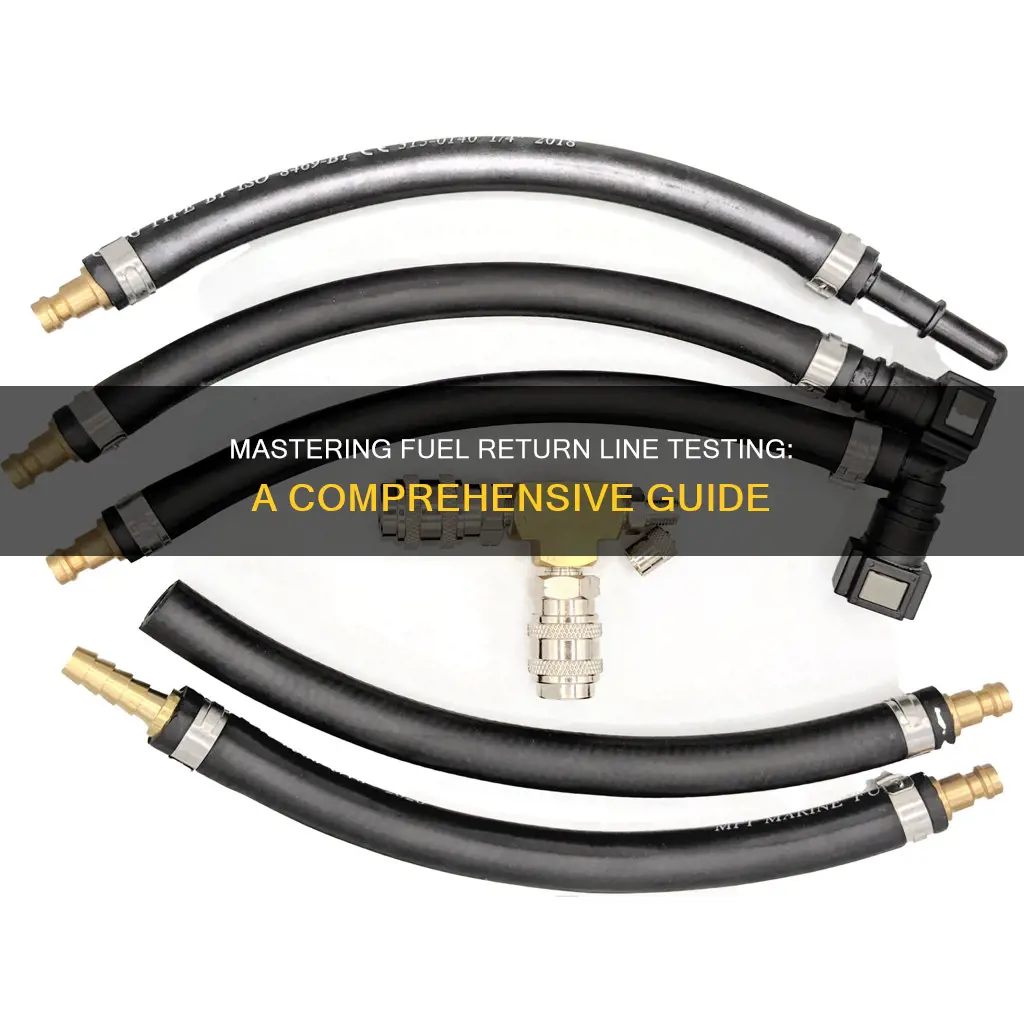
Testing the fuel return line is a crucial step in ensuring the proper functioning of a vehicle's fuel system. This process involves checking for leaks, verifying the flow rate, and assessing the overall performance of the line. By following a systematic approach, mechanics can identify potential issues, such as blockages or pressure drops, which may lead to poor engine performance or fuel efficiency problems. Understanding how to test the fuel return line is essential for maintaining a vehicle's reliability and longevity.
What You'll Learn
- Visual Inspection: Check for cracks, leaks, and debris in the fuel return line
- Pressure Testing: Use a gauge to measure pressure and identify blockages or leaks
- Flow Rate Measurement: Assess the fuel flow rate to ensure proper operation
- Ultrasonic Testing: Employ ultrasonic waves to detect internal damage or blockages
- Pressure Drop Analysis: Measure pressure drop to identify potential restrictions or leaks
Visual Inspection: Check for cracks, leaks, and debris in the fuel return line
A visual inspection is a crucial step in testing the fuel return line, as it provides an initial assessment of the line's condition and can help identify potential issues before more invasive testing methods are required. This inspection should be conducted with a keen eye for detail and a systematic approach to ensure nothing is missed.
Start by locating the fuel return line, which is typically a flexible hose or a rigid tube that connects the fuel tank to the engine. It is important to inspect the line in its entirety, from the point where it exits the fuel tank to its connection with the engine. Look for any visible signs of damage, such as cracks, tears, or punctures. These defects can be caused by age, wear and tear, or previous repairs, and they may lead to fuel leaks or contamination. Inspect the line for any signs of corrosion or rust, especially if the line is made of metal. These issues can weaken the line and compromise its integrity.
Next, check for any leaks. A fuel return line that is leaking will result in fuel dripping or pooling around the line's connections or at the line's ends. This can be a serious issue, as it may lead to fuel wastage, engine performance problems, and even safety hazards. Look for any signs of fuel seeping or dripping, especially at the line's fittings and attachments. If you notice any leaks, it is important to address them immediately, as they can quickly escalate into more significant problems.
In addition to looking for physical damage, it is also important to check for the presence of debris or contaminants. Over time, fuel can accumulate debris, such as sediment, water, or varnish, which can clog the line and affect fuel flow. Inspect the line for any signs of discoloration or the presence of small particles or sediment. If you notice any debris, it may indicate that the fuel system needs to be flushed or that there are other issues that need to be addressed.
During the visual inspection, it is also beneficial to check the surrounding areas for any signs of fuel contamination. Look for any fuel stains or residue on the ground or nearby surfaces. This could indicate a leak or a problem with the fuel system that needs immediate attention. Additionally, inspect the fuel tank and its surroundings for any signs of damage or corrosion, as these issues can also impact the fuel return line's performance.
By conducting a thorough visual inspection, you can identify potential issues with the fuel return line, such as cracks, leaks, and debris, which can help prevent further complications and ensure the efficient operation of the fuel system. This initial step is a valuable tool in the overall testing process, providing a foundation for more targeted and effective troubleshooting.
Replacing Fuel Line in Poulan Chainsaw: A Step-by-Step Guide
You may want to see also
Pressure Testing: Use a gauge to measure pressure and identify blockages or leaks
Pressure testing is a crucial method to assess the integrity of a fuel return line system. This process involves using a pressure gauge to measure the system's pressure at various points, allowing for the detection of potential issues such as blockages or leaks. Here's a step-by-step guide on how to perform this test effectively:
Preparation: Before initiating the pressure test, ensure you have the necessary tools and equipment. You will need a pressure gauge specifically designed for fuel systems, which can measure pressure in pounds per square inch (PSI) or bar. Additionally, obtain a suitable fuel pressure regulator and a source of compressed air or nitrogen to generate the test pressure. It is essential to wear protective gear, including safety goggles and gloves, to safeguard against any potential fuel splashes or spills.
System Preparation: Locate the fuel return line and identify the points where pressure measurements will be taken. Typically, these points include the inlet and outlet of the fuel pump, the fuel filter, and the return line itself. Ensure the engine is off and the vehicle is in a stable position to prevent any movement during the test. Disconnect the fuel lines at the identified points to facilitate pressure measurements.
Pressure Application: Attach the pressure gauge to the fuel return line at the desired measurement point. Connect the fuel pressure regulator to the gauge and the compressed air or nitrogen source. Gradually increase the pressure in the system using the compressed air or nitrogen, ensuring it reaches a predetermined target pressure. This pressure should be sufficient to simulate normal operating conditions but should not cause any excessive stress on the fuel system components.
Pressure Measurement: With the system pressurized, carefully read the pressure gauge to obtain the measurement. Record this value, as it will serve as a baseline for comparison during the test. If the pressure drops significantly or fluctuates, it may indicate a potential issue. Note any changes in pressure at different points along the fuel return line to identify specific areas of concern.
Leak Detection: During the pressure test, pay close attention to any signs of fuel leakage. Even small leaks can be detected by observing fuel accumulation around the fuel lines or engine components. If a leak is suspected, carefully inspect the connections and fittings for any damage or corrosion. Address any leaks promptly to prevent further issues and ensure the safety of the fuel system.
Blockage Identification: Pressure testing also helps identify blockages within the fuel return line. If the pressure measurement remains constant or drops only slightly, it could indicate a blockage. This may be caused by debris, contaminants, or a restricted flow path. To address this, consider using a fuel line cleaner or a compressed air blast to clear any obstructions. Regular maintenance and cleaning can help prevent blockages and ensure optimal fuel system performance.
By following these steps and utilizing pressure testing, you can effectively identify and address issues within the fuel return line system. This method is a valuable tool for mechanics and vehicle owners, ensuring the fuel system operates efficiently and safely.
Fuel Line Removal: A Step-by-Step Guide for Your Cadillac Seville
You may want to see also
Flow Rate Measurement: Assess the fuel flow rate to ensure proper operation
To ensure the proper operation of a fuel return line, it is crucial to measure the flow rate of fuel. This process involves assessing the rate at which fuel is flowing through the line, which can provide valuable insights into the system's performance and identify potential issues. Here's a step-by-step guide on how to measure the flow rate of fuel for testing the return line:
Step 1: Gather Equipment
You will need a few essential tools for this test. Firstly, obtain a flow meter specifically designed for fuel measurement. These meters can be either positive displacement or velocity-based, depending on your preference and the system's requirements. Additionally, you'll require a fuel source that can provide a steady flow of fuel through the return line. This could be a fuel pump or a controlled fuel supply system. Make sure you have the necessary adapters and connections to interface the flow meter with the fuel line.
Step 2: Set Up the Test
Locate the fuel return line and ensure it is accessible for testing. Clean the line to remove any debris or contaminants that might affect the measurement accuracy. Securely attach the flow meter to the fuel line, ensuring a tight and leak-free connection. It is essential to position the flow meter in a straight section of the line to minimize any potential flow disturbances.
Step 3: Calibrate the Flow Meter
Before taking measurements, calibrate the flow meter according to the manufacturer's instructions. This process ensures that the meter provides accurate readings. You may need to adjust the meter's settings or use a calibration standard to verify its performance. Proper calibration is critical for reliable flow rate data.
Step 4: Measure and Record
Start the fuel flow and allow it to stabilize. Measure the pressure drop across the flow meter, as this will provide valuable information about the flow rate. Record the pressure drop value and the corresponding flow rate displayed on the meter. Repeat this process at different flow rates to create a comprehensive data set. Ensure you take multiple readings to account for any variations in the system's performance.
Step 5: Analyze the Results
Examine the measured flow rates and compare them to the expected values based on the system's design and specifications. Any significant deviations from the expected flow rates may indicate issues with the fuel return line, such as blockages, leaks, or improper sizing. Analyze the data to identify patterns or anomalies that could help diagnose problems.
By following these steps, you can effectively measure the flow rate of fuel to assess the performance of the return line. This process is essential for maintaining the efficiency and reliability of fuel systems in various applications, including automotive, aviation, and industrial settings. Regular flow rate measurements can help prevent potential issues and ensure optimal fuel management.
Optimizing Generator Performance: The Best Spots for Fuel Pickup Lines
You may want to see also
Ultrasonic Testing: Employ ultrasonic waves to detect internal damage or blockages
Ultrasonic testing is a non-invasive method that utilizes high-frequency sound waves to examine the internal structure of a fuel return line, offering a detailed insight into its condition. This technique is particularly useful for identifying hidden damage or blockages that might not be visible through other means. By emitting ultrasonic waves into the line, technicians can detect and analyze various issues, ensuring the system's optimal performance and safety.
The process begins with the application of a coupling gel or paste, which acts as a medium for the sound waves to travel through the fuel line. This gel is carefully applied to the line's surface, ensuring complete coverage. The ultrasonic probe, a small device emitting and receiving sound waves, is then positioned along the line. As the probe sends out pulses, it creates a pattern of high-frequency sound waves that penetrate the material. These waves reflect off any internal structures, such as damage or blockages, and return to the probe, providing valuable data.
The received data is then processed by the ultrasonic testing equipment, which interprets the reflected waves to create a visual representation of the line's internal condition. This interpretation reveals the presence and location of any defects, such as cracks, holes, or blockages. Technicians can identify the severity of the issue by analyzing the wave patterns and their reflections. For instance, a change in wave pattern or a decrease in signal strength might indicate a blockage or a damaged section of the fuel line.
One of the key advantages of ultrasonic testing is its ability to detect issues at an early stage. This is crucial for fuel return lines, as internal damage or blockages can lead to reduced performance, increased fuel consumption, and potential safety hazards. By identifying these problems before they cause significant damage, maintenance can be scheduled, and necessary repairs or replacements can be made, ensuring the system's longevity and reliability.
Furthermore, ultrasonic testing is a rapid and efficient process, allowing for quick assessments of multiple fuel return lines. This method is particularly beneficial in industrial settings where time is of the essence, and regular maintenance is essential to prevent costly downtime. With its non-invasive nature and high accuracy, ultrasonic testing provides a comprehensive solution for maintaining the integrity of fuel return lines, contributing to the overall efficiency and safety of fuel systems.
Step-by-Step Guide: Removing the Fuel Line on Your 2007 Chevy Suburban
You may want to see also
Pressure Drop Analysis: Measure pressure drop to identify potential restrictions or leaks
Pressure drop analysis is a critical method for assessing the performance and integrity of fuel return lines in automotive systems. This technique involves measuring the pressure difference between two points in the line to identify any potential issues such as restrictions, leaks, or blockages. By understanding the pressure drop, technicians can gain valuable insights into the system's health and functionality.
To perform this analysis, you'll need a pressure gauge, which is a specialized tool designed for this purpose. The gauge should be calibrated and appropriate for the fuel system's pressure range. Start by ensuring the engine is off and the fuel system is cool to avoid any safety hazards. Locate the two points in the fuel return line where you will measure the pressure. Typically, these points are close to the fuel pump and the fuel tank, respectively. Securely attach the pressure gauge to the line at these locations, ensuring a tight seal.
Once the gauge is in place, slowly open the fuel valve or release the pressure in the system to create a controlled pressure drop. Record the initial pressure reading at the fuel pump side. Then, slowly close the valve or reconnect the line to restore pressure. Measure and record the final pressure at the tank side. The difference between these two pressure readings will give you the pressure drop.
A significant pressure drop indicates a potential issue. For instance, a drop in pressure from the pump to the tank might suggest a restriction or blockage in the line, which could be caused by debris, corrosion, or a faulty fuel filter. Conversely, an unexpected rise in pressure could indicate a leak in the system, where fuel is escaping and not returning to the tank. These findings are crucial for diagnosing and resolving fuel system problems, ensuring optimal engine performance and fuel efficiency.
Regular pressure drop analysis can help prevent unexpected breakdowns and costly repairs. It allows for early detection of potential issues, enabling technicians to take corrective actions before the problem becomes critical. This method is a valuable tool for maintaining the health of fuel return lines and ensuring the overall reliability of the vehicle's fuel system.
Honda CR-V '98 Fuel Line Cut-Off: Causes and Fixes
You may want to see also
Frequently asked questions
Testing the fuel return line is crucial to ensure the proper functioning of the fuel system in an engine. It helps identify any blockages, leaks, or pressure issues that could lead to poor engine performance, reduced fuel efficiency, or even engine damage.
There are several signs that may indicate a problem with the fuel return line. These include engine misfires, reduced power output, unusual noises from the fuel system, frequent stalling, or a noticeable drop in fuel efficiency. If you experience any of these symptoms, it is recommended to have the fuel system, including the return line, inspected and tested.
Testing the fuel return line often involves the use of a fuel pressure gauge, a fuel pump flow bench, and a pressure tester. The procedure typically includes measuring the fuel pressure at the pump, checking for leaks in the line, and ensuring the pump is delivering the correct volume of fuel. A professional mechanic may also use a fuel system diagnostic tool to identify any trouble codes related to the fuel return line.