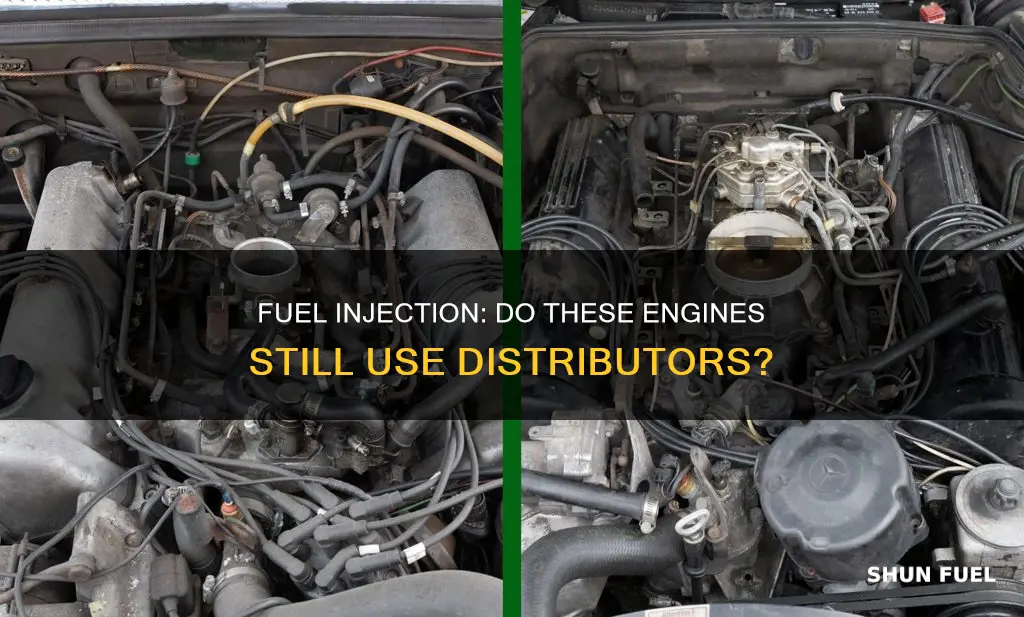
Fuel-injected cars, which are a common type of modern vehicle, have evolved significantly from their carbureted predecessors. One of the key differences between these two systems is the method by which fuel is delivered to the engine. While carbureted cars use a carburetor to mix air and fuel, fuel-injected cars rely on an electronic fuel injection system. This system is more precise and efficient, but it also differs in its approach to ignition timing. In contrast to the traditional distributor used in carbureted cars, fuel-injected cars often use an ignition coil and spark plugs, which are controlled by the engine's computer. This shift in technology has led to more reliable and efficient engines, but it also means that the concept of a distributor is less relevant in modern fuel-injected vehicles.
Characteristics | Values |
---|---|
Fuel Injection System | Fuel-injected cars use an electronic system to deliver fuel to the engine, which can be either port fuel injection (PFI) or direct fuel injection (DFI). |
Distributor | A distributor is a component in a traditional carbureted engine that routes high-voltage electricity from the ignition coil to the spark plugs at the correct timing. |
Modern Engines | In modern fuel-injected engines, the distributor is typically replaced by an ignition coil and spark plugs, which are controlled by the engine's computer. |
Advantages | Fuel injection offers better fuel efficiency, improved performance, and reduced emissions compared to carbureted engines. |
Reliability | The absence of a distributor in fuel-injected cars can lead to more reliable and consistent performance, as there are fewer moving parts. |
Maintenance | Without a distributor, these cars often require less maintenance related to ignition system components. |
Application | Fuel injection is commonly found in newer vehicles, including cars, trucks, and motorcycles. |
Retrofit Options | Some car enthusiasts might choose to retrofit a fuel-injected system onto a carbureted engine, but this is not a common practice for modern cars. |
What You'll Learn
- Fuel Injection Basics: Fuel injectors deliver fuel directly to the engine, bypassing the carburetor
- Distributor Role: In older cars, distributors manage spark timing, but fuel injection doesn't need this
- Fuel Injection Systems: These systems use electronic controls to precisely manage fuel delivery
- Spark Plug Location: Fuel injection often eliminates the need for a distributor, changing spark plug placement
- Engine Management: Modern fuel injection systems use sophisticated sensors and computers to optimize performance
Fuel Injection Basics: Fuel injectors deliver fuel directly to the engine, bypassing the carburetor
Fuel injection is a vital component of modern engine technology, offering a more efficient and controlled way of delivering fuel to the engine compared to traditional carburetor systems. The primary advantage of fuel injection is its ability to precisely manage the fuel-air mixture, ensuring optimal combustion and improved engine performance. This technology has become increasingly prevalent in recent years, especially in high-performance and luxury vehicles.
At the heart of this system are the fuel injectors, which are responsible for spraying the fuel into the engine's intake manifold or directly into the combustion chamber. Unlike the carburetor, which mixes air and fuel in a single step, fuel injectors provide a more accurate and efficient process. They deliver the exact amount of fuel required for each cylinder, taking into account various engine parameters such as speed, load, and temperature. This level of precision results in a more complete combustion process, reducing emissions and improving overall engine efficiency.
The process begins with the engine control unit (ECU), which acts as the brain of the fuel injection system. The ECU receives input from various sensors, including engine speed, temperature, and oxygen levels. Based on this data, it calculates the ideal fuel-air ratio and sends a signal to the fuel injectors. Each injector then delivers the precise amount of fuel required, ensuring a consistent and efficient burn. This real-time adjustment capability is a significant improvement over carburetors, which rely on a fixed jetting design and cannot adapt to changing engine conditions as quickly.
One of the key benefits of fuel injection is its ability to provide a more consistent and controlled fuel supply, especially under varying load conditions. When an engine is under heavy load, such as during acceleration or climbing a steep hill, the fuel injectors can deliver an additional burst of fuel to meet the increased demand. Conversely, during light load conditions, the injectors can reduce the fuel flow, optimizing fuel usage and reducing waste. This dynamic adjustment ensures that the engine always operates at its most efficient level.
In summary, fuel injectors play a critical role in modern engine design by delivering fuel directly to the engine, bypassing the traditional carburetor. This system offers improved fuel efficiency, reduced emissions, and enhanced engine performance. With the ability to precisely manage the fuel-air mixture, fuel injection technology has become a standard feature in many vehicles, providing drivers with a more responsive and environmentally friendly driving experience. Understanding the basics of fuel injection is essential for anyone looking to optimize their vehicle's performance and maintain its longevity.
Troubleshooting: Revive Your Ride with These Steps to Start a Car with a Bad Fuel Filter
You may want to see also
Distributor Role: In older cars, distributors manage spark timing, but fuel injection doesn't need this
The distributor is a crucial component in the ignition system of older cars, particularly those with carbureted engines. Its primary function is to manage the timing of the spark plugs, ensuring that the engine receives the precise spark at the right moment during the combustion cycle. This process is essential for efficient and effective engine operation. In the context of fuel injection, the distributor's role becomes less significant, as fuel-injected engines operate differently.
In older cars, the distributor is typically located near the top of the engine and houses a set of rotating components. These components include the distributor cap, which holds the spark plugs, and the rotor, which rotates and makes contact with the distributor cap's points. When the rotor turns, it creates a controlled electrical path, allowing current to flow and generating a spark at the plug. This spark ignites the air-fuel mixture in the engine's cylinders, initiating the combustion process.
However, with the advent of fuel injection technology, the distributor's role has diminished. Fuel-injected engines rely on an electronic control unit (ECU) to manage the fuel delivery and spark timing. Instead of a mechanical distributor, these engines use a camshaft sensor to determine the engine's position and a crankshaft sensor to monitor the engine's speed. This information is then used by the ECU to precisely control the fuel injection and spark timing.
The key difference lies in the fact that fuel injection systems do not require a mechanical distributor to manage spark timing. The ECU can directly control the fuel injectors and spark plugs, ensuring optimal performance without the need for a rotating distributor. This results in improved fuel efficiency, better engine performance, and reduced emissions, as the fuel injection system can precisely manage the air-fuel mixture and spark timing.
In summary, while distributors played a vital role in managing spark timing in older cars with carbureted engines, fuel injection technology has evolved to eliminate the need for a mechanical distributor. The ECU's ability to directly control fuel injection and spark plugs has led to more efficient and environmentally friendly engines, marking a significant advancement in automotive technology.
Fuel Injector Cleaner: Safe for Modern Engines?
You may want to see also
Fuel Injection Systems: These systems use electronic controls to precisely manage fuel delivery
Fuel injection systems have revolutionized the way engines operate, offering a more efficient and controlled method of fuel delivery compared to traditional carburetor systems. One of the key advantages of fuel injection is its ability to precisely manage the fuel-air mixture, ensuring optimal combustion and improved engine performance. This technology has become increasingly prevalent in modern vehicles, replacing the once-common carburetor setup.
At the heart of fuel injection systems are electronic controls, which play a crucial role in their operation. These controls are sophisticated computer systems that monitor and adjust various parameters to ensure the engine runs smoothly and efficiently. The primary function of these controls is to manage the fuel injection process, which involves several key steps. Firstly, the system calculates the required fuel amount based on engine load, speed, and temperature. This calculation is based on data from various sensors, such as the engine's temperature, air intake, and exhaust gases.
Once the fuel amount is determined, the electronic controls activate the fuel injectors, which spray the precise amount of fuel into the engine's intake manifold or directly into the combustion chamber. This process is highly controlled and ensures that the fuel is atomized to the perfect size, allowing for efficient combustion. The timing of fuel injection is also critical, and electronic controls ensure that the fuel is injected at the optimal moment during the engine's intake and compression strokes.
The precision offered by fuel injection systems is a significant improvement over older carburetor-based setups. Carburetors, which were once the standard, mix air and fuel in a mechanical process that can be less accurate. This imprecision often leads to reduced engine performance, especially under varying load conditions. In contrast, fuel injection systems provide a more consistent and responsive fuel delivery, resulting in better throttle response, improved power output, and enhanced fuel efficiency.
Modern fuel injection systems are designed to be highly adaptable and customizable. They can adjust to different driving conditions and driver preferences, offering a tailored driving experience. For instance, some systems provide a sportier driving mode with more aggressive fuel injection, while others focus on economy and fuel conservation. This adaptability is made possible by the electronic controls, which can quickly adjust the fuel-air mixture in real-time, ensuring the engine operates optimally in any situation.
Ethanol Fuel Storage: Can Cars Safely Sit with Ethanol in the Tank?
You may want to see also
Spark Plug Location: Fuel injection often eliminates the need for a distributor, changing spark plug placement
The evolution of fuel injection technology has significantly impacted the internal combustion engine's design, particularly in how spark plugs are positioned. One of the most notable changes is the elimination of the distributor, a component traditionally used in carbureted engines to route high-voltage current to the spark plugs. This shift is primarily due to the nature of fuel injection, which directly injects fuel into the engine's cylinders, allowing for more precise control over the air-fuel mixture and combustion process.
In a fuel-injected engine, the ignition system is often integrated into the cylinder head, which houses the spark plugs. This design change is a direct result of the distributor's removal. Without the distributor, the spark plugs are typically positioned in a specific pattern within the cylinder head, ensuring optimal spark distribution for efficient combustion. This arrangement is crucial for maintaining the engine's performance and reliability, especially under varying operating conditions.
The absence of a distributor in fuel-injected engines simplifies the overall design, reduces the number of moving parts, and minimizes the risk of mechanical failure. This simplification is particularly beneficial for high-performance applications where reliability and precision are paramount. Additionally, the direct placement of spark plugs in the cylinder head allows for more efficient cooling, as the plugs are often surrounded by a cooling jacket, ensuring they operate at optimal temperatures.
For vehicle owners and mechanics, understanding the spark plug location in fuel-injected engines is essential for maintenance and troubleshooting. The plugs are usually accessible through the engine compartment, and their placement is often indicated by markings or labels on the cylinder head. Regular inspection and replacement of spark plugs are critical to maintaining engine performance, especially in high-mileage vehicles or those subjected to harsh operating conditions.
In summary, fuel injection technology has revolutionized engine design, leading to the elimination of the distributor and a more integrated approach to spark plug placement. This change has brought about numerous benefits, including improved reliability, simplified design, and enhanced performance. Understanding the new spark plug location and its implications is vital for anyone working with fuel-injected engines, ensuring optimal operation and longevity.
Car Fuel Pump Burnout: Signs, Causes, and Solutions
You may want to see also
Engine Management: Modern fuel injection systems use sophisticated sensors and computers to optimize performance
Modern fuel injection systems have revolutionized engine management, offering a more efficient and precise approach to fuel delivery compared to traditional carburetor-based systems. At the heart of this technology are sophisticated sensors and computers that work in harmony to optimize engine performance. These systems have become a cornerstone of modern automotive engineering, ensuring that engines run smoothly, efficiently, and with minimal emissions.
The key to this system's success lies in its ability to monitor and adjust various engine parameters in real-time. It utilizes a network of sensors, including mass airflow (MAF) sensors, oxygen sensors, and temperature sensors, to gather critical data about the engine's operating conditions. For instance, the MAF sensor measures the amount of air entering the engine, while oxygen sensors provide feedback on the air-fuel mixture's composition. This data is then fed into a central engine control unit (ECU), which acts as the brain of the system.
The ECU processes this information and makes instantaneous decisions regarding fuel injection. It calculates the precise amount of fuel required for optimal combustion, taking into account factors such as engine speed, load, and temperature. By continuously monitoring and adjusting the fuel-air mixture, the system ensures that the engine operates at its most efficient level, delivering the right amount of power when needed. This level of precision is particularly beneficial during transitions, such as when accelerating from a stop or when cruising at varying speeds.
One of the significant advantages of this technology is its ability to adapt to different driving conditions. For example, during high-load situations, such as towing or hill climbing, the system can compensate by delivering a richer fuel mixture, ensuring that the engine maintains its power output. Conversely, during low-load conditions, it can lean out the mixture to improve fuel economy. This dynamic adjustment is made possible by the ECU's ability to interpret sensor data and make quick decisions, all within milliseconds.
Furthermore, modern fuel injection systems contribute to reduced emissions. By optimizing the fuel-air mixture, these systems minimize the formation of harmful pollutants, such as unburned hydrocarbons and nitrogen oxides. This not only benefits the environment but also ensures that vehicles meet stringent emission standards. The use of advanced sensors and computers in these systems has been instrumental in achieving cleaner and more efficient combustion processes.
Is 110 Racing Fuel Safe for Your Car?
You may want to see also
Frequently asked questions
No, fuel-injected cars typically do not use distributors. The traditional distributor and ignition coil system has been largely replaced by electronic fuel injection (EFI) and direct ignition systems.
Fuel-injected engines rely on electronic control units (ECUs) to manage the fuel injection process. The ECU sends precise fuel and timing signals to the injectors, eliminating the need for a mechanical distributor.
The absence of a distributor improves reliability and fuel efficiency. Without the distributor's moving parts, there is less chance of mechanical failure, and the engine can run more efficiently with better control over the fuel-air mixture.
In fuel-injected cars, the ignition system is often a coil-on-plug (COP) design, where each cylinder's spark plug has its own ignition coil. The ECU sends a high-voltage pulse to the coil, which then ignites the air-fuel mixture in the cylinder.
Converting an older car with a distributor to a fuel-injected system is possible but can be complex. It requires replacing the distributor with an EFI system, which may involve engine modifications and the installation of an ECU, sensors, and injectors. Professional assistance is recommended for such a conversion.