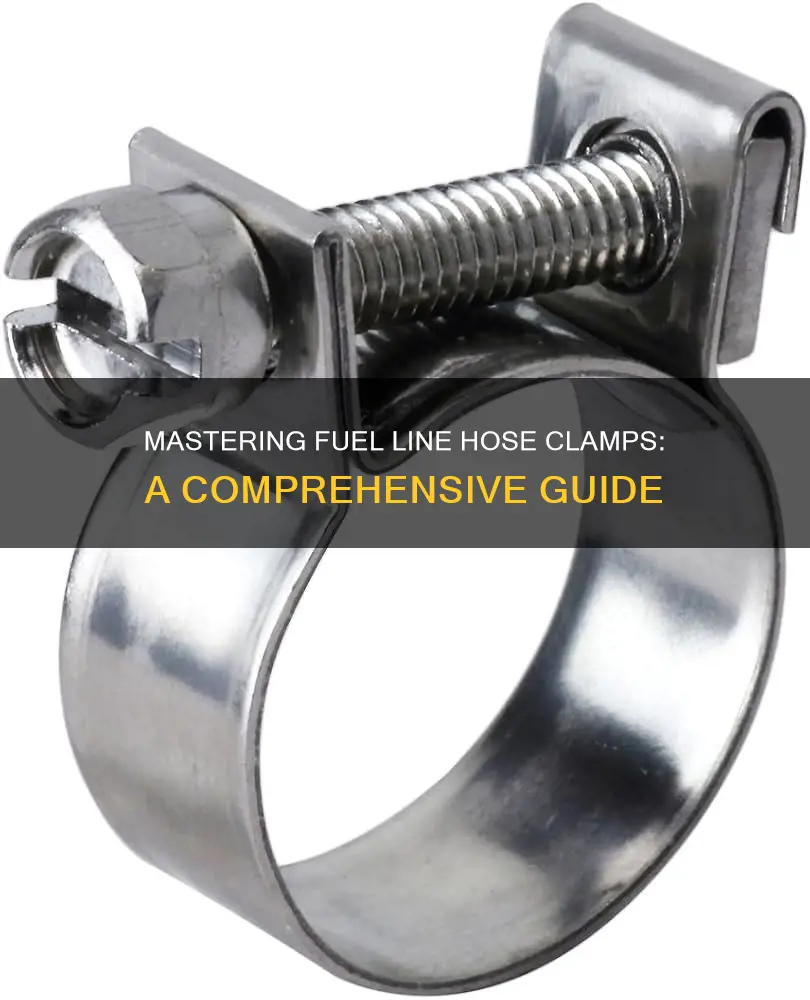
Fuel line hose clamps are essential components for securing fuel lines and hoses in automotive and industrial applications. These clamps are designed to provide a tight and reliable seal, ensuring that fuel lines remain secure and leak-free. They are typically made from durable materials such as stainless steel or aluminum, which offer excellent resistance to corrosion and wear. When using fuel line hose clamps, it's important to follow a few key steps. First, measure the hose or fuel line to determine the appropriate clamp size. Then, position the clamp around the hose, ensuring it is centered and aligned properly. Next, tighten the clamp using a wrench or spanner, being careful not to overtighten, as this can damage the hose. Finally, check the clamp's tightness by gently pulling on the hose to ensure it is securely held in place. Properly installed fuel line hose clamps are crucial for maintaining the integrity of fuel systems and preventing potential leaks or damage.
Characteristics | Values |
---|---|
Material | Stainless steel, aluminum, or brass |
Clamping Range | 1/8" to 2" (3mm to 50mm) |
Temperature Tolerance | -40°F to 400°F (-40°C to 204°C) |
Applications | Fuel lines, oil lines, water lines, and more |
Installation | Tighten by hand or with a tool, ensuring a secure grip |
Advantages | Secure and reliable, resistant to corrosion and heat |
Disadvantages | May require more force to install compared to other types of clamps |
Maintenance | Regularly check for tightness and damage |
Usage | Automotive, marine, and industrial applications |
Brand Examples | Gates, Kleenex, and various automotive suppliers |
What You'll Learn
- Clamping Technique: Tighten clamps by hand, then use a tool for a secure grip
- Fuel Line Routing: Ensure hoses are routed away from heat sources and sharp edges
- Clamp Placement: Position clamps at bends and joins for optimal support
- Size Selection: Choose clamp size based on hose diameter for proper fit
- Maintenance: Regularly inspect and replace clamps to prevent fuel leaks
Clamping Technique: Tighten clamps by hand, then use a tool for a secure grip
When working with fuel line hose clamps, a secure and tight connection is crucial to ensure the safety and efficiency of your vehicle's fuel system. One effective clamping technique involves a combination of hand tightening and the use of a specialized tool for added leverage and precision. This method ensures that the clamps are tightened evenly and securely, providing a reliable seal.
Start by placing the hose clamp around the fuel line, positioning it where you want to secure the connection. It's important to ensure that the clamp is centered and aligned properly. Begin tightening the clamp by hand, using a firm grip. Apply a steady force, turning the clamp in a clockwise direction. This initial tightening by hand helps to set the foundation for a secure hold.
Once you've tightened the clamp by hand, it's time to use a tool for a more secure grip. This step is crucial for achieving the desired level of tightness and ensuring the clamp doesn't loosen over time. Take a fuel line hose clamp tool, which is designed to provide a firm grip and allow for precise tightening. Place the tool over the clamp, ensuring it covers the entire length of the clamp.
Now, apply force to the tool, turning it in the same clockwise direction as before. This action will further tighten the clamp, ensuring a snug fit. The tool's design provides a mechanical advantage, allowing you to exert more pressure and achieve a tighter seal. Take care not to overtighten, as this can lead to damage to the fuel line or clamp.
After tightening the clamp with the tool, inspect the connection to ensure it is secure. Check for any signs of leakage or movement in the hose. If everything appears tight and secure, you can be confident that your fuel line is now properly clamped and protected. This technique ensures a professional-grade installation, providing peace of mind and optimal performance for your vehicle's fuel system.
Painting Fuel Lines: A Pre-Install Guide
You may want to see also
Fuel Line Routing: Ensure hoses are routed away from heat sources and sharp edges
When it comes to fuel line routing, proper placement is crucial to ensure the safety and longevity of your vehicle's fuel system. One essential aspect of this process is routing the fuel hoses away from potential heat sources and sharp edges. This practice helps prevent damage to the hoses and reduces the risk of fuel leaks, which could lead to dangerous situations.
Heat sources, such as exhaust manifolds, engine blocks, or even nearby components like the transmission, can cause the fuel hoses to degrade over time. High temperatures can lead to the deterioration of the hose material, causing cracks, brittleness, or even complete failure. To mitigate this, it is recommended to route the fuel lines as far away from these heat sources as possible. This can be achieved by carefully planning the hose path and considering the vehicle's architecture. For example, if your car has a front-engine layout, ensure the fuel lines are directed away from the engine bay and towards the rear of the vehicle, where temperatures are generally lower.
Additionally, it is vital to avoid routing fuel hoses near sharp edges or protruding objects. These can include engine mounts, transmission mounts, or even the vehicle's body panels. Sharp edges can easily cut or puncture the hose, leading to fuel leaks and potential fire hazards. When installing the hoses, take the time to carefully route them around these potential hazards, ensuring a smooth and secure path. You might consider using protective sleeves or shields to further safeguard the hoses from sharp objects.
To ensure optimal routing, consider the following steps: first, inspect the vehicle's architecture and identify potential heat sources and sharp edges. Then, plan the hose route, aiming to keep the fuel lines as far away from these hazards as possible. Use flexible hoses with adequate bend radii to accommodate any necessary turns without causing stress on the material. Finally, secure the hoses in place using appropriate clamps and ties, ensuring they remain stable and free from any obstructions.
By following these guidelines, you can effectively route your fuel lines, minimizing the risk of damage from heat and sharp edges. This proactive approach to fuel line management contributes to the overall safety and reliability of your vehicle's fuel system. Remember, proper routing is just one aspect of maintaining a healthy fuel system; regular inspections and maintenance are also essential to keep your vehicle running smoothly and safely.
Harley Sportster Fuel Line: Unveiling the Optimal Diameter
You may want to see also
Clamp Placement: Position clamps at bends and joins for optimal support
When working with fuel line hose clamps, proper placement is crucial to ensure a secure and reliable connection. One of the most critical areas to focus on is the bends and joins in your fuel lines. These points are prone to leaks and can be vulnerable to damage, especially during tight turns or when the vehicle is in motion. By strategically positioning the clamps at these bends and joins, you can provide optimal support and prevent potential issues.
Start by identifying the bends and joins in your fuel line setup. These are the areas where the hose changes direction or connects to other components. It's essential to apply the clamps at these specific points to maximize their effectiveness. For bends, place the clamps on both sides of the curve, ensuring they are centered and evenly distributed. This approach provides a sturdy grip, preventing the hose from kinking or bending excessively, which could lead to premature wear and potential leaks.
At joins, the goal is to secure the connection and prevent any movement or separation. Position the clamps on either side of the joint, ensuring they cover the entire circumference of the hose. This setup creates a tight seal, minimizing the risk of fuel leakage and ensuring a reliable connection. Remember, the key is to apply the clamps firmly but carefully, avoiding any damage to the fuel line itself.
Additionally, consider the orientation of the clamps. They should be positioned in a way that allows for easy access during maintenance or inspections. Avoid placing them in a way that might obstruct future work or make it challenging to remove the hose if needed. By keeping the clamps accessible, you ensure that your fuel system remains efficient and well-maintained.
In summary, proper clamp placement is an essential aspect of using fuel line hose clamps effectively. By focusing on bends and joins, you can provide the necessary support and security to your fuel lines. This approach helps prevent leaks, ensures a reliable connection, and contributes to the overall longevity of your vehicle's fuel system. Always remember to follow the manufacturer's guidelines and apply the clamps with care to achieve the best results.
Backwards Fuel Lines: A Recipe for Disaster
You may want to see also
Size Selection: Choose clamp size based on hose diameter for proper fit
When it comes to using fuel line hose clamps, one of the most critical aspects is selecting the right size. The size of the clamp is directly proportional to the diameter of the hose it will secure. Choosing the appropriate clamp size is essential to ensure a proper and secure fit, preventing any potential leaks or damage to the fuel line.
The process of selecting the right clamp size involves measuring the diameter of the fuel line hose. Most hose manufacturers provide the diameter of their hoses, which is typically measured in millimeters or inches. It is crucial to have this measurement accurate as it will determine the size of the clamp needed. For example, if you have a 1/2-inch diameter hose, you will require a specific size of hose clamp that fits this dimension.
Hose clamps come in various sizes, often indicated by a numerical code or a specific diameter range. It is essential to refer to the manufacturer's guidelines or the product packaging to identify the correct size for your hose. Using a clamp that is too small may result in a loose fit, allowing the hose to move and potentially causing leaks. Conversely, a clamp that is too large might damage the hose material and create a hazardous situation.
To ensure a proper installation, it is recommended to use a sizing chart or a clamp selection guide provided by the manufacturer. These tools will help you match the hose diameter with the appropriate clamp size. Additionally, it is worth noting that some hose clamps have adjustable features, allowing for a customized fit, but this is more common in specialized applications.
In summary, when using fuel line hose clamps, always prioritize size selection based on the hose diameter. This attention to detail will guarantee a secure and reliable connection, contributing to the overall safety and performance of your fuel system. Remember, the right size clamp is the foundation for a successful and leak-free installation.
Unraveling the Mystery: Why Fuel Lines Bubble
You may want to see also
Maintenance: Regularly inspect and replace clamps to prevent fuel leaks
Regular maintenance of fuel line hose clamps is crucial to ensure the safety and efficiency of your vehicle's fuel system. These clamps play a vital role in securing fuel lines, preventing leaks, and maintaining the integrity of the fuel supply. Over time, clamps can wear out, become damaged, or loosen, leading to potential fuel leaks, which can cause engine misfires, reduced performance, and even pose a fire hazard. Therefore, it is essential to inspect and replace these clamps regularly as part of your vehicle's maintenance routine.
During routine inspections, look for any signs of damage or deterioration. Clamps should be intact and free from cracks, brittleness, or any visible signs of wear. Check for any bends or kinks in the clamp body, as these can affect its ability to secure the fuel line tightly. Inspect the clamp's rubber or plastic components for any hardening or softening, as this can impact its flexibility and sealing properties. It is recommended to use a pair of pliers or a clamp tool to gently pull and feel for any play in the clamp, ensuring it remains tight and secure.
If you notice any issues during the inspection, it is best to replace the clamp immediately. Fuel leaks can be dangerous and costly, so do not attempt to repair a damaged clamp. When replacing clamps, ensure you have the correct size and type for your specific fuel line. Different fuel lines may require different clamp styles, such as V-band, slip-on, or quick-release clamps. Always refer to your vehicle's manual or consult a professional mechanic to determine the appropriate clamp specifications.
In addition to visual inspections, it is beneficial to develop a routine maintenance schedule. Create a checklist to remind yourself of the inspection intervals, typically every 6 months or 10,000 miles, depending on your driving conditions and the manufacturer's recommendations. Keep a record of the inspections and replacements to track the history of your fuel line clamps. This documentation can help identify patterns or recurring issues, allowing you to take proactive measures to prevent fuel leaks.
Remember, proper maintenance of fuel line hose clamps is a simple yet critical aspect of vehicle care. By regularly inspecting and replacing these clamps, you can ensure the reliability and safety of your engine's fuel supply, ultimately contributing to a smoother and more efficient driving experience.
The Ultimate Guide to Choosing the Right Hose Clamp for Your 3/8" Outboard Fuel Line
You may want to see also
Frequently asked questions
Fuel line hose clamps are essential components in the automotive industry, primarily used to secure fuel lines and hoses to ensure a tight and leak-free connection. They provide a reliable and adjustable hold, allowing for easy installation and maintenance of fuel systems.
Installation is a straightforward process. First, ensure the fuel line is clean and free of any debris. Place the hose clamp over the fuel line, positioning it at the desired point of attachment. Use pliers to tighten the clamp firmly, being careful not to overtighten, as this can damage the hose. Test the connection by applying pressure to ensure it is secure.
Reusing hose clamps is generally acceptable if they are in good condition. However, over time, clamps may become brittle or corroded, affecting their performance. If you notice any signs of damage, such as cracks or a loss of tension, it is best to replace them. Regular inspection and replacement will ensure the safety and efficiency of your fuel system.