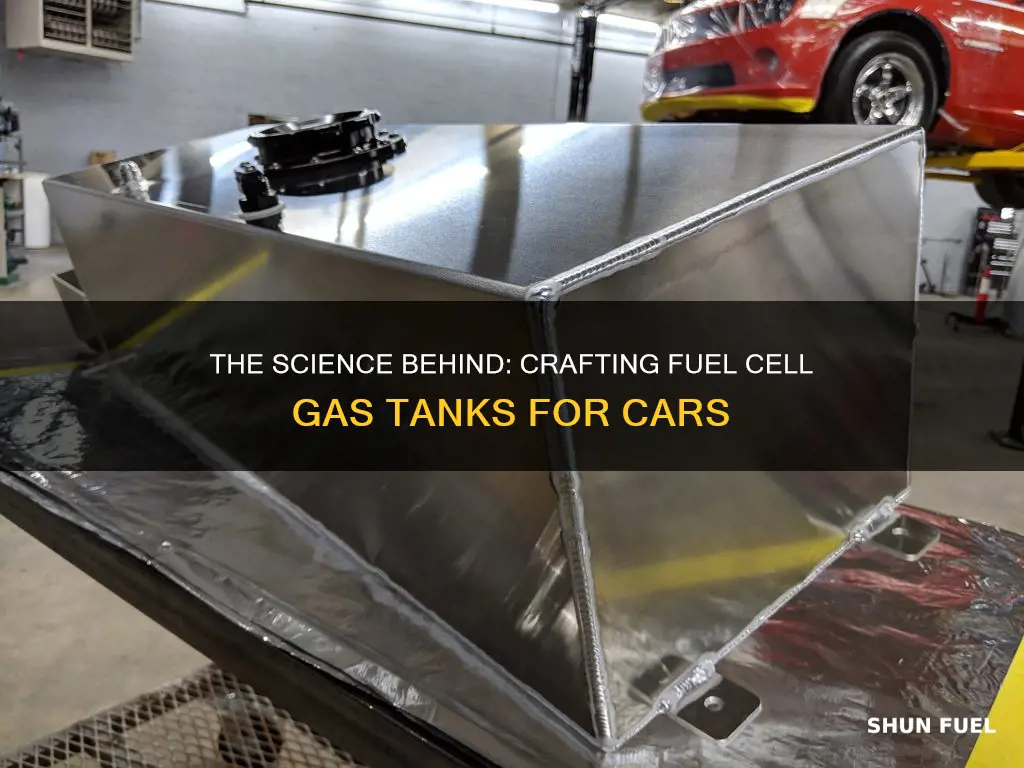
Fuel cell gas tanks in cars are a crucial component of the vehicle's energy system, and their manufacturing process is intricate and precise. These tanks are designed to store hydrogen gas, a clean and efficient energy source, in a safe and compact manner. The production involves several steps, starting with the selection of high-quality materials such as carbon fiber composites or aluminum alloys, which offer the necessary strength and corrosion resistance. The manufacturing process includes intricate molding, welding, and sealing techniques to ensure the tank's structural integrity and prevent any leaks. This introduction sets the stage for a detailed exploration of the manufacturing process and the challenges involved in creating these specialized fuel storage systems.
What You'll Learn
- Material Selection: Choosing lightweight, durable materials like carbon fiber or advanced composites for fuel cell gas tanks
- Design and Engineering: Engineers optimize tank shape and size for efficient fuel storage and vehicle integration
- Manufacturing Process: Involves molding, welding, and assembly techniques to create high-pressure-resistant fuel tanks
- Safety Standards: Adhering to strict safety regulations for materials, design, and testing to ensure vehicle and passenger safety
- Environmental Impact: Sustainable production methods and materials to minimize environmental impact of fuel cell gas tank manufacturing
Material Selection: Choosing lightweight, durable materials like carbon fiber or advanced composites for fuel cell gas tanks
The development of fuel cell gas tanks for vehicles is a critical aspect of the automotive industry, especially with the growing focus on sustainable and efficient transportation. When it comes to material selection for these tanks, engineers and designers prioritize lightweight, durable materials to ensure optimal performance and safety. One of the primary choices for fuel cell gas tanks is carbon fiber, a material renowned for its exceptional strength-to-weight ratio. Carbon fiber composites offer a unique combination of high strength and low density, making them ideal for applications where structural integrity and weight reduction are essential. By utilizing carbon fiber, manufacturers can significantly reduce the overall weight of the vehicle while maintaining the necessary structural integrity to withstand the pressures and conditions associated with fuel storage.
Advanced composites, another innovative material, are also considered for fuel cell gas tank construction. These composites are engineered to provide superior mechanical properties, including excellent impact resistance and fatigue strength. The use of advanced composites allows for the creation of lightweight tanks that can withstand the demanding environments of fuel cell vehicles. This material choice is particularly advantageous as it enables designers to optimize the tank's shape and size, potentially increasing the overall fuel capacity while maintaining a compact form factor.
The selection of lightweight materials is crucial for fuel cell gas tanks as it directly impacts the vehicle's overall efficiency and performance. Lighter tanks contribute to improved acceleration, better handling, and increased range, all of which are essential for electric vehicles powered by fuel cells. Moreover, the use of advanced materials helps in reducing the overall weight of the vehicle, which is a significant factor in achieving better fuel efficiency and reducing the environmental impact of transportation.
In the manufacturing process, the chosen materials undergo precise engineering and fabrication techniques. Carbon fiber composites, for instance, are often formed using processes like resin transfer molding (RTM) or vacuum bag molding, ensuring uniform distribution of the material and achieving the desired structural integrity. Advanced composites may utilize processes such as pultrusion or compression molding to create tanks with complex shapes and optimized mechanical properties.
Additionally, the manufacturing process should consider the integration of sensors and monitoring systems within the fuel cell gas tank. These sensors can provide real-time data on fuel levels, pressure, and temperature, ensuring safe and efficient operation. The materials used should be compatible with these electronic components and capable of withstanding the harsh environmental conditions inside the vehicle. By combining lightweight, durable materials with advanced sensor technology, fuel cell gas tanks can be designed to meet the stringent requirements of modern automotive engineering.
Powerful Top Fuel Funny Car Price: A Wild Ride's Cost
You may want to see also
Design and Engineering: Engineers optimize tank shape and size for efficient fuel storage and vehicle integration
The design and engineering of fuel cell gas tanks in automobiles is a critical aspect of the vehicle's overall performance and efficiency. Engineers play a pivotal role in optimizing the tank's shape and size to ensure efficient fuel storage while seamlessly integrating it into the vehicle's structure. This process involves a meticulous understanding of the vehicle's architecture and the specific requirements of the fuel cell system.
One key consideration is the available space within the vehicle's body. Engineers must carefully analyze the dimensions and layout of the car to determine the most suitable location for the fuel tank. This involves a trade-off between maximizing storage capacity and ensuring the tank's accessibility for maintenance and refuelling. The tank's shape is often designed to fit the available space optimally, considering factors such as the vehicle's center of gravity and overall aesthetics.
Size optimization is another critical aspect. Engineers aim to strike a balance between storing enough fuel to meet the vehicle's range requirements and minimizing the tank's overall volume. This involves precise calculations and simulations to determine the ideal tank capacity. The goal is to provide sufficient fuel for the fuel cell while keeping the tank's weight and size manageable, ensuring the vehicle's overall efficiency and performance.
Shape optimization is where engineers truly showcase their creativity and technical prowess. The tank's shape is designed to minimize fuel loss and ensure efficient distribution. This includes considerations for fuel flow, pressure distribution, and the prevention of dead zones that could lead to fuel starvation during operation. Engineers might employ complex geometric designs, such as elliptical or cylindrical shapes, to optimize fuel storage while maintaining structural integrity.
Additionally, engineers focus on the integration of the fuel tank with the vehicle's systems. This involves ensuring proper communication and control between the tank, fuel cell, and other components. The tank's design must accommodate the necessary plumbing, sensors, and control mechanisms, all while maintaining a streamlined and compact overall structure. This level of integration is crucial for the efficient operation of the fuel cell vehicle.
Unveiling the Power: How Oil Fuels Your Car's Engine
You may want to see also
Manufacturing Process: Involves molding, welding, and assembly techniques to create high-pressure-resistant fuel tanks
The manufacturing process of fuel cell gas tanks in cars is a complex and precise procedure, ensuring the structural integrity and safety of these critical components. The primary goal is to create a high-pressure-resistant tank that can store hydrogen or other fuels efficiently while adhering to strict automotive standards.
Molding: The process begins with the selection of appropriate materials, typically a composite of carbon fiber and plastic or a specialized metal alloy. The chosen material is then heated and shaped using advanced molding techniques. This step involves injecting the material into a custom-designed mold, which is carefully crafted to match the exact dimensions and contours of the fuel tank. The mold is heated to ensure the material flows evenly and fills all the required spaces. This molding process creates a strong, lightweight structure with a precise shape, setting the foundation for the tank's durability and performance.
Welding: Once the molded components are prepared, welding comes into play. High-pressure fuel tanks require seamless construction to prevent any potential leaks. Welding techniques such as gas tungsten arc welding (GTAW) or gas metal arc welding (GMAW) are employed to join the various parts together. Skilled technicians carefully align and join the tank's walls, base, and top, ensuring a strong and leak-proof connection. The welding process demands precision and adherence to specific standards to guarantee the tank's structural integrity.
Assembly: After the individual components are molded and welded, the assembly phase begins. This stage involves carefully integrating the fuel tank into the vehicle's fuel system. The tank is positioned and secured in the designated space, often requiring custom-made brackets and fasteners. All connections and interfaces must be meticulously fitted to ensure a secure and reliable assembly. This process includes testing the tank's pressure containment and sealing to identify and rectify any potential issues.
The manufacturing process also includes rigorous quality control checks at each stage. Non-destructive testing methods, such as ultrasonic and radiographic inspections, are employed to identify any defects or imperfections in the molded parts, welded joints, and overall assembly. This meticulous approach ensures that the fuel cell gas tanks meet the highest safety and performance standards, providing a reliable energy storage solution for vehicles.
Electric Revolution: Unveiling the Green vs. Fuel Debate
You may want to see also
Safety Standards: Adhering to strict safety regulations for materials, design, and testing to ensure vehicle and passenger safety
The development of fuel cell gas tanks in vehicles is a complex process that demands adherence to stringent safety standards. These tanks are designed to store hydrogen gas, a highly flammable and explosive substance, hence the critical importance of ensuring their safety. The primary goal is to prevent any potential hazards that could arise from the storage and transportation of this volatile fuel.
Safety regulations for these tanks are set by various governing bodies, such as the National Highway Traffic Safety Administration (NHTSA) and the International Organization for Standardization (ISO). These standards dictate the materials, design, and manufacturing processes that must be followed to ensure the tanks' integrity and performance. For instance, the materials used must be able to withstand extreme conditions, including high pressure and temperature, without compromising their structural integrity. Common materials include advanced composites and alloys, specifically engineered to meet these demanding requirements.
Design considerations are equally vital. The tank's shape and size must be optimized to provide maximum storage capacity while minimizing the risk of damage during vehicle collisions or other accidents. This often involves intricate engineering to ensure the tank's structural stability and to prevent any potential hazards, such as the risk of hydrogen gas leakage. The design must also account for the tank's integration into the vehicle's overall structure, ensuring it does not interfere with the vehicle's performance or safety features.
Testing is a critical phase in the development process. Tanks undergo rigorous testing to validate their performance and safety. This includes pressure tests to ensure the tank can withstand the required operating pressures, as well as flame and explosion tests to assess the tank's resistance to potential hazards. Additionally, thermal cycling tests are conducted to evaluate the tank's performance under varying temperature conditions, ensuring it can maintain its structural integrity and safety features across a wide range of environmental conditions.
In summary, the creation of fuel cell gas tanks in cars involves a meticulous process that adheres to strict safety regulations. This includes the selection of appropriate materials, the implementation of careful design principles, and the conduct of comprehensive testing. By following these standards, manufacturers can ensure that the gas tanks are not only functional but also safe, contributing to the overall safety of the vehicle and its occupants.
Revive Your Ride: Can You Reuse a Fuel Pump?
You may want to see also
Environmental Impact: Sustainable production methods and materials to minimize environmental impact of fuel cell gas tank manufacturing
The manufacturing of fuel cell gas tanks for vehicles is an area where environmental considerations are crucial, especially as the automotive industry aims to reduce its carbon footprint. Sustainable production methods and the choice of materials play a pivotal role in minimizing the ecological impact of these components. One key aspect is the adoption of lightweight materials that offer equivalent or superior performance to traditional heavy metals while reducing the overall weight of the vehicle. This approach not only enhances fuel efficiency but also contributes to a more sustainable manufacturing process.
Advanced composites, such as carbon fiber-reinforced polymers (CFRP), are emerging as viable alternatives for fuel cell gas tanks. These materials provide excellent strength-to-weight ratios, making them ideal for structural components that require high integrity. The production of CFRP can be optimized to reduce the use of non-renewable resources and minimize waste generation. For instance, utilizing recycled carbon fiber or bio-based resins can significantly lower the environmental impact of the manufacturing process.
In addition to material selection, the implementation of energy-efficient production techniques is essential. Manufacturing processes should aim to reduce energy consumption and minimize waste generation. This can be achieved through the adoption of lean manufacturing principles, which focus on optimizing production flow and reducing waste. For example, implementing just-in-time inventory management can minimize storage and reduce the need for excessive packaging, thereby lowering the environmental impact.
Furthermore, the recycling and end-of-life management of fuel cell gas tanks are critical aspects of sustainability. Developing efficient recycling processes for composite materials ensures that valuable resources are recovered and reused, reducing the demand for new raw materials. This not only conserves natural resources but also decreases the carbon emissions associated with mining and processing.
In summary, the environmental impact of fuel cell gas tank manufacturing can be significantly reduced by adopting sustainable production methods and materials. Utilizing lightweight composites, optimizing manufacturing processes, and implementing efficient recycling strategies are all essential steps towards a more eco-friendly approach to fuel cell technology. As the automotive industry continues to evolve, these considerations will play a vital role in shaping a greener future for transportation.
Exploring the Three Main Types of Car Fuel: Gasoline, Diesel, and Alternative Fuels
You may want to see also
Frequently asked questions
Fuel cell gas tanks are primarily made from composite materials, often a blend of carbon fiber and epoxy resins. These materials offer excellent strength-to-weight ratios, corrosion resistance, and the ability to withstand high-pressure environments, making them ideal for storing hydrogen gas in vehicles.
The process involves advanced composite manufacturing techniques. It starts with the design and engineering of the tank's shape and structure. Then, layers of carbon fiber fabric are carefully laid and bonded together using epoxy resins, creating a strong and lightweight structure. This composite material is then cured and formed into the desired tank shape.
Yes, a common method is the use of a vacuum bag molding process. This process involves placing the carbon fiber layers into a mold and then applying a vacuum to draw the material into the desired shape. The vacuum ensures proper fiber alignment and resin distribution, resulting in a strong and consistent tank.
Safety is a critical aspect of fuel cell tank manufacturing. Manufacturers employ various testing and inspection methods. These include pressure testing to ensure the tank can withstand hydrogen gas pressures, leak testing to identify any potential defects, and rigorous quality control checks at each production stage.
Coatings play a vital role in protecting the tank's interior surface. A specialized coating, often a thin layer of metal or ceramic, is applied to the inner surface of the tank. This coating prevents hydrogen permeation, corrosion, and ensures the tank's longevity. The coating process is carefully controlled to maintain the structural integrity of the composite material.