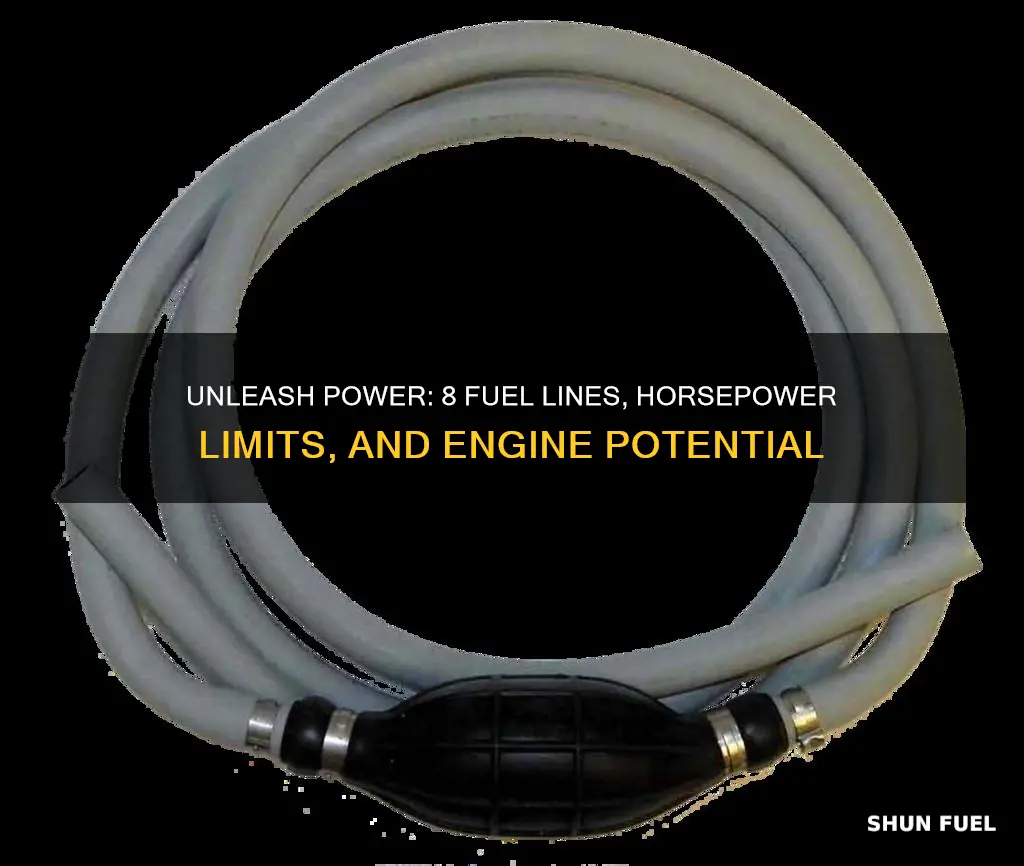
When it comes to engine performance, the fuel line plays a crucial role in delivering the right amount of fuel to the engine. The question of how many horsepower an 8-fuel line can support depends on several factors, including the engine's design, the fuel line's diameter, and the engine's overall configuration. In this paragraph, we will explore the relationship between horsepower and fuel lines, discussing the key considerations and providing insights into optimizing engine performance.
What You'll Learn
- Fuel Line Material: Different materials have varying pressure limits, affecting horsepower capacity
- Line Diameter: Thicker lines handle more power; thinner lines may restrict high-horsepower engines
- Length and Routing: Longer lines with complex routes can reduce pressure and performance
- Fuel Pump Capacity: The pump's flow rate must match the line's capacity for optimal horsepower
- Engine Requirements: Engine specifications dictate the necessary fuel line size for specific horsepower levels
Fuel Line Material: Different materials have varying pressure limits, affecting horsepower capacity
The choice of fuel line material is a critical factor when considering the horsepower capacity of a fuel system. Different materials have distinct pressure limits, which directly impact the system's ability to handle higher performance engines. For instance, a fuel line made of steel might be suitable for high-pressure applications, but it could be heavy and prone to vibration, which might not be ideal for certain vehicle types. On the other hand, a fuel line constructed from flexible materials like rubber or silicone may offer better flexibility and reduced weight, but it might not withstand the same pressure levels as steel.
When selecting a fuel line, it's essential to consider the engine's requirements and the overall vehicle design. For high-performance applications, where engines produce substantial horsepower, a fuel line with a higher pressure rating is necessary. This ensures that the fuel system can deliver the required amount of fuel efficiently and safely. For example, a fuel line rated for 100 psi (pounds per square inch) or more might be necessary for engines generating over 500 horsepower, ensuring optimal performance and preventing potential issues like fuel starvation or pressure drops.
The material's flexibility is another crucial aspect. High-horsepower engines often require fuel lines that can accommodate the engine's movement without restricting fuel flow. Flexible materials like silicone or braided steel can provide the necessary flexibility while maintaining a suitable pressure rating. These materials are commonly used in high-performance applications due to their ability to withstand pressure and temperature changes while offering a smooth, flexible fuel delivery.
Additionally, the temperature range of the fuel line is essential. Different materials have varying tolerances to heat and cold. For instance, rubber fuel lines might become brittle in extremely cold temperatures, while silicone can maintain its flexibility over a broader temperature range. Understanding the operating conditions of the engine and selecting a fuel line material that can handle those temperatures is vital for long-term reliability.
In summary, when determining the horsepower capacity of an 8 fuel line, the material's pressure rating, flexibility, and temperature tolerance are key considerations. Each material has its advantages and limitations, and the right choice will ensure a reliable and efficient fuel system, capable of supporting the engine's performance requirements. It is always recommended to consult with experts or refer to manufacturer guidelines to make an informed decision regarding fuel line specifications.
Mastering the Art of Rubber Fuel Line Installation
You may want to see also
Line Diameter: Thicker lines handle more power; thinner lines may restrict high-horsepower engines
When it comes to fuel lines, the diameter of the line plays a crucial role in determining its ability to handle increased horsepower. Thicker fuel lines are designed to accommodate more powerful engines, ensuring efficient and reliable fuel delivery. The increased diameter allows for a larger volume of fuel to flow through the line, which is essential when dealing with high-performance engines that require a substantial amount of fuel to reach their full potential.
In contrast, thinner fuel lines may become a bottleneck when it comes to high-horsepower applications. These lines have a smaller cross-sectional area, which can restrict the flow of fuel, especially when the engine is producing a significant amount of power. As a result, the engine may not receive the necessary fuel to operate optimally, leading to reduced performance and potential issues.
The key to ensuring that your fuel lines can handle the power of your engine is to choose the appropriate diameter. Thicker lines are generally recommended for high-horsepower applications, as they provide a larger pathway for fuel to travel, minimizing the risk of restriction and ensuring that the engine receives the required amount of fuel. This is particularly important in racing or high-performance driving scenarios where every ounce of power matters.
It's worth noting that the material of the fuel line also plays a role in its performance. High-quality materials with good flexibility and durability are ideal to ensure that the lines can withstand the demands of high-horsepower engines without compromising on fuel delivery. Additionally, considering the length of the fuel lines is essential, as longer lines may require thicker diameters to maintain optimal performance.
In summary, when dealing with high-horsepower engines, thicker fuel lines are generally preferred to ensure efficient fuel delivery. Thinner lines may restrict the flow, leading to potential performance issues. By understanding the relationship between line diameter and horsepower, you can make informed decisions to optimize your engine's performance and ensure a reliable fuel supply.
Pipe Thread Sealant: Essential for Fuel Line Maintenance?
You may want to see also
Length and Routing: Longer lines with complex routes can reduce pressure and performance
The length and routing of a fuel line are critical factors that can significantly impact the performance and efficiency of a fuel delivery system, especially when considering the power output it needs to support. Longer fuel lines, while sometimes necessary for specific vehicle designs or engine configurations, can introduce challenges that affect the overall performance.
When a fuel line is extended, it creates a longer path for the fuel to travel from the tank to the engine. This increased length can lead to a few key issues. Firstly, the longer distance means that the fuel has to travel through more air, which can result in a slight reduction in fuel pressure. This is because the fuel has to overcome the force of gravity and the resistance of the air as it moves through the line. Secondly, longer lines are more susceptible to pressure drops due to the increased surface area exposed to the air. This can lead to a situation where the fuel pressure at the engine is lower than the ideal pressure required for optimal performance.
The routing of the fuel line is another crucial aspect. Complex routes, such as those that twist and turn around various engine components, can also impact performance. These intricate paths can cause the fuel line to experience increased friction and stress, especially during acceleration or when the vehicle is in motion. The fuel line may rub against sharp edges or vibrate against other parts, leading to potential damage over time. Such damage can result in fuel leaks, which not only reduce performance but also pose safety risks.
To optimize the fuel delivery system, it is essential to keep the fuel lines as short as possible while ensuring they are properly routed. This can be achieved by carefully planning the layout of the fuel system during the vehicle's design phase. Engineers should aim to minimize the length of the lines and avoid complex routes that could compromise performance. Additionally, using flexible fuel lines with protective coatings can help reduce friction and the risk of damage.
In summary, longer fuel lines and complex routing can negatively impact the pressure and performance of the fuel delivery system. Engineers and mechanics should be mindful of these factors to ensure optimal power output and system longevity. Proper design and maintenance can help mitigate these issues, ensuring that the fuel system operates efficiently, even under high-performance conditions.
Dodge Ram Fuel Line Shortening: A Step-by-Step Guide
You may want to see also
Fuel Pump Capacity: The pump's flow rate must match the line's capacity for optimal horsepower
When it comes to maximizing the performance of your engine, understanding the relationship between fuel pump capacity and horsepower is crucial. The fuel pump's flow rate plays a pivotal role in ensuring that your engine receives the necessary fuel for optimal power output. Here's a detailed breakdown of why this correlation is essential.
The primary function of a fuel pump is to deliver fuel from the tank to the engine's injectors or carburetor at the required pressure and volume. The flow rate, measured in gallons per minute (GPM), determines how much fuel the pump can supply in a given time. For instance, if your engine requires a specific amount of fuel to reach its peak horsepower, the pump must be capable of delivering that amount efficiently. If the flow rate is insufficient, the engine may not receive enough fuel, resulting in reduced power and potential performance issues.
An 8-fuel line, a common configuration in many automotive applications, has a specific capacity in terms of flow rate. This capacity is typically measured in gallons per minute and varies depending on the line's diameter, length, and material. When designing or modifying an engine, it's essential to consider the fuel line's capacity and match it with the pump's flow rate. If the pump's flow rate exceeds the line's capacity, it can lead to fuel pressure drops, ensuring that the fuel reaches the engine at the right pressure and volume.
To achieve optimal horsepower, the fuel pump's flow rate should be carefully selected to match the fuel line's capacity. This ensures that the engine receives the precise amount of fuel required for efficient combustion. For example, if your engine operates best with a specific fuel-to-air ratio, the pump must deliver the corresponding amount of fuel to maintain this ratio. Any discrepancy can lead to poor performance, such as reduced power, poor throttle response, or even engine misfires.
In summary, the fuel pump's flow rate is a critical factor in determining the horsepower output of your engine. It must be carefully matched with the fuel line's capacity to ensure efficient fuel delivery. By understanding this relationship, you can make informed decisions when upgrading or modifying your engine's fuel system, ultimately unlocking the full potential of your vehicle's performance.
Understanding 1-2A Fuel Line Tubing: A Comprehensive Guide
You may want to see also
Engine Requirements: Engine specifications dictate the necessary fuel line size for specific horsepower levels
When it comes to engine performance and fuel delivery, the relationship between horsepower and fuel line size is a critical aspect of engine design and maintenance. Engine specifications play a pivotal role in determining the appropriate fuel line size required to support a specific horsepower output. This is because the fuel line acts as the conduit for delivering fuel to the engine, and its diameter and construction must be able to handle the flow rate necessary to meet the engine's demands.
Engineers and mechanics often refer to engine specifications sheets, which provide detailed information about the engine's performance capabilities, including the recommended fuel line size. These specifications are derived from extensive testing and research, ensuring that the engine operates optimally within its performance envelope. For instance, an engine with a higher horsepower output will require a larger fuel line to accommodate the increased fuel flow needed to sustain that power level.
The calculation of the required fuel line size involves considering factors such as the engine's displacement, compression ratio, and the desired horsepower output. A larger engine displacement, for example, will demand a more substantial fuel line to manage the higher volume of fuel required. Similarly, a higher compression ratio can lead to increased fuel pressure, necessitating a fuel line with a larger diameter to handle the additional stress.
Engine requirements dictate that the fuel line size should be proportional to the engine's horsepower. A fuel line that is too small may restrict fuel flow, leading to reduced performance and potential engine damage. Conversely, an oversized fuel line could result in unnecessary fuel wastage and increased system complexity. Therefore, adhering to the engine manufacturer's recommendations for fuel line size is essential to ensure optimal performance and longevity.
In summary, engine specifications are the guiding principle for determining the necessary fuel line size to support specific horsepower levels. By understanding and following these requirements, engine enthusiasts and professionals can ensure that their engines receive the appropriate fuel delivery system, enabling them to reach their full potential while maintaining reliability and efficiency.
Is a Larger Return Fuel Line Necessary for Your Chevy Lumina?
You may want to see also
Frequently asked questions
The horsepower capacity of an 8-fuel line depends on various factors, including the engine's design, the fuel pump's capabilities, and the overall system efficiency. Generally, an 8-fuel line can support engines with power outputs ranging from 300 to 600 horsepower, but this can vary.
The horsepower limit is influenced by the fuel line's diameter, length, and material. Thicker and larger-diameter fuel lines can handle higher pressure and flow rates, allowing for more powerful engines. Additionally, the fuel pump's capacity and the engine's fuel injection system play a crucial role in determining the horsepower potential.
Yes, an 8-fuel line can be designed to accommodate high-performance engines. However, it requires careful consideration of the engine's requirements, including fuel pressure, flow rate, and the need for efficient fuel delivery. Upgrading the fuel line to a higher-quality material and increasing its diameter can enhance its performance capabilities.
Using an 8-fuel line for high horsepower engines may carry some risks if not properly installed and maintained. These risks include potential fuel leaks, increased pressure that could lead to line failure, and the need for precise tuning to avoid engine performance issues. Proper installation, regular inspections, and using high-quality fuel lines can mitigate these risks.
Consulting with automotive experts or engine specialists is recommended to determine the appropriate horsepower capacity. They can assess your engine's requirements, consider factors like engine displacement, compression ratio, and intended use, and suggest the optimal fuel line specifications.