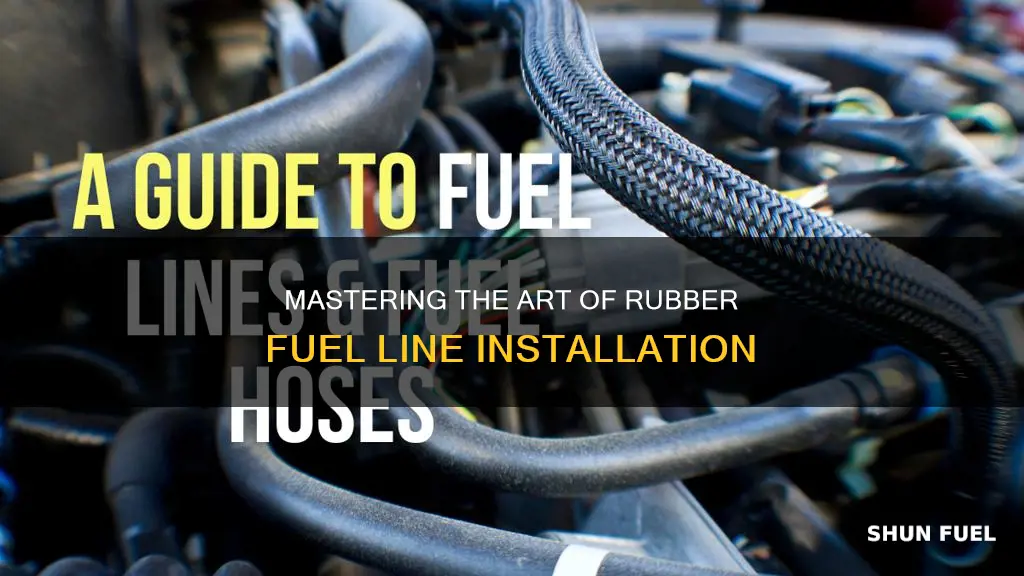
Starting a rubber fuel line is a crucial step in any engine-powered vehicle or equipment setup. It involves connecting the fuel source, typically a fuel tank, to the engine's fuel system. This process requires careful consideration of the materials and connections to ensure a secure and efficient fuel supply. The rubber fuel line is a flexible hose that carries fuel from the tank to the engine, and it must be properly installed to prevent leaks and ensure optimal performance. This guide will provide a step-by-step approach to help you understand the process and ensure a successful installation.
What You'll Learn
- Prepare Tools: Gather necessary tools like fuel line, connectors, and a fuel pump
- Clean Hoses: Ensure old fuel lines are clean and free of debris
- Cut and Fit: Measure and cut the new fuel line to the correct length
- Connect Securely: Use the right connectors and ensure a tight, leak-free seal
- Test and Adjust: Check for leaks and adjust as needed
Prepare Tools: Gather necessary tools like fuel line, connectors, and a fuel pump
Before you begin, it's crucial to gather all the necessary tools and materials to ensure a smooth and efficient process. Here's a step-by-step guide on preparing the tools required for starting a rubber fuel line:
Fuel Line and Connectors: The primary component you'll need is the fuel line itself, which is typically made of rubber or a similar flexible material. Measure and cut the fuel line to the appropriate length, ensuring it fits the specific area where it will be installed. Along with the fuel line, you'll require various connectors to join the line to the fuel tank, pump, and other components. These connectors can be quick-release fittings, barbed connectors, or any other type suitable for your fuel line system. Make sure to have enough connectors to join the fuel line to all the necessary parts.
Fuel Pump: A fuel pump is essential to ensure a steady flow of fuel from the tank to the engine. If you're replacing an existing pump, ensure you have the correct model that matches your engine's requirements. If you're installing a new pump, consider the type—electric or mechanical—and choose one that suits your needs.
Other Tools: In addition to the above, you'll need some basic hand tools. These include a wrench or socket set for tightening connections, a pair of pliers for gripping and bending, and a fuel filter (if not already included in your purchase). It's also a good idea to have a fuel container for testing the pump's functionality.
By gathering these tools and materials, you'll be well-prepared to begin the process of installing or repairing a rubber fuel line. Remember to always refer to the manufacturer's instructions or seek professional guidance if you're unsure about any step.
Perfect Fuel Line Size for Yamaha 150 Ox Ox66
You may want to see also
Clean Hoses: Ensure old fuel lines are clean and free of debris
Before you begin the process of starting a rubber fuel line, it is crucial to ensure that the old fuel lines are thoroughly cleaned and free of any debris. This step is often overlooked but is essential for the safe and efficient operation of your vehicle's fuel system. Over time, fuel lines can accumulate dirt, rust, and other contaminants, which can lead to reduced performance and potential issues. Here's a detailed guide on how to clean your fuel lines:
- Identify the Fuel Lines: Locate the fuel lines in your vehicle. These are typically rubber tubes that carry fuel from the fuel tank to the engine. They are usually connected to the fuel pump and the injectors or carburetor. It's important to identify the correct lines to avoid any accidental disconnections.
- Remove the Fuel Tank: To access the fuel lines, you'll need to remove the fuel tank. This process may vary depending on your vehicle's make and model. Generally, you'll need to drain the fuel tank, locate the mounting bolts, and carefully lift or slide the tank out of its position. Ensure you have a suitable container to catch any remaining fuel.
- Inspect and Clean the Fuel Tank: Once the tank is removed, inspect the inside for any signs of corrosion or contamination. Use a fuel tank cleaner or a mixture of vinegar and water to flush out any debris. This step is crucial to ensure that the fuel lines are not contaminated with old, dirty fuel. Rinse the tank thoroughly to remove any residue.
- Disassemble the Fuel Lines: Carefully disconnect the fuel lines from the fuel pump, injectors, and the tank. Take note of the connections and their positions. You may need to use specific tools to loosen the fittings, especially if they are tight. As you disconnect the lines, inspect them for any signs of damage, cracks, or blockages.
- Clean the Fuel Lines: Now, you can clean the fuel lines. Soak the lines in a fuel line cleaner or a mixture of warm water and dish soap. This will help loosen and remove any built-up debris, rust, or old fuel residue. You can also use a small brush or a fuel line cleaning tool to scrub the inside of the lines, ensuring a thorough clean.
- Reassemble and Test: After cleaning, reassemble the fuel lines, ensuring they are connected securely. Reinstall the fuel tank and test the system by starting the vehicle. Check for any leaks and ensure that the fuel lines are functioning properly. This step is vital to guarantee that the cleaning process has been effective.
By following these steps, you can ensure that your fuel lines are clean and ready for the new fuel line installation process. Proper cleaning is an essential maintenance task to keep your vehicle's fuel system in optimal condition.
Perfect Fuel Line Fit for Your 1992 Polaris Trail Deluxe
You may want to see also
Cut and Fit: Measure and cut the new fuel line to the correct length
Before you begin the process of replacing or installing a new rubber fuel line, it's crucial to measure and cut it to the correct length. This step ensures a proper fit and prevents any unnecessary strain or damage to the line during installation. Here's a detailed guide on how to measure and cut the fuel line accurately:
Step 1: Identify the Old Line's Length
Start by removing the old fuel line from the vehicle. Carefully inspect the line to identify any unique markings or measurements. Often, the original equipment manufacturer (OEM) will provide specific length measurements on the fuel line itself or on the vehicle's manual. Take note of these measurements as they will serve as a reference for the new line.
Step 2: Measure and Mark
Place the old fuel line on a flat surface and measure its length using a flexible measuring tape or a ruler. Ensure the tape is straight and taut to get an accurate measurement. Mark the measured length on the old line with a permanent marker or a piece of tape. This marking will guide you when cutting the new line.
Step 3: Prepare the New Line
Lay out the new rubber fuel line on a clean, flat area. Compare it to the marked length of the old line. If the new line is longer, you can adjust it by carefully cutting off the excess length using a sharp utility knife or a fuel line cutter. If it's shorter, you'll need to consider how to extend it or if an alternative length is available.
Step 4: Precision Cutting
When cutting the fuel line, precision is key. Use a sharp, dedicated fuel line cutter or a sharp knife with a guard to ensure a clean and accurate cut. Place the cutting tool along the marked length and make a single, smooth cut. Avoid applying excessive force, as it may compromise the line's integrity.
Step 5: Test the Fit
After cutting the new fuel line to the correct length, carefully slide it into place, connecting it to the fuel source and the destination component (e.g., the fuel tank or engine). Ensure it fits snugly without any excessive bending or kinking. Test the line by applying slight pressure to check for any leaks or vulnerabilities.
By following these steps, you can ensure that the new rubber fuel line is properly measured, cut, and fitted, providing a reliable and safe fuel supply for your vehicle. Remember, accurate measurements and precise cutting are essential to avoid potential issues during installation and long-term performance.
Mastering the Art of GM Fuel Line Clip Removal: A Step-by-Step Guide
You may want to see also
Connect Securely: Use the right connectors and ensure a tight, leak-free seal
When it comes to connecting a rubber fuel line, ensuring a secure and leak-free seal is crucial to prevent any potential hazards. The process requires careful consideration of the connectors used and the overall assembly to guarantee a reliable connection. Here's a step-by-step guide to achieving a tight and secure seal:
Choose the Right Connectors: The first step is to select the appropriate connectors for your rubber fuel line. Rubber fuel lines are commonly used in various applications, such as automotive, marine, and industrial settings. Different connectors are designed for specific purposes, so it's essential to match the connector type to your fuel line's requirements. For example, you might need a barbed connector for a quick and easy connection or a compression fitting for a more secure and permanent seal. Consider the material compatibility, size, and thread type to ensure a perfect fit.
Prepare the Fuel Line and Connector: Before connecting, ensure that both the fuel line and the connector are clean and free from any debris or contaminants. Use a cloth or a soft brush to wipe down the surfaces, removing any dirt or old sealant. This step is crucial to ensure a proper bond between the fuel line and the connector. If you're reusing a connector, inspect it for any signs of damage or wear and replace it if necessary.
Assembly Process: Start by inserting the fuel line into the connector, following the manufacturer's instructions. Ensure that the line is fully seated and aligned correctly. For barbed connectors, twist the fuel line onto the barb until it is securely locked in place. With compression fittings, insert the fuel line into the fitting and crimp or tighten it according to the specified method. Make sure there is no kinking or bending of the fuel line during the assembly process, as this can compromise the seal.
Tighten Securely: Once the connector is in place, tighten it securely using the appropriate tool. Over-tightening can damage the fuel line, so be cautious and use the right amount of force. The goal is to achieve a tight, leak-free connection without causing any harm to the rubber material. Check for any leaks by gently pressing around the connector and observing if any fuel escapes. If there are any leaks, carefully disassemble the connection and re-tighten it, ensuring a secure seal.
Testing and Inspection: After completing the connection, it's essential to test the system to ensure its integrity. Start the engine and monitor for any signs of fuel leakage. Check the area around the connection for any fuel stains or damp spots. If everything is secure, the engine should run smoothly without any fuel-related issues. Regularly inspect the connections, especially in high-vibration environments, to ensure the seal remains intact over time.
By following these steps and paying close attention to the connector selection and assembly process, you can create a secure and leak-free connection for your rubber fuel line. This approach ensures the safe and efficient operation of your fuel system, reducing the risk of fuel leaks and potential engine damage.
Safe and Effective Methods to Thaw Frozen Car Fuel Lines
You may want to see also
Test and Adjust: Check for leaks and adjust as needed
When you've installed or replaced a rubber fuel line, it's crucial to test and adjust it to ensure it functions correctly and safely. This process involves checking for leaks and making any necessary adjustments to guarantee a tight and secure fit. Here's a step-by-step guide to help you through this critical phase:
Step 1: Visual Inspection
Start by visually inspecting the fuel line for any visible signs of damage or wear. Look for cracks, tears, or any other physical damage that could compromise the line's integrity. Also, check for any signs of deterioration, especially if the line has been exposed to harsh conditions or chemicals. If you notice any issues, you may need to replace the line or make repairs before proceeding.
Step 2: Leak Test
The primary purpose of this step is to ensure that there are no leaks in the fuel line. You can perform a leak test using a simple method:
- Disconnect the fuel line from the fuel tank and the engine.
- Apply a small amount of diesel fuel or a suitable fuel line sealer to the connections and the interior of the line.
- Reattach the fuel line and securely fasten it.
- Start the engine and allow it to run.
- Observe the fuel line for any fuel leakage. You can also use a rag or paper towel to catch any potential leaks.
- If you detect any leaks, you'll need to adjust the connections or consider replacing the line if the damage is extensive.
Step 3: Adjusting Connections
If the leak test reveals any issues, it's time to adjust the connections:
- Carefully disconnect the fuel line from the engine and the fuel tank.
- Inspect the connections for any signs of damage or corrosion.
- Use a fuel line cleaner or a suitable solvent to remove any debris or contaminants.
- Ensure that all connections are tight and secure. You can use a wrench or a fuel line tool to tighten the fittings, but be careful not to overtighten, as this can damage the line.
- Reattach the fuel line and repeat the leak test to ensure the issue has been resolved.
Step 4: Final Adjustments
After addressing any leaks, make any final adjustments to ensure the fuel line is functioning optimally:
- Check the fuel line's flexibility and ensure it can move freely without kinking or bending excessively.
- Verify that the line is securely attached to the engine and fuel tank, with no loose connections.
- Inspect the line for any signs of strain or stress, especially if it's routed through tight spaces or under the vehicle.
- If everything looks good, you can start the engine and run it for a while to ensure the fuel line is functioning as expected.
Remember, proper testing and adjustment are essential to ensure the safety and efficiency of your fuel system. Always follow manufacturer guidelines and best practices when working with fuel lines to avoid any potential hazards.
Engine Trouble: What Happens When Your Fuel Line Seals Fail
You may want to see also
Frequently asked questions
A rubber fuel line is a type of flexible hose used to transfer fuel from a tank to an engine. It is commonly used in automotive applications, especially for classic or vintage cars that require a more flexible and durable fuel delivery system compared to rigid metal lines. Rubber fuel lines offer better resistance to fuel-related chemicals, making them ideal for vehicles with older, less refined fuel systems.
Selecting the appropriate size is crucial for optimal performance and safety. Measure the length of the fuel line required, considering the distance between the fuel tank and the engine. Rubber fuel lines are typically available in various diameters, with common sizes ranging from 3/8" to 1/2" ID (inside diameter). Consult your vehicle's manual or seek advice from a mechanic to determine the correct size for your specific make and model.
While it is possible to install a rubber fuel line yourself, especially for DIY enthusiasts, it is generally recommended to seek professional assistance for a secure and reliable setup. Proper installation involves ensuring a tight fit, avoiding sharp bends, and using appropriate fuel line connectors. A qualified mechanic can ensure the line is correctly routed, secured, and compatible with your vehicle's fuel system, minimizing the risk of leaks or fuel contamination.
Proper maintenance is essential to keep your rubber fuel line in good condition. Regularly inspect the line for any signs of damage, cracks, or deterioration, especially in areas prone to heat or vibration. Keep the line clean and free from debris. Avoid using sharp objects that could puncture the rubber. In colder climates, consider using a fuel line insulator to protect against freezing temperatures. Regularly check for leaks and ensure all connections are secure.