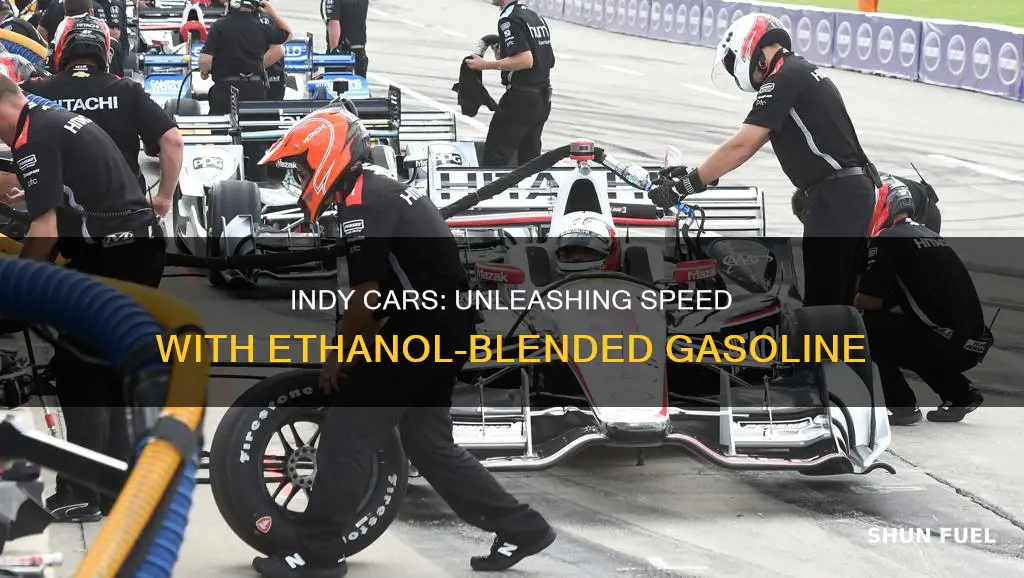
Indy cars, the high-speed racing vehicles that compete in the IndyCar Series, rely on a specific type of fuel to power their engines. This fuel is a carefully engineered blend of ethanol and gasoline, designed to meet the unique demands of the sport. The use of ethanol in Indy car racing is a distinctive feature, as it is the only form of racing that utilizes this biofuel. The choice of ethanol is not only a performance consideration but also a strategic decision to promote sustainability and reduce the environmental impact of the sport. Understanding the composition and properties of this fuel is essential to appreciating the technical aspects of Indy car racing and the challenges faced by engineers and drivers.
What You'll Learn
- Fuel Type: Indy cars use a special blend of ethanol and gasoline, known as E130
- Octane Rating: The fuel has a high octane rating to support the high-performance engines
- Fuel Injection: Advanced fuel injection systems ensure precise fuel delivery for optimal performance
- Fuel Conservation: Strategies are employed to conserve fuel during races and practice sessions
- Fuel Safety: Strict safety protocols are in place to handle and store the fuel
Fuel Type: Indy cars use a special blend of ethanol and gasoline, known as E130
Indy cars, the high-performance vehicles that compete in the IndyCar Series, have a unique fuel requirement that sets them apart from other racing series. The fuel used in these powerful machines is a carefully crafted blend of ethanol and gasoline, specifically formulated to meet the demands of the sport. This special fuel is known as E130, a term that might sound familiar to those in the know.
E130 is a high-octane fuel, typically containing 130 octane, which is a measure of its anti-knock quality. This blend is crucial for the performance and efficiency of Indy cars. The ethanol component, usually derived from plant sources, provides a renewable and sustainable aspect to the fuel, aligning with the sport's commitment to environmental responsibility. The gasoline component, on the other hand, contributes to the fuel's energy density, ensuring the engines have the power needed to reach incredible speeds.
The use of E130 in Indy cars is a result of extensive research and development to optimize engine performance and meet the rigorous safety standards of the sport. This fuel blend is designed to provide a balance between power and control, allowing the cars to accelerate rapidly while maintaining stability at high speeds. The specific formulation also ensures that the engines operate efficiently, reducing emissions and promoting a cleaner racing environment.
One of the key advantages of using E130 is its ability to enhance engine durability. The high octane rating helps prevent engine knock, a phenomenon that can cause premature engine damage. By using this specialized fuel, Indy car engines can operate at their peak performance levels without compromising long-term reliability. This is particularly important in a sport where speed and precision are paramount.
In summary, the fuel type used in Indy cars is a carefully engineered blend of ethanol and gasoline, known as E130. This fuel is tailored to provide the power and stability required for high-speed racing while also promoting sustainability and engine longevity. The use of E130 is a testament to the IndyCar Series' commitment to innovation and safety, ensuring that the sport continues to push the boundaries of automotive performance.
Understanding Car Fuel Pump Systems: More Than One?
You may want to see also
Octane Rating: The fuel has a high octane rating to support the high-performance engines
The high-performance engines used in IndyCar racing demand a specific type of fuel with exceptional properties to meet their rigorous demands. This fuel is meticulously formulated to provide the necessary energy and stability required for the extreme conditions encountered on the track. One of the most critical characteristics of this fuel is its octane rating.
Octane rating is a measure of a fuel's resistance to engine knock or detonation, which occurs when the air-fuel mixture in the engine ignites prematurely before the intended spark plug firing. This phenomenon can cause significant engine damage and is a critical factor in high-performance racing. IndyCar engines are designed to rev extremely high, often exceeding 10,000 rpm, and the fuel must be able to withstand these extreme conditions without losing power or causing engine knock.
The high octane rating of the fuel used in IndyCar racing is a direct result of its carefully selected blend of hydrocarbons. These hydrocarbons are chosen for their ability to resist engine knock and provide a stable combustion process. The fuel is typically a blend of gasoline and ethanol, with the ethanol content contributing to the higher octane levels. This blend is then further refined to ensure the fuel meets the specific requirements of the IndyCar engines.
The octane rating of the fuel is a critical specification, and it is carefully controlled to ensure the performance and reliability of the engines. The fuel is tested and calibrated to meet the exact octane requirements, ensuring that the engines operate optimally without the risk of engine knock. This precision in fuel formulation and testing is a testament to the advanced engineering and technology employed in IndyCar racing.
In summary, the high octane rating of the fuel used in IndyCar racing is a crucial aspect of its design, enabling the engines to perform at their peak while maintaining stability and reliability. This specific fuel formulation is a result of extensive research and development, ensuring that the fuel meets the demanding needs of the high-performance engines used in this prestigious racing series.
Car Fuel Tank Drain: A Step-by-Step Guide
You may want to see also
Fuel Injection: Advanced fuel injection systems ensure precise fuel delivery for optimal performance
The world of IndyCar racing demands cutting-edge technology to achieve the highest levels of performance, and fuel injection systems play a pivotal role in this pursuit. Advanced fuel injection technology has become a cornerstone of IndyCar's quest for speed and efficiency. This system revolutionizes the way fuel is delivered to the engine, ensuring a precise and controlled process that maximizes power output and minimizes emissions.
At the heart of this innovation is the fuel injection system's ability to precisely manage the fuel-air mixture. In IndyCar, the fuel injection system is designed to inject fuel directly into the engine's cylinders, replacing the traditional carburetor setup. This direct injection approach offers several advantages. Firstly, it allows for a more accurate measurement and mixing of fuel and air, resulting in a leaner and more efficient combustion process. This precision is crucial for achieving the high power outputs required in IndyCar racing.
The advanced fuel injection system operates by utilizing a network of sensors and electronic controls. These sensors monitor various engine parameters, such as temperature, pressure, and airflow, providing real-time data to the engine control unit (ECU). The ECU then calculates the optimal fuel injection timing and amount, ensuring that the engine receives the precise fuel-air mixture required for each specific driving condition. This level of control enables drivers to extract maximum performance from their engines while maintaining optimal fuel efficiency.
One of the key benefits of this technology is its ability to adapt to changing conditions. During a race, IndyCar drivers encounter various scenarios, from high-speed straightaways to tight corners, and from different altitudes to varying temperatures. The advanced fuel injection system responds dynamically to these changes, adjusting fuel delivery accordingly. This ensures that the engine performs optimally throughout the race, providing the driver with the power and responsiveness needed to navigate the track effectively.
Furthermore, the precision of fuel injection contributes to improved engine longevity. By delivering fuel accurately, the system reduces the risk of engine damage caused by excessive fuel or improper combustion. This not only enhances the reliability of the vehicle but also allows for more aggressive engine tuning, pushing the boundaries of performance without compromising durability.
In summary, advanced fuel injection systems are a critical component in the evolution of IndyCar racing. They enable precise fuel delivery, resulting in improved performance, efficiency, and engine longevity. This technology showcases the marriage of engineering and racing, where innovation drives the pursuit of speed and excellence on the track.
The Ultimate Guide to Using Racing Fuel in Any Car
You may want to see also
Fuel Conservation: Strategies are employed to conserve fuel during races and practice sessions
The high-performance nature of IndyCar racing demands efficient fuel management, especially during extended races and practice sessions. Fuel conservation is a critical strategy for teams to optimize performance and ensure a competitive edge. Here are some key approaches employed in the sport:
Fuel Efficiency in Design: IndyCar engineers focus on creating lightweight yet robust vehicles. Every pound of weight reduction translates to improved fuel efficiency. Advanced materials and innovative design techniques are utilized to minimize the car's overall mass without compromising structural integrity. This includes the use of carbon fiber composites, which offer exceptional strength-to-weight ratios, and meticulous attention to aerodynamics, ensuring the car slices through the air with minimal resistance.
Engine Calibration and Tuning: Fine-tuning the engine's performance is crucial for fuel conservation. Teams adjust engine settings, such as spark plug timing, fuel injection rates, and air-fuel mixture, to optimize power output while maintaining fuel efficiency. This delicate balance ensures the engine operates at its most efficient point, delivering the required power without excessive fuel consumption. Regular engine calibration is a critical aspect of race preparation.
Strategic Pit Stops: Pit strategy plays a significant role in fuel conservation. Teams carefully plan their pit stops to make the most of the available fuel. This involves calculating the optimal pit stop timing, taking into account factors like tire wear, aerodynamic performance, and the car's speed. By minimizing unnecessary pit stops and optimizing pit lane speed, teams can stretch their fuel supply further, gaining a strategic advantage over competitors.
Driver Technique and Awareness: Driver skill and awareness are vital components of fuel conservation. Drivers are trained to maintain a consistent pace, avoiding aggressive driving that could lead to rapid fuel consumption. Smooth acceleration and deceleration techniques, along with efficient use of the throttle, contribute to better fuel economy. Additionally, drivers are taught to recognize and react to changing track conditions, such as varying tire grip, to optimize their driving lines and reduce unnecessary fuel usage.
Advanced Data Analytics: IndyCar teams leverage cutting-edge data analytics to monitor and optimize fuel consumption. High-definition onboard sensors and trackside telemetry provide real-time data on various vehicle parameters. This data is analyzed to identify patterns and trends, allowing teams to make informed decisions about fuel conservation. By studying lap times, tire wear, and engine performance, engineers can fine-tune strategies and make adjustments during practice and qualifying sessions to set the car up for optimal fuel efficiency during the race.
Fuel Injector Cleaner: Friend or Foe for Your Car?
You may want to see also
Fuel Safety: Strict safety protocols are in place to handle and store the fuel
The fuel used in IndyCar racing is a highly specialized and carefully managed component of the sport. The primary fuel of choice for IndyCar engines is a unique blend of ethanol and gasoline, specifically designed to meet the performance and safety requirements of the series. This fuel is a carefully formulated mixture, often referred to as 'E85' or 'IndyCar fuel', and it plays a critical role in the sport's success and safety.
The handling and storage of this fuel are subject to strict safety protocols to ensure the well-being of both the personnel and the environment. When transported to the race tracks, the fuel is carefully loaded into specialized containers designed to withstand the rigors of the journey. These containers are often made of high-strength materials and are equipped with safety features such as pressure relief valves and emergency shut-off mechanisms to prevent any potential leaks or spills.
Upon arrival, the fuel is stored in designated areas, typically in fuel farms, which are designed to maintain optimal temperature and humidity levels. These areas are often climate-controlled to prevent any adverse effects on the fuel's properties. The fuel is then carefully transferred to the race cars using specialized fueling equipment, ensuring that the process is efficient and safe.
One of the key safety measures is the implementation of a comprehensive fueling protocol. This protocol includes detailed procedures for fueling, such as the use of non-sparking tools to prevent any ignition sources, and the requirement for trained personnel to handle the fuel. The protocol also includes strict guidelines for the fueling process, such as the need to maintain a safe distance from the car and the requirement to check for any signs of fuel contamination or degradation.
Additionally, IndyCar racing has a robust safety culture, and the handling of fuel is a critical aspect of this. The series has developed and adheres to a comprehensive set of safety standards, which include regular inspections of fuel systems, the use of advanced fire suppression systems in the cars, and the implementation of emergency response plans. These measures ensure that any potential issues related to fuel are quickly identified and addressed, contributing to the overall safety of the sport.
Fuel Filter Issues: Why Your Car Won't Start
You may want to see also
Frequently asked questions
IndyCar Series vehicles primarily use a high-octane racing gasoline, which is a special blend of fuel and additives designed specifically for high-performance engines. This fuel is typically a premium-grade gasoline with a higher octane rating compared to regular gasoline, allowing for more efficient combustion and higher power output.
Yes, the fuel specifications in IndyCar are unique and tailored to the demands of the sport. The fuel used in IndyCar is a custom blend, often referred to as "IndyCar fuel" or "IndyCar gasoline," and it is not the same as the fuel used in other racing categories or road vehicles. This specialized fuel is produced by various suppliers and meets strict performance and safety standards set by the IndyCar Series.
Fuel delivery in IndyCar is a precise process. The fuel is injected into the engine's intake manifold or directly into the combustion chambers through a fuel injection system. This system ensures that the correct amount of fuel is delivered at the right time during the engine's operation, optimizing power and performance while maintaining control and stability during high-speed racing.