts to deform the connector's metal, forming a robust bond. Repeat this process for any additional fuel lines or connectors you need to secure.
Finishing Touches: After crimping, inspect the connections for any signs of imperfections or uneven pressure. If needed, gently adjust the crimping tool to ensure a uniform and complete connection. Once satisfied with the crimping, test the fuel line's functionality by applying pressure and checking for any leaks. This step is crucial to ensure the repair is secure and reliable.
By following these steps, you can effectively repair a quick-disconnect fuel line, ensuring a safe and efficient fuel transfer system. Remember, precision and attention to detail are key during the cutting and crimping process to achieve a long-lasting repair.
Optimizing Fuel Line Routing for Maximum Performance in Race Cars
You may want to see also
Testing and Reassembly: Test the system and reassemble, ensuring proper alignment and functionality
Before reassembling the quick disconnect fuel line, it's crucial to test the system to ensure it functions correctly and to identify any potential issues. Start by checking the fuel line for any visible damage or leaks. Inspect the fittings and connectors for cracks, corrosion, or signs of deterioration. If any damage is found, replace the affected components with new ones.
Next, ensure that all components are clean and free of debris. Use a mild detergent and water solution to clean the fuel line, fittings, and connectors. Rinse thoroughly to remove any residue. This step is essential to prevent contamination and ensure a proper seal when reassembling.
Now, reassemble the quick disconnect fuel line, following the manufacturer's instructions or a trusted repair guide. Pay close attention to the alignment of the fittings and connectors. Ensure that all components are properly seated and secured. Tighten the fasteners securely but avoid over-tightening, as this can damage the components.
After reassembly, test the system by applying pressure to the fuel line and checking for leaks. Use a soapy water solution to create a visual indicator for any potential leaks. If a leak is detected, carefully inspect the connections and fittings to identify the source. Tighten or replace the affected components as necessary.
Finally, start the engine and listen for any unusual noises. Check for any fuel leaks around the quick disconnect fittings. If the system passes these tests, it is likely functioning correctly. However, if any issues arise during testing, carefully troubleshoot and address the problems before final reassembly. Proper testing and reassembly will ensure a reliable and safe fuel system.
Maximizing Fuel Efficiency: The Role of Return Lines in Pumps
You may want to see also
Frequently asked questions
A quick disconnect fuel line is a type of fuel line that uses a quick-release coupling to connect the fuel tank to the engine. It allows for easy fueling and maintenance. Over time, the fittings can wear out, become corroded, or be damaged, leading to fuel leaks or a loss of fuel supply, which requires repair or replacement.
Look for signs of damage, such as cracks, brittleness, or corrosion around the fittings. Check for any fuel leaks, especially when the fuel tank is full or when the engine is running. If you notice a strong fuel odor or see fuel pooling under the vehicle, it's a clear indication of a potential issue. Regular maintenance and inspections can help identify problems early on.
Simple repairs, such as tightening loose fittings or replacing worn-out O-rings, can be done by vehicle owners with some mechanical knowledge and the right tools. However, if the damage is extensive, or if you're unsure about the process, it's best to consult a professional mechanic. They have the expertise and specialized tools to ensure a proper repair, ensuring your vehicle's fuel system is safe and reliable.