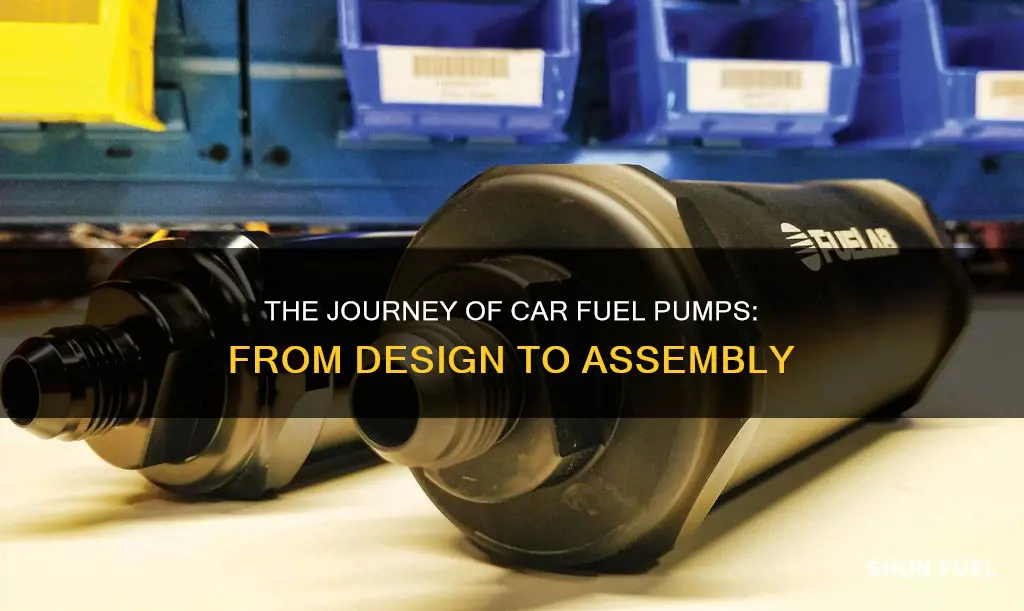
The intricate process of manufacturing car fuel pumps involves a series of precise steps. It begins with the selection of high-quality materials, such as durable metals or alloys, which are then meticulously shaped and formed using advanced manufacturing techniques. Engineers design the pump's components, including the pump body, inlet and outlet valves, and the intricate internal mechanisms that facilitate the transfer of fuel. These parts are assembled with utmost care, ensuring every piece is aligned and secured in place. Finally, rigorous testing and quality control measures are implemented to guarantee the pump's reliability and performance, ensuring it can efficiently deliver fuel to the engine while withstanding the demands of everyday use.
What You'll Learn
- Design and Engineering: Engineers create precise blueprints for the fuel pump's structure and function
- Materials Selection: Choose materials like steel, aluminum, or plastics based on durability and cost
- Manufacturing Process: Involves molding, casting, or machining to shape the pump components
- Assembly: Components are assembled, including the pump head, diaphragm, and electrical connections
- Testing and Quality Control: Rigorous testing ensures the pump meets performance and safety standards
Design and Engineering: Engineers create precise blueprints for the fuel pump's structure and function
The process of designing and engineering a car fuel pump involves a meticulous approach to ensure optimal performance and reliability. Engineers play a pivotal role in this phase, utilizing their expertise to create detailed blueprints that guide the manufacturing process. The design phase begins with a comprehensive understanding of the vehicle's requirements and the specific needs of the fuel system. Engineers analyze the engine's power output, fuel consumption rates, and the overall vehicle architecture to determine the pump's necessary specifications. This includes calculating the required flow rate, pressure, and dimensions to match the vehicle's fuel requirements.
Once the requirements are established, engineers employ computer-aided design (CAD) software to create precise 3D models of the fuel pump. These models incorporate intricate details, such as the pump's housing, impeller, and diaphragm, ensuring every component is accurately represented. The CAD software allows for easy modification and optimization, enabling engineers to fine-tune the design for efficiency and performance. By virtually testing and simulating different configurations, they can identify potential issues and make adjustments before the physical prototype is built.
In the engineering phase, the focus shifts to creating detailed blueprints that serve as the manufacturing instructions. These blueprints include precise dimensions, material specifications, and assembly guidelines. Engineers specify the type of materials to be used, considering factors like corrosion resistance, durability, and compatibility with fuels. For instance, the pump's housing might require a specific alloy to withstand high-pressure fuel environments. The blueprints also outline the pump's mounting positions, connections, and integration with the fuel tank and engine components.
Attention to detail is crucial during this stage to ensure the fuel pump's functionality and longevity. Engineers must consider factors such as noise reduction, vibration damping, and thermal management to enhance the pump's performance and minimize potential issues. They also define the manufacturing processes, including casting, machining, and assembly techniques, to ensure the pump's production aligns with the designed specifications.
After the blueprints are finalized, they are shared with manufacturers, providing them with the necessary information to produce the fuel pump. This collaborative effort between engineers and manufacturers ensures that the final product meets the original design intent, delivering efficient and reliable fuel supply to the vehicle's engine. The engineering and design process is a critical aspect of fuel pump manufacturing, requiring precision, technical expertise, and a systematic approach to create a vital component for modern automobiles.
Unleash Your Engine's Power: A Guide to Opening Fuel Injectors
You may want to see also
Materials Selection: Choose materials like steel, aluminum, or plastics based on durability and cost
The selection of materials for a car fuel pump is a critical aspect of its design and performance. The primary goal is to ensure durability, reliability, and cost-effectiveness while meeting the specific requirements of the fuel pump's function. Here's an overview of the materials commonly used and the considerations for their choice:
Steel: This is a traditional and robust material for fuel pump construction. It offers excellent durability and strength, making it ideal for withstanding the demanding conditions inside an engine compartment. Steel fuel pumps are known for their longevity and ability to handle high-pressure environments. However, steel can be heavier and more expensive compared to other options. The choice of steel grade is crucial; for instance, stainless steel provides additional corrosion resistance, ensuring the pump's longevity in various fuel types.
Aluminum: Lighter and more cost-effective than steel, aluminum is often used for fuel pump components that require a balance between strength and weight reduction. It is an excellent choice for parts that experience moderate stress and heat. Aluminum's corrosion resistance is also beneficial, especially in fuel systems where moisture and various fuel types can be present. Modern aluminum alloys can provide the necessary strength while keeping the overall weight of the fuel pump low.
Plastics: Plastic materials, such as engineering plastics (e.g., nylon, polyamide), are increasingly used in fuel pump design due to their lightweight, corrosion resistance, and cost-effectiveness. These plastics can handle moderate temperatures and pressures, making them suitable for specific pump components. For instance, the impeller, which is responsible for moving the fuel, can be made from a durable plastic that ensures efficient flow while maintaining its shape over time. Plastic fuel pumps are often used in smaller vehicles or applications where weight reduction is a priority.
When selecting materials, engineers must consider the fuel pump's operating environment, including temperature extremes, fuel type, and the presence of moisture. For instance, aluminum might be preferred in high-temperature environments, while steel could be chosen for its strength in extreme cold. Additionally, the cost of materials is a significant factor, especially for mass-produced vehicles, where lightweight and cost-effective solutions are essential.
In summary, the choice of materials for a car fuel pump involves a careful balance between durability, cost, and the specific requirements of the vehicle's engine and fuel system. Each material offers unique advantages, and the decision should be based on a comprehensive understanding of the pump's function and the overall vehicle design.
Siphoning Fuel: Can It Still Work on Modern Cars?
You may want to see also
Manufacturing Process: Involves molding, casting, or machining to shape the pump components
The manufacturing process of a car fuel pump involves several intricate steps to ensure its functionality and reliability. One of the primary methods used to shape the pump components is molding, which is a common technique in the automotive industry. This process typically begins with the creation of a mold, which is designed to mimic the desired shape of the fuel pump. The mold can be made from various materials, such as aluminum, steel, or even plastic, depending on the specific requirements of the pump. Once the mold is prepared, it is used to inject a molten material, often a type of plastic or composite, into it. This material solidifies within the mold, taking on the exact shape of the pump component. This method allows for the production of intricate and precise parts, ensuring the fuel pump's performance and durability.
Casting is another manufacturing process employed in fuel pump production. This technique involves pouring a molten material, typically a metal alloy, into a mold to create the desired shape. The mold is carefully designed to include any necessary internal passages and chambers to form the pump's components. After the material solidifies, the mold is removed, revealing the shaped part. Casting is particularly useful for creating complex geometries and ensuring the structural integrity of the fuel pump. The process requires precise control of temperature and cooling rates to achieve the desired material properties.
Machining is a subtractive manufacturing process that is often used in conjunction with molding and casting. It involves removing material from a solid block to create the final pump components. The raw material, usually a metal blank, is secured in a machine tool, and a cutting tool is used to shape it. Machining allows for fine adjustments and precise tolerances, ensuring the fuel pump's components fit perfectly together. This process may include operations like turning, milling, grinding, and drilling to achieve the required dimensions and surface finishes. Machining is crucial for achieving the intricate internal passages and precise alignments necessary for the pump's efficient operation.
The manufacturing process of a car fuel pump often involves a combination of these techniques. For instance, a pump might be initially molded to create the outer casing, and then machining is used to refine the internal components, ensuring optimal performance. The choice of manufacturing method depends on factors such as the required material properties, desired production volume, and the complexity of the pump's design. Each step in the manufacturing process is carefully executed to meet the stringent standards of the automotive industry, ensuring that the fuel pump delivers reliable performance under varying driving conditions.
F1 Fuel Efficiency: How Do Cars Stay Afloat?
You may want to see also
Assembly: Components are assembled, including the pump head, diaphragm, and electrical connections
The assembly process of a car fuel pump is a precise and intricate task, requiring careful attention to detail. Once all the individual components have been manufactured, the assembly begins. The pump head, a critical component, is attached to the base or housing, ensuring it is securely positioned. This step demands precision to guarantee the pump's functionality and longevity. The diaphragm, a flexible membrane, is then carefully inserted into the pump head. This diaphragm plays a vital role in the pumping mechanism, expanding and contracting to facilitate fuel flow. It is crucial to align the diaphragm correctly to avoid any potential leaks or performance issues.
After the pump head and diaphragm are in place, the electrical connections are made. These connections are essential for the pump's operation, as they provide the necessary power and control signals. Wires are carefully soldered or crimped to the pump's terminals, ensuring a secure and reliable connection. The electrical assembly also involves installing any sensors or control modules that may be present, allowing for precise fuel pressure monitoring and adjustment. This stage requires a high level of skill to ensure the electrical system functions flawlessly.
During assembly, quality control checks are performed at various stages. Each component is inspected for any defects or deviations from the design specifications. This includes checking the pump's flow rate, pressure, and electrical connections to ensure they meet the required standards. Any issues identified during this process are addressed immediately, and the components are either replaced or adjusted to maintain the overall quality of the fuel pump.
The assembly process also involves the use of specialized tools and equipment. These tools are designed to handle the delicate components and ensure precise assembly. For instance, precision torque tools are used to apply the correct amount of force when securing electrical connections, preventing damage or loose fittings. Specialized jigs and fixtures may also be employed to hold components in place during assembly, ensuring consistent and accurate results.
Once the assembly is complete, the fuel pump undergoes rigorous testing. This includes bench testing to verify its performance and functionality, as well as more comprehensive system-level testing to ensure it works seamlessly with the vehicle's fuel system. This testing phase is crucial to identify and rectify any potential issues before the final product is installed in a vehicle.
Old Fuel Filter: Can It Cause Engine Failure?
You may want to see also
Testing and Quality Control: Rigorous testing ensures the pump meets performance and safety standards
The manufacturing process of a car fuel pump involves several critical stages, and testing and quality control are integral to ensuring its reliability and performance. Once the fuel pump is assembled, it undergoes rigorous testing to verify its functionality and adherence to strict standards. This testing process is designed to identify any potential issues or defects, ensuring that the final product meets the required specifications.
One of the initial tests is a visual inspection, where technicians examine the pump for any visible defects or damage. This step is crucial as it helps identify any manufacturing errors or imperfections that might affect the pump's performance. The inspection includes checking the pump's housing, connections, and overall assembly to ensure all components are correctly aligned and securely fastened.
Performance testing is then conducted to evaluate the pump's efficiency and functionality. This involves measuring the pump's flow rate, pressure, and power consumption under various conditions. Technicians simulate different driving scenarios to assess the pump's ability to deliver fuel accurately and consistently. The test results are compared against predefined performance benchmarks to ensure the pump operates within the specified parameters.
Safety is a paramount concern, so the fuel pump must undergo rigorous safety testing. This includes pressure and temperature tests to simulate extreme conditions that the pump might encounter in a vehicle. By exposing the pump to high-pressure and high-temperature environments, engineers can identify potential failure points and ensure it meets safety regulations. Additionally, electrical tests are performed to verify the pump's compatibility with the vehicle's electrical system and to prevent any short circuits or electrical malfunctions.
Quality control also involves a series of tests to ensure the pump's longevity and durability. This includes vibration testing to simulate the pump's operation on the road and assess its resistance to mechanical stress. Furthermore, environmental tests are conducted to evaluate the pump's performance in different climatic conditions, ensuring it can withstand varying temperatures and humidity levels. These comprehensive tests guarantee that the fuel pump is robust, reliable, and capable of withstanding the demands of everyday use.
Nitro Fuel Sources: RC Car Enthusiasts' Ultimate Guide
You may want to see also
Frequently asked questions
Car fuel pumps are typically made from materials such as cast iron, aluminum, or brass. These materials are chosen for their durability, corrosion resistance, and ability to withstand high pressure and temperatures, which are essential for the pump's functionality in an engine.
The fuel pump assembly involves several steps. Firstly, the pump's components are manufactured using precision machining and casting techniques. These parts include the pump body, check valves, and pressure relief valves. Once assembled, the pump is tested to ensure it meets the required specifications. The assembly also includes the installation of the pump into the fuel tank, where it is connected to the fuel lines and electrical wiring.
Absolutely! The fuel pump is a critical component in the fuel injection system of an engine. Its primary function is to deliver the required amount of fuel at the precise pressure needed for efficient combustion. The pump ensures that the engine receives a consistent fuel supply, optimizing power output and overall performance. It also helps maintain the engine's efficiency and reduces fuel consumption, making it an essential part of modern vehicle engines.