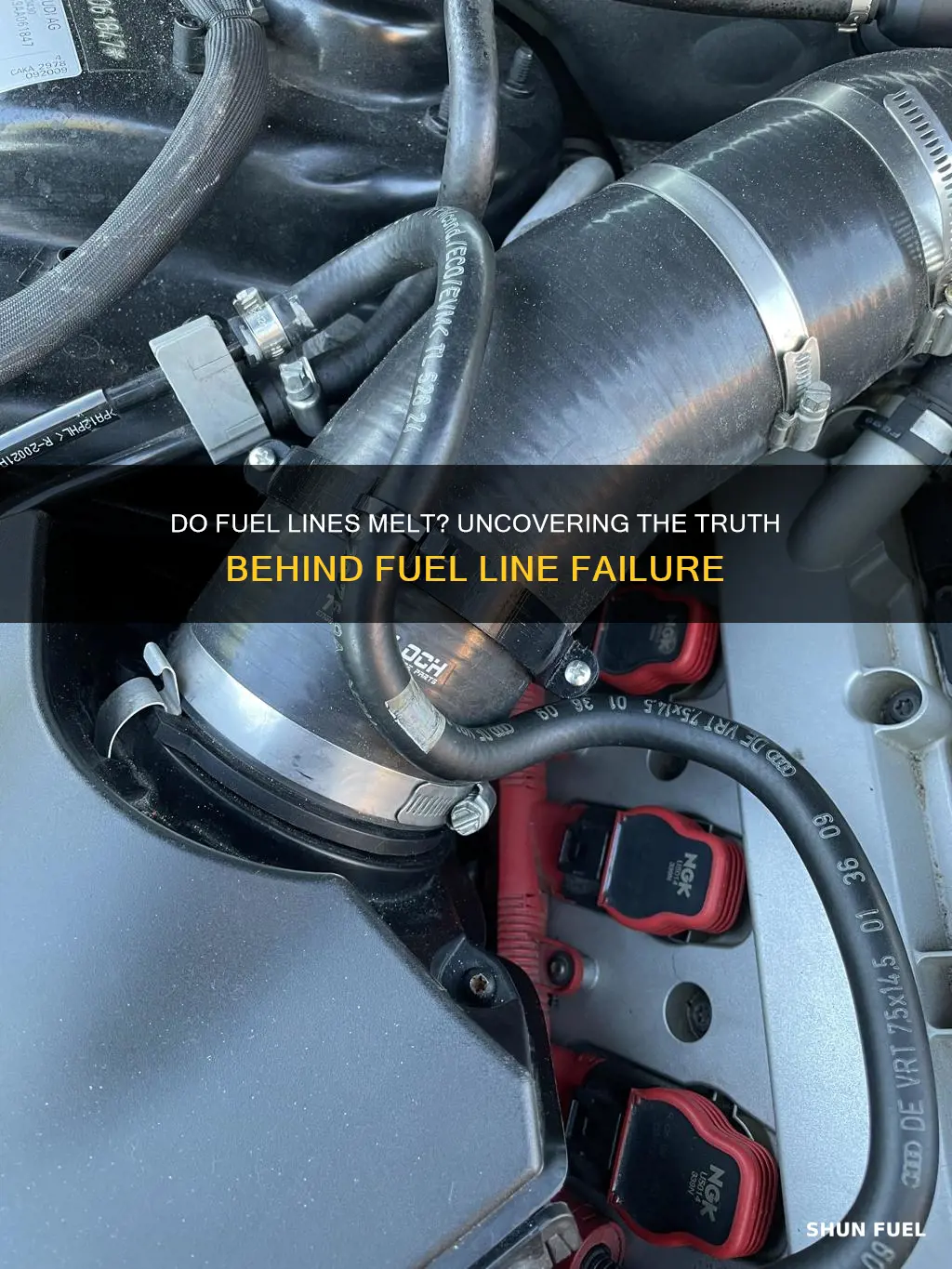
Fuel lines are an essential component of any vehicle's fuel system, responsible for transporting fuel from the tank to the engine. While they are designed to withstand high temperatures and pressures, there are concerns about whether fuel lines can melt under certain conditions. This paragraph will explore the factors that can cause fuel lines to melt and the potential consequences, as well as discuss the materials and design features used to prevent such incidents.
Characteristics | Values |
---|---|
Material | Plastic, metal, rubber |
Temperature Resistance | Varies, typically up to 250°F (121°C) |
Fuel Compatibility | Gasoline, diesel, ethanol, biofuel |
Melting Point | Depends on material, but generally above 200°C (392°F) |
Durability | Resistant to fuel degradation and corrosion |
Flexibility | Can bend and move with engine vibrations |
Installation | Easy to install and replace |
Cost | Affordable, depending on material and brand |
Maintenance | Regular inspection and replacement recommended |
Safety | Important to use high-quality fuel lines to prevent leaks and fires |
What You'll Learn
- Fuel Line Material: Different materials have varying melting points, affecting fuel line durability
- Fuel Temperature: High temperatures can cause fuel lines to melt, especially during engine operation
- Fuel Line Routing: Proper routing prevents heat buildup and potential melting
- Environmental Factors: Extreme weather conditions can accelerate fuel line degradation and melting
- Fuel Line Protection: Insulation and shielding can prevent fuel lines from melting
Fuel Line Material: Different materials have varying melting points, affecting fuel line durability
The material of a fuel line is a critical factor in determining its durability and performance. Different materials have distinct melting points, which directly impact how well the fuel line can withstand high temperatures and the overall longevity of the component. When considering fuel line material, it's essential to understand the specific requirements of the application, as certain materials may be more suitable for high-temperature environments, while others might be better suited for low-temperature conditions.
One common material used for fuel lines is rubber, which is known for its flexibility and resistance to abrasion. Rubber fuel lines are often used in automotive applications due to their ability to withstand the fluctuating temperatures experienced in engines. However, it's important to note that natural rubber has a relatively low melting point, typically around 200-220°F (93-104°C). This means that in high-temperature environments, rubber fuel lines may not be the most durable option, as they can become soft and more susceptible to damage over time.
In contrast, synthetic rubber, such as neoprene or butyl rubber, offers improved heat resistance. These materials have higher melting points, often exceeding 300°F (149°C), making them more suitable for high-temperature applications. Synthetic rubber fuel lines are commonly used in racing cars or vehicles operating in extreme conditions, ensuring that the fuel lines remain intact and functional even when exposed to intense heat.
Another material often utilized in fuel line construction is vinyl, which is known for its chemical resistance and flexibility. Vinyl fuel lines are lightweight and can provide good durability, especially when combined with a suitable reinforcement material like braided steel. Vinyl has a higher melting point compared to natural rubber, typically around 250-300°F (121-149°C), making it a more reliable choice for high-temperature environments. However, it's important to choose the right type of vinyl for the specific fuel type, as some vinyls may not be compatible with certain fuels, leading to potential degradation over time.
For applications requiring the highest level of heat resistance, materials like fluoropolymer or PTFE (polytetrafluoroethylene) can be considered. These materials have extremely high melting points, often exceeding 500°F (260°C), making them ideal for extreme high-temperature environments. Fluoropolymer fuel lines are commonly used in aviation or industrial applications where fuel temperatures can soar. However, these materials are typically more expensive and may require specialized installation techniques due to their unique properties.
In summary, the choice of fuel line material depends on the specific requirements of the application, including temperature extremes, fuel type, and environmental conditions. Understanding the melting points and properties of different materials ensures that the fuel lines are durable, reliable, and capable of withstanding the challenges they may encounter in various automotive, industrial, or aviation settings.
Defrosting Frozen Diesel: Quick Tips for Thawing Gelled Fuel Lines
You may want to see also
Fuel Temperature: High temperatures can cause fuel lines to melt, especially during engine operation
The concept of fuel lines melting is a critical concern for vehicle owners and mechanics alike, especially when considering the high temperatures that fuel systems can experience during operation. When an engine is running, the fuel system is subjected to intense heat, which can have detrimental effects on the fuel lines. These lines, often made of rubber or plastic, are designed to withstand a certain degree of heat, but prolonged exposure to excessive temperatures can lead to their deterioration and potential failure.
High fuel temperatures are a common issue, particularly in older vehicles or those with inefficient fuel systems. The engine's combustion process generates a significant amount of heat, and this heat is transferred to the fuel as it circulates through the system. Over time, this can cause the fuel lines to become brittle and more susceptible to damage. Rubber fuel lines, in particular, are at risk due to their composition; they can crack, split, or even melt when exposed to prolonged high temperatures.
The melting of fuel lines is a serious problem as it can lead to fuel leaks, which pose a fire hazard and can also cause engine performance issues. When fuel lines melt, they may lose their structural integrity, allowing fuel to leak out onto hot engine components, potentially igniting a fire. Additionally, a fuel leak can lead to reduced engine performance, as the engine may not receive the correct amount of fuel, resulting in poor acceleration, reduced power, and even engine stall.
To prevent fuel line melting, it is essential to maintain the engine and fuel system properly. Regularly checking for signs of wear and tear, such as cracks or brittleness, is crucial. Upgrading to high-temperature-resistant fuel lines can also be a preventative measure, especially for older vehicles or those with known fuel system issues. Ensuring that the engine is properly cooled and that the fuel system is well-maintained can significantly reduce the risk of fuel line melting and the associated hazards.
In summary, high temperatures during engine operation can cause fuel lines to melt, leading to potential fuel leaks and engine performance issues. Understanding the risks and taking proactive measures to prevent this can help ensure the safety and reliability of a vehicle's fuel system. Regular maintenance and the use of appropriate materials can go a long way in mitigating the dangers associated with fuel line melting.
The Ultimate Guide to Propane Fuel Line Manufacturers
You may want to see also
Fuel Line Routing: Proper routing prevents heat buildup and potential melting
Fuel lines are an essential component of any vehicle's fuel system, responsible for transporting gasoline or diesel from the tank to the engine. While they are designed to withstand the pressures and temperatures encountered during operation, improper routing can lead to heat buildup, which in turn may cause the fuel lines to melt. This is a critical issue that can result in engine damage and costly repairs. Therefore, understanding the proper routing techniques for fuel lines is crucial for maintaining a vehicle's performance and longevity.
The primary cause of heat buildup in fuel lines is the proximity to hot engine components. Exhaust manifolds, catalytic converters, and engine blocks can radiate significant heat, which can be transferred to the fuel lines if they are not routed correctly. When fuel lines are too close to these hot surfaces, the fuel can absorb heat, leading to a rise in temperature. Over time, this can cause the fuel lines to become brittle and potentially melt, especially if the fuel contains certain additives or if the vehicle operates under extreme conditions.
To prevent heat buildup and potential melting, it is essential to follow manufacturer guidelines for fuel line routing. These guidelines often specify the minimum distance that fuel lines should maintain from hot engine components. For example, fuel lines should be routed away from exhaust manifolds and placed in areas with better insulation or cooler temperatures. In some cases, additional insulation or heat shielding may be required to protect the fuel lines from excessive heat.
Proper routing also involves considering the flexibility and movement of the vehicle. Fuel lines should be routed in a way that allows for natural expansion and contraction due to temperature changes. This is particularly important for vehicles that experience extreme temperature variations, such as those used in racing or off-road applications. By allowing the fuel lines to move freely, you reduce the risk of damage and ensure optimal performance.
Furthermore, regular inspection of fuel lines is vital to identify any potential issues early on. Over time, fuel lines can develop cracks or become damaged, which may not be immediately noticeable. Inspecting the lines for any signs of wear, corrosion, or heat damage is essential, especially in high-temperature environments. If any issues are found, the fuel lines should be replaced promptly to prevent further complications.
In summary, proper fuel line routing is a critical aspect of vehicle maintenance. By ensuring that fuel lines are routed away from hot engine components and allowing for flexibility, you can prevent heat buildup and the potential melting of the lines. Following manufacturer guidelines and conducting regular inspections will help maintain the integrity of the fuel system and ensure the vehicle's overall performance and reliability.
Mastering Plastic Fuel Lines: The Ultimate Seal for Long-Lasting Performance
You may want to see also
Environmental Factors: Extreme weather conditions can accelerate fuel line degradation and melting
Extreme weather conditions, such as intense heat, cold, and humidity, can significantly impact fuel lines and contribute to their degradation and melting. These environmental factors play a crucial role in the performance and longevity of fuel lines, especially in vehicles and machinery that operate in varying climates.
In regions with scorching summers, the heat can cause fuel lines to expand and contract rapidly, leading to stress and potential damage. Over time, this thermal cycling can result in cracks, leaks, and even complete melting of the fuel lines. The high temperatures can also cause the fuel to degrade, forming varnish and sludge, which further exacerbates the issue. It is essential to use fuel lines made from materials that can withstand such extreme heat to prevent premature failure.
Conversely, extremely cold environments can also be detrimental. When temperatures drop, the fuel can thicken and become more viscous, making it challenging to flow through the fuel lines. This situation can lead to reduced engine performance and even complete engine failure if the fuel lines are not properly insulated or made from materials that can handle low temperatures. In such cases, the fuel lines may crack or even freeze, causing internal damage.
Humidity is another critical factor, especially in coastal areas or regions with high levels of moisture in the air. Moisture can penetrate the fuel lines, leading to corrosion and the formation of rust. Over time, this can result in fuel contamination and reduced engine performance. The moisture can also contribute to the growth of microorganisms, further degrading the fuel and causing blockages in the fuel lines.
To mitigate these environmental factors, it is recommended to use high-quality fuel lines made from durable materials such as stainless steel or reinforced rubber. Proper insulation and regular maintenance, including fuel line inspections and replacements, are essential to ensure optimal performance and longevity, especially in regions with extreme weather conditions. Understanding and addressing these environmental influences are vital to preventing fuel line-related issues and ensuring reliable operation in various climates.
Mastering the Process: Extracting Fuel Lines from Transfer Pumps
You may want to see also
Fuel Line Protection: Insulation and shielding can prevent fuel lines from melting
Fuel lines are an essential component of any vehicle's fuel system, responsible for transporting gasoline or diesel from the tank to the engine. While these lines are designed to withstand the high pressures and temperatures encountered during operation, they are not immune to damage. One of the most common concerns is the possibility of fuel lines melting, which can lead to fuel leaks, engine misfires, and even complete engine failure. Fortunately, there are several measures that can be taken to protect fuel lines and prevent them from melting.
Insulation is a critical aspect of fuel line protection. Fuel lines are typically made of rubber or plastic, which can become brittle and susceptible to heat damage over time. Insulation helps to maintain a consistent temperature along the fuel line, preventing localized hotspots that could cause the material to degrade. There are various types of insulation available, including rubber sleeves, foam wraps, and even specialized thermal blankets. These materials are designed to absorb and distribute heat evenly, ensuring that the fuel line remains within safe temperature limits.
In addition to insulation, shielding is another effective method to safeguard fuel lines. Shielding involves using protective barriers to guard the fuel lines against external heat sources. For example, in high-performance vehicles or those operating in extreme environments, the fuel lines may be exposed to intense heat from nearby exhaust systems or engine components. By installing heat shields, made of metal or heat-resistant materials, the fuel lines are physically protected from direct contact with hot surfaces, reducing the risk of melting.
The installation of insulation and shielding should be done carefully to ensure optimal protection. It is essential to follow manufacturer guidelines and best practices to ensure a proper fit and secure attachment. Insulation should be applied continuously along the length of the fuel line, paying attention to any bends or joints, as these areas may require additional protection. Shielding should be strategically placed to cover vulnerable sections, such as those near heat sources or under the vehicle where they might be susceptible to road debris or impact damage.
Regular maintenance and inspections are also crucial for fuel line protection. Over time, insulation can degrade or become dislodged, especially in areas with high vibration or temperature fluctuations. Inspecting the fuel lines periodically for any signs of damage, cracks, or discolored insulation can help identify issues early on. Replacing worn-out insulation or reinforcing vulnerable sections can prevent potential fuel line failures and ensure the longevity of the vehicle's fuel system.
Unleash the Power: Milwaukee's Fuel Line Revolution
You may want to see also
Frequently asked questions
Yes, fuel lines can melt if exposed to extremely high temperatures. The melting point of fuel lines varies depending on the material, but generally, they are designed to withstand the operating temperatures of the engine. However, prolonged exposure to excessive heat, such as near a hot exhaust manifold or a malfunctioning fuel pump, can cause the fuel lines to degrade and eventually melt.
There are a few indicators that a fuel line might be overheating and at risk of melting. These include fuel leaks, reduced engine performance, engine stalling, or a burning smell. If you notice any of these symptoms, it's essential to inspect the fuel lines for damage and address the issue promptly to prevent potential engine failure.
Absolutely! Preventive measures include using high-quality fuel lines made from heat-resistant materials, ensuring proper engine maintenance, and regularly checking for any signs of damage or overheating. It's also crucial to address any underlying issues, such as a faulty fuel pump or exhaust system, to prevent excessive heat buildup in the fuel lines.
Fuel line melting can be identified through visual inspection. Look for any signs of warping, cracking, or charring along the length of the fuel line. If you notice any of these issues, it's best to consult a mechanic for a thorough inspection and potential replacement of the affected fuel lines.
No, the susceptibility to melting varies depending on the material and construction of the fuel lines. Some materials are more heat-resistant than others. It's important to choose fuel lines that are compatible with your engine's operating conditions and to ensure proper installation to minimize the risk of melting.