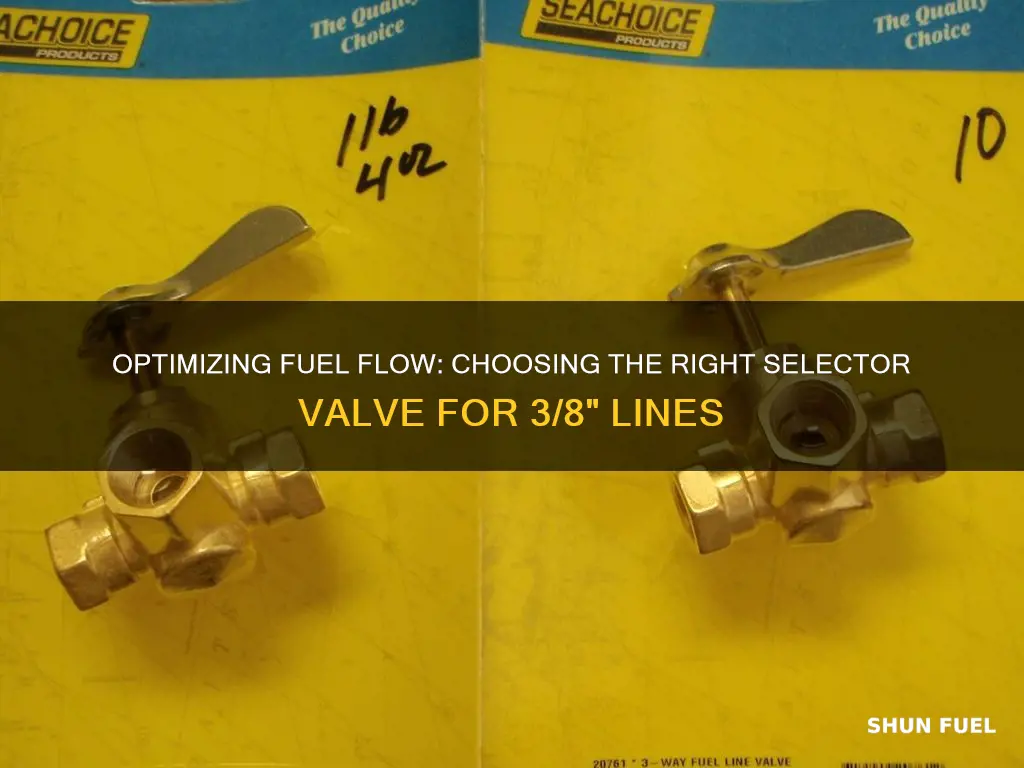
When it comes to choosing the right fuel selector valve for a 3/8 fuel line, it's important to consider several factors. The size of the valve is crucial, as it needs to match the diameter of the fuel line to ensure efficient and safe operation. A 3/8 fuel line requires a specific size of fuel selector valve that can handle the flow rate and pressure of the fuel. This introduction aims to explore the various options available and provide guidance on selecting the appropriate valve size to ensure optimal performance and compatibility with the fuel line.
Characteristics | Values |
---|---|
Fuel Line Diameter | 3/8" |
Flow Rate | 1.5-2 gallons per minute (GPM) |
Pressure Rating | 100-150 psi |
Material | Brass, Stainless Steel |
Connection Type | G1/4" threads, Flanged |
Temperature Range | -40°F to 400°F |
Color | Natural Brass, Chrome Plated |
Brand | Various (e.g., Walbro, Stihl, Kohler) |
Compatibility | Small engines, lawn mowers, generators |
Weight | 0.5-1.5 lbs |
What You'll Learn
- Fuel Line Diameter: Determine the correct diameter of the fuel line for your engine
- Flow Rate: Calculate the required flow rate to match your engine's fuel consumption
- Pressure Considerations: Account for pressure drops and engine requirements
- Material Compatibility: Choose a valve material compatible with your fuel type
- Mounting Options: Consider the available mounting positions on your fuel tank
Fuel Line Diameter: Determine the correct diameter of the fuel line for your engine
When it comes to selecting the appropriate fuel line diameter for your engine, it's crucial to consider the specific requirements of your vehicle and the engine's fuel system. The fuel line diameter is a critical factor in ensuring efficient and reliable fuel delivery, as it directly impacts the flow rate and pressure of the fuel. Here's a comprehensive guide to help you determine the correct diameter:
Understanding Fuel Line Sizes: Fuel lines are typically measured in inches, with the most common sizes ranging from 3/8" to 1/2" in diameter. The 3/8" size is often used for smaller engines or applications where space is limited, while larger engines may require a 1/2" or even 3/4" diameter fuel line. It's essential to match the fuel line size to the engine's fuel requirements to optimize performance.
Engine Specifications: Start by consulting your engine's manual or specifications. Manufacturers provide detailed information about the recommended fuel line sizes for their engines. Look for technical data or diagrams that illustrate the fuel system, including the fuel lines and their respective diameters. This information is crucial as it ensures compatibility and optimal performance. For example, a 3/8" fuel line might be suitable for a smaller, less powerful engine, while a 1/2" line could be necessary for high-performance applications.
Flow Rate and Pressure: The fuel line diameter directly influences the flow rate and pressure of the fuel. A larger diameter allows for higher flow rates, which can be beneficial for engines that require a steady and robust fuel supply. However, it's important to balance this with the engine's capabilities and the overall fuel system design. Insufficient pressure or flow rate can lead to poor engine performance, while excessive pressure may cause fuel leaks or damage to the fuel system.
Consideration of Length: The length of the fuel line is another critical factor. Longer fuel lines may require a larger diameter to maintain the desired flow rate and pressure. If the fuel line is extended, you might need to upgrade to a larger diameter to compensate for the increased distance and potential restrictions. Always consider the overall fuel system layout and ensure that the fuel lines are routed efficiently to minimize pressure drops.
Testing and Verification: Once you've determined the recommended fuel line diameter, it's essential to verify the installation. Test the fuel system under various conditions to ensure that the chosen diameter provides the required flow rate and pressure. This step is crucial, especially when modifying or upgrading an existing fuel system. Proper testing will ensure that your engine receives the optimal fuel supply, resulting in improved performance and reliability.
Jeep Grand Cherokee Fuel Line Sizes: A Comprehensive Guide
You may want to see also
Flow Rate: Calculate the required flow rate to match your engine's fuel consumption
When determining the appropriate size of a fuel selector valve for a 3/8" fuel line, it's crucial to consider the flow rate required to match your engine's fuel consumption. This calculation ensures that the valve can handle the necessary volume of fuel efficiently and without any performance issues. Here's a step-by-step guide to help you calculate the required flow rate:
Step 1: Understand Engine Requirements: Begin by consulting your engine's manual or specifications. Identify the maximum fuel flow rate your engine can handle. This information is typically provided in liters per minute (LPM) or gallons per minute (GPM). For instance, if your engine requires a maximum of 15 LPM of fuel, you need to ensure that your fuel system, including the selector valve, can deliver this amount.
Step 2: Measure Fuel Line Diameter: The next step is to measure the diameter of your 3/8" fuel line. This measurement is essential because the flow rate is directly related to the cross-sectional area of the fuel line. Using a caliper, measure the diameter of the fuel line and then calculate the area using the formula: Area = π * (diameter/2)^2. This will give you the cross-sectional area in square meters or square inches.
Step 3: Calculate Flow Rate: Now, you can calculate the required flow rate using the formula: Flow Rate = (Engine's Maximum Fuel Flow Rate) / (Cross-sectional Area of the Fuel Line). For example, if your engine requires 15 LPM and the cross-sectional area is 0.05 square meters, the calculation would be: Flow Rate = 15 LPM / 0.05 m^2 = 300 LPM/m^2. This means your fuel selector valve should be capable of handling a minimum of 300 LPM for a 3/8" fuel line.
Step 4: Consider Pressure and Efficiency: Keep in mind that fuel flow rate can also be influenced by system pressure and valve efficiency. Higher pressure may require a larger flow rate to ensure proper fuel delivery. Additionally, some valves may have efficiency ratings, which can impact the actual flow rate. It's essential to choose a valve that meets or exceeds your calculated flow rate while also considering the system's overall efficiency.
Step 5: Consult Experts and Manufacturers: If you're unsure about the calculations or valve selection, consult automotive experts or manufacturers who can provide guidance based on your specific engine and fuel system requirements. They can offer valuable insights to ensure you choose the right-sized fuel selector valve for optimal performance.
Fuel Line Sizing Guide: Perfect Fit for Your SSR Pit Bike
You may want to see also
Pressure Considerations: Account for pressure drops and engine requirements
When selecting the appropriate fuel selector valve for a 3/8" fuel line, it's crucial to consider the pressure requirements of your engine. Pressure drops can significantly impact fuel delivery and performance, so understanding these factors is essential for a successful installation. Here's a detailed guide on how to account for pressure drops and engine needs:
Engine Power and Pressure Needs: Different engines have varying pressure requirements for optimal performance. High-performance engines often demand higher fuel pressure to ensure efficient combustion and power output. When choosing a fuel selector valve, consider the engine's power output and the pressure it requires. For high-performance applications, you might need a larger valve with a higher pressure rating to accommodate the engine's demands.
Pressure Drop Calculation: Fuel lines experience pressure drops due to various factors, including line length, diameter, and bends. The pressure drop can be calculated using the Darcy-Weisbach equation, which takes into account the fluid's properties, flow rate, and line characteristics. For a 3/8" fuel line, you can estimate the pressure drop by considering the length of the line and the desired flow rate. Longer lines or those with multiple bends might require a larger valve to compensate for the increased pressure loss.
Selector Valve Pressure Rating: Fuel selector valves are designed with specific pressure ratings. It's essential to choose a valve that can handle the maximum pressure your engine requires. Look for valves with a pressure rating that exceeds your engine's needs. For instance, if your engine operates at 50 psi, select a valve with a minimum 60 psi rating to ensure it can withstand potential pressure fluctuations and provide reliable fuel distribution.
Flow Rate and Pump Capacity: The flow rate of your fuel pump should also be a consideration. Ensure that the selected fuel selector valve can handle the pump's output without causing excessive pressure drops. Properly sizing the valve to match the pump's flow rate will optimize fuel delivery and prevent engine performance issues.
Testing and Adjustment: After installation, it's beneficial to test the fuel system under various conditions. This includes running the engine at different speeds and loads to observe the pressure drops and ensure the selector valve performs as expected. Adjustments might be necessary to fine-tune the system, especially if you encounter any pressure-related issues.
Fuel Injector Linearity: A Matter of Efficiency and Precision
You may want to see also
Material Compatibility: Choose a valve material compatible with your fuel type
When selecting a fuel selector valve for your 3/8" fuel line, material compatibility is a critical factor to ensure optimal performance and longevity. The valve material must be able to withstand the corrosive nature of different fuel types, preventing degradation and ensuring a reliable fuel supply to your engine. Here's a detailed guide on how to choose the right material:
Understanding Fuel Types: Different fuels have varying chemical compositions, which can lead to different levels of corrosion and degradation. For instance, gasoline, ethanol blends, and diesel have distinct properties that require specific material considerations. Gasoline, often containing ethanol, can be more corrosive due to its higher water content, while diesel is more lubricating and can cause wear in certain materials. Understanding the fuel type you're working with is the first step in selecting the appropriate valve material.
Common Materials for Fuel Valves:
- Brass: This is a popular choice for fuel valves due to its excellent corrosion resistance and relatively low cost. It is suitable for gasoline and ethanol blends but may not be ideal for diesel, as it can lead to wear over time.
- Stainless Steel: Known for its superior corrosion resistance, stainless steel is an excellent option for diesel fuel, which is more challenging on valve materials. It is also suitable for gasoline and ethanol blends, offering a long-lasting solution.
- Bronze: Bronze valves are often used in aviation applications due to their ability to withstand the corrosive effects of aviation fuel. They are a good choice for gasoline and ethanol blends but may not be as durable for diesel.
- PTFE (Polytetrafluoroethylene): This material is highly resistant to corrosion and is often used in high-temperature applications. It is an excellent choice for fuels with high water content, as it prevents corrosion and maintains valve integrity.
Considerations for Material Selection:
- Fuel Type and Concentration: If you're using a fuel blend, consider the proportions of different fuels. For example, a higher ethanol content in gasoline may require a more corrosion-resistant material like stainless steel or PTFE.
- Operating Conditions: The environment in which the valve will operate is crucial. Consider factors like temperature, pressure, and exposure to sunlight or other elements that could affect material performance.
- Long-Term Reliability: Choose a material that ensures the valve's longevity and maintains its sealing properties over time. This is especially important for critical applications where fuel supply cannot be interrupted.
By carefully considering the material compatibility with your specific fuel type and operating conditions, you can select a fuel selector valve that provides reliable performance and ensures the longevity of your fuel system. It is always advisable to consult manufacturer guidelines and seek expert advice when in doubt to make an informed decision.
Understanding the Role of Fuel Line Hoses in the Evaporative Emissions System
You may want to see also
Mounting Options: Consider the available mounting positions on your fuel tank
When it comes to choosing the right fuel selector valve for your 3/8 fuel line, one crucial aspect to consider is the mounting options available on your fuel tank. The placement of the valve can significantly impact its functionality and overall performance. Here's a detailed guide to help you make an informed decision:
Assess the Tank's Design: Start by examining the fuel tank's design and layout. Different tanks may have varying mounting positions, such as the top, side, or even a more unique configuration. Consider the ease of access and the space available for the valve. For instance, if your tank has a limited space at the top, a side-mounted valve might be more practical. Understanding the tank's dimensions and the available real estate will help you narrow down the suitable valve options.
Mounting Orientation: Another important factor is the orientation in which the valve can be mounted. Some fuel selector valves are designed to be mounted horizontally, while others can accommodate vertical installation. Ensure that the chosen valve can be securely mounted in the desired orientation to prevent any leaks or malfunctions. This consideration is especially vital if your fuel line has a specific angle or if the tank's design requires a particular orientation.
Consider Tank Material: The material of your fuel tank can also influence the mounting process. Different materials, such as steel, aluminum, or plastic, may require specific mounting techniques or hardware. For example, some tanks might have a protective coating or a textured surface that could affect the adhesion of mounting screws or brackets. Knowing the tank's material will help you select the appropriate fasteners and ensure a secure installation.
Access and Maintenance: Think about the ease of access for future maintenance or repairs. Mounting the valve in a position that allows for convenient access will make it simpler to service or replace the valve when needed. Consider the angle and height of the tank, as well as any obstacles that might hinder access. Proper access points will ensure that you can efficiently perform maintenance tasks without causing unnecessary complications.
By carefully evaluating the available mounting positions on your fuel tank, you can select a fuel selector valve that fits perfectly and functions optimally. Remember, the right choice will not only ensure a reliable fuel supply but also contribute to the overall longevity and performance of your fuel system.
Understanding Feed Fuel Lines: Powering Your Engine's Performance
You may want to see also
Frequently asked questions
The size of the fuel selector valve depends on the specific application and engine requirements. For a 3/8" fuel line, a common size used is a 3/8" fuel selector valve, which is designed to fit the line perfectly. This valve typically has a 3/8" male pipe thread (MPT) on one end and a 3/8" female pipe thread (FPT) on the other, allowing for easy connection to the fuel line and other components.
While it is technically possible to use a larger valve, it is generally not recommended. A larger valve might not fit the fuel line snugly, leading to potential fuel leaks or reduced performance. It's important to choose a valve that matches the fuel line size to ensure a secure and efficient connection.
To determine the right size, consider the engine's fuel requirements, flow rate, and pressure. Consult the engine's manual or specifications to find the recommended fuel line diameter and valve size. Additionally, factors like the length of the fuel line and the presence of any fuel filters or pumps can influence the choice of valve size. It's always best to consult with a fuel system specialist or refer to industry guidelines for accurate sizing.