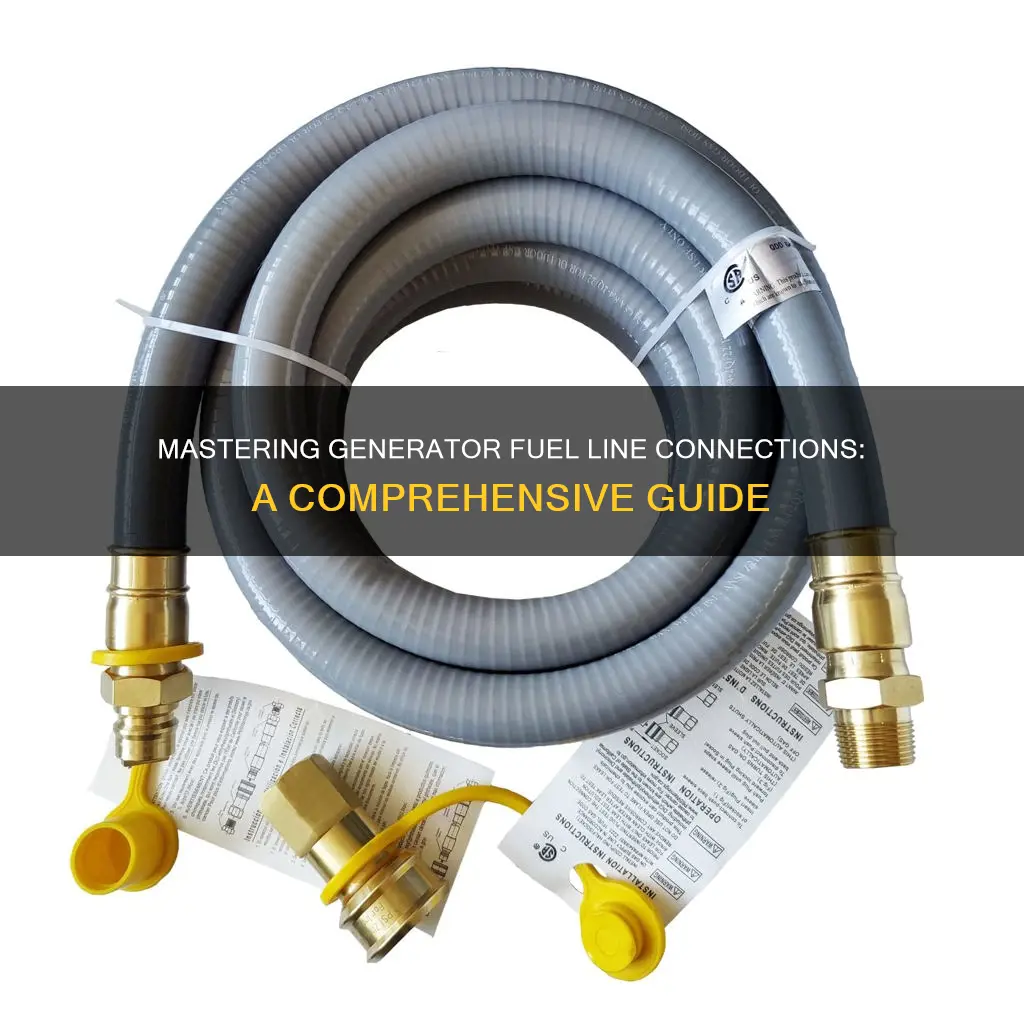
Understanding how to properly connect a generator fuel line is essential for ensuring the safe and efficient operation of your generator. This process involves several key steps, including selecting the appropriate fuel line material, ensuring a secure connection to the fuel source, and properly grounding the system to prevent electrical hazards. By following these guidelines, you can ensure that your generator runs smoothly and reliably, providing power when you need it most.
What You'll Learn
- Fuel Pump: The generator's fuel pump ensures a steady flow of fuel to the engine
- Fuel Filter: Filters impurities, preventing blockages and ensuring clean fuel
- Fuel Injectors: These inject fuel into the engine's cylinders for combustion
- Fuel Lines Material: Choose appropriate materials like steel or rubber for durability
- Fuel Tank: The tank stores fuel and connects to the generator via lines
Fuel Pump: The generator's fuel pump ensures a steady flow of fuel to the engine
The fuel pump is a critical component in any generator setup, as it plays a vital role in delivering a consistent and controlled supply of fuel to the engine. This pump is designed to maintain a steady flow of fuel, ensuring optimal performance and longevity of the generator. Here's an overview of its function and importance:
In the context of generators, the fuel pump's primary task is to regulate and deliver fuel from the tank to the engine. It operates by creating a vacuum or pressure, which draws fuel from the reservoir and pushes it through the fuel lines to the engine's carburetor or injection system. This process is essential because it ensures that the engine receives the required amount of fuel at the right pressure, allowing for efficient combustion and power generation.
The pump's design and functionality are key to its effectiveness. It is typically located near the fuel tank and is powered by the generator's electrical system. When the generator is started, the pump activates, creating a continuous flow of fuel. This flow rate is carefully calibrated to match the engine's requirements, ensuring it runs smoothly and efficiently. The pump's ability to maintain a steady pressure is crucial, as it prevents fuel starvation and ensures the engine operates within the optimal fuel-air mixture range.
One of the critical aspects of the fuel pump is its ability to handle varying fuel loads. As the generator operates, the fuel level in the tank decreases, and the pump must adjust its performance accordingly. It must continue to deliver the required fuel volume and pressure, even when the tank is nearly empty. This adaptability ensures that the generator can run for extended periods without the risk of fuel depletion or engine misfires.
Furthermore, the fuel pump's design often includes safety features. These mechanisms prevent fuel from overheating or being exposed to excessive pressure, which could lead to engine damage. For instance, some pumps have built-in pressure relief valves that open if the pressure exceeds a safe limit, protecting the engine and the pump itself. Such safety measures are essential to guarantee the reliable operation of the generator over time.
In summary, the fuel pump is a critical component that ensures the generator's engine receives a consistent and controlled supply of fuel. Its role in maintaining a steady flow and pressure is vital for optimal performance and longevity. Understanding the pump's function and its impact on the generator's operation highlights the importance of regular maintenance and care to ensure reliable power generation.
Reusing Fuel Line Clips: A Practical Guide to Extending Life
You may want to see also
Fuel Filter: Filters impurities, preventing blockages and ensuring clean fuel
The fuel filter is a critical component in any generator system, as it plays a vital role in maintaining the health and longevity of the engine. Its primary function is to filter out impurities and contaminants from the fuel, ensuring that only clean and pure fuel reaches the engine's combustion chamber. This process is essential to prevent blockages and maintain optimal performance.
When fuel is supplied to a generator, it often contains various impurities such as water, dirt, rust, and other contaminants that can accumulate over time. These impurities can lead to several issues, including engine misfires, reduced power output, and even complete engine failure. The fuel filter acts as a barrier, trapping these unwanted particles and ensuring that only the cleanest fuel passes through.
A typical fuel filter consists of a cylindrical housing with a filter element inside. The fuel line from the fuel tank connects to the filter, and the filtered fuel then continues its journey to the engine. As fuel flows through the filter, the filter element captures and holds the impurities, keeping them separate from the main fuel stream. This process is often referred to as 'fuel purification'.
Regular maintenance and replacement of the fuel filter are crucial to its effectiveness. Over time, the filter can become clogged with trapped contaminants, reducing its ability to filter effectively. It is recommended to check and replace the fuel filter at regular intervals or when the generator is serviced. This ensures that the fuel system remains clean and efficient, contributing to the overall reliability of the generator.
In summary, the fuel filter is a generator's guardian, ensuring that the fuel supplied to the engine is free from impurities. By preventing blockages and maintaining clean fuel, it plays a vital role in keeping the generator running smoothly and reliably. Proper maintenance and attention to the fuel filter are essential to avoid potential issues and ensure the generator's long-term performance.
Unveiling the Milwaukee Fuel Line: Powering Your Projects
You may want to see also
Fuel Injectors: These inject fuel into the engine's cylinders for combustion
Fuel injectors are an essential component of modern engines, playing a crucial role in the combustion process. These devices are responsible for precisely injecting fuel into the engine's cylinders, ensuring efficient and controlled burning of the fuel-air mixture. The primary function of fuel injectors is to optimize engine performance, improve fuel efficiency, and reduce emissions.
In an internal combustion engine, the fuel-air mixture is created by mixing gasoline (or diesel) with air. This mixture is then ignited in the engine's cylinders, causing the piston to move and generate power. Fuel injectors are designed to deliver this fuel in a highly controlled manner, ensuring that the right amount of fuel is injected at the right time. This precision is vital for maintaining optimal engine operation and preventing issues like engine knocking or misfires.
The process begins when the engine's computer sends a signal to the fuel injectors, instructing them to release fuel at a specific rate and timing. This signal is based on various engine parameters, such as speed, load, and temperature, to ensure the engine operates efficiently under different conditions. When the signal is received, the fuel injectors open, allowing high-pressure fuel to be injected into the engine's intake manifold or directly into the cylinders.
Modern fuel injectors use a solenoid-operated valve to control the fuel flow. When the engine's computer activates the solenoid, it opens the valve, allowing fuel to pass through and be injected. This process is highly efficient and ensures that the fuel is atomized to the correct size, allowing for proper combustion. The fuel injectors are strategically positioned to deliver fuel to the engine's cylinders, where it mixes with air and is ignited by the spark plugs.
The design and placement of fuel injectors vary depending on the engine type and manufacturer. Some engines use a single fuel injector per cylinder, while others may have multiple injectors per cylinder to ensure optimal fuel distribution. The fuel injectors are typically located close to the intake valves, allowing for efficient mixing of fuel and air in the combustion chamber. This design ensures that the fuel is injected at the optimal point in the engine's cycle, maximizing power output and fuel efficiency.
Optimizing Fuel Flow: Choosing the Right Selector Valve for 3/8" Lines
You may want to see also
Fuel Lines Material: Choose appropriate materials like steel or rubber for durability
When it comes to generator fuel lines, choosing the right material is crucial for ensuring durability and reliable performance. The fuel lines are responsible for transporting fuel from the tank to the engine, and they must withstand various environmental factors and mechanical stresses. Here's a detailed look at the two primary materials used for fuel lines: steel and rubber.
Steel Fuel Lines:
Steel is renowned for its exceptional strength and durability. It is an excellent choice for fuel lines, especially in heavy-duty applications or where the generator is exposed to harsh conditions. Steel fuel lines are known for their ability to withstand high pressure and temperature fluctuations. They are less susceptible to corrosion and can handle the rigors of long-term use without degradation. The rigidity of steel ensures that the fuel lines maintain their shape and do not collapse under pressure, which is essential for proper fuel flow. Additionally, steel fuel lines are often preferred for their longevity, as they can last for many years without showing signs of wear and tear.
Rubber Fuel Lines:
Rubber is a more flexible and lightweight material compared to steel, making it a popular choice for fuel lines in many applications. Rubber fuel lines are highly resistant to abrasion and can flex and bend without permanent deformation. This flexibility is advantageous in situations where the generator's fuel lines need to navigate around obstacles or experience movement during operation. Rubber is also naturally resistant to many chemicals, including those found in fuel, which helps prevent leaks and corrosion. However, it's important to note that rubber fuel lines may not be as pressure-resistant as steel and can be more susceptible to cracking over time, especially in low-temperature environments.
Choosing the Right Material:
The decision between steel and rubber fuel lines depends on the specific requirements of your generator setup. For high-performance, heavy-duty generators or those operating in extreme conditions, steel fuel lines are often the preferred choice due to their superior strength and durability. On the other hand, rubber fuel lines are ideal for general-purpose applications, portable generators, or situations where flexibility and resistance to abrasion are more critical. It's essential to consider the operating environment, temperature ranges, and the specific demands of your generator to make an informed decision.
In summary, the material of the fuel lines is a critical aspect of generator maintenance, as it directly impacts the system's reliability and longevity. Both steel and rubber have their advantages, and selecting the appropriate material will ensure that your generator's fuel lines function efficiently and withstand the test of time.
Mastering Fuel Line Removal: A Guide for BMW 528 Owners
You may want to see also
Fuel Tank: The tank stores fuel and connects to the generator via lines
The fuel tank is a critical component of any generator system, serving as the primary storage unit for the fuel that powers the generator. It is designed to hold the necessary amount of fuel to ensure the generator can operate for an extended period without needing to be refueled. The tank is typically made of durable materials such as steel or aluminum to withstand the pressures and temperatures associated with fuel storage.
The fuel tank is connected to the generator through a series of carefully designed lines and connections. These lines are crucial for delivering fuel from the tank to the generator's engine, ensuring a continuous supply of power. The fuel lines are usually made of high-quality materials like rubber or plastic, which can withstand the corrosive effects of fuel and the internal pressures within the tank.
One end of the fuel line is connected to the fuel tank, often using a quick-release coupling or a threaded fitting. This connection allows for easy refilling of the tank and facilitates the transfer of fuel when needed. The other end of the line is then connected to the generator's fuel inlet, which is typically located near the engine. This inlet is designed to accept the fuel line and ensure a secure and airtight connection.
When connecting the fuel tank to the generator, it is essential to consider the orientation and positioning of the lines. The lines should be routed in a way that minimizes the risk of damage and ensures easy access for maintenance. Proper routing also helps to prevent fuel leaks and ensures that the generator receives a steady supply of fuel. In some cases, fuel filters and pumps may be installed along the line to further ensure the quality and flow of the fuel.
Additionally, the fuel tank may have a built-in gauge or indicator to monitor the fuel level. This feature allows users to keep track of the remaining fuel and plan refills accordingly. The connection between the fuel tank and the generator is a critical aspect of the overall system, and proper installation and maintenance of these lines are essential for the efficient and safe operation of the generator.
VW Fuel Line Sizes: A Comprehensive Guide
You may want to see also
Frequently asked questions
To establish a reliable connection, it's crucial to use the appropriate fittings and hoses designed for fuel lines. Start by cleaning the fuel tank's inlet port and the fuel line's outlet. Then, insert the fuel line into the port, ensuring a snug fit. Secure the connection with a fuel line clamp or a fuel tank fitting, following the manufacturer's instructions. Regularly inspect the connection for any signs of leaks or damage.
When routing the fuel line, it's essential to keep it away from heat sources, sharp edges, and potential impact areas. Route the line in a straight line from the fuel tank to the generator, avoiding sharp bends that could restrict fuel flow. Use fuel line supports or brackets to secure the line at regular intervals, ensuring it remains flexible and doesn't kink. Proper routing minimizes the risk of damage and ensures efficient fuel delivery.
No, it's not advisable to use just any fuel line for your generator. Generators require specific fuel lines designed to handle the fuel type and pressure they operate with. Different fuels, such as gasoline or diesel, have varying properties that affect the choice of fuel line material. Always refer to the generator's manual or consult the manufacturer to determine the recommended fuel line specifications. Using the correct fuel line ensures optimal performance and safety.