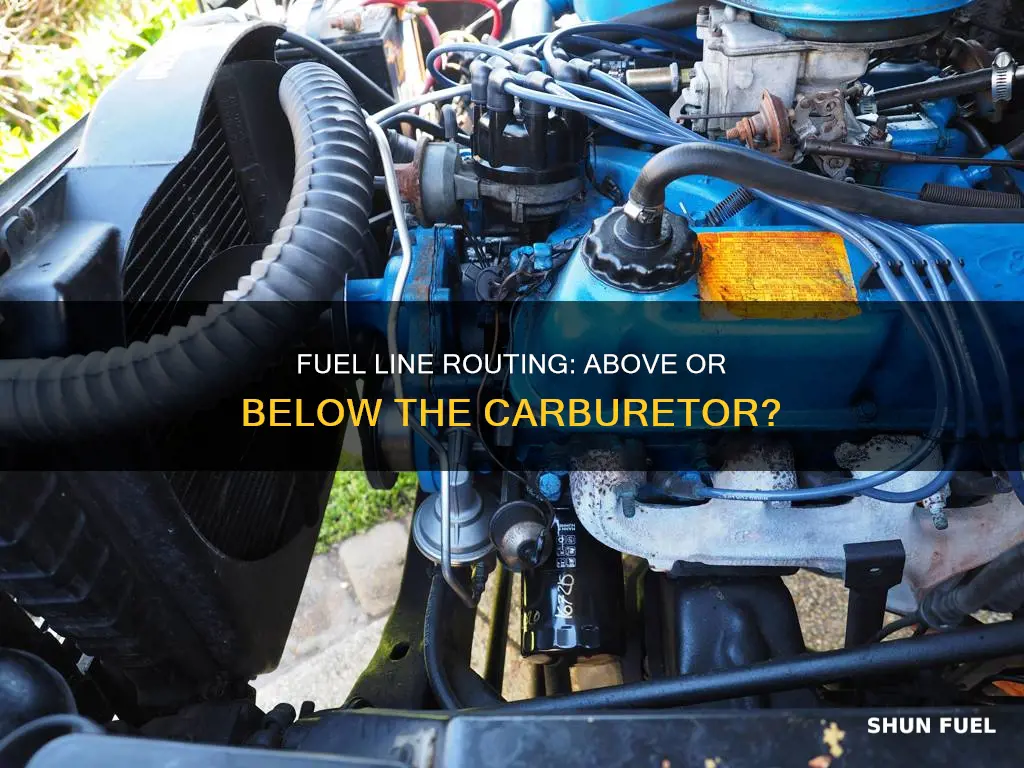
When it comes to engine performance and reliability, the routing of fuel lines is a critical aspect of vehicle maintenance. One common question among car enthusiasts and mechanics is whether the fuel line should be routed above the carburetor. This query delves into the optimal placement of fuel lines to ensure efficient fuel delivery and engine operation. By exploring this topic, we can gain insights into the best practices for fuel line installation, considering factors such as engine design, performance, and longevity. Understanding the proper routing of fuel lines is essential for maintaining a well-functioning engine and optimizing overall vehicle performance.
Characteristics | Values |
---|---|
Fuel Line Placement | Fuel lines can be routed either above or below the carburetor, depending on the vehicle's design and the specific requirements of the fuel system. |
Performance Considerations | Routing the fuel line above the carburetor can help prevent fuel contamination from engine oil or other substances. However, it may also make the system more susceptible to damage from heat and vibration. |
Design Variations | Some vehicles are designed with fuel lines that pass through the carburetor or are integrated into the carburetor's housing for better protection. |
Maintenance and Repairs | Access to the fuel line may be easier when routed above the carburetor, making maintenance and repairs more convenient. |
Safety and Reliability | Proper routing of the fuel line is crucial to prevent fuel leaks, which can lead to dangerous situations. |
Regulatory Compliance | In some regions, there might be regulations or standards regarding fuel line routing to ensure safety and performance. |
What You'll Learn
- Fuel Line Material: Consideration of fuel line material compatibility with fuel type and temperature
- Routing Height: Proper height of fuel line to prevent vacuum leaks and ensure efficient fuel flow
- Flexibility: Importance of flexible fuel lines to accommodate engine movement without restriction
- Clamping: Secure clamping of fuel lines to maintain a tight seal and prevent fuel leaks
- Vibration Resistance: Selection of fuel lines resistant to engine vibrations to ensure long-term reliability
Fuel Line Material: Consideration of fuel line material compatibility with fuel type and temperature
When it comes to fuel lines, the choice of material is crucial and directly impacts the performance and longevity of the fuel system. The compatibility of the fuel line material with the type of fuel being used and the operating temperature is essential to ensure optimal performance and prevent potential issues. Different fuels have varying properties, and the fuel line must be able to withstand these characteristics to maintain a reliable fuel supply.
For instance, gasoline and ethanol blends require fuel lines that can handle the volatility and potential corrosion caused by these fuels. Rubber or synthetic rubber-based materials are commonly used for gasoline fuel lines due to their flexibility and resistance to gasoline's corrosive effects. On the other hand, diesel fuel is more robust and has a higher boiling point, making materials like nylon or braided stainless steel suitable choices for fuel lines to ensure durability and prevent fuel leakage.
Temperature considerations are equally important. Fuel lines must be able to withstand extreme temperatures, especially in high-performance engines or vehicles operating in diverse climates. For high-temperature applications, materials like stainless steel or high-temperature plastics are preferred. These materials offer excellent heat resistance and can handle the intense heat generated by the engine without compromising the fuel's integrity. In colder environments, flexible fuel lines made from materials like rubber or silicone are recommended to prevent brittleness and cracking due to freezing temperatures.
Additionally, the temperature at which the fuel is stored and used can vary, and the fuel line material should be compatible with these temperature fluctuations. Some fuels may experience thermal expansion or contraction, and the fuel line must accommodate these changes without compromising its structural integrity. Materials with good thermal stability, such as certain types of rubber or plastic composites, are ideal for such applications.
In summary, selecting the appropriate fuel line material involves considering the specific fuel type and its properties, as well as the operating temperature range. Compatibility ensures that the fuel line can effectively convey the fuel while maintaining its structural integrity and performance over time. It is a critical aspect of engine maintenance and should be given careful attention to avoid potential fuel system failures.
Choosing the Right Fuel Line: A Guide for 9N Cobalt Owners
You may want to see also
Routing Height: Proper height of fuel line to prevent vacuum leaks and ensure efficient fuel flow
The routing height of the fuel line is a critical factor in ensuring optimal performance and reliability of a vehicle's fuel system. When it comes to routing the fuel line above the carburetor, there are specific considerations to keep in mind. Firstly, the fuel line should be positioned at an appropriate height to avoid any interference with the carburetor's operation. The ideal height is typically around 6 to 12 inches above the carburetor, allowing for a clear path for the fuel to flow without any restrictions. This height range helps prevent vacuum leaks, which can occur if the fuel line is too close to the carburetor, leading to reduced engine performance.
Maintaining the correct routing height is essential for several reasons. Firstly, it ensures that the fuel line is not constricting the flow of fuel, which can result in inefficient combustion. Proper height allows for a smooth and continuous flow of fuel from the tank to the carburetor, promoting optimal engine performance. Additionally, routing the fuel line at the right height helps prevent the formation of air bubbles, as a higher position reduces the chances of the fuel line being too close to the ground, where air can easily enter and cause issues.
In some cases, the fuel line may need to be elevated even higher, especially in vehicles with modified or high-performance engines. These modifications can alter the engine's operating conditions, requiring the fuel line to be positioned at a higher elevation to maintain the necessary vacuum levels. It is crucial to consult the vehicle's manual or seek professional advice to determine the specific routing requirements for your engine.
Furthermore, the material and construction of the fuel line play a role in its proper routing. Flexible fuel lines are more susceptible to kinking and bending, so they should be routed with extra care to avoid any sharp turns or tight spaces. Rigid fuel lines, on the other hand, can be more straightforward to route but may require additional support to maintain the required height. Understanding the characteristics of your fuel line is essential for ensuring a proper installation.
In summary, the routing height of the fuel line above the carburetor is a critical aspect of vehicle maintenance. By maintaining the correct height, you can prevent vacuum leaks, ensure efficient fuel flow, and promote optimal engine performance. Always refer to the vehicle's manual or consult with experts to determine the specific routing requirements for your engine, taking into account the fuel line's material and construction to ensure a reliable and safe fuel system.
Troubleshooting Fuel Pump and Line Issues: A Comprehensive Guide
You may want to see also
Flexibility: Importance of flexible fuel lines to accommodate engine movement without restriction
The routing of fuel lines is a critical aspect of engine design, especially when considering the performance and longevity of the fuel system. One of the key factors to ensure optimal functionality is the flexibility of these lines. Fuel lines, which carry gasoline from the tank to the carburetor or fuel injectors, need to be flexible enough to accommodate the natural movement and vibrations of the engine during operation. This flexibility is crucial for several reasons.
Firstly, engines experience significant movement and stress during operation, especially in high-performance vehicles. The engine block, cylinders, and various components shift and vibrate, and the fuel lines must be able to move with the engine without becoming restricted or damaged. Rigid fuel lines can lead to fuel starvation, as they may become kinked or pinched, obstructing the flow of fuel. This can result in poor engine performance, reduced power, and even engine stall. Therefore, using flexible fuel lines is essential to ensure a consistent and uninterrupted supply of fuel to the engine.
Secondly, the design of the fuel system should consider the engine's natural movement. As the engine operates, the fuel lines need to bend and adjust to the changing angles and positions of the engine components. Flexible lines can easily conform to these movements, ensuring that the fuel remains in a constant state of flow. In contrast, rigid lines may become taut and restrict fuel flow, leading to potential issues with starting the engine or maintaining stable operation.
Furthermore, the flexibility of fuel lines is vital for the overall maintenance and longevity of the engine. Over time, fuel lines can degrade due to heat, vibration, and chemical exposure. Flexible lines are more resistant to these factors, reducing the risk of cracks, leaks, or fuel contamination. This not only ensures a reliable fuel supply but also helps prevent costly engine repairs and replacements.
In summary, the importance of flexible fuel lines cannot be overstated. They play a critical role in accommodating the engine's movement, ensuring a consistent fuel supply, and contributing to the overall reliability and performance of the vehicle. When designing or modifying an engine, it is essential to prioritize the use of flexible fuel lines to avoid potential issues and maintain optimal engine functionality.
Optimizing Performance: Choosing the Right Fuel Line for Your Mahle 145 Engine
You may want to see also
Clamping: Secure clamping of fuel lines to maintain a tight seal and prevent fuel leaks
When it comes to fuel line routing, one common practice is to route the fuel lines above the carburetor. This is a design choice often made in older vehicles, especially those with carburetors, as it provides easy access for maintenance and allows for better air flow around the engine bay. However, this placement can also lead to potential issues if not properly secured. One of the critical aspects of maintaining a reliable fuel system is ensuring that the fuel lines are clamped securely to prevent any leaks.
Clamping is a crucial step in the installation process of fuel lines. The primary purpose of clamping is to create a tight seal between the fuel lines and the surrounding components, such as the carburetor, fuel tank, and engine block. By using specialized fuel line clamps, you can ensure that there is no movement or vibration-induced movement of the fuel lines, which could lead to fuel leaks or even damage to the lines over time. These clamps are typically made of durable materials like stainless steel or nylon, designed to withstand the high pressure and temperature variations within the fuel system.
The clamping process involves several steps. First, you need to identify the correct type and size of clamp for your specific fuel line. Different fuel lines have varying diameters and materials, so using the appropriate clamp is essential. Once you have the right clamp, locate the fuel line and position the clamp securely around it, ensuring that it covers the entire length of the line where it connects to other components. The clamp should be tight enough to provide a secure hold but not so tight that it causes any damage to the fuel line or surrounding parts.
To achieve a proper seal, it's important to follow the manufacturer's guidelines for clamping. This may involve using specific tools to tighten the clamp securely without causing any distortion or damage. Over-tightening can lead to fuel line damage, while under-tightening may result in a poor seal, allowing fuel to leak. Regularly checking and tightening the clamps, especially after any engine work or when replacing fuel lines, is essential to maintain the integrity of the fuel system.
In summary, clamping fuel lines is a critical step in ensuring a reliable and safe fuel system, especially when routing the lines above the carburetor. By using the right type of clamp and following proper installation techniques, you can maintain a tight seal, prevent fuel leaks, and protect the overall performance of your vehicle's engine. Regular maintenance and inspection of the fuel lines and clamps are recommended to identify and address any potential issues promptly.
Understanding the Key Differences: Brake vs. Fuel Lines
You may want to see also
Vibration Resistance: Selection of fuel lines resistant to engine vibrations to ensure long-term reliability
When it comes to engine performance and longevity, the choice of fuel lines is often overlooked, but it plays a crucial role in ensuring optimal operation. One critical aspect to consider is vibration resistance, especially for fuel lines that are routed above the carburetor. These lines are susceptible to constant movement and vibrations generated by the engine's operation, which can lead to potential issues over time.
Vibration resistance in fuel lines is essential to maintain a consistent and reliable fuel supply to the engine. The carburetor, being a moving component, can cause the fuel lines to experience excessive movement, leading to potential damage or disconnection. Over time, this can result in fuel leaks, poor engine performance, and even costly repairs. Therefore, selecting fuel lines with superior vibration resistance is a proactive approach to ensure the long-term reliability of the vehicle.
Engineers and manufacturers have developed various materials and designs to enhance vibration resistance in fuel lines. One common approach is to use flexible yet sturdy materials such as high-density rubber or synthetic compounds. These materials can absorb and dampen the vibrations, reducing the risk of damage to the fuel lines and the carburetor. Additionally, fuel lines with reinforced layers or protective coatings can further enhance their durability and resistance to wear and tear.
The routing of fuel lines also plays a significant role in vibration resistance. Proper installation and routing techniques can minimize the impact of engine vibrations. For lines above the carburetor, it is recommended to secure them with robust clamps or brackets that provide a firm grip, preventing excessive movement. Additionally, routing the lines away from sharp edges or protruding engine components can help reduce the risk of damage.
In summary, when dealing with fuel lines above the carburetor, vibration resistance is a critical factor to consider. By selecting high-quality fuel lines with appropriate materials and ensuring proper routing, vehicle owners can significantly improve the long-term reliability of their engines. This simple yet essential aspect of maintenance can contribute to a smoother and more efficient driving experience, ultimately saving time and money on potential repairs.
Fixing a Fuel Line Leak: A Step-by-Step Guide
You may want to see also
Frequently asked questions
While it is not mandatory to route the fuel line above the carburetor, it is a common practice in many vehicle designs. This routing allows for better access to the carburetor and can facilitate easier maintenance and repairs. However, some vehicles may have fuel lines routed elsewhere for structural or space constraints.
In some cases, routing the fuel line above the carburetor can lead to potential problems. Over time, the fuel line may rub against the carburetor or other engine components, causing damage or leaks. Additionally, if the fuel line is not properly secured, it might come loose, resulting in fuel spillage or loss of power.
Routing the fuel line below the carburetor can offer advantages in terms of aesthetics and engine protection. It helps keep the fuel line away from potential heat sources and reduces the risk of damage from road debris or accidental impacts. This routing also provides a cleaner and more streamlined appearance to the engine bay.