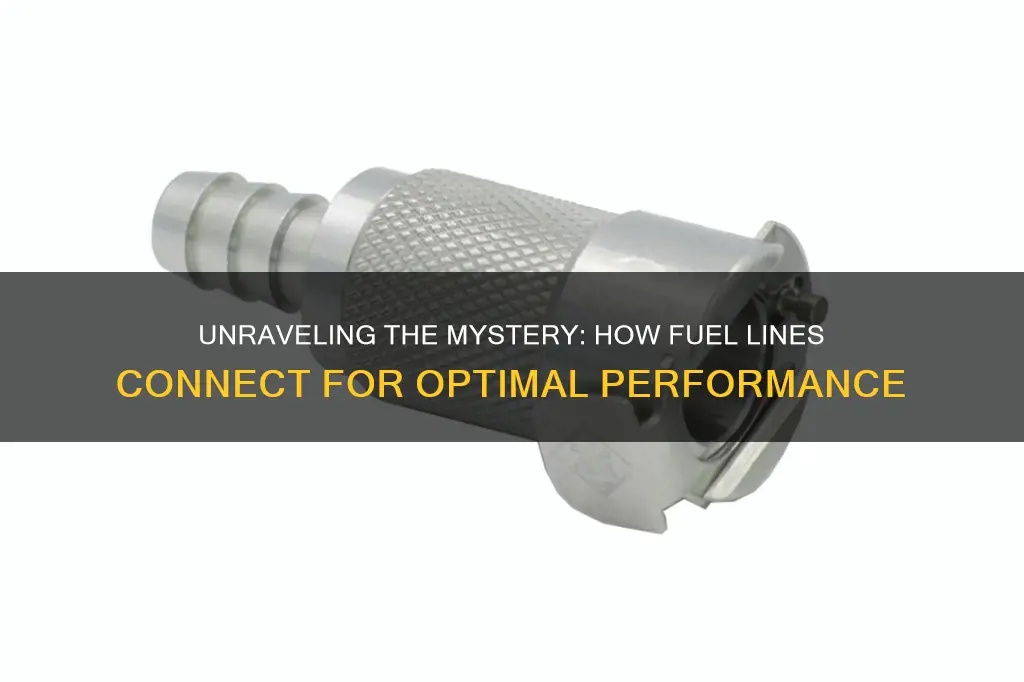
Fuel lines are an essential component of any vehicle's fuel system, and understanding how they connect is crucial for maintaining a reliable and efficient engine. These lines are responsible for transporting fuel from the tank to the engine, and their proper connection ensures that the engine receives the necessary fuel for optimal performance. The process involves precise connections to prevent fuel leaks and maintain the integrity of the fuel system. This paragraph will explore the various methods and considerations involved in connecting fuel lines, highlighting the importance of proper installation and maintenance to ensure a vehicle's longevity and reliability.
What You'll Learn
- Fuel Line Materials: Different materials offer varying durability and flexibility
- Fuel Line Routing: Proper placement prevents damage and ensures efficient fuel flow
- Fuel Line Clamps: Secure connections with various types of clamps for different needs
- Fuel Line Filters: Filters prevent contaminants from entering the engine
- Fuel Line Pressure: Maintaining optimal pressure ensures efficient fuel delivery
Fuel Line Materials: Different materials offer varying durability and flexibility
When it comes to fuel lines, the choice of material is crucial as it directly impacts the performance, durability, and reliability of the fuel delivery system. Different materials offer varying levels of flexibility, strength, and resistance to wear and tear, making them suitable for specific applications. Here's an overview of common fuel line materials and their characteristics:
Rubber: Rubber fuel lines are a traditional and widely used choice. They are known for their flexibility, making them ideal for accommodating engine vibrations and movements. Rubber is naturally resilient and can absorb minor impacts without permanent deformation. This material is often used for shorter fuel lines and is cost-effective. However, rubber may not be the best choice for long-term use in high-temperature environments, as it can degrade over time.
Reinforced Rubber: To enhance durability, some fuel lines are constructed with reinforced rubber. This involves layering rubber with a flexible fabric or wire, providing additional strength and flexibility. Reinforced rubber lines are more resistant to punctures and can handle higher pressure, making them suitable for longer fuel lines and high-performance applications. They offer a good balance between flexibility and durability.
Braided Steel: Braided steel fuel lines are known for their exceptional strength and rigidity. The steel core is surrounded by a flexible rubber or synthetic material, creating a durable and flexible line. Braided steel is highly resistant to corrosion and can withstand extreme temperatures, making it ideal for high-performance engines and racing applications. While it may be more rigid than rubber, it provides excellent protection against fuel leaks and punctures.
Polyurethane: Polyurethane fuel lines offer a balance between flexibility and strength. They are more rigid than rubber but provide better resistance to fuel degradation and temperature changes. Polyurethane lines are often used in high-temperature environments and applications where flexibility is required. They are less flexible than rubber but offer improved durability and resistance to abrasion.
The choice of material depends on the specific requirements of the fuel system, including engine type, operating conditions, and desired performance. For example, high-performance engines may benefit from braided steel lines for their strength and resistance to fuel-related degradation. In contrast, standard vehicles might use reinforced rubber lines for their flexibility and cost-effectiveness. Understanding the properties of each material allows mechanics and enthusiasts to select the most appropriate fuel line for their needs, ensuring optimal fuel delivery and system longevity.
Choosing the Right Fuel Line for Your Outboard Motor: A Guide
You may want to see also
Fuel Line Routing: Proper placement prevents damage and ensures efficient fuel flow
Fuel lines are an essential component of any vehicle's fuel system, responsible for transporting fuel from the tank to the engine. Proper routing and placement of these lines are critical to ensure optimal performance, prevent damage, and maintain efficient fuel flow. Here's an in-depth guide on why and how to achieve this:
Understanding the Risks of Improper Routing:
Incorrectly routed fuel lines can lead to numerous issues. Firstly, sharp bends or kinks can restrict fuel flow, causing pressure drops and potential engine performance problems. Over time, these restrictions can lead to fuel starvation, especially during acceleration or high-load conditions. Secondly, fuel lines that are routed too close to hot engine components can overheat, leading to fuel degradation and potential engine damage. Additionally, sharp turns or tight spaces might cause the lines to rub against other parts, resulting in damage or leaks.
Key Principles of Proper Fuel Line Routing:
- Smooth Curves: Fuel lines should be routed with gentle, smooth curves to avoid creating pressure points or restricting flow. The general rule is to keep the radius of curvature as large as possible to minimize stress on the line.
- Minimize Bends: Straight runs are ideal, but if bends are necessary, they should be gradual and not exceed a certain angle (often 90 degrees) to prevent kinking.
- Avoid Heat Sources: Keep fuel lines away from hot engine components, exhaust systems, and other heat-generating areas. Insulation or protective sleeves might be required in such cases.
- Secure Mounting: Fuel lines should be securely mounted to prevent movement or vibration-induced damage. Use appropriate clamps or brackets to ensure a firm hold.
- Clearance: Allow sufficient clearance between the fuel lines and other vehicle components to prevent rubbing or interference.
Best Practices for Fuel Line Placement:
- Low and Horizontal: Route fuel lines as low and horizontal as possible to maintain consistent pressure and minimize the risk of damage from road irregularities.
- Group Lines Together: Grouping fuel lines together in bundles can help manage routing and provide some protection against damage from road debris.
- Use of Fuel Line Protectors: Consider using protective sleeves or shields, especially in areas prone to impact or vibration, to safeguard the lines from potential hazards.
- Regular Inspection: Regularly inspect fuel lines for any signs of damage, cracks, or leaks. Early detection can prevent costly repairs and ensure the vehicle's safety.
By adhering to these principles and best practices, you can ensure that your fuel lines are properly routed, minimizing the risk of damage and maximizing efficient fuel delivery to the engine.
Unraveling the Mystery: How Fuel Lines Power Your Engine
You may want to see also
Fuel Line Clamps: Secure connections with various types of clamps for different needs
Fuel line clamps are essential components in the intricate network of a vehicle's fuel system, ensuring secure and reliable connections between fuel lines and various components. These clamps play a critical role in maintaining the integrity of the fuel supply, preventing leaks, and ensuring optimal performance. When it comes to connecting fuel lines, understanding the different types of clamps available and their specific applications is crucial for a successful and safe installation.
One common type of fuel line clamp is the metal clamp, typically made from durable materials like stainless steel or aluminum. These clamps are known for their strength and ability to withstand high pressure and temperature variations. Metal clamps often feature a simple design with a U-shaped or V-shaped groove that securely holds the fuel line in place. They are ideal for heavy-duty applications, such as connecting fuel lines to fuel tanks or high-pressure fuel pumps. The metal's rigidity ensures a tight seal, minimizing the risk of fuel leakage and potential engine damage.
For applications requiring a more flexible connection, rubber or silicone clamps are commonly used. These clamps offer a degree of flexibility, allowing for slight movement and vibration dampening. The rubber or silicone material provides a soft yet secure grip on the fuel line, accommodating minor misalignments during installation. This type of clamp is often used in areas where the fuel line may experience some movement, such as under the hood or in engine compartments with limited space. The flexibility of these clamps helps to prevent excessive stress on the fuel line, ensuring a longer lifespan and reduced risk of damage.
In certain scenarios, specialized clamps are employed to meet specific requirements. For instance, fuel line clamps with gaskets or O-rings provide an additional layer of protection against leaks. These clamps have a built-in gasket or O-ring made from compatible rubber or silicone, creating a sealed connection between the clamp and the fuel line. This design is particularly useful in high-vibration environments or when connecting fuel lines to sensitive components, as the gasket or O-ring provides a reliable seal even under challenging conditions.
Furthermore, the choice of clamp material is essential for compatibility and performance. Stainless steel clamps, for example, offer excellent corrosion resistance, making them suitable for fuel lines exposed to harsh environments or those containing ethanol-blended fuels. On the other hand, aluminum clamps are lightweight and provide good heat dissipation, which can be beneficial in high-temperature applications. The selection of the appropriate clamp material ensures that the fuel line connection remains secure and reliable over the long term.
In summary, fuel line clamps are a critical aspect of maintaining a vehicle's fuel system, offering secure connections and preventing potential issues. From metal clamps for heavy-duty applications to rubber or silicone clamps for flexibility, each type serves a specific purpose. Understanding the various clamp options and their advantages allows mechanics and enthusiasts to make informed decisions when connecting fuel lines, ensuring optimal performance and longevity of the fuel system.
Fuel Costs: Should Truckers Include Fuel in Line Haul Rates?
You may want to see also
Fuel Line Filters: Filters prevent contaminants from entering the engine
Fuel line filters are an essential component of any vehicle's fuel system, designed to protect the engine from contaminants that could cause significant damage. These filters are strategically placed along the fuel lines, which are the pathways that carry fuel from the tank to the engine. The primary function of these filters is to trap and remove impurities, ensuring that only clean, high-quality fuel reaches the engine. This is crucial because impurities in fuel can lead to various engine issues, such as reduced performance, increased wear and tear, and even engine failure.
The design of fuel line filters varies, but they all share the common goal of contaminant removal. Some filters use a mesh or screen to physically trap particles, while others employ a more intricate process called 'adsorption,' where contaminants are drawn to and held by the filter's surface. This process is particularly effective in removing water, which can cause corrosion and damage to the engine's fuel system. Over time, water can lead to the formation of rust and other corrosive substances, which can block fuel lines and injectors, resulting in a loss of power and potential engine damage.
In addition to water, fuel line filters also target other common contaminants. These include sediment, which can accumulate and restrict fuel flow, and volatile organic compounds (VOCs), which are harmful chemicals that can evaporate and cause engine misfires. By capturing these impurities, filters ensure that the fuel remains clean and free-flowing, promoting optimal engine performance. Regular maintenance, including the replacement of fuel line filters, is vital to maintaining the health and longevity of the vehicle's engine.
The placement of these filters is strategic, often located close to the fuel tank and before the fuel reaches the engine. This positioning allows for the early detection and removal of contaminants, preventing them from causing further issues. It is recommended that drivers check their vehicle's manual to understand the specific locations of fuel line filters, as different makes and models may vary. Proper maintenance, including the timely replacement of these filters, is key to ensuring the vehicle's engine operates efficiently and reliably.
In summary, fuel line filters play a critical role in safeguarding the engine from contaminants. They are designed to capture and remove impurities, ensuring that the fuel supplied to the engine is clean and free from harmful substances. Regular maintenance and attention to these filters are essential to keep the vehicle's fuel system in optimal condition, ultimately contributing to the overall performance and longevity of the engine.
Kreem Fuel Tank Liner: A Comprehensive Guide to Installation and Benefits
You may want to see also
Fuel Line Pressure: Maintaining optimal pressure ensures efficient fuel delivery
Fuel line pressure is a critical aspect of ensuring efficient and reliable fuel delivery to an engine. Maintaining the correct pressure is essential for optimal performance and longevity of the fuel system. When the pressure is too low, it can lead to poor atomization of the fuel, resulting in incomplete combustion and reduced power output. Conversely, excessive pressure can cause fuel to vaporize, leading to potential issues with fuel stability and engine performance. Therefore, understanding and managing fuel line pressure is key to achieving the best possible engine operation.
The pressure in a fuel line is typically regulated by a fuel pump, which is designed to deliver fuel at a specific pressure to the engine. This pressure is often measured in pounds per square inch (PSI) and varies depending on the engine's requirements and the vehicle's specifications. For instance, a typical gasoline engine may operate within a fuel pressure range of 40 to 60 PSI, while diesel engines often require higher pressures, sometimes exceeding 100 PSI. Achieving and maintaining this precise pressure is crucial for the engine's ability to efficiently draw and utilize fuel.
One way to ensure optimal fuel line pressure is by using a fuel pressure regulator. This component is designed to limit the pressure within the fuel line to a predetermined value. It acts as a safety mechanism, preventing excessive pressure that could lead to fuel line damage or engine misfires. Regularly checking and replacing the fuel pressure regulator is essential, especially in high-performance vehicles, to guarantee consistent fuel delivery.
In addition to the regulator, the fuel pump itself plays a vital role in pressure management. The pump's performance can be influenced by factors such as electrical connections, pump wear, and contamination in the fuel. Ensuring that the fuel pump is in good condition and properly maintained is crucial for consistent pressure. Regular fuel filter changes and the use of high-quality fuel can also help prevent contamination, which can negatively impact pressure and engine performance.
Maintaining optimal fuel line pressure is a balance of precision and regular maintenance. It involves understanding the engine's requirements, using the appropriate fuel pressure regulator, and ensuring the fuel pump operates efficiently. By doing so, vehicle owners can guarantee that their engines receive the correct amount of fuel at the right pressure, resulting in improved performance, fuel efficiency, and overall engine longevity. Regular checks and attention to these details will contribute to a well-functioning fuel system.
Optimizing Performance: Choosing the Right Fuel Line for Your Atomic 4 Engine
You may want to see also
Frequently asked questions
Fuel lines are usually connected to the fuel tank using a quick-connect fitting or a threaded adapter. These fittings ensure a secure and leak-proof connection, allowing the fuel to flow efficiently from the tank to the engine.
A fuel line strainer is installed between the fuel tank and the engine to filter out contaminants and debris. It helps prevent dirt, rust, and other particles from entering the fuel system, ensuring clean fuel delivery and reducing the risk of engine issues.
Yes, fuel lines can be connected using a clamp-style fitting. This method involves inserting the fuel line into a sleeve and then clamping it securely in place. Clamps provide a reliable connection and are often used for temporary or low-pressure applications.
To achieve a tight seal, it's essential to use the correct type of fuel line and fitting for the specific application. Applying a small amount of fuel line adhesive or tape around the connection can also help create a secure seal. Proper alignment and tightening of fittings are crucial to avoid leaks.
Yes, fuel line connections can vary depending on the engine type and design. Some engines may use high-pressure fuel lines with specialized fittings, while others might have low-pressure lines with quick-connect adapters. It's important to consult the vehicle's manual or seek professional advice to ensure the correct connection method.