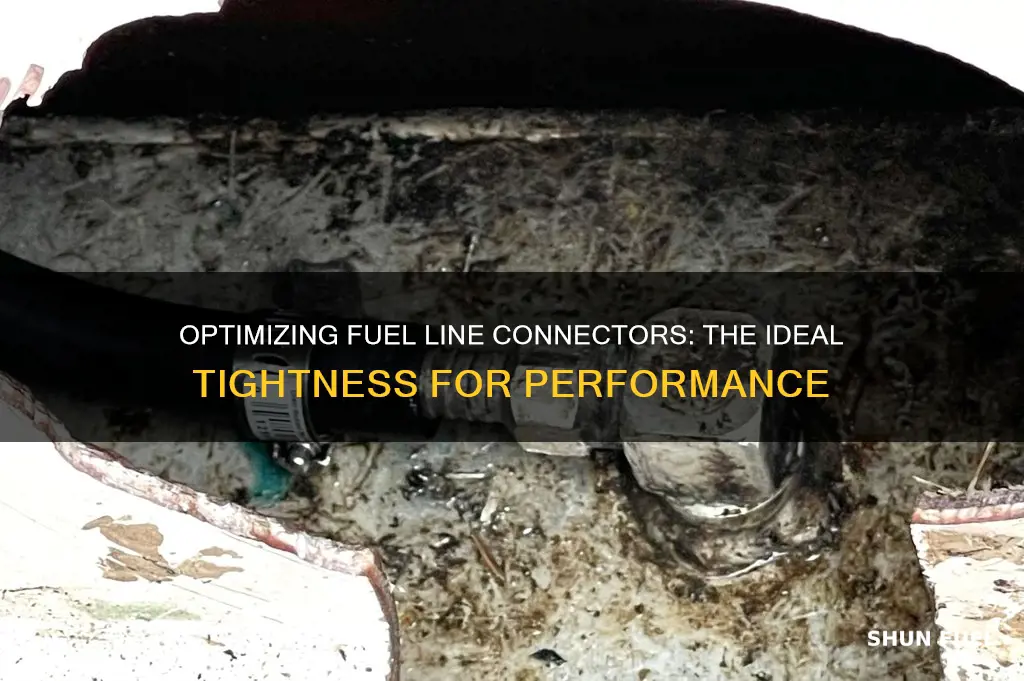
When it comes to fuel line connectors, ensuring a secure and tight connection is crucial for optimal performance and safety. The tightness of the connector plays a significant role in preventing fuel leaks, which can lead to engine misfires, reduced power, and potential safety hazards. In this guide, we'll explore the ideal tightness specifications for fuel line connectors, providing you with the knowledge to maintain your vehicle's fuel system effectively. Understanding the correct torque settings and visual cues for a secure connection will help you achieve a reliable and leak-free fuel delivery system.
Characteristics | Values |
---|---|
Tightness | The fuel line connector should be tightened to a specific torque value, typically around 20-25 Nm (Newton meters) or 15-20 lb-ft (pound-feet). This ensures a secure connection without over-tightening, which can damage the fuel line or connector. |
Material Compatibility | Ensure the fuel line connector is made of materials compatible with the fuel type. For gasoline, common materials include steel, brass, or stainless steel. For diesel, materials like aluminum or bronze might be used. |
Flexibility | The connector should allow for some flexibility to accommodate engine movement without excessive stress on the fuel line. |
Vibration Resistance | It should be designed to withstand engine vibrations without loosening or leaking. |
Temperature Resistance | Connectors should be able to operate within the temperature range of the fuel and engine, typically from -40°C to +120°C. |
Pressure Rating | Check the manufacturer's specifications for the pressure rating of the fuel line and connector to ensure it matches the fuel system's requirements. |
Color Coding | Some systems use color-coded connectors for identification, ensuring the correct fuel type is used. |
Length and Routing | The fuel line should be routed away from hot surfaces and sharp edges, and its length should be sufficient to allow for easy access during maintenance. |
What You'll Learn
- Fuel Line Material: Choose fuel line material based on engine requirements
- Connector Compatibility: Ensure fuel line connector matches engine and fuel type
- Tightening Torque: Follow manufacturer's torque specifications for fuel line connectors
- Leak Testing: Test fuel line connections for leaks after tightening
- Vibration Resistance: Fuel line connectors should withstand engine vibrations without loosening
Fuel Line Material: Choose fuel line material based on engine requirements
When it comes to choosing the right fuel line material, it's crucial to consider the specific requirements of your engine. Different engines have unique needs, and selecting the appropriate material ensures optimal performance and longevity. Here's a breakdown of how to make the right choice:
Engine Type and Performance: The first step is to identify the type of engine you have. Modern engines, especially those in high-performance vehicles, often require specialized fuel lines. For instance, high-performance engines might need fuel lines with enhanced flexibility to accommodate rapid acceleration and deceleration. In contrast, older or less powerful engines may have simpler fuel systems. Understanding your engine's performance characteristics will guide you in selecting the right material.
Fuel Line Material Options: There are several materials commonly used for fuel lines, each with its advantages and limitations. Rubber is a traditional choice, known for its flexibility and durability. It is suitable for most engines but may not withstand extreme temperatures or high-pressure environments. Braided stainless steel is another popular option, offering excellent resistance to corrosion and high temperatures, making it ideal for high-performance applications. For engines in marine or off-road environments, flexible fuel lines made from materials like silicone or EPDM rubber are recommended due to their resistance to UV radiation and harsh chemicals.
Engine Operating Conditions: Consider the operating conditions of your engine. If it operates in extreme temperatures or harsh environments, you'll need fuel lines that can withstand these conditions. For example, engines in hot climates might require fuel lines with higher temperature resistance. Similarly, engines in marine environments need lines that are resistant to saltwater corrosion. Always choose materials that match the specific operating conditions to ensure long-term reliability.
Engine Manufacturer's Recommendations: Always refer to the manufacturer's guidelines for your engine. Automotive manufacturers provide specific recommendations for fuel line materials and specifications. These guidelines are designed to ensure compatibility and optimal performance. Using the recommended materials can help avoid potential issues and ensure your engine operates efficiently and safely.
In summary, selecting the right fuel line material is a critical aspect of engine maintenance. By considering the engine type, performance, operating conditions, and manufacturer's recommendations, you can make an informed decision. This ensures that your fuel lines are not only compatible but also contribute to the overall efficiency and longevity of your engine.
The Release of 'Frontline: Fuel of War' in 2008
You may want to see also
Connector Compatibility: Ensure fuel line connector matches engine and fuel type
When it comes to maintaining your vehicle's fuel system, one crucial aspect often overlooked is the compatibility of fuel line connectors. The fuel line connector is a vital component that ensures a secure and leak-free connection between the fuel tank and the engine. Using the wrong connector can lead to a myriad of problems, from reduced engine performance to potential safety hazards. Therefore, understanding the importance of connector compatibility is essential for any vehicle owner.
The first step in ensuring compatibility is to identify the specific fuel type your vehicle uses. Different engines are designed to run on various types of fuel, such as gasoline, diesel, or alternative fuels like ethanol or CNG. Each fuel type has unique properties and requires specific connectors to handle its characteristics. For instance, ethanol-blended fuels demand connectors that can withstand the higher ethanol content without compromising performance.
Once you've determined your fuel type, the next critical factor is the engine's make and model. Different engines have distinct mounting points and connector sizes. It's essential to refer to your vehicle's manual or consult a reputable automotive resource to find the correct connector specifications. Using a connector that doesn't match your engine's requirements can result in an improper fit, leading to fuel leaks, reduced power, or even engine damage.
To ensure a proper fit, look for connectors that have the appropriate thread size and sealing mechanism. The thread size should match the fuel line's internal diameter to create a tight seal. Common thread sizes include 1/4-inch, 3/8-inch, and 1/2-inch, each designed for specific fuel line diameters. Additionally, check for the presence of an O-ring or gasket that provides a secure seal between the connector and the fuel line.
In summary, when dealing with fuel line connectors, compatibility is key. Always verify the fuel type and engine specifications to select the right connector. This attention to detail will help prevent potential issues and ensure your vehicle's fuel system operates efficiently and safely. Remember, a small investment in the right connector can save you from costly repairs and potential hazards associated with fuel system malfunctions.
Unkinking Fuel Lines: A Step-by-Step Guide to Smooth Operation
You may want to see also
Tightening Torque: Follow manufacturer's torque specifications for fuel line connectors
When it comes to tightening fuel line connectors, it's crucial to adhere to the manufacturer's torque specifications. These specifications are carefully determined to ensure the proper installation and functionality of the fuel system. By following these guidelines, you can guarantee a secure and reliable connection, minimizing the risk of fuel leaks and potential engine damage.
The torque requirements for fuel line connectors are typically provided in pound-force per square inch (psi) or Newton-meters (Nm). These values are specific to the particular connector design and application. It is essential to use a torque wrench to achieve the exact amount of force needed. Over-tightening can lead to damage to the connector or the fuel line itself, while under-tightening may result in an insecure connection, potentially causing fuel leaks.
To ensure accuracy, it's recommended to consult the vehicle's service manual or the manufacturer's guidelines for the specific torque value required for your fuel line connectors. These sources will provide the correct specifications for your particular make and model. Using the right torque value ensures that the connector is tightened to the appropriate level, providing a secure seal and preventing any potential issues.
In practice, you should apply the specified torque value in a controlled manner. Start by positioning the connector in the correct location and ensuring it is aligned properly. Then, using the torque wrench, apply the required force in a steady and consistent motion. Avoid any sudden movements or excessive force, as this can compromise the connector's integrity.
Remember, proper tightening of fuel line connectors is a critical aspect of vehicle maintenance. It ensures the safety and performance of your engine. By following the manufacturer's torque specifications, you can maintain a reliable fuel system and avoid potential problems associated with improper installation. Always refer to the vehicle's documentation for the correct torque values to ensure a professional and secure finish.
Polaris Sportsman Fuel Line Sizes: A Comprehensive Guide
You may want to see also
Leak Testing: Test fuel line connections for leaks after tightening
After ensuring that the fuel line connectors are tightened according to the manufacturer's specifications, the next crucial step is leak testing. This process is essential to identify any potential issues that might have been overlooked during the tightening process. Here's a detailed guide on how to perform this test effectively:
Preparation: Before beginning the leak test, ensure you have the necessary tools and materials. You'll need a fuel line connector leak detection kit, which typically includes a specialized dye or a leak detection solution. These kits are designed to reveal even the smallest leaks. Additionally, have a clean rag or cloth ready to wipe down the connectors and the surrounding area.
Procedure: Start by disconnecting the fuel line from the engine and the fuel tank. This step is crucial for creating a controlled environment during the test. Then, apply a small amount of the leak detection solution or dye to the fuel line connector. Ensure that the entire connector, including the threads and the O-ring or gasket, is coated. Reattach the fuel line to the connector, ensuring a secure and tight connection.
Now, the critical part: observe the fuel line for any signs of leakage. This test should be conducted in a well-lit area to make it easier to spot any potential leaks. Check for any drips or traces of the dye/solution around the connector, especially at the point where the fuel line connects to the engine and the tank. Even a small amount of leakage can indicate a potential issue.
Interpretation: If you notice any leaks, it's essential to address them immediately. Leaks can lead to fuel loss, engine performance issues, and potential safety hazards. Tighten the connector further if necessary, but be cautious not to overtighten, as this can damage the fuel line or connector. If the leak persists, consider replacing the connector or seeking professional assistance.
Outboard Fuel Line Slack: The Ultimate Guide to Finding the Right Amount
You may want to see also
Vibration Resistance: Fuel line connectors should withstand engine vibrations without loosening
Vibration resistance is a critical aspect of fuel line connector design, ensuring that the fuel system remains secure and reliable even under the intense conditions of an engine's operation. The primary goal is to prevent fuel line connectors from loosening or detaching during engine vibrations, which could lead to fuel leaks, reduced engine performance, and potential safety hazards.
Engine vibrations can be substantial, especially in high-performance or heavy-duty applications. These vibrations can cause the fuel line connectors to loosen over time, particularly if the initial installation was not secure enough. The connectors typically consist of a nut or clamp that secures the fuel line to the engine's fuel rail or injection system. To ensure vibration resistance, these connectors must be tightened to a specific torque value, which is often provided by the manufacturer. This torque value is carefully calculated to provide the necessary clamping force while also allowing for some flexibility to accommodate minor vibrations without causing damage.
The process of tightening fuel line connectors requires precision and attention to detail. It is essential to use the correct torque wrench to achieve the manufacturer's recommended torque. Over-tightening can damage the fuel line or the connector, while under-tightening may not provide adequate vibration resistance. A common practice is to tighten the connectors in multiple stages, starting with a low torque to position the components correctly, and then applying the final torque value. This method ensures a secure connection without excessive force.
In addition to the torque specifications, the quality of the fuel line connectors themselves is vital. High-quality connectors are designed to maintain their integrity under extreme conditions, including vibrations. They often feature robust materials and precise manufacturing processes to ensure a tight seal and secure attachment. Some connectors may also incorporate vibration-damping materials or designs that absorb and reduce the impact of vibrations, further enhancing their resistance to loosening.
Regular maintenance and inspections can also contribute to vibration resistance. Over time, fuel lines and connectors may experience wear and degradation, affecting their ability to withstand vibrations. Inspecting the fuel system during routine maintenance checks can help identify any loose connections or signs of damage, allowing for prompt repairs or replacements. By addressing these issues, vehicle owners can ensure that their engines continue to operate efficiently and safely, even in demanding environments.
Thawing Frozen Fuel Lines: A Step-by-Step Guide to Unfreezing
You may want to see also
Frequently asked questions
The fuel line connector should be tightened to a specific torque value, typically around 20-25 foot-pounds. This ensures a secure and leak-free connection without causing damage to the fuel lines or the vehicle's engine.
It is not recommended to use a regular hose clamp for fuel lines. Fuel line connectors are designed specifically for the high-pressure and temperature requirements of fuel systems. Hose clamps may not provide the necessary sealing and could lead to fuel leaks or system malfunctions.
If the fuel line connector is tightened beyond the recommended torque, it can cause damage to the fuel lines, fittings, or even the engine. Over-tightening may result in stripped threads, cracked lines, or fuel leaks, which can be costly to repair.
Yes, it is essential to use a torque wrench to ensure the correct tightening. A standard socket wrench or a fuel line connector wrench can be used to tighten the connector, but always refer to the vehicle's service manual for the recommended torque specifications.